Introduction: Laser Cut 3D Printer
I want a 3D printer. I like making things, any thing. I believe that a 3D printer, coupled with a few other tools, could allow people to have full manufacturing capabilities in a small room or garage.
Say for example, you needed an oddly shaped part as a replacement or upgrade you're making for a car. Design it in CAD, print it, use the printed plastic item as a mold for sand casting, and with your home crucible: melt down some old soda cans and pour into your cast. Boom, in a few hours you have a solid metal part that just needs some touching up and installation. Artwork, toys, even cookware can be made this way.
I decided that to realize the most opportunity from a 3D printer, it had to be large. The Makerbot line is getting a larger workspace, with Replicator 2 having 11.2" x 6.0" x 6.1". I thought, however, that many of my own applications would need a larger workspace. That's why I designed a 3D printer that has a monstrous 16" x 16" x 13" workspace.
Step 1: Decisions
1. Do want a 3d printer? YES (that was easy)
I got my inspiration to build my own after following etotheipiplusone.net for some time now. (http://www.etotheipiplusone.net/?page_id=1114)
2. What style of manufacturing will it use? (http://en.wikipedia.org/wiki/3D_printing)
For the common, in-home, DIY printer FDM/FFF is the most likely choice.
3. How big will the workspace be?
HUGE, 16" x 16" should do
4. How will it move?
Stepper motors, controlled by Makerbot electronics.
Step 2: Functional Layout of the Workspace
There are three major ways of manipulating the workspace and the extruder. For the following explanations x-motion is in and out of the screen, y-axis motion is across the screen (left-right) and z-axis motion is up and down (with respect to gravity).
1. Keep the extruder (or tool) stationary and manipulate the workspace and part with respect to the stationary head. This means the "carriage" must move in x, y, and z axes. This is how most small to medium scale CNC machines work. This is not difficult, but the workspace becomes heavy and requires larger motors to move around. If you're looking to have a fast production time, the physically larger workspace starts providing issues with mass and inertia--creating issues with accuracy and final finish of your part.
2. Keep the workspace stationary and manipulate the extruder (or tool) with respect to the part. This means the extruder moves in x, y and z axes. With this you can achieve speed by keeping the moving parts small, but moving in all three axes provides a bit of a challenge and adds complexity. Much faster or much larger CNC machines work this way, usually because the production part is so large, that it needs to stay still.
3. Hybrid. Have the workspace and extruder (or tool) share the 3 axes of motion. This allows you to take advantage of the benefits and minimize the drawbacks of (1) and (2). I chose this method. I decided that the extruder would move in x-y and the workspace would provide z-axis motion. This is somewhat logical in that the FDM method prints layers at a time, so most of the motions are in the x-y plane anyways. The alternative to this set up is to have the workspace move in x and y, while the extruder only provides z-axis motion. The downside to using a moving workspace in a FDM process, is that you have plastic at near-melting temperatures and the machine is "sloshing" that around at high speeds.
Parallel Gantry.
The parallel gantry provides the design an ability to have a very light weight extruder assembly. Since this will be the moving part, it needs to be lightweight in order for accuracy at high speeds.
Each of the x- and y-axes have 3 precision shafts that induce motion into the extruder assembly. You can see this in the second image. The motors for each x- and y-axes connect to the sliders by a timing belt (flexible belt with teeth) and pulleys. Rotation of the motor yields translation of the slider. By providing sliding bushings/bearings at all locations, the action is quite smooth.
The third image shows the workspace height in mid-stroke. Basically, to add height to a part, the workspace slowly moves down. This actuation is controlled by a lead-screw (often called acme screw or acme shaft).
Step 3: Component Design: Case
Throughout this entire design, I needed to consider the fact that I don't have the capability to produce many of these parts with the precision that they need to support a usable assembly.
For instance, the parallel gantry shafts MUST be parallel to avoid binding while moving.
To account for this, I avoided brackets or drilling any holes myself. The way I accounted for this is by relying on a laser cutter to do all of the work. The case is more than just a case, it is also the structure and chasis for the entire assembly. Since the panels determine the shape and quality of the final part. Each of the panels have interlocking tabs, much like the original Makerbot designs.
