Introduction: Make a Ray Gun
When I started building this project, I was just mucking around on the lathe trying to make a hand grip of some sort, I really didn't have any further plans. But then I thought I should do something with the thing I had made, so with that thought in mind, I combined my love of classic sci-fi design and the fact that I had a handle that could be made in to that of a ray gun, and I decided to build just that, a ray gun. I then thought that it would be cool to record my build and chuck it on Instructables just to see what would happen, so that's what I'm doing now.
Step 1: Tools and Materials.
Tools:
- Lathe
- Woodturning tools
- Sandpaper
- Woodsaw
- Hacksaw
- Files
- Chisels
- Pencil
- Rubber (eraser)
- Vice
- Hobby engraving tool (dremel)
- Staple gun
Materials:
- Wood (it really depends on how you want your gun to look in terms of grain and colour, to what type of wood you choose to use.)
- Pieces of dowel
- Wood glue
- Super glue
- Small spring
- Paper (for design, unless you just want to freestyle.)
Step 2: Starting With the Handle. (Part 1)
I found a branch off a tree that was cut down ages ago, it seemed good enough for what I wanted to do, so I cut it to size and put it on the lathe and started to turn it.
I got it so it was round enough for me and I started to sand it. I wanted to keep a bit of the bark on the wood just to add character, so I made sure I didn't keep turning it until the wood was perfectly round. I sanded it then because it would've been harder to sand after cutting the grooves in the handle.
I then went ahead and drew up a design for the groves in the handle, you could probably skip this step if you want though, because I mostly did it freehand anyway.
In order to get the grooves, I offset the piece of wood in the lathe. It was way quicker than using a file, but I would just say that maybe it's not the best idea. It made the lathe jiggle around quite a bit, as you would expect, but still, I think it put more stress on the motor than I probably should have put on it. So I mean, do it at your own risk.
The lathe left the wood a bit rough after offsetting it, so I went over it again with some sandpaper.
After all that, I realised that the fourth groove wasn't actually necessary because your forefinger should be resting beside the trigger, rather than gripped around the handle. So with a bit more sawing and a little more sanding I took off the end and fixed it all up.
Step 3: Making the Body.
So, again I started out with a piece of wood, and again I put it on the lathe, but now that I had more of a plan building in my mind, instead of just messing around on the lathe, I started making a slightly bullet-shaped body for my ray gun.
This step was pretty straight forward, I just made one end taper more that the other, and I left the middle part flat-ish, so that I didn't have to do crazy angles for the handle when I attach the two (if that makes any sense, sorry.)
I then had to trim off both the ends that were left over after I had the shape I wanted. I used a hacksaw for this, just because the cut is cleaner than that of a normal woodsaw. After chopping the ends off, I left the front end (the narrower end) pretty much just how it was when it was cut because I knew I had to attach the ray gun "laser" later. On the fatter end, I just used a file and some sandpaper to get the curve that I wanted.
Also, as you can see, I used a flannel to pad the vice when I was clamping the wood in place to work on it. It was just so the vice didn't bite into the wood, leaving dents.
Step 4: Making the "laser."
To be honest, I don't really know what to call the thing sitting on the front of a ray gun, so I'm going to run with laser for now, but if you guys know what they are actually called or if you can come up with a better name like "static electropulse array" or something, then it would be awesome to find out your thoughts if you put them in the comments.
Anyway, yet again I started with a piece of wood, which I cut to size and then proceeded to turn on the lathe. As the lathe was spinning, I used a pencil to draw where I wanted to make the cuts, this was so I could measure the distance between each ring and make sure it was all uniform.
The rings were the easy part, it is the ball on the end that gets hard. The hardest part is making it decently shaped, as in, not too stumpy, but not too skinny either. It might pay to practice doing spheres on another piece of wood, since you can't un-turn wood, or you could just have a crack at it first shot and you might nail it. I think the trick for me, is imagining the sphere beyond the cut, so that you don't end up with a flat nose. Give yourself some room to sand/file back the nose.
