Introduction: Leather Portmanteau for All Your Storage Needs!
Hello Everyone!
I really fell in love with leatherworking a few years ago thanks to a few enterprising friends and a lot of extra time on my hands. Ever since then, I've been acquiring as many skills and tools as I can to make bigger and better things. The problem is, of course, how should I store all these new and exciting goodies? Some of my friends and a few history books on materials culture, gave me an idea and pattern for a Rollbag/Portmanteau that I've since outgrown. Now the time comes once again to create another larger bag to accommodate even more tools and supplies.
Portmanteaus can come in all sorts of shapes and sizes depending on a persons needs. Some are round, others look more like treasure chests. They can have handles to help haul them around, straps to secure to a saddle, or even a should strap to carry them long distances. The possibilities are really endless, so there is never really any one size fits all pattern available, but that's part of the fun.
In this Instructable, I'll show you the techniques I used to make a new portmanteau by hand, so that all of your valuables, tools or personal effects can easily be taken anywhere and everywhere.
Oh and as a self serving request, please vote for me if you like this ible!
Step 1: Materials and Tools
Tools
- Ruler
- Square
- Compass or Edge Groover
- Needles (thicker needles are far easier to grip)
- Leather Shears or Heavy Scissors
- Round Knife
- Round Tip Leather Awls (round tip will let you reopen holes without breaking your thread)
- Leather Punch or Rotary Punch
- Mallet (wooden or rubber so your tools won't die)
- Pliers
Consumables
- Thread or Sinew
- Beeswax
- Oil (I prefer Neatsfoot Oil but the choices are nearly endless)
- Cardboard
And last but not least:
- Leather! - (I used both 4-5 oz for the main parts and 2-3 oz for the accessories in this ible)
If you want a really nice finished look I'd also recommend a Burnisher or two, they can really take a project to the next level if you know what you are doing. Also with the thread, I work with 4 ply linen thread that I coat with beeswax, but there are waxed threads for sale out there that eliminate the extra step, and I even know of a couple folks who choose to use Dental Floss!
Step 2: Planning It Out
So our first step is to plan what type of portmanteau we would like, as well as laying out the dimensions to suit our needs.
Regardless of whether you go with a round bag like my first one or a treasure chest style like my new one here, I always prefer to start with the sides and use them as the basis for the main body of the bag. This has saved me a lot of aggravation and sorrow since the pieces will be cut to match from the get go.
The method I'm using to stitch these parts together is called the Saddle Stitch, and requires the you to give it a bit of seam allowance. With this in mind, I sketched out a quick pattern on a piece of cardboard and moved in slightly to accommodate my stitches. I went ahead and also marked out the circumference of the side so that I could properly size the main body. In this instance the circumference of my side template, again adjusted for the seam, was roughly 18 1/2 inches total.
Now that we have the sides sorted out, we can move on to the width and opening of the main body, as well as the lid.. I went with a width of 15 inches, and cut out a rectangle 15" by 18" and set to work on cutting out a good opening to access the bag.
I used the circumference of the curved section of my side to determine how large to make the hole, and sketched out a design I felt comfortable with. I recommend rounded edges as opposed to straight ones, it makes life a lot easier as you start using your bag as straight squared edges can cause tears from stress and repeated use.
Last but certainly not least is the lid to close up the bag. Like a fool I forgot about this until I was almost ready to cut out the bag, luckily it was just a simple matter of creating a rectangle to cover the opening I planned out roughly 9" by 15".
Last but not least keep a watchful eye on any trouble spots on your leather and plan around them as much as possible.
Step 3: Cut It Out!
Once you've traced your templates onto your material it's time to cut all the parts out. You can use a round knife like the one pictured or a good pair of heavy leather shears.
From my experience, the knife usually works a bit better on the long edges, as you can rock it back and forth in a straight line, but the shears usually are more effective on curves as you can usually manhandle them a bit easier.
Regardless of the method you choose to cut out your leather, always remember to be very careful. These tools are made to cut through thick cowhides, and our skin is far thinner, and therefor far easier to cut open.
After the parts are cut out, compare them to your template to ensure that they are all the correct sizes and shapes.