The design is pretty simple, no complex curves or tricky assembly steps. I designed in all of the mounts needed for holding the equipment. In the back, there is a "shelf" for holding the z-axis motor and the shafts used to hold up the workspace. Since the case will also be a heat-cabinet all of the parts (motors, bearings, etc) will be subject to higher temperatures. The only components I'm really concerned about are the motors. So the motors that will be doing the most work (x and y axes) are mounted outside of the case to cut down on heat exposure.
You'll notice that there are no fasteners for the case panels. I did this because I intend on gluing (solvent welding) all of the components together with the exception of the top panel. The top panel will simply slide into place--allowing me to remove it for maintenance/repair of other parts within the assembly.
Additional features are:
The motor hole patterns are provided, and allow for belt tensioning.
The three main sides have windows which get closed to control drafts/temperature when building large parts.
Step 4: Component Design: Parallel Gantry
The layout for the parallel gantry looks complicated, but its quite symmetrical. It also uses common parts that can be found at McMaster or Sparkfun (motors).
The first picture shows the whole assembly, and the next few pictures show details of the components.
The center of the gantry is the extruder mount. This is the most complicated part of the assembly, but pretty simple at that. It uses the same interlocking tabs method as the case, but it also uses t-slotted fasteners so that I can disassemble this in the future. I don't want to glue this part up if I'm going to need to address bearings, or other maintenance items in the future. Also I've included extra mounts so that multiple extruders, or other tools like a dremel, could be mounted to provide additional performance or capabilities later on down the road.
The sliders, however, are small and simply glue together. The stationary shafts are held in place by a large washer on a small bolt.
Step 5: Component Design: Extruder
The extruder assembly consists of two main items mounted together in a housing.
The motor assembly pushes the filament through the heater head. The hub is a Makerbot item, but the tensioner is custom. These parts are intended to be printed, either using Shapeways, or asking someone who has a printer. The filament comes in from the top of the housing, and a spring holds the idling hub to the motor-driven hub. Using a stepper motor for powering the extruder allows for better control over the out-feed of the filament. This would use the A-axis port of the Makerbot electronics.
The heater assembly is based on an idea I read online about using a 5/16" vented screw to pass the filament through. The tip of the extruder is also a Makerbot item.
The actual heating element is a small block of aluminum. Has a 5/16" thread on one end to receive the vented screw, and a thread on the other end for the extruder tip. Three 15W power resistors get mounted to the aluminum block to provide the heat for melting the filament.
Step 6: Component Design: Work Table
The work table has to be strong since it has to hold a few pounds of plastic for the larger parts. The underside is braced by two large gussets the span the whole underside.
In the back area of the work table is space for bearings. I opted for three support shafts since the cantilever will be high from bigger parts. Offsetting one of the shafts provides a righting moment to counteract the weight of the part. Through the center is an Acme nut for interfacing with the Acme screw.
The work table has a removable/replaceable top to address wear over time, or modularity in the future.
Step 7: Component Design: Case Heater
As an option, an aluminum plate with 7 power resistors provide 105 Watts of heat to maintain a high case temperature to control the temperature of the plastic part (and avoid warping).
This is a pretty simple design, and it would simply mount using standoffs. The size of the assembly still allows the work table to extend all the way to the bottom of the case (the heater tucks in between the legs of the table).
A fan is included to circulate the heat around the case.
Step 8: Extras: Filament Guides
As an extra bit of flair, I've designed some Filament Guides to help the filament go from the reel to the extruder.
The larger guide has two bellmouths (or rounded entry/exit ways) to allow the filament to gently enter and exit the case without coming into contact with hard edges. The large guide also provides the mount for the filament spool.
The smaller guide only has a single bellmouth to help the filament enter the extruder.
Step 9: Assembly and Conclusion
The main parts are all able to be cut from lexan/acrylic sheet on a laser cutter.
I figure that everything could be purchased and assembled for just under $1000.
I sure hope you like this design.
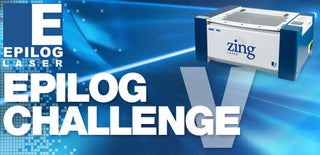
Participated in the
Epilog Challenge V