The only power tools I used in this whole project was the lathe and a hobby engraver tool (dremel). The engraver was really handy just to speed up some of the sanding and to get more intricate shapes when doing detailing. The sanding attachment on the engraver left the wood a bit rough still, so I went over all the areas I sanded with a finer grain sandpaper and it smoothed it all out.
Step 5: Making the Handle. (Part 2)
In order to get the handle to fit properly to the body, I knew I had to do some intense hand-filing/sanding. Then I had a thought though, what if I attached some sandpaper to a piece of wood that I had already turned on the lathe and used that to sand the groove? So that's what I did and it worked perfectly! I just used some staples for the edges and a bit of super glue to tack down the middle of the sandpaper. I'm sure there is an actual tool out there that you can use to get this kind of curve, and if you have it, then use that, but for other people like me who don't have very many specialty tools at their disposal, then this is an adequate solution.
I used the saw to cut a line part way down the middle of the handle as well, just to guide the sanding a bit. Also, as I'm sure most of you are aware or at least could guess, the wood heats up quite a bit when you sand one particular spot, which can lead to burning and cracking of the wood due to it being dried out. I usually have to wait a while to let it cool between sanding, but this time I just thought why not chuck it in the freezer for a bit to cool it down faster, so I did.
For those who are wondering how to get the curve in the handle to match with the curve of the body, then I suggest testing it regularly by fitting them together until it fits perfectly snug, at least that's what I did.
Step 6: The Trigger.
You have two options when it comes to making the trigger, do you want the trigger to move, or do you just want it to stay in place. The benefits of making a trigger that doesn't move is that you are less likely to stuff up your lovely workmanship that you have already put precious hours into, and it is way simpler and it takes less time to make, the downside is that it doesn't feel as fun to play with, but if you were going for just a shelf model that doesn't really matter. The benefits of a moving trigger is that it feels way cooler. I wanted to challenge myself and make the trigger move so I went about thinking of a way I could do it, and this is what I came up with.
First, I took one of the offcuts of the wood I turned, and I cut it into a manageable shape. Then I drew the shape of the trigger on the wood and I started filing again until I got the right shape for me.
When it was all looking good in terms of shape, I started to drill the holes for the small piece of dowel and for the spring, one thing to keep in mind is where the dowel is in relation to the spring, making sure that the dowel (pivot point) is in between where the finger actually pulls the trigger and where the spring is. I didn't think about this the first time I drilled the hole for the spring, so I had to re-drill the hole at a different angle in order to get the leverage, as you can see in the photos. Fortunately for me, I left enough room on the top of the trigger to make this adjustment.
Step 7: Assembly.
The first thing I put together was the body and the laser. I drilled two holes, one in the body and one in the laser, then I inserted a piece of dowel in the holes, made sure they lined up and then used some glue to set them in place.
After that, I held the handle and trigger in the correct position on the body and I drew the marks where they should be.
Next, I chiseled out a hole to fit the trigger in. I started by drawing the outline for the hole, notice the little slots on the sides, that's for the dowel in the trigger to pivot on. I then drilled multiple holes inside that outline just to start off the chiseling. After a little testing and adjusting I could slot the trigger right in place and it was working just how I intended it to work.
The next thing I did, was mark and drill the holes for the dowel used to attach the handle to the body, I had to angle it a little bit so just make sure that you are using the same angle for both holes in both pieces of wood, also make sure that the holes are the same distance apart, you know, basic common sense and stuff. After a little bit of adjusting, the dowels were ready to be glued in place.
I had pulled the trigger out earlier, just to avoid breaking the trigger while I was still working on the rest of the ray gun, so after re-installing it, the entire ray gun was complete!
Step 8: Done!
Now you can be sure of your safety, knowing that you have this to protect you. Or you could just use it as a cool ornament, you pick.
If you guys did like this, I'm entering it into the woodworking contest and I would greatly appreciate a vote or two!
Thank you all for taking your time to read this, cheers.
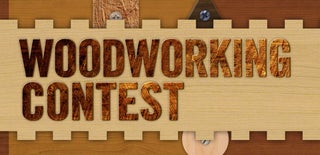
Participated in the
Woodworking Contest