Introduction: Make Your Own Lego Motor Case and Shaft Adapter
In this instructable I will be covering the motor casing and shaft adapter. The circuit for power and control I will leave for another instructable but I will answer most questions in the comments.
In the last page I will discuss some of the things I did to make my design more durable and user friendly.
Step 1: What Do We Need?
Everybody loves Lego's right? My kids have (and by my kids I mean Myself as well) all kinds of them. Bricks, plates, axels, pins, connectors, spacers, gears, pulleys, etc... But no Lego motors. There's only so many times you can make a crank and spin something by hand before you start to look at motorized toys with envy. Well, Lego motors sure are nice, but they can be kinda pricey and I don't care for online shopping, but I do have a bunch of hobby motors from old cannibalized toys, a dremel tool, and a hot glue gun!
So let's make our own!
Here's the parts:
-Standard DC hobby motor (just about every cheap moving toy on the planet uses them, but you can buy them separately too).
-Plastic gear (usually comes on the motor in the toy).
[Any scrap of solid plastic could do in a pinch. As long as it's about the same size as that aforementioned gear, we'll be sanding it into oblivion anyway. You could even use a section of Lego axel.]
-Lego parts in the picture for this step. You may substitute parts, they don't have to be these exact ones.
-Battery pack (I use 4 AA batteries to make about 6V supply, which is typical for these motors).
-NOTE: The standard operating voltage range for these motors is between 3 and 9 volts. Outside of that range will either be too weak to drive anything, or risks burning up the motor.
-Wire (I used twisted pairs from an old Ethernet cable as they're flexible and fairly durable).
-Switch or controller of some type. Or just touch/tape wires to contacts
Tools and materials:
-Small clamp.
-Dremel tool with sanding drum (files or sand paper will do, it'll just take a bit longer).
-5/64 inch drill bit.
-Hot glue gun with a couple glue sticks.
-Super glue.
-Paper tape, AKA Masking tape.
-Exacto knife or other fine blade (could use file for the step needing this).
-Soldering iron and solder.
Step 2: Assemble Your Bricks.
The base is your 4x4 stud plate. Place the 2, 4 stud long bricks (stacked) on one side of the plate.
The opposite side will be 2 bricks tall by 3 studs wide of bricks. I didn't have 2, 3 stud wide bricks so I used one and then a 2 stud wide and a 1 stud together. It really only matters that that wall is 2 bricks tall by 3 studs wide. (If you didn't already know, a brick is 3 'plates' tall).
The grid plate will need to be modified just a bit.
Step 3: Completing the Housing
About that grid plate (the 1x2 flat lego piece with the lengthwise slots pictured)...
You don't have to have the grid plate but I like to enclose as much as possible and the 'grid' makes it easy to cut in this step.
With your knife, take a small notch out of one of the long sides of the plate. Here's what this is for; on the Lego connector pins, there is a little collar in the middle, this notch gives room for that collar without rubbing on it.
After putting that in place just collar the top plate as shown (it's bottom side up and above the housing assembly in the pic).
Step 4: Shaft Adapter
This is the critical piece here. The shaft adapter allows us to tightly pressure fit on a Lego coupler pin (it's a cylinder on one half and a plus cross-section on the other, usually grey colored) on the motor shaft. You could forego the rest of this instructable to make your own motor mount and just use this method for the adapter.
Sanding the shaft adapter while the motor is powered (shaft spinning) makes it easy to ensure its concentric with the motor shaft so any Lego attachments placed in it won't wobble.
Pictures, in order of appearance:
1) Hobby motor shaft diameter is .078 inches. It just so happens that a 5/64 inch drill bit is a few thousandths less than that. This is perfect because it'll create a nice pressure fit.
2) If your using the plastic gear, you can skip the step with the drill bit as your gear already fits, leave it on the motor shaft.
-However, if your using a scrap of plastic, this step is for you. The plastic piece I'm using here is the front wheel alignment knob from a cheap RC car I harvested. It already had a hole just a bit smaller than what I needed so I was able to drill it by hand.
