Introduction: Multi-Rotational Mirrored Starburst
Step 1:
in addition to the complete kit of routed parts you will need the following:
about 3 large bottles of moisture activated polyurethane glue (gorilla glue, or elmers' ultimate polyurethane glue)
about 4 rolls of 1 1/2" or 2" good quality masking tape to be used in the gluing process.
about 30 feet of 3/8" threaded rod
30 3/8"x1 1/2" coupling nuts
60 3/8"locking nuts with nylon inserts
permanent thread locking compound (Loctite 262)
30 split pins
30 3/8"x1 3/8"x1/2" bearings
about 20 feet of 1" copper pipe
30 copper reducing fittings 1 1/4" to 1"
plumbers solder and flux
30 inexpensive disco ball motors (around $10/ea from cheaplights.com)
90 3 1/2"x 1/8" carriage bolts
90 1/8" nuts
6 6 outlet power strips
1 6 foot power cord
approximately 1/2 sheet of quality 1" plywood
1 foot section of 1 1/2" black pipe threaded at each end
1 1 1/2" pipe flange
1 1 1/2" pipe cap
1 3 foot length of 1/2" threaded rod
1 1/2"x2" coupling nut
1 1/2"x 5" eye bolt
2 1/2" washers
4 1/2" nuts
1 1/2" locking nut with nylon insert
assorted small hardware and zip ties
NOTE: it is strongly recommended that you review all of this instructible and have a thorough understanding of the materials list and how all the materials come together. i also recommend that you source any materials that interface directly with routed parts, prior to beginning this project, and verify the affected dimensions with calipers, and make any changes if necessary to the files before sending them off to be cut. failure to do so will be quite co$tly.
you will also need access to:
a table saw with a tilting arbor, rip fence, and a good quality miter gauge. (i recommend the
Kreg KMS7102 precision miter gauge)
a drill press and assorted bits 1/8" to 1/2"
plus a good assortment of common hand tools to include but perhaps not limited to a hammer, punch, crescent wrenches, socket wrenches, assorted pliers and vise grips.
common sense safety should be observed at all times, especially for those less experienced.
safety glasses are a must, a mask should be worn while cutting foamboard products on the table saw, and gloves are also recommended when working with the aluminum faced foamboard products as the edges can be very sharp.
this instructable is not recommended for beginners, and i would rate it a 4 out of 5 as far as difficulty is concerned. you should be experienced with the use of table saws and their associated guides, gauges, fences and safety features, and have a personality that works to perfection or precision in all aspects of a project if you desire a satisfactory result.
estimated cost for this project: $2400
Step 2:
step 1. after receiving your set of routed parts, separate them according to part type, taking care not to mix triangles destined for pentagonal spikes with those intended for hexagonal spikes. (the triangles intended for pentagonal points are slightly narrower and shorter than those for hexagonal points.) do not remove the protective film covering the metallic surfaces at this time.
step 2. set aside 1 metal faced pentagon. laminate the remaining metal faced hexagons and pentagons with a 2" foamboard hexagon or pentagon respectively with metal side out. you may wish to build a jig to ensure the alignment of the 6 3/16" holes in the center of the pieces. prepare the surfaces for gluing and follow glue manufacturer instructions. clamp or weight the pieces until fully cured.
step 3. using the metal faced pentagon from the previous step as a template, trace around it onto the 1" plywood to make 2 pentagons. cut out the two 1" thick plywood pentagons and glue them together to make a 2" thick pentagon. this pentagon will bear the entire weight of your death star, so it is very important to use a good quality ply for this piece. when the glue has fully cured or dried, place it on top of the metal faced pentagon. it may be slightly smaller, bit it must not extend beyond the template in any place. if necessary, remove any excess material with a belt or disc sander. when properly sized, glue the 2" thick plywood pentagon to the metal faced pentagon, once again metal side out, and allow glue to cure fully.
step 4. in this step we will use a table saw to create the appropriate bevel on all of the core pieces we laminated in the previous step. pentagons and hexagons have different bevel angles, so they will be addressed separately, but the process is the same. angle the saw blade towards the rip fence to the required angle, then lock the angle using the arbor locking knob. then raise the blade until it's highest point is just shy of the thickness of the laminated pentagons and hexagons. clamp a board which is straight and true the the existing rip fence of the table saw to create a sacrificial rip fence. with the saw turned on, slowly bring the rip fence over to meet the spinning blade until the highest point of the blade intersects the face of the board. switch the saw off then lock down the rip fence. verify that when a pentagon is placed against the fence with the metal side up, that the saw blade removes the material just below the metal face, but does not cut into the metal. (you may wish to try it out on scraps first.)
