Introduction: Leaf Bowls
I love finding my forms for pieces out of what I find in nature. I grew up on the bush and sometime I do have a close look at the different shapes in the leaves. I have now made 5 bowls based off the shape of leaves, with this last set of 3 my best ones. They are a great project for learning how to use angle grinders to carve and shape wood. Its not as intimidating as it sounds working with tools like this on a larger scale. It also has the element of the stem to make it more challenging. Hopefully this instruction could show you something new or inspire you to create.
Supplies
Materials
Timber- my choice was camphor laurel. 500mm x 200mm x 50mm
Lacquer/finish- my choice was NC lacquer, satin
3mm MDF
Tools
Angle grinder
Arbourtech gear- Turboplane, mini turbo and contour sander.
Drill with sanding pads
Bosh backing disc and abrasive
Bandsaw/ jigsaw
Quick grip clamps
Linisher sander/ belt sander/ bobbin sander
Palm sander
Rotary tool- my choice is the foredom micromotor
Abrasive
Drill press
Step 1: Template
With my first 2, I made them by free hand drawing the design straight onto the timber. As I wanted to do a set, a template is the way to go. It also helps for the future for when I make more. Before sketching the design, I went for a quick walk and found a leaf that I liked the shape of. I was looking for one with some width and a little bit of interest in the shape. I didnt want to pick something symmetrical.
Setting the size is dependent on your timber and the shape of the leaf. I think a good standard is 500mm long and 200mm wide. From these perimeters, I then sketched out my design on some scrap 3mm mdf. Using the band saw and the linisher sander, I shaped my template.
A step that I did do later was carving a dashed line along the stem. This allows me to mark my center line for the stem. To cut those dash marks out, I used a star cutter and a cylindrical cutter in my foredom rotary tool. The star cutter is great for controlled lines and the cylindrical cutter got the depth of cut, guided by the v grove.
When the template is done, you can trace the template onto the wood. The good thing with this shape is that you can flip the template and butt them up to each other. This means there is less waste and you can get 2 out of 850mm rather than 1000mm.
Step 2: Cutting Out and Refining the Shape
I have a fairly large band saw so I was able to make the splitting cut between 2 different leaves. If I couldnt get the angle, I would have used a jig saw or something similar. With my cuts to separate the different pieces, I tend not to go too close to the pencil lines. The smaller sections are far more manageable and easier to cut accurately. With tighter curves, I do some clearance cuts. This allows smaller pieces to fall away and the blade doesnt bind. If you can do a curve in one continuous cut, that is ideal.
Step 3: Preparing the Wood for Carving (outside)
To fully refine my design to my pencil marks, I used a linisher sander to work up to my lines. Linishers are great as they have a flat section and the radius. The radius shape could also be done with a bobbin sander. This stage isnt really needed as it could be fixed in the carving stages.
To clean up the rough sawn, I ran the pieces through the thicknesser. The reason why I do this now rather than when its all in one board is the fact that the board had some high and low points that would have forced to remove thickness if I didnt cut them away first. The first 2 leaves that I carved, I didnt have a flat surface, so carving a flat bottom was time consuming challenge. This was much easier.
After the shape and thickness is sorted, I then marked out the bottom of the bowl. With a width of 200mm, I wanted my flat section to be about 40%, therefore it 80mm. I marked a point 60mm from the edge and used a finger guide to mark and even line around the outside shape. This is done by locking your pencil into your hand and using finger as a reference to guide a fairly consistent line around the perimeter
Step 4: Safety and Set Up
When carving with angle grinders, its important to be safe. I have a mate that just did some damage with and angle grinder and it wasnt pretty. I want to avoid that.
PPE, I use an armadillo face shield as its light and its pretty easy to forget that its on as it covers your entire face really well. It also allows me to be able to wear my ear muffs and the noise does get to you after a while of carving.
The work is secured to the table with clamps. I like the quickgrip clamps as they are easy to move and quite secure when in place. Using 2 is much better than one as there is no pivot point if it slips. I like using the larger clamps as they have a better reach compared to the standard ones. I also had a fan behind to remove the shavings so I could see my work well. When doing the other side of the leaf, I screwed blocks into my bench but I will cover that more later.