-All you need is a solid piece of plastic about the size of a small pencil eraser. A drill press is handy because you can drill a nice straight hole without the bit 'wobbling' and making it big or uneven.
-Drill your hole all the way through the piece.
-Slip the part onto your motor shaft. Slide it until there's only a small gap (about as thick as your fingernail) between it and the motor body.
3-4) Clamp the motor to the edge of your table as shown. Tighten your clamp just to the point that the motor won't move easily, you can make it a bit tighter later if needed. If your too tight, you could warp the motor body and keep it from moving or damage it.
-Get your Dremel rotary tool ready with a sanding drum, medium speed is enough here.
-Connect your motor to your DC power source, 6V to 9V will turn it well against the rotating tool. Make sure it's spinning the opposite direction of your tool or it won't take off any material. Meaning that the side your sanding on is moving opposite of the side of the drum your sanding with.
-I used my Exacto knife and Dremel with a cutoff wheel to trim the part flush with the tip of the motor shaft.
5) Keep your sanding drum parallel to the motor shaft.
6-7) Sand it down a bit, see if the Lego pin slides on, rinse, repeat as necessary. In picture 6 our adapter is almost the right size. Don't force your pin on, all you'll do is either split your pin, or at least make it not spin concentric to your motor shaft. It won't last long with the kids either way.
-Pic 7: Once your pin slips on snug, but without forcing it, you're done.
-Slip your adapter off the motor (remove the Lego part first) and put a tiny drop of superglue on the tip of the motor shaft (make sure the motor shaft is clean of any grease or debris first) and QUICKLY slip your shaft adapter onto your motor shaft in the same position as I mentioned before. Yes, you'll probably glue it to your fingers a bit, it's nearly unavoidable with super glue to do so, you'll live.
-You may glue the Lego pin on if you like now, I don't just in case it breaks or bends. Also, not gluing the pin on is a designed point of failure for safety. If the kids get something bound up or put too much force on the shaft this pin can come off minimizing damage to the motor.
Step 5: Assemble Motor With Housing Assembly
Now we need to put the motor into the Lego housing we created. (The numbers correspond to the pictures of this step, in order)
1) You will notice in the first picture that theres a significant gap between the motor and inner wall of the housing assembly, we need to close that gap. Get your masking tape out.
-You need a strip of masking tape not more wide than the metal body of the motor is long.
-It will take about 5 layers of tape wrapped around the motor body to fill the gap evenly.
2) Take a flat plate 4x6 or longer and attach the housing assembly on top at one end. This is temporary but essential to ensure motor alignment.
2) Now put a black Lego connector pin on your motor shaft. We use the black one here because they are made to fit tightly in the Lego holes. This will help make sure our motor lines up well for gluing in place. This piece is temporary.
2) Here you see I've put a 1x4 Lego Technic brick (the yellow brick with the 3 holes through it) on top of a 2x4 brick lengthwise. It doesn't have to be 1x4, can be longer if you like but I don't like to use the 1x2 brick with only one hole because they don't always hold the motor in place as well. This is temporary.
3) Snap the black connector pin (that's on the motor shaft) into the center hole on the yellow brick.
4) Place the motor into the assembly as shown, snapping the bricks on the shaft onto the long plate that the housing is on as well. Now the motor is lined up just right so that gears and other parts will line up according to Lego dimensions once were done.
5-6) Is your hot glue gun warmed up? I love hot glue, it can be permanent or temporay, insulates and fills in gaps, is stiff but pliable, very versatile.
-Make sure you don't put glue in any holes in the motor casing or too close/on to motor shaft as this will impede motor operation.
-Don't detach the motor or any bricks at this point, make sure all the bricks are tightly together.
-Put some hot glue first under the back of the motor. My glue gun is aimed there in pic 5.
-Apply along the sides of the motor. We aren't putting any glue on the top of the motor or on the shaft end yet.
-Wait about 30-60 seconds for that glue to cool.
