Introduction: Mage Dice Tower: Lasercut and 3D Printed
We play a lot of board games around my house, and if you have kids, then you know what it's like to be fetching dice off the floor every few turns. So a few months back, my girlfriend and I started looking into dice towers in order to keep the dice from flying across the room.
I took note of different features like size, portability and level of complexity; yet they all seemed to look the same after a while. We never did find one that seemed like it really fit the bill, so that's when we decided to make our own.
Step 1: Sources of Inspiration.
We looked all around auction sites, local and online stores and made a list of the features we liked and didn't like. Once we had our list, we sat down to start designing our custom tower.
The dice tower we designed will have:
- Look like a tower that would be useful on a tabletop miniatures game, if it's going to take up table space, it might as well be multi-functional
- 6 sides instead of the typical 4
- The "drawbridge / dice tray" will be retractable
- Wanted to do a dual layer wall: plexi and wood, makes for better looking windows. But let's space the two apart to give it more depth.
- The central "tumbler" could be an interchangeable piece to allow for personalizing.
Step 2: Tools and Materials.
I've been working with the laser engraving machine at work for the last few years. So, we decided to use this and the 3D printer we had at the house. For me, I prefer to design the 3D parts in SketchUp, and then export them to the laser cutter / Corel (.SVG) and printer / Cura (.OBJ).
Tech Tools
- Laser cutter (Epilog mini)
- 3D Printer (Printrbot Simple XL)
Hand Tools
- Small saw
- Hobby Knife
- Hobby sized mitre box (Optional)
Software
- SketchUp - Design
- Cura - Slicing the model for 3D Printing
- CorelDraw - Cutting out the pieces on the laser cutter
Materials
- Plywood (0.2" thick oak ply)
- PLA (1.75mm Color of your choice)
- Plexiglass (Optix 0.08" thick)
- Dowel Rod (1/2" and 1/8")
- Felt (optional: use whatever type of material you like for the padding)
- Superglue (just use your favorite type)
A quick reference guide to laser settings on various materials.
Critical Notes:
Know how thick your materials are and the kerf (amount of material removed by your tool cutting). A simple set of inexpensive calipers can be invaluable for measuring how thick your chosen wood and plexiglass are. The laser also removes material when it cuts and can be a factor in making sure your joints fit properly. However, even if your joints are not perfect, they should be close and you can reinforce them with the glue.
Step 3: Where to Begin.
Note: I did not document the original project steps in detail, so as I build this Instructable, I'll also be building the model again and hopefully point out some key areas to help you save time.
I used SketchUp for the modeling of the tower because it's free and it's easy to export to the file types I needed for lasering and 3D printing.
I began by setting up my base shape. I made the sides of my hexagon 2" wide and the walls are 0.2" deep (Thickness of my plywood) by 8" tall. Making each piece a Component allows you to edit one wall and it changes each of the other copies for you.
Step 4: Detail Your Wall.
I took some inspiration from stain glass windows and medieval architecture and used that to rough out some basic arches.
Move another copy of your wall out away from your working model in order to make your adjustments. This allows you to work on a feature without everything else being in your way. I subdivided the space and then drew in arcs till I found a shape that I liked. I added some details and framing then removed the empty space to allow you to see through. There will be plexiglass walls inside these so it's ok to open these walls up.
Note: I use the general rule of: The thickness of the frame is the thickness of the material. Of course you can make the frames thinner, but this model was going to be handled by children, so I didn't want it to be too fragile.
Step 5: Add the Plexiglass Walls.
Since you have the shape you want in your wooden frame, simply use that for your plexiglass. Make a copy and then remove the empty space. Set the thickness to that of your plexiglass, mine was around 0.08". These pieces will be added on the interior of the wood.
The spacing between the walls is going to be about the same as the thickness of the plexiglass. I wanted them to be close, but not touching. Also, there needs to be a bit of space between the plates to allow for a finger joint to be added on the upper side later on.
Step 6: The Base Plate.
Make a copy of your base hexagon and move it down and away from your main model. You can again make this a Component and edit it easily. Make this piece 0.2" thick.
Clean up any extra lines that don't need to be there. Keep in mind that this is going to be lasercut and only keep the lines you need. The cleaner the model is now, the easier it will be when it's exported and prepared for cutting.
Note:Add something to hold all the pieces: make sure to add material where you need it. Generally I like to have at least three faces touching in order to have something to glue to.
Step 7: Add the Buttresses.
For this step I added a guide shape and drew lines out from the center in the direction I wanted the buttresses to point.
