Introduction: Night Light Table
Thanks for looking.
Step 1: Front View.
Step 2: Dim in Low Light
Step 3: It Will Glow in Full in Dark.
Step 4: How It Starts.
When I have an image in my head and I want to apply it to paper I end up with something different than the original thought and when it comes to creating it, so many variables like deviations, mood of the day and those “what if” questions normally produce something that does not resemble the original thought. This is why I have never committed my creations unto paper. This project was an exception though. Woke up one day around four A.m. and decided to use Excel to draw what I had in mind. I know excel is not the best program to draw furniture on. After all, it is a database program designed with functions and formulas to calculate and manipulate data. However, I am familiar with this program and it was the only thing I had at disposal at the time. This is what I managed to come up with:
Step 5: Raw Material
Later on that day, I went to my woodpile and found this 2-1/4” live edge cherry to start the project. There were cracks on both ends of the lumber and I had to start at 22” from the end and mark it at 64” to get the best piece from it. A total of 42” out of a 96” board seem like a lot of waste, but that is how it works. The two “bad” ends will be used for something else that require smaller pieces of wood with narrower width.
Step 6: Through Thick and Thin.
The board is about 2-1/4” thick; after putting an straightedge on it, it has a good 1/2” dip near the middle.
Step 7: Dip.
The black arrow points to the straight edge I placed on surface of the wood. At this point I wish I had a 22” planer since the board is 19” wide, I am going to hand plane it flat. With this task, no need to join a health club to get a good workout.
Step 8: Workout.
I went ahead and started to plane the section I will need while keeping the ends intact. The weight of the board made it easier to do the job.
Step 9: Almost There.
So far, I have ended up with 1-3/4” thickness.
Step 10: Chop.
Step aside Freddy Krueger and Texas chain saw massacre leather face… There is a new guy in town; the Makita slicer and deicer.
Step 11: Debark.
Now, this baby is small enough to carry around. Both sides of the natural edge were too damaged to save and were cut in order to make a rectangular piece of board. Marking the distance between the saw blade and the end of face-plate serve as a guide to attach the straight edge for the face-plate to run against while making the cut.
Step 12: The Plane Boss.
After using the joiner and table saw, I had a straight edge on both side of the board. Here, I am back in the assembly shop smoothing the surface with a smaller plane.
Step 13: Signature.
I think I am pretty close to 1-1/2” and just refuse to go any thinner than this since I need to scrape and then sand as well. The surface is not very even, but it is close. I went ahead and made the front of the table with this
design which has almost become my signature on most of the desks and tables I make.
Step 14: She's Got the Legs.
Utilizing French rulers, I came up with this design, which I was happy with at first.
Step 15: Knows How to Use Them?
All four legs were cut on the band saw to resemble one another as close as possible.
Step 16: Turn Right.
I found this curved shape walnut and decided to use it as the facing that attach the two front legs together. The initial thought was with this piece having a natural curve; it would enhance the look of this furniture.
Step 17: Hmmm.
Thinking was to make the front to look natural edge at the bottom with the bark intact but it really didn't work out and it just didn't look right to me.
Step 18: Bad Idea.
Yuck. Talk about a bad idea. Once the front legs and the face-plate were temporary attached to evaluate the looks, all I can say, is that it looked horrible to both my wife and me. It looked so bad, that even the picture of it would not come out clear. That curvy walnut board will be going to project # infinity. This table is not wanting to be natural edge in any shape or form and I have to respect that.
Step 19: Getting There.
Next, I got a cherry board and using my French rulers, I came up with a pattern that was appealing. I have had a narrow, short and partially rotted board lying around for while now. The magnificent grain patter was just to impressive to dispose of it. I decided to use it for this project’s drawer facing. Meanwhile, I ended up redesigning my project since the straight legs just did not look appealing. In addition, the legs were redsized to make them less bulky. The cuts for the top facing and bottom braces were made with handsaw first before the curve marks were carved out.
Step 20: One Section at a Time.
So, here is what it looks like. The legs are angled at about 18 degrees outward and their thickness complement the front apron.
The drawer assembly was pretty straight forward, all made with cherry, oak and the walnut piece.
Step 21: Dry Fit.
Here is what the project looks like dry assembled. Notice that at this point, I had not made the bottom mortise and tenon yet as I thought the structure didn't need it. However, after dry assembly, it was evident that additional support was necessary.
Step 22: Assembly.
As the saying goes, "it ain't done until its assembled". Thankfully, everything fit just right and there were no wobbles on the legs.
Step 23: Light Her Up.
After several coats of lacquer, It was time to drill the holes for the tabletop supports both on the top and the supports. This is the top view that shows how the power supply is connected to the table. Also, note the hole on the right center where the LED light is placed. Second picture shows the supports installed.
Step 24: Juice.
The holes at the bottom of the table have to exactly match the supports on the top or it will look awkward. The top of the rails were the wiring runs slide open for easy access to repair and or replace led lights with different colors.
Step 25: Note to the Reader.
I hope I have provided the reader with a better understanding of the process it takes to perceive and execute a project and make decisions as it relates to modifications and improvements. My total hours from start to finish on this project was 93 hours. This project can be copied in less than half of that time for obvious reasons. However, I have made it my practice to never replicate my work. My hope is that the reader is encouraged to utilize these steps to execute his or her own creation.
Thanks
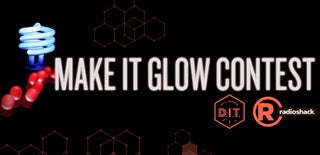
Participated in the
Make it Glow!