Introduction: Live Edge Cherry Java Clock
What uses scrap live edge cherry wood, epoxy and coffee beans to make an awesome clock that also smells great? How about this very easy Cherry Java Clock for your next project? I had a piece of split cherry that was too beautiful to throw away, so rather than go with the basic "river" look with epoxy, I mixed it up and made this great clock and integrated everyone's favorite motivator... coffee beans!
For more great projects head over to Lazy Guy DIY!
Step 1: Here's What You'll Need!
I documented the entire build in the YouTube video so take a look and please subscribe to my channel!
Ready to make your own wall art?
Here’s what you’ll need outside of the tools I used in the video (*affiliate links to follow):
- Epoxy/Resin: East Coast Resin Super Gloss 1 Gallon Kit
- Acrylic Craft Paint: Deco Art 2oz Metallics
- Cheap Whole Bean Coffee 24oz
- Clock Movement: Mudder Maximum Thickness Clock Movement
- Ceramic Sanding Belt: Shop Smith P36 Ceramic Sanding Belt
- Water Proof Tape: T-Rex Tape
- Finshing Oil: Walrus Oil Cutting Board Oil
Step 2: Take Note*
Coffee beans actually float in epoxy. So if you want to get a look where the beans aren't all at the surface you need to space out your epoxy pours. Do a little the first day to set the coffee beans, then come back the next day with the bigger pour to get the best surface look. If you notice on my piece I did a little of both.
Also, the coffee beans do sand easily and you're essentially making coffee grounds. Wear a mask. Inhaling straight coffee dust, epoxy and cherry wood can't be good for you... but you'll work faster...
Happy building!
Step 3: Square Up Your Live Edge Wood
In order to make a clock face with the proper 12, 3, 6 and 9 time markers, you need to square up at least two edges of your live edge material. I used a makeshift sled and my table saw to cut the longer edge and then my miter saw for the shorter edges. Ultimately, you want to make a + sign in the middle.
Step 4: Build a Box
Before you pour your epoxy, you need to build a mold the size and shape of your clock to hold the project. I used scrap 1x3's and plywood. You will then need to seal your edges and gaps to prevent leaking. I use T-Rex tape because it's waterproof and holds up to the heat the epoxy gives off. Tape the outside and the inside surface where the epoxy will make contact. The oils in the coffee beans react slightly with the epoxy and make it seep and stick more to the mold than normal, so taping up the inside of the mold will help.
Step 5: Fill Your Mold
Pour your coffee beans (or any other sand-able object) and start filling with epoxy. I tint my epoxy slightly with just a drop or two of any type of paint.
Coffee beans do float, so if you want a layered effect then pour a small amount of epoxy the first day so the beans mostly stick to the bottom and then go back and pour the rest on top after it dries. You can see how this turned out in the picture.
Step 6: Add Some Flair
In order to add a marbled effect, I let the epoxy start to set for about 5 minutes and then I go back and add a few drops of paint or ink. I then gently swirl those through with a spoon. Do not mix.
Once the flair has been added, I make sure the piece is level and all bubbles are tapped out and then let it set to dry. Depending on humidity, depth of pour and brand of epoxy, dry time can take anywhere from 8-36 hours.
Step 7: Start Sanding
Once the epoxy is completely dry, it's time to start sanding. I use a combination of a belt sander and a random orbit sander to remove the over pour. For the bulk removal I use Shop Smith Ceramic 36 grit belts that really cut down on work time. From there I use my random orbit sander with 80 grit discs and work my way up to a smooth 220 grit finish.
Step 8: Prep for the Clock Movement
With the sanding finished, it's time to make room for your clock movement. I pre-drilled the hole for the clock post right in the middle, then on the back I'm able to trace the outside edge of the rest of the clock housing. From there I use a plunge base router with a downward spiral bit to remove the material to inset the clock movement.
Step 9: Add Your Finish
With the surface fully prepped, I added Walrus Oil Cutting Board oil as my finish. Simply apply a generous amount, then wipe off the excess and let it dry. I also buffed in a little of Walrus Oil Wax as well for a protective coat.
Step 10: Finish Your Clock
Once the oil has dried over night, add the final pieces of your clock movement, slap in a battery and set the time. Enjoy. You now have a unique piece of wooden art that looks great and smells great too!
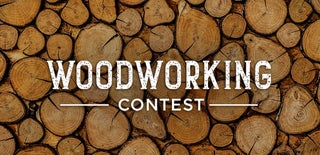
Participated in the
Woodworking Contest