Step 4: Plan, Count and Punch the Holes
Now we need to plan out the holes which will be punched in the next step. You definitely don't want to try and wing this process, because the edges you're going to be joining together need to match up in order for the finished product to look as good as you originally planned.
For this process I rely on a wing divider, which is available for a fairly low price from most leather companies. You can also use a groover and rotary wheel to mark out the spacing if you'd like, but I'm a cheap guy and have found the wing divider can pretty much do it all. To mark where the stitches will fall I set my divider to about 3/16 of an inch.
As far as the spacing goes, you'll want to use the same setting for all the pieces, or else the holes aren't going to line up as well, if at all. I used the same spacing of 3/16 an inch as the distance between the holes and "walked" my wing divider down the channel I created earlier while applying pressure to leave some strong indentations.
Don't panic if there aren't enough marks on one piece to fit with another, as now is the time to correct things like that. In fact if you don't correct that during this step, you'll be hard pressed to fix it at all. If you find that you are short one or two, its a pretty simple fix, what you'll do is essentially duplicate a hole, which will throw your spacing of slightly but will allow you to join the pieces with minimal impact. If you're short more than two you may not have cut the right length on your pieces, which is a little harder to fix as it usually requires cutting out a new section.
Also try to keep in mind which edges are to be attached to one another, to try and illustrate this I color coded my template to reflect where the edges are joined.
Once you're happy with how the holes are laid out you can use your awl to punch them out, and count them once again to ensure that they are all there.
With that done with set aside your main pieces for a little bit so we can get the accessories together.
Last but not least, you may notice that in the picture my lid has lost a small section near where my planned stitches are set to be placed. This was done to prevent the lid stitches from overlapping with the sides when they are put on the piece.
Step 5: Accessories Part 1: the Handle
Historically speaking, portmanteaus could have one, two or three handles to allow you to lift and carry them much easier. For this one I decided to just use a single handle on the very top of the bag.
I used rectangle roughly three inches wide and five inches long to begin to shape the handle, since it will be sewn to itself and rolled up that will give me a completed handle of about and inch and a half in width.
First up I cut the corners down by a half inch leaving me with a little nub on each side. Then I shaped it with my shears into a more rounded shape to give it a more pleasing appearance.
Last but certainly not least was to plan out and punch the holes on all the edges, and as an added bonus the long edges are being sewn to one another, and as such were the same length exactly!
Again, set this part aside for the moment.
Step 6: Accessories Part Two: Closure Straps
Next up are the straps and buckles to hold the lid closed. normally you'd find the straps and buckles joined together as one, but in this case, they are separate.
The width of both is set by our buckles, which for me was one inch. I used my round knife to carefully cut the straps out, to a length of about twelve and a half inches. I will say if you can get your hands on a draw gauge, or strap cutter, it makes this process far easier to do. However you cut them out, once your straps are made you can give them a more pointed or rounded end, whichever you prefer, and ready the back end for stitching later on, again using the same skills you've been using on the other pieces.
As for the buckles, I cut a one inch strap roughly five inches long. As we are affixing a buckle to these, extra stitches need to be planned. you'll also need a short gap to accommodate the tongue of the buckle. If you notice in the photos, there is an extra row of holes, which will be used to stitch over the bottom edge. as far as the slot for the tongue goes, I used my rotary punch to pop open a hole down the middle of the strap between the two sets of stitches to allow the buckle to move freely.
Step 7: Dyeing
Typically you'll want to dye your leather before you cut it out, to ensure an even coating and finished product. In my case I got the dye late into the process because the leather I had available had several stains on it, so I needed to apply the dye to give it an even coating.
I left all the pieces and parts to dry overnight and continued on to sewing it all together.
Step 8: Sew Up the Buckles
Before you sew on your buckle, make sure it fits into the slot you created earlier. Assuming it does, you can begin to stitch it in.
You'll need to draw out a length of thread, cord, sinew, floss or other material you intend to sew this project together with. If the thread you've chosen is like mine, and I mean unwaxed linen thread, you'll need some beeswax to run it through before beginning to sew, to both lubricate it as well as give it some additional strength and water resistance. As a general rule of thumb, you'll want it to be roughly long enough to cover all the stitching at least three times so you can properly tie it off in the end.
