Introduction: Knife Forged From Bicycle Spokes - a Truly Bespoke Knife!
I set out to make a knife using an unusual material, something I hadn't used before. And a quick search on the web yielded few results of anyone forging a knife from bicycle spokes. At the beginning I wasn't sure if the spoke material was suitable for a knife blade so I did a quick spark test (see step 1) and found there should be sufficient carbon content. However, when later testing the hardness of the quenched blade, it didn't harden to my satisfaction. (EDIT: See below) Even though the finished knife isn't going into active kitchen service, I went on to complete the knife as I was intrigued by the pattern in the blade. And I'm hoping you may learn something from reviewing the steps in my process.
Can bicycle spokes be forge welded into a knife? Yes!
In this instructable I'll show you how I forged 90 bicycle spokes into an 8 inch chef knife. This knife features a full tang, integral forged bolster, stabilised New Zealand native timber and stainless steel pins.
EDIT: We've been using the knife in our kitchen and it's working great, cutting well and comfortable in the hand. We'll be using the knife on a regular basis.
Observations:
The spokes are coated to prevent corrosion. This coating gave off some nasty fumes when heated and also contributed to some gaps in the forge welding which can be seen in the photos. Cleaning the spokes back to shiny steel would probably have resolved these issues.
Supplies
Bicycle spokes
disc grinder
welder
forge
press
hammer and anvil
power hammer (optional but speeds up forging process)
belt grinder
handle material
epoxy
Personal safety protection (breathing mask, hearing protection, apron, eye protection, steel toe boots)
Step 1: Prepare the Spokes
My donor material came from a couple of old bikes. I removed the tyres and cut the spokes out of the rims.
I cut the spokes into lengths of 110mm then bundled them together using wire. I mig welded one end to hold the spokes in place then attached a length of rebar at the other end to use as a handle when forging.
All up I had 179 lengths of spoke.
During welding it became apparent that some nasty fumes were being burned off the spokes. Good ventilation is needed here so as not to inhale the fumes.
Note
I wanted to check the presence of hardenable material in the spokes. Performing a spark test on the belt grinder resulted in star-burst sparks, a good indicator of the presence of carbon in the spokes.
Step 2: Heating the Spokes and Forge Welding
The bundle of spokes goes into the forge and when beginning to take on color, flux (anhydrous borax) is added to help with welding and drive out impurities.
When the billet had heated thoroughly, I pressed it a few times to tighten the bundle, then placing it in a vice I twisted it to further tighten the billet. By this stage, it was a solid steel mass.
The mig welded end cap is removed using a disc grinder.
Step 3: Forging to Shape
I begin to work the billet into shape, first flattening then drawing out, then introducing a step that will become the bolster and tang.
Check out the video to see the power hammer in operation.
Step 4: Final Forging to Shape
I cut off the rebar handle then forge the bolster and tang to shape. I heat the blade again and allow to slowly cool in vermiculite to anneal the blade.
Step 5: Profile Shaping
The cooled blade is marked with a sharpie then the profile is ground in. I begin to shape the bolster and flat grind the blade.
Finally I drill holes in the tang.
Step 6: Quench the Blade
I heat the blade until it is non-magnetic, let the heat build a little more then quench in oil.
The blade goes through a temper cycle then I continue with final grinding of the blade. The bolster is finished with a file to ensure square shoulders and good fitting of the handle.
Step 7: Attaching Handle
I prepare some stabilized timber and drill holes through it using the tang as a template. The handle scales are epoxied onto the blade and allowed to dry overnight.
Step 8: Shaping the Handle
My aim for the handle is to contour it and have it smooth in the users hand. This takes patience and fine adjustments until I am satisfied the handle is silky smooth.
Step 9: Etching My Logo, Etching the Blade
Until this point, the blade has been shiny but the underlying patterning of the forged blade is mostly unseen.
The blade is cleaned with acetone then allowed to sit in a solution of ferric chloride until the pattern is seen. Beautiful!
Step 10: The Completed Blade
The completed knife feels good in the hand and the blade patterning is complemented by the light colored timber handle.
I hope you have enjoyed this project.
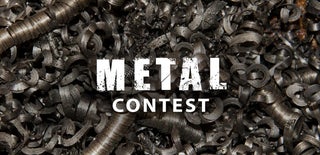
First Prize in the
Metal Contest