Introduction: Joinery Mallet
There are all kinds of mallets made of of various materials-metal ones, wooden ones, plain and fancy ones. This is a joinery mallet. It has some weight to it and some size. I will use it to tap prepared pieces of wood together into joinery joints. This mallet could also be used for working with a chisel.
For this project I used the following hand tools...
Chisels, mallet, Japanese hand saw for rip and cross cuts, pencil, carpenter's combination square, brace and 5/8" auger bit, bevel gauge, metal dividers, hand plane, workbench with holdfasts, clamps, sandpaper, boiled linseed oil for a finish.
The wood is a chunk of unknown species I found on the floor of a closet.
Step 1: Rough Shape
My stock of wood has water stains, dings and shows saw marks that might be from a saw mill. But I think there is a nice mallet hiding inside. It has a flat bottom and square sides, but the ends are not 90 degrees to the bottom. To correct this, I used the combination square to draw a 90* line on the side face, referenced from the flat bottom.
I wanted this mallet to have sloping ends - wider at the top than at the bottom. This shape aids in striking surfaces with a flat blow. I set the bevel gauge to this desired angle, referenced from the bottom edge and the 90* line. I marked this angle with pencil on the left and right sides of the mallet, keeping the bottom as my reference.
Next I transferred this line to both sides, by striking a 90* line on the bottom and then on the top of the mallet referenced off the angle line I had drawn. This layout let me transfer and verify that I had the angle line also drawn correctly on the opposite face. I followed this process two times, once for each end of the mallet.
Once the layout lines were marked on all sides of the stock, I used a chisel and mallet to cut down near the line. This created what Paul Sellers calls a "knife wall," a shallow straight edge that a saw blade can follow for an accurate cut.
My next step was to secure this block of wood to my work bench with holdfasts. When the block was secure, I used a square scrap to guide my saw as I started the cut. As the cut progressed, the block wasn't needed. I repeated this on the other end. At this point, the stock had a flat bottom, and two mirrored angled sides.
Step 2: Shape the Top
The top of this piece is not parallel to the bottom. The picture above shows the difference. Instead of making the top flat. I decided to match this slope to the opposite side of the top. To do this, I found the center of the side and transferred this mark to the top. Next I set the bevel gauge to match the existing angle at the top edge. Then I transferred this angle to the other side of the stock. I marked this with a pencil, making certain this line meets the existing slope at the center of the top. After transferring this line to the back. I cut this piece off with the saw.
Step 3: Refine the Mallet Head
I used a block plane to fine tune the top, blending the existing angle with the new cut. I also used this hand plan to create a soft chamfer on all the edges. The purpose of chamfering this is to prevent the edges from chipping and splitting when the mallet is used. It also reduces the chance of getting splinters when handling the piece.
Step 4: Creating a Handle
For a handle I selected a length of oak approximately 15" in length, 1 1/2" x 3/4". Since I wanted the handle to tapper, I marked the top at 1 1/2" and the bottom at 1 1/4". The difference between the top and bottom will be 1/4". This should be enough to cause the handle to wedge in place if I cut the mortise correctly. Between these two marks, I drew a line with a straight edge. Placing the handle in a vise I used a rip saw to cut just off the line. After the cut, the edges were planed smooth and square.
Next I marked a center reference line on a face running the length of the handle. I also placed center lines on the mallet head. Placing the head on the handle in its final position, I lined up the center lines and marked the bottom and top of the mallet head in its final location on the handle. These lines will be used to create the layout for the mortise on the head.
Step 5: Layout Lines for a Mortise
Using the combination square, I measured, marked and checked the center lines on the top and bottom of the mallet head. I actually had to do this twice on the bottom until I was certain of my marks. Once the center lines were certain, I transferred the width and depth of the handle to the head. Of course since the handle tapers, these distances are different for the top and bottom of the mallet head.
