Introduction: Lap Harp, Psaltery
The Lap Harp, also known as the psaltery or zither is an ancient instrument built in many forms with many variations in many cultures. It is capable of serenading your most favoured loved one or providing accompaniment to your cherubic children's nap time lullaby. Probably not that crash hot for an ACDC cover band but if you want that you will have to make your own bagpipes.
Link to demo video here https://youtu.be/EDiBByxrxm4
Step 1: Draw Out a Plan
There are a lot of photos of old zithers, lap harps and psalteries out there and other stringed instruments like violins, ukuleles and guitars that will give you an idea on how long strings need to be for particular pitches and what types of strings they use. There were a few Youtubes I looked at where people were playing small lap harps with nylon strings in G I also looked up the specifications on a set of harp plans (the Waldorf 22 http://www.sligoharps.com/plans and their string length discussion page http://www.sligoharps.com/string.html) where the strings for the lowest G using a nylon string I wanted to put on this lap harp is about 19 inches (43cm) G and the Violin's scale length (with that low G note I was after) is around 36 cm (14 inches) Somewhat ruining my plans was the fact that my longest pieces of wood I had resawn for making this thing were only 40cm long (a touch under 16 inches). I decided to proceed regardless and freehanded a piano like shape. Unfortunately after fitting bridges and tuning pins and string anchors the actual string length dropped to more like 12 inches/30cm. I may fix that issue later by fitting wound strings like a Guitar D string to the lowest notes or switching to Flourocarbon (which has a higher density).
Step 2: Create Your Frame
In this design I needed to have a solid piece of hard wood at the top and bottom for strength and to hold the zither pins (tuning pegs) tight. I had initially toyed with having the pins in the straight end rather than the curved end or alternating the pins to share the splitting risk. In the end I put all the zither pins at the curved end so I could have expanded the amount of soundboard freedom at the straight end by making it thinner.
If I had used made a simple trapezoid version this curve cutting could have been avoided.
I used some leftover Tasmanian oak floor boards I got from my brother.
Step 3: Glue It Together and Level It Off
After adding some tape to the sound board to avoid glue spills I glued the frame together using the soundboard to hold it square. Then I levelled it off with a plane and some sandpaper. Simple lap joints were used and I cut some 45 degree bevels on the side pieces to free up the soundboard. As you may see my level of precision was a bit off so some filling with sawdust and superglue was required.
Step 4: Glue the Soundboard to the Frame
Spread your glue around the frame, tape the soundboard into place with sticky tape (masking tape so you can remove it easily) and add clamps. Be careful with the first few clamps so you don't knock things out of alignment and add as many as you got.
Step 5: Measure Out Your String Spacing and Mark Out Your Sound Holes
Make sure you don't be boring and wreck your perfectly formed psaltery by having a boring sound hole. Or if you prefer you can lose your nerve and cut a simple round hole in the middle. Just remember that the shape will need to be self supported so an octopus may sound good but nobody will compliment you much on having a quadopus that has funny legs after the bits break off.
I glued a bit of reinforcement to the back to minimise the chance of ouchies.
I have attached a couple of files with some sound hole templates feel free to mash them up- for example here I used triangles in my final version rather than the little hearts in the document. I used Libreoffice to draw them hence the ODG file but if you can not read that to open/edit them the PDF is identical.
Step 6: Cut Out Your Holes
I drew the shapes onto the soundboard using masking tape to provide a bit of safety/manoeuvrability. I then used my trimming knife to cut out the outlines to make things clearer. I started out on the rosette by drilling with a 3mm drill bit in each corner and where the little triangles would go then I swapped to a bigger bit and drilled out the next tightest bit. The remaining scrap was easily removed using the trimming knife. Make sure to use a backing block to prevent blow out.
I made this trimming knife by cutting off and grinding down a Kiwi brand kitchen knife I bought from my local Asian grocer for $1.75 Australian.
The small decorative holes were made triangular using a triangular needle file I just pushed it in to the hole and worked it round till the hole was triangularised to my satisfaction. I have a square file as well. A star of David like shape would be simple to make like that too.
The F hole was started using a step drill bit which is much safer for making larger holes on thin wood. and cut out using my reciprocating saw. There was also lots of smoothing off using sandpaper and files.
Step 7: Get or Make Some Zither Pins
If you live in a part of the world where zither pins are easy to get and cheap then by all means go ahead and be a coward. Chicken out now and buy some on the internet and wait ages for them to arrive.
On the other hand if the cost of freight or the convenience or just the sheer joy of making your own appeals to you read on.
