Introduction: Nested Cube Butcher Block Tables

I made these dancing* nested cube tables mostly to practice MIG welding and powder coating. The larger table measures about 22" x 22" x 22".
Continue on to see how they were made. Next step - screenshots of my design.
* Thanks to SelkeyMoonbeam for the helpful instructable on embedding images in the text of an Instructable. Trying and failing to get this GIF to fit nicely with the still photos above was really grinding my gears.
Step 1: Design
My design process went as follows
- Thought about things to make that involve welding and powder coating - decided on furniture
- Picked up an old workbench top (see Materials in next step) - thought I'd make a coffee table
- Decided a steel coffee table would be too cumbersome to move around in my car - googled "nesting tables"
- Measured the old workbench top, decided the number (2) and size (22", 19") of the tables
- Hacked around in Autodesk Inventor until I had the model shown above.
- Thought, "Hey, those look pretty decent."
With my design in mind, I was off to buy some steel.
Step 2: Materials
As I mentioned before, I bought the old workbench top before I had my design. It was all covered in gum and pretty scratched up - i have a feeling it came from a school. It was 1.75" thick and heavy as heck. I bought it for $30 bucks at a wonderful place in Pittsburgh called Construction Junction. Their thing is reselling donated building material and they almost always have some interesting stuff on their warehouse floor (If you live in the area, check them out. If not, I've heard of similar establishments in other cities, you should check them out too. Reusing old material is cool!)
The steel is hot rolled, 1/8th inch wall, 1 inch square tube. I bought it at Metal Supermarket and had them cut it down to fit in the backseat of my car. It wasn't cheap - I payed about about $100 - and I'm told you can buy cheaper from local sellers that deal in bulk. Next time...
Also, 1/8th in thick is probably excessive - I could have cut down on costs and the weight of the tables by going thinner.
Step 3: Table Base Fabrication - Cutting Steel Tube
I made all of my straight and mitre cuts using a cold saw. Pretty straightforward.
Step 4: Table Base Fabrication - Grind Before Welding
Before welding, I used an angle grinder to clean off the areas where I would be welding my steel together. This keeps impurities out of the welds. Impurities in welds lead to weak bonds and cracks, I'm told.
Step 5: Table Base Fabrication - Weld Base Sides
For each base, I started by welding two rectangles (rectangles and not squares because the frames are 1 inch shorter than they are wide and deep - leaving 1 inch for the table top to bring the whole construction to an approximate cube).
Before welding I arranged my pieces and clamped them down tight on the table. I had minimal warping and everything turned out almost exactly square, so I'd say this strategy was effective.
Once everything was in place, I tack welded each joint in a few spots, then went through and completed my welds.
Step 6: Table Base Fabrication - Grinding Round 2
After welding the sides of the base, I took them back to the grinding room to clean up my welds. I got everything as flat and clean as possible in preparation for connecting the sides together with the 3 cross tubes.
Step 7: Table Base Fabrication - Welding the Base
Just like when I welded the sides, I started welding together the whole base by arranging the pieces and clamping them down. I used some arrow magnets to positions the cross tube that I couldn't clamp to the table. Again, I tack welded everything, then went back around and completed my welds.
Step 8: Finishing the Base - Grinding Welds, Removing Mill Scale
I used a general purpose grinding disk to grind my welds smooth on all the outside surfaces of the base. I wasn't sure how to grind down the inside welds and decided just to leave them be.
Next, to prepare for powder coating I needed a clean uniform surface. To clean off the mill scale of the steel I switched over to a flap disk on the angle grinder. This allowed me to clean the surface without removing too much material.
Step 9: Finishing the Base - Cleaning Before Powder Coating
Powder coating seems to be one of those subjects where you ask three different people how to do something and you get three different answers. First I was told that I absolutely should clean my steel with TSB to remove any traces of grease and oils. Later, while scrubbing away, I was told I was wasting my time and that my steel was more than clean enough already. I was also advised that I'd be better off just wiping the base down with some break cleaner.