Occasionally I will wear a skin tight glove on one of my hands to protect form the shavings. I normally do this with hardwood burls as those shaving can really hurt. When ever using a glove, you have to be extra careful. If that hits the cutter or pinches, it will drag your hand in. Not fun at all.
Step 5: Roughing the Shape (outside)
To carve my leaves, I love working with the arbortech turbo plane as my main tool and the mini turbo for some more detail. I also have a saburr tooth and a merlin disc that I have used in the past. I find the turbo plane to be quicker and it can get a better surface finish. It also creates chips and shavings rather than dust. I find that better for the lungs and easier to clean up. I do like the abrasive discs for timbers that tend to tear. The other disc that I use is the cheap bosh backing disc for abrasives that I buy from bunnings. 120 grit discs are pretty good at removing waste.
To start I clamp it to the edge of the table so it over hangs. This way I can carve right up to the edges. For now, Im just trying to get a nice radius from my marked out base area to the edges. I aim to stop 1-2mm away from the edges with the roughing tools as will get blended with the sanding tools. Pictures 3 and 4 show how I was able to remove a defect that wasnt fully cut out. I knew the depth and accounted for its removal in my prediction of the shape.
Picture 5 shows how depending on the approach angle of cut, I can get a lot of tear out. By changing my angle of approach, I was able to easily remove the tear. Dont blame the tool or timber straight away but change your approach or angle of the tool.
After removing most of the waste with the turbo plane which is my most efficient tool, I change to the bosh disc to remove ridges and the little bit of tear out. Make sure you leave the stem square as that is a good clamping point for the rest of the carving. One important feature to get right is the ridge line at the end of the leaf. This should be a nice curve and can be adjusted by working on the high side to get it right. This can be seen in pic 7
Step 6: Preparing the Wood for Carving (inside)
Using your finger gauge again, mark out a wall thickness that you are happy with. It can be good to even go a little bigger than your desiered finish size. Also using your template, mark your center line for the stem. To make sure I have a consistent depth in the lowest section, I drilled some depth holes as a guide. A drill press is a great tool for consistency.
Clamping a now rounded surface to the table can be a challenge. I know some people use sand bags to support the piece. Other options included using hot glue to attach waste blocks or creating a cradle for the piece. What I did was use the stem as a clamping point as well as wedging the other end between a block I screwed to the table and another clamp. I used a towel to take the uneven shape better. This allowed me to move the piece to more convenient positions.
Step 7: Roughing the Shape (inside)
Using the turbo plane I started to remove the bulk out of the middle. to control the tool, I always lock my elbows into my side and the pivot the grinder down into the wood. This limits my movement and as I move my entire body from waste up, there is a lot of mass behind the small movements. If you hold the tool out from your body, it has the power to run where it wants. By pivoting down, it slowly introduce the cutter into the wood, causing it to cut, rather than catch. The cool think about the turbo planes is it only cuts on the bottom of the cutter so you can use the edge to guide your cuts.
To get some of the deeper parts, I use the mini turbo. This cuts more on the corner so It will cut a bit on the sides and the bottom. It reacts differently to the turbo plane which is worth knowing. These differences allow me to get to those other sections a bit easier. Smaller discs tend to create more ridges but can get tighter radius. Pros and cos. Having both allows be to pick and choose to get all areas.
Step 8: Shaping the Stem
The stem is the hardest part. I reckon it almost doubles the time it takes to make these but its a great detail to add. I use my foredom micro motor with a range of burs to shape it. These tools are quite expensive but you can do the same thing with a $40 rotary tool. Mine is just so much more comfortable to work with but I do a huge amount with it so its pays its self off for me. The cutters that I used were mainly 2 different shapes of saburrtooth burrs. The cylindrical one with a domed top and the small disc shape. The disc shape was to set a depth down and the cylinder was used to round the stem over. This could be done with all sorts of cutters. I know that carbide burrs give a much cleaner finish and could be used over the top of these.
