Introduction: Ledge Style Gypsy Wagon
This Instructable shows how I built (a work in progress) my ledge style gypsy wagon. I'm a newbie at this site and this is my first post so please forgive me if I've done anything wrong.
Step 1: Design
I know it's not a classic wooden boatbuilders idea of design/build but I used AutoCAD. This turned out to be a very useful way of designing on the fly. Instead of lofting the entire design, I printed out specific parts at full scale on an as-needed basis, for example, when I needed to tilt my table saw blade to a particular angle. For other fitments, like getting the right distance between the sidewalls at the top I could obtain the correct distance on the drawing then use a tape measure for accurate placement. Worked well for me anyway.
Attachments
Step 2: Scrounging Wood.
I took the 5/4 cedar siding off this building to make 3/8" (or thereabouts) T&G siding. With no router table or shaper, I used a table saw; each board required multiple passes.
Step 3: Floor Framing
The floor framing is store bought 2x4's with the width milled to design dimensions (1-1/2 x 2-1/2 Inch). All framing connections for the floor and walls are glued butt joints using the Kreg pocket screw method.
Step 4: Wall Framing
Wall framing is 1-1/2 x 3/4 inch hand milled Douglas fir from a tree that I grew up with. It blew down in the Seattle area Inaugural Day wind storm in 1992. All sheathing is marine plywood, glued and stapled (1/4-inch crown staples) to framing. The 3.5 degree angle of the front and back walls had to be incorporated in the ledge riser.
Step 5: Angle Braces
I built the angle braces using dovetailed through-mortise and tenon joints. The shape was cut after glue up. Siding on the ledge riser was installed at this stage because of easier access. Framing for the ledge lateral is mocked up on one side. Final placement of ledge laterals awaited plywood sheathing top (1/2-inch ACX) and bottom (6mm marine).
Step 6: Ready for Sidewalls...But First
I decided to make glue-lam beams at this stage to confirm fitment of the two sidewalls. I lofted the 8-foot diameter circle and screwed gluing stantions along the curve. They looked pretty rough after glue-up but cleaned up really well with a hand plane. The glu-lams are made from six layers of 1-inch wide by 1/4-inch thick doug fir. They were plently flexible enough to bend over the curve. I used Tight-bond III, which is kinda flexible and the glu-lams sprung back a little upon removal from the gluing jig. "I'll figure that problem out later."
Step 7: Sidewalls and Endwalls
These show the sequence I used for wall installation. The sidewalls were temporarily braced while the endwalls were built. Siding went on over the marine plywood. It's beginning to look a lot like a gypsy wagon!
Step 8: Decorative Porch Roof Supports
I decided to carve the decorative supports before beginning the roof framing since the porch roof is integral to the rest of the roof. I have very little carving experience and after I did the first one, I had to make the second one's nose different because I was bored with carving. I used clear Alaska Yellow Cedar, which carvers claim to be among the best carving wood species. I can see why, it does carve easily and smells wonderful. The ears and tongues are made of scraps of marine plywood. I painted them with acrylic paint before final installation.
Step 9: Roof Framing and Construction
Since I wanted to include a mollycroft, I had to cut 6 of the 10 glue lams into thirds. That took some commitment! Framing for the mollycroft top was glued seperately and installed as one assembly. Bead boards were installed with stainless steel screws. They look really nice from the inside. The spacing of the glu-lams is equal to the width of the roofing panels because I wanted to be able to screw the roof hardware with long screws into the beams and not just the bead board. The horizontal brace in the last photo was used to hold the full-length beam to the correct curve (remember, they sprang back a little after glue up). This was not needed for the shorter ones associated with the mollycroft.
Step 10: Metal Roofing
The roofing material was commercially purchased. I wanted the ribs to conform to the roof curve rather than straight lines along the length of the roof so the panels and ribbing were fabricated to the design curve. The ends of the short panels were bent as part of the flashing using a low-tech, home-made bending tool. A lot of thought and effort went into design and construction of metal flashing for the mollycroft. Sorry, I don't have any pictures of that.
