Introduction: Leather Pouch for Leatherman Wave® and Mini Flashlight With Free Pattern
This Instructable will show you how to make a leather pouch for a Leatherman Wave® multipurpose tool with a mini flashlight holder, out of a single piece of leather. I find that both tools are essential whether I'm at work, in my shop or in the piney woods. I sized this pouch so it could be made from an 11” x 8” cut of leather, readily available at Tandy Leather Factory or most craft stores.
I’ve saved you the work of making a pattern by supplying you with a free outline. It has the option for either a ‘AA’ or ‘AAA’ aluminum body flashlight.
Attachments
Step 1: Tools and Supplies
Tools Used
- Poly Head Mallet
- 1” Oblong Bag Punch
- 4-in-1 Stitching Hole Punch
- 6-in-1 Rotary Punch
- Wing Divider
- Awl
- Leather Knife (Or Utility Knife)
- Snap Setter & Anvil
- Burnishing Tool /Slicker
- Metal Square
- Metal Straight Edge
- Edge Beveller
- Adjustable Stitching Groover
- Freehand Stitching Groover
- Stylus Tool
- Bone Folder
- Leather Cutting Scissors
- Basket Weave Stamping Tool #X511
- Camouflage Stamping Tool #C432
- Sponge
- Applicator for Dye/Stain
- Small Artist's Brushes
- Granite Slab or Similar Hard, Flat Surface
Supplies*
- 8-1/2” x 11” Veg. Tanned Leather (6 to 7 oz.) [4033-08]
- Eco-Flo® Gel Antique (Med. Brown) [2607-03]
- Tracing Film [3500-00]
- Eco-Flo Super Sheen® Finisher [2611-03]
- Gum Tragacanth [2620-01]
- Leather Sewing Needles [1195-00]
- Waxed Thread (Brown) [1227-02]
- Fiebing's Acrylic Resolene [2270-01] (Optional)
- Disposable Vinyl or Latex Gloves
- 1/16" Adhesive-Backed Neoprene Foam Padding
- Blue Masking Tape (low-adhesive)
- Paper Towels
- Water
*Tandy Leather Factory Item # in Brackets [ ]
Hardware*
- Medium Belt Clip [1240-00]
- Small Double Cap Rivet [1371-12]
- Line 20 Snap [1261-02]
*Tandy Leather Factory Item # in Brackets [ ]
Step 2: Tape It Down
Tape the leather to your work surface, smooth side up using “blue” (low adhesive) masking tape. Be careful to put the tape on only the edges as it can leave adhesive residue or mark your project even preventing the dye/stain from being absorbed.
Step 3: Case (Wet) the Leather
Begin by casing (wetting) the leather. Immerse the whole piece in water for a half- minute or so. Set it on your work surface and wait until the water has soaked in and the color has lightened. It will feel slightly cool, but not wet to the touch. Cased leather is easier to cut, shape, mark and stamp. Be careful with it because it is also easy to accidentally scratch or stretch out of shape. During the various steps, moisten the leather with a damp sponge. During breaks, store the leather in a zip-up plastic storage bag so it will retain its moisture.
Step 4: Trace the Pattern Onto the Leather
I use tracing film between the pattern and the leather to keep the paper pattern from getting wet. Tape the film and pattern to the work surface to keep everything from moving. On the other hand, you can trace the pattern on to the film with a pencil and use it to outline the pattern on the leather. Because the leather is moist, the impression from the stylus will show clearly even after going through a couple of layers.
The pattern is for a multi-tool pouch with the flashlight holder/sleeve on the right side. This arrangement seems to work best for a right-handed person when the pouch is worn on the left side of your waist as the flashlight sits behind the multi-tool. Just flip the pattern over if you want the flashlight on the left and trace through the backside of the pattern.