Most commercially made zither pins have a square head and microthreads so in theory they can be screwed in though most sets of instructions say they should be driven in. I have seen however a few Asian long zithers (Koto Guzheng etc) that had flat ended zither pins.
Because I live far from the centers of zither fashion and manufacture (mostly because most Aussie rock and roll bands fail to make best use of the zither in their repertoire) I had a choice between making my own or getting way too many at a reasonable per pin price or paying way too much for too few and waiting weeks for them to arrive.
I first experimented with a few nails I had laying around in my shed. To form them I used a highly technical cold forging process dating back to the earliest recording of blokes in sheds. I hit it with a hammer to flatten the end. When doing this it is vital that you wear safety glasses and hold the pin firmly (preferably with locking pliers). I used my brickie's club hammer held steady with a clamp on a bid of scrap MDF on a rug as an improvised anvil. It would be really easy to damage your floor doing this.
Then I used the smallest drill bit in my set (1.6 mm) to make holes I could feed the string through. Pretty much every nail I tried worked except that the galvanised nails had to have the oxidised zinc dust sanded off before they would hold. Unfortunately I didn't have enough sufficiently large nails that I was happy with so I was forced to go to my local hardware store and spend about $6 on a 50 pack of 100 mm by 3.75 mm bullet head bright nails. after cutting off the heads and tips and cutting them in half each nail yielded two 45 mm long zither pins at a cost of about 5 cents each, less than 10% of the cheapest price I could find on the interweb. The hole these fit into needs to be the size down so they will be a tight fit. These were 3.75 mm in diameter so I drilled a 3 mm hole to mount them.
Take a bit more time than I did to keep the ends uniform thickness and length of flattening and the holes in the end a uniform length from the end.
Seeing I was lacking a microthread tap and die I put concentric grooves around the pin by bending a bit of 60 grit sandpaper over the pin and gripping it tight with my fingers and twisting it in one direction for a while. The purpose of the microthreads is to increase the surface area and increase the friction zone on the pins. It also removes any lubricant left over from the manufacturing process.
If you make the grooves along the length of the pin it will start off having even more friction but it will ream out the hole when you turn it eventually resulting in no friction. So don't do that.
You will make your job easier later on if you level off and flatten the tops of your zither pins now.
Step 8: If You Made Your Pins You Will Need Something to Twist Them With
Because I made my own pins with flat rather than square ends I could not use one of the special square ended spanners that you need for regular zither pins. I could however use a regular shifting spanner. However this was a suboptimal solution and I had to sticky tape it into position so it didn't wobble about and it was a little orkward. A better quality shifting spanner or pair of locking pliers would also have been better.
So I decided to make myself a proper twister spannery key thingy. All I needed was a T shaped thingey with a slot in the end right? After a bit of thinking and a digging through my spare odds and sods I used a spare bolt I had laying around and (after a bit of trial and error and mucking about) eventually took three hacksaw blades taped together to achieve the correct width to cut a slot in the head of the bolt. Because I had the bolt firmly held in a vice, the taped together blades were actually quite easy to hold together and cut the slot with. I wish I had worked that out the first time I tried to cut it because after all the fiddling about the slot in the end of mine is not as neat as it could have been. For a handle any nice piece of hardwood cut to fit your hand should be fine.
My initial attempt at using a couple of nuts to lock the bolt into place on the handle was woefully inadequate so I used my advance tecknolowloderodgy knockometer to flatenate the end of the bolt in the same manner as I had for the zither pins. A small chisel widened the original handle hole sufficiently to take the flatenated end of the bolt and a bit of sticky tape closed off the end of the hole and the hole was filled with epoxy that had been thickened with sawdust. The purpose of the nut purposely wound on the inside of the flatenated bit was so there would be a horizontal I could rest the bolt on in the epoxy filled hole to ensure it stayed vertical. Mine fitted so well I didn't actually need it but you might so don't forget it or find a different way of holding it vertical. I'm sure a couple of strips of masking tape over the top or a bit of bent wire or even just a clothes peg, a nail and a block of wood would do the job.
Finish off by removing the tape sanding the wood down and make it look pretty and smooth to the touch with a coat of shellac or varnish or whatever you have handy.
You don't have to make this but once you get round to tightening up 15 or so Zither pins and retuning for the 20th time you'll be mighty glad you have the right tool.
Step 9: Work Out Where the Holes Should Be and Drive Your Zither Pins In
Spacing of the zither pins at the top was around 15mm but Because I was planning on a low end straight bridge I worked out a 14mm spacing would make the strings at that end just marginally closer allowing the soundboard to bridge contact to be optimised.