Step 11: Time for Trial Mounting Onto the Trailer
I designed and had built a steel frame that bolts to the floor joists and also to steel cross members of the trailer using grade-8 bolts. One design constraint was that I had to be able to get it through the garage door. I had about 1 inch of clearence. Whew! Looks pretty cute on the trailer.
Step 12: Door and Windows
Because of the 3.5 degree angle of the wall, I had to fabricate an angled door casing so the door could be plumb. While this complicates construction a lot, I think angled endwalls look a lot better than pumb endwalls (the endwalls and sidewalls were built at the same angle). I used oak veneer glued around a gluing form. Window frames are typical style/ rail construction. This is the front window, which is a casement. Two of the side windows are awning windows (next step).
Step 13: Painting, Exterior Finishing, and Glass
I used acrylic house paint over an oil-based primer. Exterior brightwork is polyurethane; beadboard ceiling is multiple coats of Seafin. The door glass etching was made by an art student in Bellingham but the work was contracted out by Seattle Stained Glass Overlay and I don't know his name. I wish I could acknowledge his work here because he did a beautiful job. The picture window was made by Seattle SGO using vinyl coloring and lead tape . I know traditionalists will not like this but that's the way it is.
Step 14: Wiring
There are three seperate wiring systems: 1) 12V running lights (LED) powered by tow vehicle battery; 2) 12V interior lights (LED), radio, and other devices powered by on-board battery and through battery charger/ control panel; and 3) 120V system (outlets only) powered by shore power. I used a 120Volt/ 30Amp charger/ controller.
Step 15: Mounted on Trailer and Exterior 90% Complete
Before mounting on the trailer, I installed 1-1/2 inch rigid foam insulation, then covered that with plastic. Was the vapor barrier a mistake? Please provide your opinion about a vapor barrier here. I'm all ears. The side clearence at the fenders is about an inch. In the photo, the wagon is suspended on camper jacks and the trailer is being rolled underneath. After installing electric brakes, I took it to a local weigh station. I estimate it's gonna weigh about 3000 lbs when done and loaded. Kinda heavy but my truck can haul it easily. In transporting it to the Seattle area, it rolled very well at highway speed.
Step 16: Interior, an Ongoing Project
Here's photos that show the interior, a work in progress. It's coming along but, frankly has languished a bit over the last year--too much else to do! The window trim is cherry that was given to me several years ago. The sink is made from Western Red Cedar and finished with thick fiberglass resin. The sink cabinet and chest of drawers (black walnut) are a work in progress as is the full-length closet, which is lined with aromatic cedar. The PlatCat heater (made near Olympia) is temporarily installed in it's own small cabinet. Paneling is 60-year old 1/4-inch CVG fir veneer plywood that has been through at least two floods and stored outside. I love it's distressed patina. It's finished with polyureathane. I even made the cushions but I've done lots of sewing and these were pretty easy to make. The lights are LED's and I made this fixture. Some people think it's a shower head because I used copper plumbing pipe. (You might need to click on the image to see the light.)
All for now. Thanks for your time in looking at my gypsy wagon. Please contact me through Instructables.com if you have any questions. After taking the 2009 gypsy wagon class at the Port Townsend School of Woodworking with Jim Tolpin and Steve Habersetzer, I thought I knew it all. They were a wealth of information. But there's no better teacher for me than experience. I spent a lot of time on the internet doing basic research regarding safe trailering; RV plumbing, wiring, and heating; and LED lighting. While I've been an amateur woodworker most of my life, I've never glued veneers over curved forms, never made a dovetail joint, and never used some of the construction techniques I learned at the PT Wood School. But it ain't rocket science. Just start cutting wood!
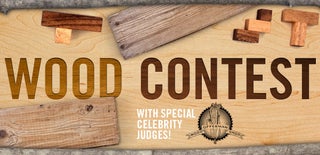
Third Prize in the
Wood Contest