Introduction: Easy-Entry Knife Block Disassembles for Cleaning
...in which software UI teaches knife blocks a lesson...
A "mile high" user interface element is one in which the mouse cursor indexes (stops) on a button placed along the edge of the screen, allowing imprecise positioning along one (or more) degrees of freedom. This works for the same reason that it is easier to place you hand on a table than a fraction of an inch above it: in the first case, you can simply move you hand in the general direction of the table until it stops; in the second, you must first find out where the table is, then accurately move your hand there.
Demonstrated in the (22 second) Youtube video here is a knife block with slots that act this way.
As a normally dexterous person, I can say that this helps, though it's not a huge game changer. People in a hurry, or with conditions which make movement imprecise, may feel otherwise.
In this Instructable, I cover the prototyping of the knifeblock, the fabrication of the final knifeblock, and (briefly) the associated cutting-board garage.
Step 1: Prototyping
The materials for the final knifeblock were expensive (-ish), my confidence was low, and a prototyping step was easy, so a prototype was a good idea.
Note that the layout template produced during the prototyping process is necessary for the production of the finished knifeblock, at least by the final production techniques I used. This is one of the reasons that a prototyping step had such a low time cost.
The captions for the pictures will explain the basic principles of the (fairly simple) dimensioning procedure for that layout template, but also:
- The length of the exposed slot is a compromise between security, required tip positioning accuracy, and required knife angular positioning accuracy: longer lengths decrease security, decrease positioning accuracy requirements, and increase angular accuracy requirements. Play around and select lengths that you like.
- The depth of the knife slots is a compromise between security and ease of insertion/angular accuracy requirements.
Step 2: Knifeblock
The cheapest source of polyethylene I could find, including shipping, was plastic cutting board. This actually warped slightly when I cut out the knifes grooves. This turned out to be a good thing, keeping the grooved layer tight up cover layer, but I don't know if this behavior is consistent between suppliers of material or even orientation on the cutting board. Do tests or copy my material usage exactly.
Anyways... the cutting board was cut to basic size, had the knife slots router-ed in and deburred, and had holes drilled and counterbored for the (stainless and brass) hardware which holds the two halves together.
Again, notes on the step-by-step procedure are with the pictures.
Step 3: Cutting Board Garage
The knifeblock needs something to hold it vertical. This need not be as complicated as the garage built here, though the added storage is really nice and the weight of the toaster keeps everything still.
The materials, by the way, are standard 2x4 and sheeting grade plywood. (plus some steel for the bracket) With 3 coats of linseed and 3 coats of polyurethane. I'm happy with their appearance (you really can polish a turd), other than the way that the shelf warped... I suppose that's what I get for using the cheapest plywood available.
Notes on the design features are with the pictures.
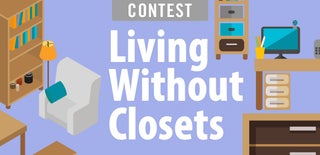
Participated in the
Living Without Closets Contest