On the top surface, I bring down the edge of the leaf with the bosh sanding disc as a small section only needs to brought down about 4mm. Its important to blend this in to the rest of the edge to create en even taper
Step 9: Refining the Shape
Now that the majority of the shape is bulked out, I want to even out the wall thickness and make sure the stem is a nice taper. I re marked out my wall thickness and center lines for the stem. To do the reducing I could use all sorts of tools but I chose to use my hand chisels, Pfeil carving tools. I used 4 different shapes. My main one was my largest 7/18. To reduce the ridges, I used a flatter one 3/12. To get the shaping of the stem I started with my 8/10 and then down to my 9/5d to get a tighter radius. I could have a crisp v grove but that takes so much more work.
When using my larger chisel, I worked down the sides and across the grain. This was really easy as I got very little tear out. I could feel the wall thickness between ever few cuts and I was able to efficiently get a fairly consistent shape. Working near the stem with the tighter radius chisels, I did get a bit of tear but by reading the grain, I was able to navigate that easily.
Step 10: Sanding
Sanding is the most time consuming part of a carving like this. I like to start with Velcro backed discs on a drill and then do the fine sanding with the arbortech contour sander. I dont think that it is as good for rough sanding as I like a bit more power for the first stage. For finer grits, its the best sanding device I have used.
Back to the drills, I use a combination of 75mm, 50mm and 25mm sided disc. The 25mm actually fits in my rotarty tool which is easier to control than a drill. The larger the disc the better as you can create a more uniform surface but the smaller discs get into tighter curves. Its always nice to have a range of options to figure out what works best. To sand the stem, I do this by hand as by pinching the abrasive over the ridge, you can create a good radius that just takes the high points. Its very important to get nice even curves and well blended shapes.
After sanding to 120 grit, I change over to the contour sander and work through to 400. This is brilliant for making a silky smooth surface. As the name suggest, its good at following contours so it will follow the surface you left with the 120 grit on the drill. I would spend about 75% of my sanding on the first grit. The fine sanding doesnt take long which is nice.
Step 11: Shaping the End of the Stem
Now that the inside is done, you no longer need the stem as a clamping point. I remove the bulk with the turbo plane after marking out a rough curve. The radius on the linisher sander is pretty much perfect so I sand the shape on there. I even add a small radius on the end so I dont have any flat surfaces on the entire piece. I can even use the discs to shape the stem to a round. By lifting the angle of approach, it will leave marks but they sand away easily. I manage to refine my shape with these 2 sanders pretty well.
Step 12: More Sanding
More sanding. Its almost done. External curves are much easier than internal curves. I use my palm sander to do the majority of it. The foam padding allows it to sculpt to the shape reasonably well. The stem might take some hand sanding. When its all done, use some 240 grit to arris the sharp edges. You want it to have a smooth finish. I cut my finger twice while making these bowls and both were on the timber, not a tool. Always seems to be the way. Good to remove the chance of that happening.
Step 13: Polishing
I finish most of my works with a nitrocellulose lacquer. The first coat is always the most fun to go on. For these bowls I use the 30% gloss (satin). This is what I find to be the most consistent finish when sprayed on. Most of my pieces are done with 3 coats of lacquer, cutting back with 600 grit between the 2nd and 3rd coat. As I work in a dusty area, its sometimes hard to get a perfect finish so I then buff it with a plain piece of paper. That seems to knock of the little flecks really well.
Step 14: Done
These did take a little longer than I was hoping but over all I got through them pretty quickly and this set of 3 is better than the first 2 that I did. The camphor is perfect for carving something like this and love how they have finished.
Carving with angle grinders can look intimidating but they are actually pretty easy to control, especially with the arbortech gear. These are relatively easy with a good shape and shallow depth. Working around the stem is the main challenge. Hopefully this inspires you to have a go with some larger carvings. Cheers
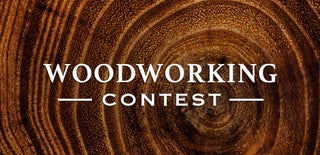
Second Prize in the
Woodworking Contest