Introduction: Make Drawer Pulls Without a Lathe
I recently was near the end of making a bandsaw box for my wife, and I needed drawer pulls. At the time I didn't have a lathe and I didn't want to run up to town and purchase metal pulls. I had the idea to chuck some wood into my drill press, and use files to shape it. After trying that, I quickly changed direction and instead used a hand-held electric drill and the process I detail in this Instructable.
Feel free to watch the movie to see the process in action. Please ask questions or make suggestions for how I might improve the Instructable after you have read through it!
Step 1: Gather Tools and Supplies
Tools/Supplies Needed:
- Small pieces of beautiful hardwoods (and some means of cutting them square)
- Various diameter dowels – I used 1/4" and 3/8" dowels
- An electric drill
- Drill bits the same diameter as your dowels
- An assortment of sandpaper
- Wood or CA glue
Optional, but recommended:
- Electric belt sander
- Electric spindle sander OR sanding drums for a drill press
- Vise (to hold the drill)
Optional:
- Drill Press
- Hand Saw
- Hole Saw
Step 2: Prepare the Blanks
Cut down some scraps of wood so the top profile is either square or round, and the height is a little taller than the desired finished height of the pull.
For the square pulls, I used a little jig on my table saw sled to cut these. For the round pull, I used a hole saw chucked into my drill press with the center drill bit removed. If you do this, be sure the work is clamped down!
The grain can really run any direction you want, depending on the look you are going for. The smaller square pull has the grain running up the piece (so the end of the pull is end grain), and the other two pulls have side grain on the face.
Step 3: Drill a Hole in the Blank
Choose the final orientation for the drawer pulls, and mark the center on the bottom of the piece (Easy to get mixed up!). Use an awl or a sharp screw to start the hole for your drill bit.
Using drill bits that match the diameter of your dowels, drill holes about half way or more into the pulls. Use the largest dowel that will both fit in your drill and in your final pull design. The thinner the dowel, the more likely it will be to break during the next process.
You don't need to use a drill press, but do your best to drill this at 90 degrees to the piece. If the hole ends up crooked, the bottom of your pull will not be flat.
Step 4: Cut and Glue the Dowels
The dowels will both be used to hold the piece in the drill, and later in the process will be cut shorter to form a tenon for installing into the final piece.
Mark and cut the dowels to between 1 3/4 and 2 inches. Don't skimp here, as you'll want your drill to have a good grip on the dowel. If the pull ends up sticking too far out of your drill, you can always cut the dowel a little shorter.
Using super glue or wood glue, glue the dowels into the pulls. I used a mallet to make sure they were seated well. If you end up using super glue, using CA activator will set the glue faster so you can keep working.
Step 5: Trim Larger Pieces
On the smaller diameter pulls, you don't need to bother trying to make the stock round. However, if you are making a larger diameter pull like this 1" block of wood, it will save you some time at the sander if you cut a way some of the excess first. That being said, with a steady hand you can just do this at the sander!
I used a washer to give me a general idea of what to cut away, and then a pull saw to remove the material.
Step 6: The Fun Part…
Insert the dowel and pull into the drill and tighten the chuck.
Now comes the fun part…
Once you have safety gear in place, plug in the drill and turn on the sander.
Slowly bring the spinning blank into contact with the sanding belt. Be sure to have the drill rotating the opposite direction of the sanding belt so you can maintain control easier. It doesn't take very long with this approach to get the pieces fully round. (The thinner pull pictured went from fully square to round in less than 30 seconds)
You don't need a power sander, but if you try this technique against a piece of sand paper be sure to keep moving the drill so you don't wear a spot in the paper. It obviously will go much quicker with an electric belt sander.
Step 7: Continue Shaping
Continue to shape as you see fit on the belt sander. Depending on the shape of the pull, you may be able to do all the primary shaping you need at the belt sander. The odd groove you see me making in the second photo is to save time on the next step at the spindle sander.
Step 8: Get Creative With the Shaping
To get some more of the natural curves, I recommend you switch over to a spindle sander. Since the spindles are spinning and moving up and down, it helps remove material quickly without burning.
Alternatives: For years before getting this machine, I just used sanding drums chucked into my drill press as my make-shift spindle sander. Be creative in how you find ways to shape these pulls! You could use curved files or even sandpaper wrapped around a dowel to assist you.
Step 9: Fine-tune the Shape
This part of the process is entirely up to you!
On two of the pulls, I added a slight dome to the front of the pull back at the belt sander. I wanted until this step so I knew I had my inside curves correct first – but it probably could have been done in a different order.
Step 10: Move Through Higher Grits
Shortly we'll transition to sanding with paper, so move through any higher grits you have on your spindle sander before continuing. You can also do this on the belt sander, though depending on how hard it is to change the belts, it might not be worth it.
Step 11: Prepare the Drill for Hands-free Use
With the drill unplugged, use painters tape to keep the button pressed.
Clamp the drill in your vise so the piece is parallel to the ground - supporting the drill as needed. Next, use something with a power switch like a surge protector to plug in the drill so you can turn the power on and off without needing to plug in and unplug the drill to control the power.
Make sure the drill is secure before turning it on.
I expect you could perform the following steps holding the drill with one hand and the sandpaper with the other, though I have not tried it myself. However, in my opinion, having the drill running hands-free makes the following steps easier and more like using a real lathe.
Step 12: Sand and Finish
Grab an assortment of sandpapers of various grits. I ended up with 220 through 2000 grit. Take your time on the lower grits and have fun with this process, stopping as needed to check your progress. You'll start to see a natural shine come out as you work toward the higher grits.
Depending on your finish, you may be even able to apply that at this stage as well. I've never applied a CA glue finish, but I suspect you could even apply that with this method.
(Finished picture is shown first)
Step 13: Repeat for the Other Pulls
I used a homemade beeswax and mineral oil blend on these pulls. I love applying finish and getting that first glimpse of what the finished pull looks like. This is especially true with exotic woods like this Bocote!
Step 14: Cut the Tenon
Once you are fully happy with the shaping, decide how much of a tenon the drawer pulls need and cut them free from the rest of the dowel. For smaller pulls, a 1/4" tenon should be enough glue surface for installing into a project.
Step 15: Finished
At this stage your drawer pulls are done and ready to be added to your project! Or, if you just enjoy making pulls – you can keep practicing!
Step 16: The Bandsaw Box
If you recall from the intro, I used this technique to make drawer pulls for a bandsaw box I made for my wife. The box is walnut and baltic birch with zebra wood pulls. This bandsaw box is a design by David Picciuto included in his Bandsaw Box Book.
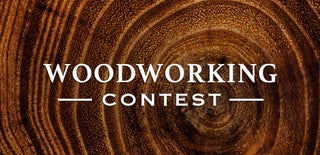
Runner Up in the
Woodworking Contest