-Remove the long flat plate that the housing assembly and shaft support are attached to.
-Remove the shaft support and black connector pin from the motor shaft. Make sure the shaft adapter is still in place.The motor should stay firmly in place at this point.
-Apply glue at the shaft end in the gap where the shoulder of the motor housing is. Remember not to get any glue on the motor shaft.
-This is the point where you would want to solder your wire to the motor contacts. Leave those capacitors in place (if present). Their function is to smooth out electromagnetic interference (EMI) produced by the motor in operation. If your motor doesn't have them don't worry, it'll still work fine.
7) Move quick here!
-Before the top goes on lay down a thick bead of glue along the top shoulders the motor, lengthwise, filling in the gap.
-Now a bead on the to of the motor, lengthwise.
-Put your housing top on quickly and apply firm downward pressure on the top for about 30-60 seconds while glue cools off.
8)DONE!
-The great thing about using the hot glue on Legos is that it holds well, but if you want to change the design later you can, with a bit of effort, pull it apart with little to no damage to parts.
Step 6: Some Things to Consider.
You'll see I added a few things to my completed project. Again, this instructable's intent was not to tell you how to make the whole circuit, just how to make the housing and shaft adapter.
Remember who your making this for. Mine was for my kids, whom I am intimately aware of the abuse they put their toys through.
That being said, here's couple things I did to make my design more durable:
I used a twisted pair of wire from some ethernet cable. Twisted pair can flex and resist kinking and being cut somewhat better than a pair of parallel wires in my opinion. Plus it was the only stranded wire I had in a proper gauge in the length I needed.
I used 1 color of paracord for each motor, and color matched that to the lego housing.
In my application I put the circuit board from an old toy RC car and battery pack in an Altoids tin. It's ugly inside it, if I did this again I'd find a better project box with a battery pack built in.
I put some yellow duck tape around the shaft of the stick on the remote that controls the corresponding yellow motor. This makes it easy for my kids to know which control stick moves which motor.
I hot glued a flat Lego plate to the top and one on the bottom of the tin so they can attach it to their creation, or use it as part of their structure.
Wire all your motors the same way. Pick which of the electrical contacts on the motors you will connect the + or - to. This will ensure that all your motors turn the same direction when power is applied in the same manner.
I ran my twisted pair of wire through the sheath of some paracord. This is intended to bear most of any tension put on the cord, and to help protect it from being smashed or cut.
-You want to make sure the paracord is shorter than the wire. If it's longer then the wire will end up taking the strain. Melting it in the following steps will take up about a quarter inch of length.
BE CAREFUL as paracord will catch on fire and drip molten plastic, It can cause severe burns!
BE CAREFUL not to melt the insulation of your wires, keep them from flame.
-At the ends I melted the paracord so it wouldn't pull back through the hole I ran it and the wire through.
-To melt the paracord this way without damaging the wires: Pull the wires down inside the paracord about an inch. Get a nail about the diameter of the inside of the paracord and push it about an inch inside the end you want to melt. Then use your lighter to melt the end of the paracord. It should draw back a bit into a black collar.
-I then pulled the wire out about an inch, squeezed some hot glue down the paracord inside and puled the wire back in place, dragging some of the glue with it.
-Gently heating up the paracoord without melting it will cause it to shrink a bit and stiffen. Doing this at the point where your cord exits an assembly can help keep it from bending sharply at the edge of a hole which will break the wire over time.
-Then I added a bead of Hot glue around the paracord inside and outside around the hole to hold it in place.
Here's an RC Lego car I made recently with this design. My boys love it!
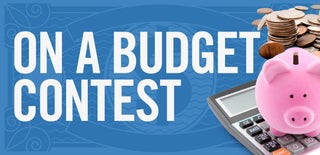
Participated in the
On a Budget Contest
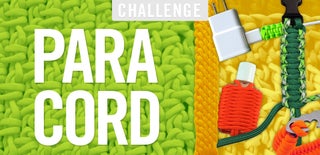
Participated in the
Paracord Challenge