Extrude the shape half the thickness of the material in each direction so its evenly spaced.
Then take your shape move it around the hexagon and give it some curve.
Move your buttresses into place. You'll notice the overlap and simply edit the base plate to remove the collision spots.
Note: You'll also notice that the space between the pieces seems a bit thin. You can measure the space to get an exact number. On my first test cut, mine was left thin and eventually cracked and didn't hold well. You can solve this problem by splitting the difference between the two pieces.
Look at the areas the two pieces touch. Move half the buttress back and half the base forward. Do this for all 6 corners.
Step 8: Add the Tray / Drawbridge.
Choose one side, make the wall plates (wood and acrylic) unique. Shorten these by the length of the drawbridge. I chose 4.05" to allow for some clearance when the drawbridge is up.
Clear away the left over slot where that acrylic sat.
Add a rectangle where the tray will sit. We can modify it as we go. This part is made just like any lasercut box with finger joints. I made the walls 0.2" thick and 0.75" tall. Then, making each piece its own component, I drew in some design elements and finished it off with interlocking finger joints.
For the sides, an easy way to make them symmetrical is to make one and then, copy and scale in the opposite direction. Add in your finger joints by dividing up the space by the depth of your material.
Note: One trick to making very tight finger joints is to add a small fraction of an inch overlap to each face. Keep in mind the orientation of the cut and add the additional space appropriately. For this project, I decided not to add in this trick because I knew I would be dealing with a small surface area, and I didn't want the joints too tight because it may cause chipping. I settled for a slightly loose fit and compensated with the superglue.
Step 9: Reinforce the Drawbridge Mount and Add Pivot Pin.
During my testing of the drawbridge, I noticed that this mounting space was very weak and too small of a space to hold a pivot joint. By adding a bit more material to this area you can strengthen it and it will be a better platform to mount the pivot dowel rod on.
Start the pivot pin by making a circle half way along the seam between the base and the drawbridge. Make the hole all the way through the drawbridge sidewall. You can add in a temporary pivot pin to represent what you'll have to make later and also to allow you to retract the drawbridge.
Select the drawbridge and rotate it 90 degrees to the vertical position by using the guide pin. This will now show you what material on the base you'll have to remove for everything to clear.
Step 10: Adjust the Base.
With the drawbridge in the vertical position, begin removing the material from the base that is in the way. Once you have removed the minimum amount of material, take an additional 0.01" away from the inside of the space. This will allow the drawbridge to rotate with only minimal drag.
Double check your spacing around your drawbridge to make sure it can clear the base. Slightly rotate it and watch from multiple angles to see where it clips other items. The drawbridge sidewalls are clipping the base so we need to remove a bit more from the inside edge.
You may notice that the lower inside corner of the drawbridge would clip the table when it's rotated. I didn't feel that this would interfere too much with the operation, and could be adjusted for with a little sand paper if needed.
Step 11: The Model So Far.
The model shown so far and some of the early test pieces.
Step 12: Connecting Bracket Pieces.
So far we're using the base to hold the plates together, but there's nothing to keep them stable at the top.
In my initial testing of these pieces, it was tough to hold them together in a hexagon shape especially once we had 6 wall plates and 6 buttresses.
Using a view from underneath, we can trace out a shape that will hold the plates together. These need to have rather shallow reliefs to allow for easier assembly. Note:since we have thin pieces and will be using superglue, these joints don't have to be super tight or you won't be able to put it all together.
Trace out the corner and add 0.1" of material to the outside. Add 0.2" split between the bracket and the piece being held. Now set the bracket to 0.2" thick and you can move them into place.
I placed mine at the height of the upper window frame because there was more material there. At this point you'll need to go into each of the 5 connected pieces and remove the overlapping material. Use the bracket as your guide. Remember:Since you made each of these a component early on, you'll only have to do this a few times and not on every single joint.
Note:Make your guide marks on the pieces in the assembly, and then use your copies outside the assembly to do your edits.
Now copy your brackets around the assembly and place them into the slots.
Step 13: The Tumbler.
I originally planned on making slots for an angled plate to set into the outer casing. However, after a few test runs and a lot of different design changes, I settled on a "drop-in tumbler" concept. The concept is to make your casing into whatever shape you like and then your tumbler is a separate, unique piece that simply sets inside. This will make the final assembly much easier.
Begin by finding out exactly how much internal volume you have in your tower. Make a shape that fills up the inside. I use the inside of the brackets because the tumbler assembly would have to go in and slide past them. Now, make it a component and copy it over to make it easy to work on.
The simplest form of this, that I came up with, was a few plates and a base held together with a pole. Remember which side is your outlet for the dice.
