Introduction: Lathing Pistons on a Drill Press With a Homemade Collet
I have never seen anyone machine using a collet (which is how you lock a bit into a typical Dremel) and I decided to explore this myself for lathing small objects (in this case, pneumatic pistons) on a drill press for cheap. This technical information is taken from the YouTube video seen here:
I like building 1" piston air guns but the pistons can be finicky. In this video I show a new method I invented with inspiration from a friend (thanks Ingemar!). The reason for using a floating o-ring is that the piston can be relatively loose compared to the pipe it sits in and still seal perfectly. This works great for pistons cast out of a bulk purchase of fiberglass resin because they shrink while curing and cannot retain a perfect seal on their own. For my guns, the pistons HAVE to shrink smaller than the pipe itself, because the construction I use chokes the pipe enough that a perfectly made piston wouldn't be able to fit (this simply happens from hammering a 1" pipe into a 1" female adapter).
The Problem: Most spudders struggle making a cheap, light piston without a lathe. This typically leads to casting with marine epoxy, or making a piston out of bolts and washers. I don't like either of these methods personally, because cast pistons (1) tend to shrink for me and (2) the poor tolerance of the small PVC fittings makes it literally impossible to put a tight fitting piston inside and have it be removable. Bolt and washer pistons made of solid steel tend to be very heavy and even if they are easy to fine tune, cost me more resources than I am willing to use.
The Solution: Buy a lathe, but that's expensive. Build a lathe, but that takes too much time and effort. Use a drill press, but mounting a piston in one can be tricky. I was pondering how to mount a self centering chuck on a drill press, but that's still expensive for my endeavors. Making a self centering chuck seemed out of the question until my friend Ingemar asked if I could buy a collet. I instantly realized I could make one using the exact same pipe I use to cast my pistons, so it would be a perfectly sized collet. The collet is made via a series of reducers so that ANY NOMINAL SIZE PISTON CAN BE MOUNTED TO A DRILL PRESS FOR LATHING. I have personally never seen anyone use collets, yet they are very easy to mount material into and are self centering.
The Video: First I explain how I made a collet from scratch for very cheap (~$8 worth of materials!) that can be tailored to custom needs. Then I demonstrate cutting a blank piston cast from fiberglass resin. The piston is finished with a floating o-ring groove, check valve notch, sealing face, and bumper material. Lastly, I demonstrate the working piston in a test gun.
As an aside, the reason I simply shoved a 3/4" bushing into a 1" pipe via heat gun was to minimize parts. Feel free to actually use a 1" bushing and a coupling, as I probably would have to for a 2" piston, but the shorter you can keep the collet the more stable it will be.
Also, the domed affect was most likely from the chisel being at a slightly downward angle. Keeping the chisel horizontal or slightly upward might eliminate this problem.
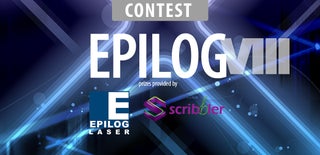
Participated in the
Epilog Contest 8