As I stated before I made these zither pins 3.75 mm in diameter and they are 45 mm long so a small block of wood 15 mm thick with a 6 mm wide hole through it is perfect for making sure I drive the pins to a uniform 30 mm depth.
The hammering in process will round the edges of some of the pins so be prepared to even them up with a file.
Step 10: Add a Back
I got lazy here and used 3 mm thick pine handy ply rather than resawing and jointing some more pine for the back. No great mystery. Mark it, cut it out slightly over sized, glue it on and trim it up with sander or something.
Step 11: Drill Holes for the String Anchors. Add Some Feet. Varnish
I drilled the holes for the string anchors all the way through with 3mm bit. In the back I used my largest automatic countersink bit to create uniform rebated holes for the stopper beads to rest in. These countersink bits are the best as they kind of automatically stop at the depth they are built for.
The feet are just small squares of wood sanded bevelled and drilled through.so they can be screwed on.
Somewhere around this point I varnished it with water based polyurethane - A little shinier but no discernable difference in colour. In fact I am not sure which pictures have a varnished version and which have the pre varnished version.
Step 12: Add Bridges and Grometts
To stop the strings from biting into the soundboard you might want to install some exquisitely hand crafted guitar string ferules that you can buy for upwards of $10 for a set of 6. Or you can be like me and use some of those old pop rivets you bought a set of and only used 4 of in your old project. Just push the nail like stick in the middle out and they work great. If you have to buy pop rivets try to get and assorted set. Given the varying size of the strings I used I had to use slightly larger pop rivets at the bass end to fit the strings, which also meant I had to enlarge my string holes slightly just deep enough for the ferrule/rivet. Other options include hardwood or plastic or bone inlays and eyelets of the sort used for shoelace holes etc. You don't need to do this but I think it looks better.
Other ways of holding the strings at the fixed end are many and varied ranging from tying them to steel or wooden pegs to having slots and knots or a mounting bar. Feel free to make up your own style.
I initially tried it with a bridge only at the straight end but after fiddling trying to get the strings at one level I decided to make one for the curvy end. If I had taken more trouble to make sure I had the 1.5mm holes in the zither pins at a more consistent height in the pins I may not have needed one. Luckily the off cut from the piece of wood used to make the pin block was already the right shape on one side and only needed a little bit more cutting and shaping to make an elegantly matched bridge about 10mm high.
Step 13: String It Up and Tune It
To anchor my strings firmly I used glass beads with figure of 8 stopper knot. To fit to the peg I fit the string through the hole and wound it back under itself. Try to minimise the number of winds as the more winds the more the string has to tighten up around the shaft.
Based on the string layouts in the harp string sets I decided to go with a mix of 1.5mm whipper snipper line, 1.0 mm 100lb fishing line and 0.9mm 80lb fishing line. I have heard people on the internet talking about using a single string gauge for all strings. The 100lb fishing line would probably have been a good compromise if the bass end had been a bit longer.
To speed up the settling in process, tug on the loose ends of the strings to tighten the knots and hit them with a spot of clear nail varnish or super glue to minimise slippage.
Because of the high angle of the curve in the top bridge I made a few shallow notches to stop the strings from sliding about, which would have affected the tuning. I used an android app called DA Tuner and tuned in the key of C from G3 up to the 16th string A5.
My original plan was for 15 strings but I divided my distance by 15 instead of 14 because I forgot the first string, the starting position is actually string 0 for these purposes and got a bonus string which was actually quite handy for playing Twinkle twinkle little star in the high register.
As anticipated the low notes are a little thunky and if I had thought breaking in the strings on a 4 string ukulele was tedious this really takes the biscuit.
To make finding my way around the strings more easy I used the traditional harp colour coding of red for C and blue (or black) for F with a pair of permanent markers.
Here is the link to the demonstration video
As a further experiment I bought some wound Guitar D strings to test the volume difference and the difference in volume was astounding, as was the increase in sustain. I then shopped around for some Musical "spring steel" wire to use to string up the rest. The cheapest way by far was to buy some One dollar guitar string sets on ebay and cut the strings up. Wire strings make the volume much louder and add a lot of sustain to the instrument.
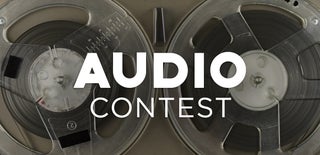
Runner Up in the
Audio Contest 2018