Rough out your plates, base and center pole (1/2" dowel rod"). I made the original plates about 0.2" thick (planned on oak plywood), however, since we're going to be 3D printing them they can be thinner. Angles of 30 to 45 degrees seem to be fairly common. I chose a rough 30 degree angle for mine.
Once we have the tumbler done we can reference the main assembly again and see that there is going to be some conflict with the drawbridge. Just use the space within the base assembly where the drawbridge rotates, as your guide and then remove the excess.
Step 14: Little Added Touch.
After building the prototype, we decided to add a protective felt pad to the underside. Due to the odd shape of the base, lasercutting was again the best choice for the task.
Simply line trace the outside profile of the base and then set the trace aside for exporting.
Step 15: Begin Your Exporting.
Note on SketchUp 2016:When I upgraded to the latest free version, it didn't come with an export to 3D model (.OBJ) or anything for a .SVG file. Simply install your preferred extension from the Extension Warehouse.
Begin by going through each of your parts and exporting them to a new folder for both printing and cutting. I named each piece and included the material to be used in the file name to make sorting easier.
One thing I found to make exporting to .SVG easier, was to select just the face of the object I'm exporting. If you have each piece separated by itself, then you can select exactly what you need and not having extra geometry to hassle with simplifies things.
Step 16: Lasercut Wood Settings.
The wood I chose was simply Oak plywood from a chain hardware store. I've had fairly decent results with it and I don't mind the slight char to the edges. Cost versus convenience was the largest factors for me.
Note:I'm not advocating one laser engraver over another, however, this is what I had to work with given the equipment my shop had purchased. So all my settings will be based on this particular machine.
For my main testing tower, I chose not to include any rastered graphics for the faces. I chose to keep it simple and work out the design and functionality.
Laser Settings: 60 Watt Epilog Mini
Vector Speed: 25
Vector Power: 100
Frequency: 350
Helpful Tip for Any Project: When you know that you will be making multiple passes, you can make duplicates of your shapes and stack them. The number of copies in your stack should be the number of passes you need. For example: you need to make 3 passes, then copy and paste your parts twice. When you draw your selection window around your parts you will have three copies, and your laser software will read it as three cut paths.
Critical Note!!!:
I've done a lot of looking around at other peoples' settings, and frequency / ppi seems to be one of the biggest things people don't say much about. I wondered for quite a while how others were cutting so clean until I sat down and experimented with frequency. It really impacted the quality of my cuts.
Step 17: Lasercut Acrylic Settings.
Again cost and convenience were key, so I chose some basic acrylic sheets from that same chain hardware store. It's simple and easy to work with and the fumes dissipate within a few hours left in open air.
Laser Settings: 60 Watt Epilog Mini
Vector Speed: 15
Vector Power: 20
Frequency: 5000
Step 18: Lasercut Felt Settings.
Just a single light pass is all that is needed. Since the felt was a synthetic material it melted the edges cleanly.
Step 19: 3D Printing Settings.
One of the things I had to contend with, when designing the tumbler, was I had to design something I could make. I have a rather small printer with a limited build plate. So I chose to break up the model into separate tumbler plates and print them individually. The times were still reasonable and I was pleased with the results.
Note: I did run into a problem with my lower tumbler plate being slightly too large of my printer. It wasn't too bad and I only had to reduce my plate size by 0.02%. Still functioned as it should.
Slicing Software : Cura 15.02.1
Printer: Printrbot Simple XL
PLA: 1.75mm
.3 layer height
20% infill
The overall settings weren't too critical due to the nature of the project. Just use something that works for you.
Step 20: Some Handmade Pieces
For the pivot joint on the drawbridge, and the center rod and pins of the tumbler, we need to cut a few pieces of dowel rod.
For the pivot joint and base pins we used 1/8" dowel, cut six pieces to 0.4" long. Also we cut one quarter out of two of them to allow for a flat edge to be super-glued to the base plate.
For the center rod of the tumbler assembly we cut a 6" piece of 1/2" dowel.
Step 21: All the Pieces.
I've laid out all the pieces used for the tower build. After a few test fittings, and double checking, we'll begin assembling the tower.
I did add a light stain and shellac to give the wooden pieces a little more appeal.
Step 22: Assembly - Base Plate Pins.
I should have done this step earlier in my build so I'm adding it here to save you some time.
Take the main base plate and the four straight pins. Thoroughly glue the pins into the holes making sure they are flush with the underside of the base. Make sure to set them straight to make it easier to slide the tumbler into place.