Use a stylus or even a dry ball-point pen to transfer the pattern to the smooth side of the cased leather. Occasionally lift one end of the film to check to make sure you're copying it all. Use a metal ruler or square to help keep lines straight and corners at a right angle. Keep checking to ensure you mark all solid lines, stitching, rivet and slot holes, except don't mark for the hole for the snap at the top of the flap. The dotted lines are reference lines for gouges on the rough (flesh) side of the leather.
Step 5: Cut It Out
A metal square or straight-edge will help to keep your knife blade perpendicular to the leather and your cuts straight. Don’t use a plastic ruler as your knife will cut into it and your line will be crooked. Use a new blade for every project because a dull blade will cause the leather to snag, stretch or bunch up. Blades are cheap compared to running the leather. On very thick leather you should make multiple passes. Go slow and take your time as bad cuts are difficult to hide.
Step 6: Holes & Slots
Use a 1” oblong bag punch to cut the slot for the belt clip or punch two 1/8” holes one-inch apart. Then use your knife to cut between the holes. Caution…when cutting out the slot, make cuts away from each end hole a little more than half-way towards the center. Refer to the ‘Slot Cutting’ photo. Then repeat the cut from the opposite hole. This will keep you from cutting beyond the holes. To cut the 3/4” wide oblong slot at the bottom of the pouch, use a 1/4” punch for the ends and cut out the slot in-between; again use caution not to cut beyond the holes.
Gouge a sewing channel over your stitching hole marks (about 1/8” from the edge) using an adjustable groover or a freehand stitching groover and a straight edge. This will keep your stitch-hole punches lined-up and allow your stitches to lay flat. Punch all stitching holes and the 1/8" holes for the rivet and snap, except for the hole on the top flap. You’ll punch that hole later.
Step 7: Feelin' Groovy
Using the freehand groover, gouge out the fold/crease lines on the rough (flesh) side of the project. This will make it easier to fold the leather and prevent the leather from cracking at the folds. (Keeping the leather damp also helps prevent the leather from cracking.) Use a bone folder or any non-metal tool to crease/fold the leather along the grooves.
Step 8: Stamp or Tool Option
Stamp or Tool
Use a wing divider or stylus to lightly mark the borders for your design. (If you are not going to stamp or carve a design on the pouch, skip this step.) I used a X511 Basket Weave tool, stamped diagonally, to create the pattern and bordered it with a C432 Camouflage stamp to cover my border marks. Re-case the leather if it gets a little dry. You’ll get better impressions. Oh, and take care not to hit the basket weave stamping tool too hard or you will punch the edges all the way through the leather. Several light taps while tilting the tool from side-to-side to works better than a single mighty strike.
Step 9: Edge Beveling
Edging
To give your project a more finished look and make it easier to slick/burnish the edges, trim all sides with an Edge Beveler.
Step 10: Give It a Rest
Allow the leather to completely dry (overnight is best.) Once dry, it is ready to either dye or if you want to maintain the natural leather color, apply Fiebings Resolne as a finisher. Apply two light coats with a soft cloth. Buff liberally with a soft cloth. This not only makes the pouch resistant to water but also to the oils and grime from your hands.
Step 11: Dye Job
Put down cardboard or several layers of newspaper to protect your work area and absorb any excess dye/stain. Glove-up; you only want to dye the leather not your skin. I like to use a cardboard box to prevent any chance of dye splashing onto my workbench. Pour a small amount of dye (if you spill the dye, you will have only a small amount to clean up) in a plastic or glass dish (never metal). I use Tandy’s Professional Waterstain® as I’ve tried others, but it works best for me; easy to apply, even staining, etc. Use a dauber, damp sponge or wool scrap to apply the dye to the leather. Don’t pour the dye directly on the leather. It’ll leave a dark spot where it first makes contact. Work the dye into the leather in a circular motion, evenly covering the entire piece. Make sure you get the edges and into all the stamp impressions. It’s a personal preference, but I dye the flesh side also. Your project; your choice. Wipe off the excess dye with a clean paper-towel. If you want the color a little darker allow the first coat to soak in for a few minutes and apply another coat. Once dry, first buff the surface with a soft cloth to remove any loose pigment, then apply a coat of Eco-Flo Super Shene® or other sealer. This will keep the dye from coming off on your hands during sewing and hardware attachment. Again, everything needs to be dry before going on to the next step.
