Introduction: Modern Li-Ion Retrofit for Older Analogue Multimeter
I came into possession recently of an old Triplet analog multimeter in very good condition. Since these old-school analog needle meters are great for measuring fluctuations that most handheld digital meters can't display well (and I like old tools), I wanted to get it working again. Upon opening up the meter I discovered that it uses two batteries, one that is easy to come by, and one that hasn't been made in decades, a 1.5V D cell (which I can get easily) and a 30V B cell (which I don't think is even made anymore). Hooking the meter up to one of my lab bench power supplies and giving it -1.5V and 30V gave me the results I wanted to verify the orientation and the meter came to life.
I decided in my work to repair this meter, I wanted to modernize the battery instead of trying to hunt down one based on a long obsolete standard. Luckily for me, since this meter appears to sip mere milliamps Analog Devices has a chip that perfectly solves this solution. The fantastic LT1945, from Linear Technology (now Analog Devices), solves this problem, as it can generate both of the required +30V/-1.5V from a standard LiPo or LiIon battery.
Supplies
Parts:
Electrical Components:
- Custom PCB (board files and gerbers provided in step 1)
- Custom PCB Stencil
- 100nF 50V 0201 Ceramic Capacitors
- 1uF 6.3V 0201 Ceramic Capacitors
- 1uF 50V 0603 Ceramic Capacitors
- 100k 0201 Resistors
- 1.74k 0201 Resistors
- 510k 0201 Resistors
- 330k 0201 Resistors
- 2.7k 0201 Resistors
- 1M 0201 Resistors
- 42.7k 0201 Resistors
- 80k 0201 Resistors
- 1N4148W SOD-123 Diodes
- LED 0805
- 10uH 0805 Inductors
- 4.7pF 50V 0201 Capacitors
- 4.7pF 10V 0603 Capacitors
- 100pF 50V 0201 Capacitors
- LT1945 Dual Rail Switching Regulator
- LTC4095 Li-Ion Charger
- 9001NC Reed Relay
- 2 Pin 2.54mm Jumper
- 2.54mm Pin Header
- AS2312 N-Channel SOT-23 MosFET
- AP9101 SOT-26 Battery Protection/BMS (choose variant based on battery used, I used AP9101CK6-AYTRG1 which is for batteries with a max voltage of 4.1V)
- Li-Ion Battery pack
Misc Materials:
- Solder Wire/Solder Paste
- Flux/Flux Cleaner (or IPA)
- Between 18-22 AWG copper stranded wire
- Countersunk M3 screws
- M3 Nuts
Tools:
- Wire Snips (flush cut is best)
- Pliers
- Allen Keys
- Crimping Tools
- Soldering Iron
- Hot Air Soldering Station
- Electrical Tape
- Double Sided Tape
- Fine Tip Tweezers
- Exacto Blade
- Wire Strippers
- Magnifying Glass/Microscope
- Cotton Swabs
- Putty Knife/Scraper
- Drill Press
- Drill Bits
- Square Needle File
- Multimeter
- Bench Power Supply
Step 1: Order Custom PCB
I ordered my board through JLCPCB, but ultimately any fab house should work with the provided Eagle/Fusion360 eCAD files/gerbers. Due to the size of the several of the components on this board I would recommend ordering a stencil with the board at a minimum or possibly opting for an assembly service. I assembled it by hand myself, but that will require steady hands and a magnifying glass.
This board serves three purposes. the first is to behave as a battery charger over USB. the second is to behave as a BMS or battery protection. And the third, probably most important, is to generate the required voltages to power the multimeter.
Attachments
Step 2: Assemble PCB
Assuming you did not opt for assembly of the board, make sure both the board and stencil are clean of any and all contaminants. When applying solder paste to my boards, I put the boards on a piece of magnetic material (a printer with a magnetic bed will work) and use strips of magnet around the board to hold the stencil down. Before applying the solder paste make sure it is well mixed and add IPA or flux to it if necessary. I generally apply a generous pile (a teaspoon or so) and spread it onto the board with a putty knife, scraping off excess as necessary. Be careful lifting the stencil off the board as any lateral movement can smudge the paste.
When assembling this board, I recommend having the board file open on your computer as a reference for what value goes in what location. In addition, I recommend starting with the larger IC's and populating the smaller resisters and capacitors around those parts after. Leave the biggest parts (through hole, electrolytic caps, connectors, and inductor) for last. I recommend working in areas at a time and using the hot air station to reflow each area before you move onto the next one. For ease of testing, I would recommend leaving the 9001 reed relay off the board until it is fully tested so as to be able to easily test the individual sections of the board on their own.
When testing the switching regulator section of the board I used a bench power supply current limited to 50mA and set to around 3.7V. When testing the Li-Ion section of the board I used a bench power supply current limited to 550mA and set to around 5V.
Update: If your meter takes slightly different voltages you can achieve those by following the equations in the datasheet (or playing with the LTSpice model) and adjusting resistors R6 and R7 for the negative rail and R8 and R9 for the positive rail.
Update: I had problems with the NTC thermistor I used with the LTC4095 so I have decided to not populate the thermistor.
Step 3: Prep Multimeter Housing for Modifications
Before installing the battery and circuit board in the case, the cutouts for the USB charging port and the switch/status indicator need to be created. I opted to place those on the side of my meter near the bottom, so I don't have to route the cables too far.
Before cutting out the holes make sure there is adequate clearance between the edge and the internal components. You do not want to drill holes in places where the parts ultimately will not fit. If you have the same meter I have, I recommend putting the holes in the center of the side as shown in the pictures. I used some black epoxy to fill in the small gaps around the USB connector, but that is completely optional. Super glue will work to hold it in place, or if you make the hole slightly undersized the friction fit will hold it.
Step 4: Install Battery and PCB
When creating the cable harnesses which connect to the board follow the labeled pinout of the board. For plug A, pin 1 is battery positive and pin 2 is battery negative. For plug B, pin 1 is USB 5V and pin 2 is USB ground. For plug C, pin 1 is the first pin of the switch, pin 2 is the second pin of the switch, pin 3 is the negative pin of the status LED, and pin 4 is the positive pin of the status LED. For plug D, pin 1 is GND, pin 2 is -1.5V voltage negative, and pin 3 is 30V voltage positive.
When connecting the output of the board to the multimeter connect to where the old batteries would have gone. In my case, my meter clearly labels which terminal is what. I connected the -1.5V to the - of the D battery terminal, the ground to the + of the D battery terminal and - of the 30V battery terminal, and the +30V to the + of the 30V battery terminal.
The black connector labeled header is for resetting the BMS when a new battery is connected. Due to how the AP9101 BMS chip works, if a new battery is connected you must bridge that jumper for a second and then disconnect it to allow the chip to reset properly.
I used double sided tape to attach the Li-Ion battery inside the void where the original batteries went and put the charging/BMS/supply board directly on top of that. After plugging all the cables in where they go and ensuring that nothing is loose, you can go ahead and close your meter up. No more needing to track down those obsolete battery standards anymore!
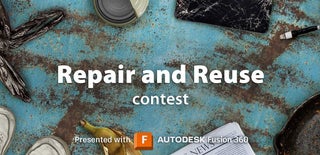
Participated in the
Repair and Reuse Contest