the bevel angle for pentagons is 71.31 degrees. cut all edges of the pentagons to this angle.
hexagons have two different bevel angles, 71.31 degrees on the sides which meet pentagons, and 69.09 degrees on the sides meeting other hexagons. the arrangement then is that there are three sides at 69.09 degrees and three sides at 71.31 degrees, arranged such that bevel angles alternate as you progress around the hexagon. i found it useful to mark every other side with brightly colored tape to keep track of which side is which. you will not need to readjust the bevel angle to cut the first three sides of the hexagon as they are the same angle as the pentagons. then reset the angle and height of the blade to 69.09 degrees, readjust the rip fence before cutting the remaining three sides of each hexagon.
Step 3:
step 5. Locate the center of the pentagon with the laminated plywood backing, then use a 1 1/2" hole saw or forstner bit to cut a hole all the way through the pentagon, starting from the wood side. then center the 1 1/2" pipe flange over the hole and mark the locations of the 4 screw holes in the flange onto the plywood. drill 4 3/8" holes all the way through the pentagon. flip the pentagon over then using a 1" spade bit with sharp spurs, carefully cut through the aluminum facing material centered over each of the four 3/8" holes. if necessary stop and remove the ring of aluminum facing, then drill away the foam only to the depth of the plywood. do not drill into the plywood with the 1" spade bit.
step 6. Examine the protective film on the plywood pentagon from the previous step paying particular attention to the edges. if the protective film is fully adhered along the edges then leave it on, if it is loose or there are air bubbles beneath it it must be removed. cut 5 pieces of wide masking tape the same length as each side of the pentagon, and adhere one to each edge of the pentagon at half its width. press it firmly into place and verify that it will not easily release. if there are adhesion problems you may need to clean the surface with alcohol or try a different tape. lay the pentagon metal face down with tape sticky side up on a very flat clean surface. (i use a large glass tabletop which assures a smooth planar surface, and any blobs of glue can be easily removed with a razor blade once cured.) place 5 hexagonal pieces around the pentagon, carefully the edge of each hexagon with that of the pentagon, assuring that their metal edges meet along their entire length. press each hexagon firmly onto the tape, then lift it while reaching under to press the tape firmly in place. by now you should have something which resembles figure a. at this point you may wish to enlist the help of a friend. you will be applying glue and folding each of the hexagons up one at a time, then taping the edges where the hexagons meet each other. do not forget to apply glue to the edges of the hexagons that will meet. verify that all edges come together tightly and that tape is well adhered along the edges. this is the only clamping that is required while the glue cures.
When the glue has fully cured you will lay in the next tier of five pentagons. each pentagon will sit with a point down in the shallow "v" formed between adjacent hexagons. affix tape along the sides of each "v," apply glue, lay in the pentagon aligning the edges carefully, then press the tape securely over the seams. allow to cure fully.
When glue has fully cured, tape, apply glue and lay 5 hexagons into the spaces between the pentagons. verify alignment and press tape firmly into place, allow glue to cure fully.
This completes the lower half of the core structure. repeat step 6 again, this time beginning with a foam pentagon.
Step 4:
step 7. cut 30 pieces of 1" copper tubing 6 1/2" long. place a 1 1/4" x 1" fitting on one end of each piece of copper tubing. make sure it is fully seated, then solder the two pieces together.
when the pieces have fully cooled, carefully press or tap a bearing assembly into wide end of the reducing fitting, taking care not to skew the bearing in the fitting. the bearing should fit snugly within the fitting. next assemble a circular metal faced connection flange, with a 2" thick foam support collar and the tubular bearing holder assembly. apply glue inside the 1" holes in the centers of the foam pieces, push the 1" tube through the 2" collar until it begins to protrude from the opposite side, apply glue to the face of the 2" collar, then press the connecting flange over the end of the 1" tube until the end of the tube is flush with the face of the connecting flange. set 30 pieces aside to cure.
step 8. using a table saw with a good miter gauge, and with the arbor tilted to 10.4 degrees cut 12 pentagons measuring 2.5 inches on a side from the 1" plywood. it's best to lay the pentagons out on a square piece of plywood first, with one side of the pentagon flush with the edge of the plywood, then cut the remaining sides using the miter gauge and your markings to align the remaining cuts.
once again using a table saw and miter gauge, this time tilting your arbor 13.1 degrees, cut 20 hexagons from the 1" plywood measuring 2.7" on a side.