For this portion you'll need only one needle and to keep your awl close at hand. Once you've threaded the needle you'll want to pass it through the first hole and leave a small tail which you'll use to tie off on later. I prefer to start near the edge of my piece and usually right next to the buckle as pictured above. Next I like to pass the needle around the outside edge of the strap and back through the hole again.
Doing this will prevent the edges of the strap from rolling up and putting stress on the thread causing it to eventually fail. This same process is repeated along most of the holes near the edges, including the bottom of the strap itself to give my project a little more longevity. As far as the rest of the stitching goes, it's as simple as passing the needle through the holes and working your way back over to the starting point to tie off the left over thread and it should go without saying that you need to pull tight to make sure everything is joined properly.
I like to try for a nice pattern, so I typically will work down half the holes first, and then attempt to duplicate the stitches on the other side, which again, you can see pictured above. One you are able to work back to where you began you'll need to tie off with a square knot and pull the portion with the needle attached through your first hole. The idea here is to sandwich the knot inside the leather so that it's less likely to come untied.
Once you have the buckles attached you can attach them to the main body of the bag. Seeing as we have already punched the holes at the bottom of the buckles, but not in the bag we need to plan out where they'll go. I decided to place one strap and buckle every three inches down my bag right around the edge of where the top flap was going to end. After measuring out the locations with a ruler and a square, I used the holes punched in the end of the buckles to mark where the new ones should be in the bag.
I also added extra holes around the perimeter to over stitch the edges of the strap, similar to the way we earlier stitched around the edges near the buckle. Once the holes are punched, and assuming you are pleased with the results, you can affix the buckles to the bag's main body, using the same pattern you developed on the buckles, or a new one if you like. Regardless it is essentially the same as sewing the buckles into their place.
Step 9: Sewing With the Saddle Stitch
Next up is to finish our other accessory, the handle. This portion will require two needles, some thread, warm water and a mallet.
The first thing we'll need to do is sew our two long edges together, and the method we'll use is called the Saddle Stitch. This is a fairly basic stitch, yet it's extremely strong as you will put pressure on both sides of the material at the same time, similar to but not quite like what a sewing machine does.
Put both needles on either end of your thread and run one of you needles through your first hole in your stitching, and pull it through until you have roughly half of your thread on either side. I like to go around any exposed edges like the one we have here, in this case with both halves of thread. The idea is the same as with our last step; keep the leather from rolling up on itself and straining our thread.
Now then, take one of the needles and run it through the second hole, as normal. Pull it tight once it's through to the other side. Now grab the other needle and run it through the SAME hole as the first. Pull both threads hard to ensure your stitch is tight. Continue repeating this process until you reach the end.
Once you've come to the last hole, go ahead and stitch around that edge as well, and work your way back up you project for two or three holes before tying off. The reason you'll want to do this is just in case your knot doesn't hold it wont unravel. Push one needle through so that everything is on the same side and pull it off the thread. Tie both of your threads together (double knot for luck) and push your remaining needle through the hole to the otherside, pulling your knot into the leather.
You should now have a leather tube, which will need to be flattened. To do so, you'll need to run warm water over the whole handle so that it's pliable, then work out your stress with your mallet! once your handle is flattened to your liking, preferably with the seam in the center of the bottom, feel free to shape it more ergonomically, and set it aside to dry out.
Step 10: Sewing on the Lid and Straps
For this part it's easiest if you sew on your lid, before you sew one the upper straps, if only because you won't have to work around the straps with every pull of your needle.
When attaching our lid/upper flap, I like to use the saddle stitch from last step. The process is exactly the same with one small addendum. Instead of going for enough thread to cover the stitches 3 times, I recommend having enough to run the length 4 times, to make sure you don't run out. It's not the end of the world if it happens, but it can be annoying. If you remember, we cut a small portion of the stitching off of the flap, to prevent it from running afoul of the sides and give our stitches some breathing room.
As far as the straps go, at this point feel free to plan out their positions so they line up with their buckles on the other side, if you haven't already. Last but not least, sew them on in just the same manner as with the buckles and this portion is complete!