Step 23: Assembly - the Walls.
Begin with the large base plate and the plexiglass window panes. Gently slide the panes into the slots of the base. Keep the underside flush and file down any edges of the base that prevent the plexi from sitting properly.
After the plexi is in place, you can begin adding the brackets and walls. Fully seat one bracket in the notch of the windows, and then slot in a wall piece on each side. Add a small drop of CA glue to the lower edge of the wall to keep it from flopping around on you.
Continue around the perimeter adding one bracket and then one wall. Leave the small window for last, this one will be slightly more difficult to manipulate. You'll need to add two brackets, the small window pane, and the small wooden wall all at the same time. Work gently, but firmly, and each piece will seat nicely.
Step 24: Assembly - Buttress.
This step is straight forward. Place the buttresses into the slots in the bracket and the base. Some slight filling may be necessary.
*Hint* The tack glued edges can be broken free to allow the tower to flex a bit more if needed.
Step 25: Assembly - Drawbridge.
Take your four drawbridge pieces and glue these together. Take some time to glue the inner edge and leave a nice finish on the outside.
Note: the left and right walls are interchangeable.
Next we'll add the drawbridge to the rest of the tower.
Take your drawbridge and the two quarter cut pins. Insert the pins into the holes of the drawbridge. You may need to do some light filing to get the faces of the quarter-cut and outer face of the drawbridge to be flush.
Set the drawbridge into the space of the base assembly and make sure the flat face of the pins is even with the base. Rotate the drawbridge up and align the front edge. Tack glue often to help hold them together.
Hint: You can remove the buttresses on this side to give you more room to work.
Step 26: Assmebly - Tumbler.
Beginning with the tumbler base and the 1/2" dowel rod. Set the dowel into the base and make sure it sits as close to perfectly straight as possible. (use whatever means you wish; squares, blocks, etc..)
Add the large lower tumbler plate to the rod. Simply slide it down into place and tack glue it. The angle should be around 30 degrees. Be as exact as you wish, the plates will still work with a fair amount of deviation.
I found it easier to continue to the upper tumbler plate. Setting it to the 30 degree angle and making sure the upper face of the dowel and the top edge of the plate were even, add a small drop of glue to hold and make your checks. (Apparently I didn't get a good picture of this step).
Note: After a few test fits of the tumbler into the tower, I filed out the holes in the tumbler to ease placement.
Add the middle tumbler plate in the same manner as the upper. Lay the tumbler on edge, split the distance between the upper and lower plate, and tack glue once you have the angle. I would strongly consider some guides, or jigs if I were doing more of these.
Once you have all the pieces fitted the way you need, finish out with some heavy gluing.
Step 27: Assembly - Finishing Touches.
At this point, you can go around and finish up any edges that need to be glued. Do this to your liking. I have small children who play with the towers, so I added a fair amount of glue.
The addition of the felt on the base helped cover the unsightly seams and also protect the tabletop surface. Also, the felt we chose had an adhesive backing which helped secure it in place.
Step 28: Finishing and Testing.
Once the tower and tumbler are complete, it's time to test fit everything one last time before turning it over to the kids. I added a picture of the original one (orange) and the one used to make this tutorial (blue).
Step 29: Final Notes
I'd like to thank you for making it to the end of this instructable. I tried to include as much of the details as I could in case you decide to build one yourself. I may include the files for this build in the future updates, but for now I would encourage you to try and design your own. It's very rewarding to see something turned from a digital model into a real life object.
Feel free to post any questions, comments, and/or concerns. I will do my best to answer them.
Full Spectrum Laser Contest Entry:
I'd like to begin this section by thanking Full Spectrum Laser and Instructables for hosting this contest. I hope to have shown that we would give a H-Series laser and a Pegasus printer a good home and plenty of use. We would like to move into some more production runs of this tower and also expound on the idea of the tumbler insert.
Our current laser being used is owned by the company I work for, and it comes with limited time and use restrictions. Having a personal laser to use would greatly expand our experimentation and would speed up the concept to product timeline.
We have already been pushing the limits of our printer and have been working around them. However, we have still not been able to produce the quality and complexity of items we would like to showcase. We have several concept ideas for more complex tumblers; but given the limits of a FDM printer and the excessive waste for support material, these ideas are slower to come forth.
Thank you again for the opportunity to enter and compete.
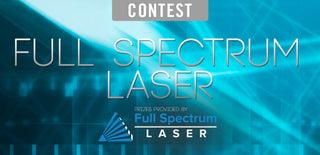
Runner Up in the
Full Spectrum Laser Contest 2016