Step 12: Snap, Clip and Cover
Attach the male side of the line 20 snap to the front of the pouch using a setter on any hard surface. Insert the belt clip into the slot on the back of the pouch and secure it with a small rivet. (These two steps are much easier to do before you stitch-up the sides. I know this from experience.) I cut a piece of adhesive-backed 1/16” neoprene foam pad to cover the inside of the snap and belt clip to protect my Leatherman® from scratches. The adhesive firmly attaches the foam to both metal and leather. It is easy to find on eBay and usually sold by the square foot. I also use it on the inside of cell phone cases to protect the screen.
One note about using a metal belt clip; you can sew a belt loop on the back of the pouch and slide the loop on/off your belt. It costs next to nothing as you can make it from a leftover scrap. However, I prefer the clip because I don't have to unbuckle my belt to put on/take off the pouch. In addition, it stays firmly attached to my side, won't flop around or stretch if it gets wet and I can clip the pouch to my front pocket if I'm not wearing a belt. I use this same clip on my cell phone cases; I've never had one accidentally come off my belt and unlike plastic clips, they won't break.
Step 13: Stitch It Up
Start sewing at the bottom of the flashlight-sleeve side of the pouch. Using waxed thread and leather needles, sew a saddle stich, doubling the bottom/first and top/last stitches. Stitching the flashlight side first will make it easier peek inside to ensure that your needle/thread passes through all three layers of leather. Check after every stitch and pull your stitches snug. Then stitch the other side again doubling the top and bottom stitches.
Wipe off any excess wax and flatten the stiches into the groove with a mallet. Not only does this make for a better look, but it also keeps the stitch thread from sticking out and wearing against your pants.
Step 14: Oh Snap!
Insert the Leatherman® all the way into the pouch so that it presses against the bottom. Fold the flap over the tool, pull it down tightly. Center it and press the leather firmly against the protruding snap. It will leave a mark on the underside of the flap. Check to ensure the hole will be centered on flap and punch a 1/8” hole; attach the snap using a snap-setter and concave anvil.
Oh, that hole at the bottom? It will allow the needle-nose of the multi-tool to extend out of the pouch when the tool is open. Handy when you are using the tool and need somewhere to put it, but don't want to fold/unfold the tool each time you pick it up.
Step 15: Edgy Guy
Apply Gum Tragacanth to all exposed edges with a small brush. Burnish the edges with an edge-slicker to compress the fibers and give the pouch a professional finished look. You can also use a piece heavy cloth (e.g.: denim or canvas) as a burnishing tool. After burnishing, apply matching edge dressing.
Step 16: Are You Finished Yet
Finish
Buff out the surface with a soft cloth and brush on another light coat of sealer. Allow the sealer to dry and buff again to a luster.
Step 17: Post Script
Post Script
There are excellent free how-to videos covering all of the leathercraft tools and techniques I catalog in the above text on the Tandy Leather website (http://www.tandyleather.com/en/free-leathercraft-instructional-videos.html) including casing, cutting, hole punching, attaching snaps, stitching, stamping, basket weave stamping, dying and finishing. I hope you find this Instructable so informative, useful and easy to follow, that you will reward me with your vote. Thank you for your time and attention.
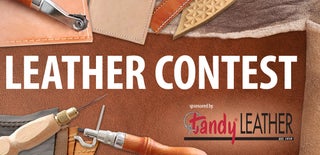
Finalist in the
Leather Contest
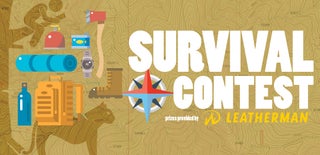
Participated in the
Survival Contest