Introduction: Jazzy Resin Wave
The popularity of resin has grown by leaps and bounds, however, there are many creatives who want to create shapes like waves but find it difficult to achieve. I teach workshops we’re resin is the medium and most of the time waves are the topic. How to create? Why do I have to wait so long? Do I need a silicone mold? I am sure you have heard all this before, especially if you love resin. Well, I created colored glass called Jazzy Glass because other colored glasses are just colored with alcohol inks and fade, etc. We needed something that was chemical resistant, and that I could make any color desired. So in this project, it started with a form and like my other Ibles on resin waves, we could use shaper sheet to form an open mold that could be used for structure and create multiple castings. The Jazzy Glass would conform to it and save on resin. So Dude/ Dudette here we go, gather up your gear and let’s get to making some fun jazzed up waves it looks like there Out-the-back and heading for a good set.
That last air I busted was totally sick!!
Supplies
Roll of Shaper Sheet
Scissor
Sharpie marker
Plastic sculpting tool or popsicle stick
Towel or foam ( for supporting Shaper Sheet while forming) be careful not to create jagged edges that can cut you.
Clear Vinyl table runner (smooth) or heavy trash bag. Clear is used for UV resin process
Gloves and goggles and proper protection for working with glass and your brand of resin used
UV resin or two part resin( if two part epoxy like liquid Diamonds just do as much as you can so the piece holds form as you build. Liquid Diamonds use code The Juliart for 20%off on $25 or more at the epoxy resin store.
UV lamp or a totally great sunshiny day
Plastic tweezers
Jazzy Glass in color choice ( I used 4 colors ) Crystal, glow in the dark blue, oasis and Tahiti (JazzyGlass.com)
Paper towels
Glitter and glitz (optional )
Step 1: Forming the Support Mold
Make sketches or view a picture of a wave. Here is the basic shape I sketched you can size it.
My wave is approximately 13”across the bottom and height is 12.5”. Your overall shape will change as you tool in the wavy lines and the white cap fold.
Lay out your piece of shaper sheet trace on your pattern foil side down. Wear gloves to protect your hands and cut out. For this wave we want the fiber facing you this just gives a cushion to your vinyl. The resin will not touch this fiber if you're careful.
Place your cut pattern fabric side down onto a towel or foam use your smooth sculpting tool or popsicle stick to scribe in your wave lines from top to bottom. Flip your wave over fiber side up. Repeating the same steps this time you will start to see the shaper sheet want to curl in creating your wave. Keep working till you get what you want. Be easy, it doesn’t take much effort to detail.
You can trim or reshape if needed, shaper sheet can be pressed flat and re-formed if needed.
Step 2: Laying in the Vinyl and Filling With Jazzy Glass
Really, this can’t get any simpler. The clear vinyl was draped into the wave form then starting with the top of the wave I poured in Crystal Jazzy Glass. Press the glass down into the venal and crevices. If you were to use two part epoxy you would add only the amount of glass that will stay in place, then pour on the epoxy playing close attention to the edges to keep it from running off. Remember, it doesn’t take a lot of resin you are just coating the JG to adhere it together. You can add alcohol inks, etc. Jazzy Glass colors are locked on. I use UV for demos, etc. just because it’s so fast. In the photo you see the UV resin being drizzled on then cure some and keep continuing until you have the wave filled with JG. Check places and if loose glass has found no problem, just add more resin.
If you set a table in front of a sunny window or do outside just keep the resin bottle covered and project out of the sun till ready to cure. The resin will burn you so wear gloves and other protective gear when working with it.
Step 3: Raising the Wave and Make Base
By this time your wave when raised it should feel very study and have a nice weight to it. While supporting the wave with one hand, add more JG to the bottom front of the wave. Drizzle on the UV resin and cure. Check to see if wave can stand on its own. Make sure all the resin is cured and not sticky, if it is place it back in the light or sun. After it is structurally sound and cured begin to remove the vinyl. Take care with this step because there could be sharp pieces of glass where you didn’t get enough resin or the vinyl may have been pinched between the glass. It will come free I do this all the time and my students do as well. Don’t rush. Any rough edges or spots just simply get a drop of resin and cure.
This is the point that you can add glitter, rocks, sand, starfish and shells more glass whatever you desire, just secure with more resin and cure or use super glue. Because the glass is transparent the UV light can easily travel around and cure very well. I like to add more glass to the wave tips and it’s very easy to just lay down small bits of JG and resin creating tiny clumps. Peel them free from vinyl and apply to the tips with more resin or glue.
Look everything over and move on to the final step.
Step 4: Finishing Touches
Time to hang 10, no, maybe just display one. Whatever you decide these waves are simple, pretty and affordable to create. The final step is to either mount onto wood, glass, resin etc.. Or just add some felt pads to the bottom.
Yes, you can incorporate strands of LED lights or place on lighted base. I sure hope you had a refreshing time watching and reading my Ible you mean the world to me.
Thank you! The Juliart
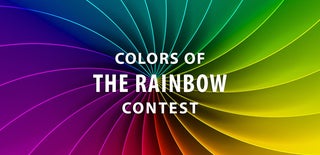
Participated in the
Colors of the Rainbow Contest