Introduction: Make Awesome Soap
This is the process I use to make awesome custom soap.
My wife and i have made custom soaps as favors, gifts and fundraisers.
I order my soap making supplies from http://www.elementsbathandbody.com/
We use melt and pour soap bases along with fragrance and colorant.
I get my mold making supplies from http://www.smooth-on.com/
oomoo series silicone are very easy to use for beginners but the mold max series silicone tend to have a longer life.
Step 1: Design Your Part
I have used quite a few different methods to create my original pattern. Sometimes it has been handsculpted from clay, carved from wax and i've even used an existing dog toy as a pattern for a soap mold.
For the purposes of this instructable i am going to show some computer generated models.
I start by importing a flat drawing in to solidworks and then trace and extrude the details that i would like to be present in the final part.
This is a little different than how i would typically build a 3d model because i am only interested in a single surface and not the full object in the round.
This will allow me to create simple slop molds that work like and ice cube tray to produce bars of soap.
Step 2: Patterns and Mold Making
In the case of the Citroen soap model, i output the cad file to an objet 3d printer to make my first part.
Because of the viscosity of the soap and the fact that this is unpressurized molding it is not necessary to do any post printing cleanup or sanding on the 3d printed model, a mold can be taken directly from the print. This may not be true if you are using a 3d printer with a lesser resolution.
I first make a single cavity mold from the print and then replicate it a few times in smooth cast resin.
I'll then use the multiple resin pieces to create a multi-cavity soap mold to build in much higher efficiency during my molding process.
Step 3:
Once the molds have cured it's pretty straight forward.
Melt and pour soap works exactly as it sounds, you can melt it in a double boiler, i prefer the microwave.
Many of the soap bases are delivered in 1lb bricks, i designed my parts and molds to use exactly 1/8th of a pound per bar and 1lb per mold set.
a 1lb brick of soap fits perfectly in a 2cup glass pyrex measuring cup.
I put my bar in my measuring cup and melt it in the microwave for approximately 3 minutes.
Then add scent and colorant and mix with a wooden popsicle stick until smooth and then pour in to my molds.
As i pour my molds i stack them on a cookie sheet and when they are all full i transfer them to my freezer to accelerate the setup process. it is important to note that if you do this, the soaps will bleed moisture when they return to room temperature and will need to be left to air dry before they can be packed up. The cure time for my soap molds in my freezer is about 45 minutes.
Step 4: Demold and Package
You can get very creative mixing different colors, scents and soap types at different stages of cooling.
I've included some images to show the variety you can achieve.
Since my soaps are detailed and not simple bars i like to package them in simple poly bags to make sure they are fully visible.
I get my poly bags from uline and then staple on a header card that lists the soap type and scent.
Step 5: Some Other Soaps We've Made
Last Christmas we made some festive soaps.
A holiday cat character designed by my wife and some large christmas lights that were molded in a two part mold and finished by dipping the bottom portion in to a second color soap.
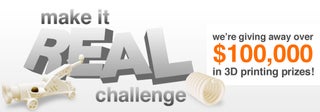
Participated in the
Make It Real Challenge