Introduction: Mission Style Cocktail Table
I made this beautiful piece to pay tribute to the artisans and furniture makers that came before me. As a child growing up in Northern California, class trips to the very mission's that inspired these pieces over a hundred years ago were common. The simple yet striking architecture had a dramatic impact on me. When the time came to design new furniture pieces, I knew I was ready to put that early education to good use. This Mission style cocktail table is my first interpretation of furniture pieces that first appeared in the early 1900's.
Regards,
J.D. Goldberg
Step 1: Plans and Lumber
I had the basic idea of what I wanted to do in my head but I always like to do a computer drawing on sketch up. Then I was off to grab some rough 5/4 red oak from my supplier. I used my planer to bring wood to 1 inch thickness and dimensioned everything down close to size, leaving all pieces long incase I wanted to make any changes to the design. Pay no attention to the Aromatic cedar plywood. It's for another project
Step 2: Making the Top
I decided to make the top 24"x 50" . I ripped 3 boards down to a little over 8 inches a piece and ran them thru the jointer to straighten the edges for gluing. After matching up the grain pattern I edge glued and clamped the top. I used domino tenons in my joints, but you can use biscuits, dowels, or nothing at all. They mostly help with alignment. I set the top aside to dry while I work on the legs.
Step 3: Making the Legs
There are many ways to make legs. I decided to laminate them. This is when you take pieces and glue them together and make a larger solid piece. This makes a very solid leg. I took 3 pieces that were 1" thick and very flat after being ran thru the planer and glued them together making 3" square legs. To do this correctly the wood must be very flat and u need a lot of clamps to apply pressure. When dry they are ran thru table saw and jointer to make nice clean looking solid pieces You can't even tell they are glued together.
Step 4: Making the Frame
After legs are cleaned up cut them @ 20". Dimension everything else to size.
2@ 2 1/2"x42"
2@2 1/2"x16"
1@ 12"x44"
12@ 1"x1"x10
all those pieces are 1" thick
make 2 @ 2x2x 16" for lower rails
I used my Domino joiner to join all the pieces. It's a very fast way to do Mortise and tenon joinery, referred to as loose tenon. Traditional mortise and tenons, or pocket hole screws will also work. Make sure you add glue and plenty of clamps, and let everything set over night. ( for the vertical pieces the gap is 3/8" the best way is to make blocks and insert them during glue up) Also I use a 5-10mm offset on all my connections to add a little depth. The apron rails are set 5mm inside the outside edge of the legs for example.
*NOTE I actually do my staining before glue up this helps me get a clean look
Step 5: Staining/Finishing
When I am happy with how everything fits I disassemble and stain. I sand everything up to 180 then wipe down with a damp rag. This piece was stained a dark brown mahogany and was almost black at one point. Then I sanded it down to bare wood but was careful to leave the dark stain in the grain to accent it. At this point I dyed the wood with a mixture of dye I make myself. Lets call it a deep reddish brown with gold undertones shall we. I dye it twice then seal it with amber shellac. that takes down some of the orange. It looks good but the final touch is I add a coat of clear. After that coat has dried I take my damp stain rag and glaze the top of the clear coat lightly. I never re wet the rag it's a dry wipe. This can be a little unnerving so if you don't feel comfortable doing it skip that step. Next three more coats of clear are applied and the top is connected with figure 8 hangers.. This is a rough outline of this project. If you would like more details or have any questions I would be happy to answer them!
Regards,
J.D. Goldberg
Step 6:
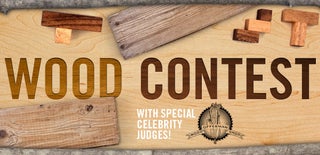
Participated in the
Wood Contest