when all pentagons and hexagons have been cut, locate the geometric center of each, then drill a hole through the center which is just large enough to to allow you to press a 3/8 inch lock nut with nylon insert into the hole. when all the parts have been drilled, place them on a table with the wide side facing up, apply epoxy to the inside3 of the hole then press 2 locking nuts into each hole with the nylon inserts facing down. you may wish to thread the two nuts onto a long bolt to tap them into the hole, as well as to verify with a square that the nuts are not skewed in the plywood.
step 9. using a table saw with a sacrificial rip fence, tilt the arbor 35.3 degrees and raise the blade to a height just shy of 1/2", then adjust the fence accordingly. bevel the long edges of all the triangular pieces for the pentagonal spikes with the metal side facing up.
now set the arbor to 29.1 degrees and bevel the long edges of all the remaining triangles.
step 10. using wide masking tape, tape together 5 (or 6 depending on which triangles you are using) of the long triangles along their edges, apply glue along the seams and edges, then roll the set of triangles into a cone and apply tape along the edge to close. apply glue to the outside edge of a plywood pentagon (or hexagon) then carefully press it into place inside the cone. set cones aside and allow glue to cure fully.
step 11. cut 30 pieces of 3/8" threaded rod to a length of 9". apply permanent thread locking compound to one end of each rod and screw it into a coupling nut to a depth of 1/2-3/4". allow bond to set fully.
use a center punch to create an impression on one of the faces of the coupling nut, 1/4" from the open end, then use a drill press with a 1/8" bit, drill a hole through the coupling nut.
step 12. slide a shaft assembly from the previous step onto the shaft of a disco ball motor and attach using a split pin.
step 13. insert a motor/shaft assembly into the cutout inside the core aligning motor mount holes with those in the core. place a bearing mount assembly over the shaft protruding from the outside of the core, once again aligning flange holes with those in the core. when pressed together the 3/8" shaft should protrude approximately 1 1/2" beyond the bearing assembly. using 3 1/2" stove bolts connect the bearing mount flange on the outside with the motor mount flange on the inside. (use a minimum of 3 evenly spaced bolts per mount.)
Step 5:
step 14. using a drill press, drill a 1/2" hole in the center of the 1 1/2" pipe cap. thread a 1/2" nut approximately 2" onto a 36" piece of 1/2" threaded rod followed by the 1 1/2" pipe cap with the open end facing away from the nut. follow this with a washer that fits within the pipe cap, then thread on a 1/2" locking nut with nylon insert until the threads fully engage the nylon insert, then tighten the opposing nut until snug with the top of the pipe cap.
apply thread locking compound to the threads inside the cap, then screw the cap onto the 12" section of 1 1/2" pipe using pipe wrenches to tighten. apply thread locking compound to opposite end then attach a 1 1/2" flange fitting, once again using the appropriate wrenches to tighten fully.
attach the flange fitting to the plywood floor of the core using appropriate bolts, washers and locking nuts.
step 15. daisy chain and place 6 power strips in the lower half of the core, then connect all of the motor leads from the bottom half to the power strips. with the help of a friend, lower the top half of the core over the threaded rod, then connect the remaining motor leads to the power strips. connect the power strips to a power cord. run the cord up through the top and attach it to the threaded rod with zip ties, leaving adequate length to reach your power supply. the two halves of the core should interlock and fit together snugly.
step 16. use a 1/2" coupling nut to connect the threaded rod with a 1/2" eye bolt. use thread locking compound, jesus nuts, pins, welds, or other means to assure that this connection will not unscrew in the course of normal use.
step 17. with the eye securely attached suspend the core at a convenient working height, then working from the top down screw the cones onto the 3/8" rods protruding from the bearing assemblies. screw the cones until you feel the second nylon insert engage the threads of the rod, you will notice an increase in the amount of force needed to turn the cone. do not tighten the cones until the contact the bearing assemblies and cannot be turned further. if you reach a hard stop, back off a few turns. the cone must not turn freely on the rod nor make contact with any stationary parts of the core. remove any remaining protective film and tape as you work your way around and down the core. use extreme caution and wear eye protection while working on or around the star, as the points are sharp and the mirrored surfaces can sometimes "disappear" in a less than optimal working environment.
step 18. attach your death star to its final rigging point, and verify that any additional motors, lifts, trolleys and electrical systems are appropriately rated to carry the loads associated with your death star device. always operate your device at a safe distance from people, and allow adequate clearance between the device, other equipment and automated luminaires. illuminate and enjoy.
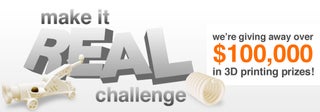
Participated in the
Make It Real Challenge
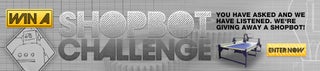
Participated in the
ShopBot Challenge