Introduction: Milling Small Pcb's (using a Big Machine to Do Little Things)
Instead of a true instructable this is a series of notes that I am putting down about my experiences using a TechnoCNC LC 4896 to mill some circuit boards. I have been training myself on large bed CNC with about a 5inch Z. In the past year I started making my own PCB's and I thought it would be a worthy project to see what I could do with this device.
Step 1: Some Illustrator Work
I designed the circuit and traces as a one-sided surface mount board using EagleCAD. I have been focusing on SMD type of board design not for SMD components, but to get away from drilling the holes on boards, which was burdensome without an automated process (though I may go back if can dial in the process here).
I want to engrave the outer edges of traces so I need to make each border into a vector path. There is a plugin to do this, but I opted to go with a program that I already knew. I exported a .tif of the board view and opened it Illustrator. Putting the image on its own layer and locking it, I then used the pen tool to draw out the paths defining all the traces.
I set the grid to a low measurement .1mm and the tool to snap to the grid so I could draw tight lines that mostly paralleled up on the horizontal or vertical axes. It took me relatively little time because I am experienced with Illustrator. The goal here is to make the paths here a far out as possible to leave as much room for you component legs to attach. I trace the geometry and then use the nudge command to make the area inside as big as possible.
On a separate layer, I added some text to help me orient the board. I labeled the 1,7, 8, and 14 pins, as well as the ground and the power. This text needs to be vectorized as paths for the CAM software to read it, so create outlines of all the text elements. I additionally take out the center paths of elements like 8 or a D which would more than likely be burned out by a double pass of the endmill.
Step 2: Machine Setup
The final illustrator file with the proper layers turned on is imported into my CAM software (we are using RhinoCAM). I setup the stock box, the tool, and the cutting parameters. I am interested in getting as small a separation as possible but deep enough to actually separate the traces from the plane of copper. Using a v-groove endmill I am able to get a good contact with .3mm of cut depth.
Step 3: Keep It Level
Expanding this to a whole sheet of pcb's proves much more difficult. The cut depth is very low, thus the material has to be a flat as possible. I tried the vacuum clamp on the table and I found that the slop of my waste board that wasn't actually being vacuum clamped was pitched up just enough that 1/5 to 1/4 of my boards we unusable because the mill had cut way too deep and removed too much material.
I attached the copperclad to a sheet of MDF using PermaCel tape. and then clamped the MDF as my waste board. This provided better results, but still small variances in the copper clad or the tape caused some error.
Note if the cut was just a bit to shallow, I can use a tool such as an etching needle to carve out the line. Following the CNC shallow path is very easy and only takes a moment.
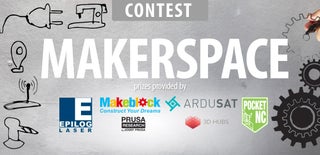
Participated in the
Makerspace Contest