Step 11: The Baseball Stitch
At this point we need to join the top and bottom of our bag together so that our bag and take on its distinctive rounded look. I like to get a bit fancy, so here I used whats called a Baseball or French stitch.
This process is very similar to our saddle stitch covered earlier, with one major difference being that we will join the pieces edge to edge, as opposed to sandwiching them together. Again you'll need to have two needles on the same thread to start out with
Push both needles from the bottom through opposing holes and pull until the sides meet up flush and the thread is roughly equal on both sides.
Next pick a needle, right or left your preference, and pass it between the leather to the next hole on the opposite side. Repeat this on the other side with your second needle. The result should be what resembles a chevron or a small "v" pulling the leather together.
You'll want to repeat this process down the length of your leather, and always make sure to start a new "chevron" with the same needle. The more stitches you have the tighter and stronger the hold will be.
When you come to the last holes, cross the needles over one another as shown and push them through to the back of the leather to tie off the ends of the thread tightly.
Repeat this process on both upper portions and you should be ready for your sides!
Step 12: Sew on Your Sides
I like to save the sides for last, because if you need to sew anything else on, they can get in your way pretty easily. For these I used, you guessed it, the saddle stitch. In this case I also needed to sort out where exactly the rounded edge was to start, so that the opening and the flap would be in the correct position. Luckily when I mapped out my original designs I made a small mark roughly 4 and 1/8 inches up each side piece to symbolize the start of the rounded top and opening.
I chose to start my stitching there so that I could reinforce my earlier french stitch a little better. I would like to recommend that since this is the longest edge, and since the amount of thread you'll be losing is pretty high, you may want to pull the ends through the needle a lot further than normal. I say this because if your thread is too far out behind the needle, it can form knots very quickly (not that I learned this the hard way when I first started leatherworking). Also you'll really be thankful if you keep your awl and a pair of pliers close by for this portion. The leather here is fairly thick and your needles can easily get stuck or break if you aren't careful.
It's also important to note that there shouldn't be any need to over stitch any edges here, so that's one less thing to worry about. You may notice, however, that the corners stick out a bit. If this happens to you, a pair of leather shears can easily correct it!
Once the threads are tied off and both ends are on, you should have something close to your finished product, and there are just a few more parts to attend to before you call it done.
Step 13: Finishing the Buckles
Now that you are starting to see your finished project, you'll need a way to close up your bag. At this point you don't have any holes in the straps to use with your buckles, but correcting that is fairly simple.
Pull the strap through as if you were about to buckle it up and pull it tight against the tongue to leave an indentation. Next take your rotary punch and punch out that first hole. Since our leather will stretch, I like to add two more holes above and one below our first. Mark these out with the compass and punch the holes with the rotary punch and you'll be ready to go!
Step 14: Adding the Handle
Now it's time to get a Handle on things...
With all your straps ready to go the last piece you'll need is the handle, or handles, to carry it! With the holes already punched at both ends of the handle, I prefer to use them as a guide for where the holes should be in the top of the flap.
I also found that it's a little easier if you sew down one side before working on the other, provided you like where it's seated. To affix this piece I chose my old standby, the saddle stitch.
Once both ends are affixed you are almost entirely done with the project!
Step 15: Finishing Your Portmanteau
With all the pieces and parts finally sewn on, your portmanteau is nearly complete. At this point you can burnish the edges if you'd like and apply oil over the whole thing. As I mentioned before I like to use Neatsfoot Oil on my projects, but pick whatever you are most comfortable with.
I hope you enjoyed this project and if you have any questions I'd be happy to help answer them!
Thank you for reading to the end!
Never Stop Creating!
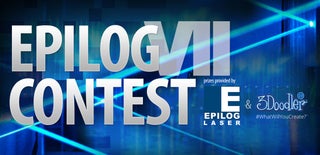
First Prize in the
Epilog Contest VII
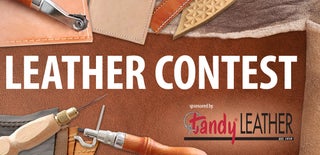
Runner Up in the
Leather Contest