To do this, I used the final reference line for the bottom of the head I had previously marked on the handle. Since the center line divides this distance in half, finding the distance was simple and direct. I registered the metal dividers from the center line to the outside edge, then locked the divider set screw. By placing the dividers on the crossing of the center lines on the mallet, transferring this measurement was easy and direct. I used the combination square to mark lines based on these marks.
To help define the mortise area, I used a chisel to lightly cut the start of each mortise, staying on the inside of the lines and marks. Next I verified that my auger bit will also cut within the lines of the mortise.
Step 6: Chopping a Mortise
In order to bore holes in the mallet head, I secured it a bench top fence with clamps. I used a 5/8" auger bit, so the bore hole would be smaller than the width of the layout lines for the handle. This is important for a tight fit. In a mortise this size, waste has to be hogged away before chopping with a chisel can start. An auger bit makes quick work of waste removal. The first holes were bored into the top of the head. Each time I drilled just over half way.
The picture above shows how I raked the angle of the drill bit off 90*. The bottom of the auger is headed toward the center line. This was so I could follow the tapper of the handle when I chopped the mortise. The second hole broke through into the hole of the first so it is canted toward the center line even more. This inward angle isn't critical since it is removing waste away from the center of the chop. The final walls of the mortise will be chopped and fine tuned with chisels. Since these two bore holes converge toward each other, the material of the outside walls of the mortise are still intact, ready to be chiseled away.
Next the bottom of the head is bored. In this case the angle of rake is the opposite from this procedure on the top. I set the auger bit to cut from the center axis outward. This follows the layout of the tapered handle. Picture these two bore holes flaring away from each other.
After the holes were bored and the debris removed, I started to carefully chop the waste away with a chisel. I removed the waste closest to the inside first and slowly crept closer to the layout cut lines. I took my time, flipping the head from top to bottom and vise versa until chopping these mortise cut-outs met.
After I had chopped through, I refined the squareness and taper of the mortise channel, keeping in mind that the critical part of the joint is where the top and bottom of the head meets the handle. In reality I couldn't be sure what was going on deep in the mortise. I probable cut that area inside the head wider than it needed to be. But I preserved the stock at the top and bottom mortise until the very end. These are the two places that make the joint tight. Since I knew my top and bottom layout lines were correct, I slowly trimmed these opening so top and bottom lines were parallel to each other, getting closer and closer to the layout. I did this by sighting down the hole, comparing the lines of the top and bottom cut out cut-lines as I went. I watched and never chopped beyond the layout cuts I made in the last step. This was not a time to rush.
Step 7: Fitting the Handle
As I carefully made the mortise hole lines parallel, I also repeatedly checked for the fit of the handle at the top and bottom of the head. When I reached a snug fit, I tapped the handle in from the top as far as it would go. Then I noted how wide the handle was were the mallet stopped, and determine a few shavings with a plane would help it fit closer to the top.
I planed a few strokes and tried the fit, repeating this until I was satisfied. Then I removed the handle and chamfered the handle edge from where the head stops to the bottom. I also chamfered the ends of the handle then finished with basic sanding.
Step 8: Finishing Up
Now that the mallet was assembled together, I decided I wanted the corners to be rounded over more on the main edges. I disassembled the mallet and dressed the rough faces with the plane. Then I marked pencil guidelines on these main corners, securing the head under holdfasts, so I could reduce the corners with the plane. Next I re-chamfered each of the end faces on the mallet.
Boiled linseed oil is my finish of choice. Boiled linseed oil is a penetrating finish, not a surface stain, this means that end grain becomes darker because it absorbs more oil than when grain presents on its side.
Just two pieces of wood, when joined with a simple mortise created a useful, appealing tool.
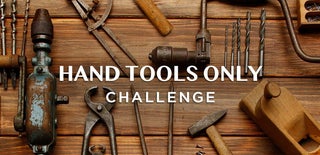
Participated in the
Hand Tools Only Challenge