Introduction: OUIJA and Heart Etched Pendants
For my birthday one of my presents was a small NEJI lazier engraver from GearBest (http://www.gearbest.com/3d-printers-3d-print…/pp_343187.html) . Despite being a little tool and in comparison to the big tools used in fabrication laboratories this little engraver is incredibly easy to use and seems fairly bullet proof from what I have asked it to do.
Its limited to an image Size of 512x512 pixels, The engraving area is limited to 4cm x 4cm
This happens to be perfect for little projects including jewelry making :)
This is my first project using the new tool and I hope you enjoy it.
Step 1: Design the Etching
I had started to design some flock wallpaper for a pub some time ago before realizing the pub had no intention to pay for the work. This left me with some reference material for designing the heart for my pendent.
I drew a center line and then started to draw half of the heart ready to have its mirror added in Photoshop later.
Step 2: Send to Burn
I used Photoshop to mirror my design and convert my art to back and white in a canvass of 512 x 512 pixles. (I did video this but my computer is under powered and I am currently un able to edit the video to show you how to do this in great detail.
The good thing is you don't need to do this as you can copy the artwork images in this step.
From there I put some wood veneer into the lazier etcher and pressed go.
Step 3: Cutting Out the Veneers
I cut out the veneers in sets of two because I new I would want a front and a back and because I knew this would make it easier to line the two parts up in a later step.
Step 4: Glue and Press
I used wood glue to glue the etched veneers to some MDF board then used greece proof paper and another board under a chair leg to to apply even pressure without the risk of the two boards sticking together.
Step 5: Cutting Out
I started using a coping saw to cut out my pendant shapes before changing to the fret saw. These two saws are very capable though I would encourage thinking about health and safety in all steps but definatly from here on.
Fun fact I have only hurt myself with 3 tools in my workshop and the coping saw was one. I was 7 years old at the time but it still hurt and I would recommend avoiding this if possible.
Step 6: Make a Hole
This step could easily be avoided if you have a pillar drill, I am aware not everyone has the expensive tools and I like to experiment with alternative ways of achieving.
My alternative method of making a hole is to cut a line on each side of the hole you want to make and then carve and file until you create a channel.
Step 7: Glue It Up
I glued each side of the pendent and clamped them together using stick proof paper takeing care not to glue in the carved channel.
Step 8: Sand Finish and Thread
I used sandpaper to refine the shape before using sanding seal and melamine finish.
Once the finish was cured I threaded cord through my pendents and gave them to friends.
I hope you have enjoyed this instructable.
:)
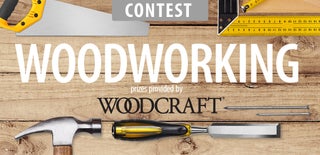
Runner Up in the
Woodworking Contest 2017
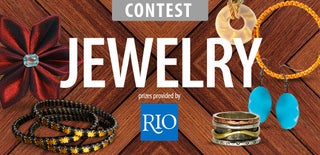
Participated in the
Jewelry Contest 2017