Introduction: Mini Art Easels
Art brings out the best in us.
A full sized easel is quite a beast, as a rule they aren't designed to be transported and sometimes they are over-kill for a small work.
But what about if you host art parties for 10 people or so where the art is fun, but the event is also about socialising and having some laughs. Putting social distancing aside for now, sharing the creative process while seated around a table leads to wonderful interactions and group support even for those who think "I can't paint".
These mini art easels are designed to sit on a table and take up minimal room so that people can share a smaller space.
Woodwork is an art in itself and as you will see, I am a struggling artist. Please learn from my mistakes ;o)
Supplies
1.7m of 42mm x 12mm timber - I used meranti. I think pine might be a little light
Not much PVA glue
1 x Butt hinge + 4 screws
200mm of 3mm string
Varnish
4 x 20mm nails
Tools:
Tape measure - go on Americans, be daring and join the rest of the world using metric.
Screw driver
Hammer
Mitre saw - or you can cut by hand if you are very good at it :P
Router or power saw or hand saw
Chisel
Drill + bits
Knife or scissors
Step 1: Cut to Size
Cut your timber into 5 lengths: 3 @ 300mm and 2 @ 400mm - yes, I know there are 4 short lengths in the photo...sigh...
The long lengths will be the A frame. Two of the shorter lengths will be the rest and the third will be the support stand.
These are arbitrary lengths, but if you change them, consider the proportions so that the easel is pleasing to the eye as well as functional.
Notice the angles. The A frame meets at 45 degrees at the top which makes cutting and calculating a bit easier. The other end of each of the 400mm lengths are cut at 22.5 degrees. The maths is 45 degrees at the top + 2 x 22.5 degrees at the bottom = 90 degrees. Notice that each piece is a trapezoid i.e. the end angles converge. This is a trap for the unwary, the end cuts should not be sort of parallel.
Where the 3 legs sit on the table, they are cut at 22.5 degrees so that as the frame leans back and the stand leans forward they are flat on the surface. Have a look at the photo showing the end of one of the pieces.
To elaborate there are two angle cuts which I am sure has a technical name, but I don't know it. First I cut one end of the length at 45 degrees then the other at 25.5 degrees. I then cut 22.5 degrees across the piece. Gosh, this is hard to explain but I hope the photos make sense of it.
Step 2: Construct the Frame
We want to make a nice overlapping joint at the top of the A frame.
If you look at the first photo where it is laid up, the joint is double thickness. To get this to the single thickness we are going to mark the angles and remove half the thickness from each piece. As a learning wood artist, this has been the hardest for me to get looking half decent. I have made a few of these now and this one was actually the best so far, so I am learning.
Lay one piece over the other like in the photo. This will help you visualise how the frame will look once constructed, as well as let you position the pieces to mark them. Draw that diagonal line and then extend it over the side to meet a line 6mm parallel to the top. We are going to remove a 6mm deep section on each leg.
I have learned over the years that to avoid tears and heartache, it is a good idea to mark what is going to be removed. The second photo shows that quite clearly.
On earlier builds of these easels I have tried using a router and a power saw and am too embarrassed to post photos. This time I cut the diagonal with a hand saw to 6mm, then I set my power saw to 6mm and ran a bunch of slices. It was pretty easy to remove the excess with a chisel.
I glued and clamped them and after a bit of sanding, I was delighted with the result.
Step 3: The Rest
Now we are going to build the rest. Not the rest as in the rest of the project. This is the rest that the artwork will sit on.
We are going to make the rest by gluing 2 pieces together with them offset to make a raised edge. Before we do that we can do some nice neat work on the string that limits the stand extension. The plan is to make an invisible knot that is hidden between the 2 pieces of timber when they are glued together.
On earlier versions, I have used Venetian blind cord which looks like 1.5mm and it works. But this time I found some 3mm utility cord lying around. I prefer this as it gives the back of the easel a bit of visual weight.
Drill a hole through one of the pieces. It should be in the middle and big enough for your string to just pass through. If you have a countersink bit use that to hollow out one end of the hole to make a cavity for the knot. If you don't have a countersink bit, use a large drill bit or a spade bit. You can see the result in the first picture.
Push the string through and tie a good solid knot on the end - I like a figure 8 knot. It will be easier to get the string through if you melt the end so it doesn't fray, but be sure to not let the melted plastic spread out so the diameter increases
Take 2 of your 300mm lengths and sit one of them on a piece of material so that it is raised compared to the other. I used an offcut of the same material, but it could be thicker or thinner. Be sure your cavity with the knot is on the inside. Glue them together and clamp them. Meranti is a little soft and my clamps a bit jagged so be sure to use some scrap timber under the clamps.
You might do something a little different here to create the lip, the first one I made was a single piece, with the lip made by routing along the length. But the indent is a little small.
Once it was dry I used a plane to take off one of the lips. This was the first time I had tried the hidden knot and dammit...I removed the wrong lip which meant the cord was coming out of the front instead of the back. It wasn't at all obvious as I was doing it. No major drama, as you will see.
Step 4: Some Finishing Touches Prior to Finishing
This is the point where it is good to finish the timber, prior to assembly.
Give everything a rub down with some sandpaper to soften those sharp edges along the timber, round the corners a little. Not only does this make it feel nicer, it looks a little less hard edged.
If you are going to varnish or paint, now is the time to do that. I gave a single coat of water-based varnish. It brought out the grain and might offer some protection from the paint that is going to be splashed around when in use.
Step 5: Add the Rear Support Stand
Adding the stand is about the easiest part of the project. There is a correct end and a correct side for the hinge, it is the opposite end to the 22.5 degree angle and it is on the short side. Mark it!
Attach the hinge to the leg, butting it up to the end. Is that why it is called a butt hinge? I seriously don't know. Be sure to pre-drill the holes, it is close to the end and the wood is likely to split.
Position the leg on the back of the frame. Again, pay attention, because there is a front and a back. The back has the shorter length of the frame legs.
Pre-drill and put in one screw, fairly tight but allow some movement. Now lay the frame face down, swing the stand so it is in the middle and then mark the second screw hole. You should be able to figure the rest ;o)
Stand it up! Pat yourself on the back! But we aren't done yet.
Step 6: Attach the Rest
This is the moment when I realised the string was now on the wrong side of the rest. I was doing so well. It was disappointing, but no drama. I have the attitude that if this is the worst thing that happens in my day, what a great day!
I cut the string off right against the wood. You can hardly notice it. Then I drilled a hole in the back, filled it with PVA glue and forced the string into the hole. If this was something I was selling I might have been upset, but they are for our own use so it is minor.
Measure up 50mm from the bottom of each leg, this is where the bottom of the rest is going to line up.
Apply some PVA to both legs and put the rest in place. You did pay attention to which side was against the frame didn't you?
I also used 2 x 20mm fine nails to attach the rest to each leg, it doesn't cost anything to add that little bit of extra strength. Clamp both legs and let it dry.
This is starting to look great...nice work!
Step 7: Finishing Up
Well, look at that! It might need a light sand once the varnish has dried.
If your artwork is bigger than the frame, a piece of board in place solves that.
So now it is your turn. Make some art so you can make some art.
This is being entered into The 1000th Contest because I won a contest in early 2014 - I am still excited by that and my Instructables t-shirt is still alive :o)
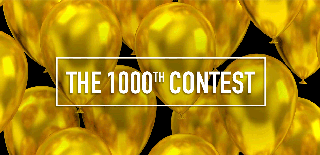
Participated in the
1000th Contest