My steel seemed pretty clean after I went over it with the flap disk, so in hindsight I'd say I probably could have skipped this step. Either way, it took 15 minutes and gave me some piece of mind.
TSB is pretty nasty stuff. It comes as a powder that is easily dissolved in water. I put on some gloves, mixed up some solution, and scrubbed the whole base with a brush. Then I rinsed with clean water and used a compressed air gun to dry everything off.
Step 10: Finish the Base - Powder Coating
With the base clean and dry, it was time for powder coating. I originally intended to do each base in a different color, but after some test pieces, I decided I only liked the one color I had purchased - Rustic Red from Prismatic Powders.
Lots of good Instructables out there about powder coating, so I'm not going into much detail about the process.
One thing I did take away from this project is that powder coating is a forgiving process. After coating, I baked my bases at 375 degrees for about 15 minutes (or maybe it was closer to 25 minutes - I lost track of time).
On one of the bases I initially applied the coat so thin that, after curing, steel was clearly visible in several spots. A day later I heated the base back up to 375 and hit it with another coat, then put it back in the oven for 15 minutes. It came out looking perfect.
Step 11: Table Top - Removing Old Polyurethane
I followed this tutorial step-for-step.
Step 12: Table Top - Sizing and Squaring
I cut the first table top with a handheld circular saw and the second on the table saw. The table saw was definitely an easier setup and more accurate. Both left scorch marks that I cleaned up with a few passes on the jointer and some sanding.
Step 13: Table Top - Rabbet on the Router Table
My design called for 1" of exposed table top, but my workpiece was 1.75" thick. As a solution, I decided to route large rabbets on the underside of the table tops. This also allowed me to make the table tops friction fit the bases, which I liked because it made assembly very simple. No screws required.
I used a basic straight bit in the router and set up the fence. It took me 3 or 4 passes to get the 3/4" deep 1" wide rabbets I needed to fit the table tops into the bases.
I used a handsaw and chisel to cut in the corners off the thicker part of my table tops to keep it from getting stuck on my ungrinded inside welds.
Step 14: Table Top - Sanding Surface and Beveling Edges
I used a palm sander and worked from 80 grit up through 220. Then I switched to hand sanding and went up to 400 grit. It had to work the sides of the table tops a bit extra to remove the scorch marks from cutting them.
Even after lots of sanding, the table tops kept their distressed character.
After sanding*, I beveled the edges of the table tops with a small hand plane. This was super simple and added a nice detail to the tables.
* I know, the pictures show me to doing this before sanding. I messed up, OK? After sanding (and destroying the nice crisp lines of the bevels) I went back along the edges and fixed things up but neglected to take more pictures.
Step 15: Table Top - Applying Finish (sort Of)
After taking the time to remove a thick coat of poly, I wasn't very into the idea of putting the table tops right back into a clear coat prison. I decided to do close to nothing and just rub in some of the oil wax finish I had lying around for turning projects. The internet advices that wax (even with a little added walnut oil) is insufficient and that I will soon have dented, scratched, and stained table tops, but I'm not too concerned. I like the natural look and feel of the table tops, and i'm not too fussy about keeping things perfect. Plus, I can always sand and refinish them.
Step 16: Acrylic Feet for the Base
I wanted to add some feet to keep the tables from scratching my floors (and floors from scratching my tables).
I considered tapping holes for screw in leveling feet, but I wanted a quicker and simpler solution. The tables are sit stable on level ground, so I decided that I'd forgo adjustability and just stick something on.
I cut some 3/4" diameter 1/8" thick acrylic discs using a laser cutter, roughed them up with sand paper, roughed up the powder coat where they would placed, and super glued them on.
Step 17: Find Somewhere to Place Chic New Tables
Tables on display in a totally natural and unposed way.
Really, I'm planning on using them as a side table / utility surfaces around the apartment.
Thanks for reading!
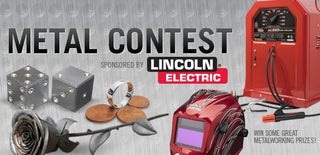
Runner Up in the
Metal Contest