Introduction: Pallet Wood and Resin Chalkboard Message Board
I have made a few message boards like this in the past, but was looking to do a little something different this time. I figured it may be interesting to some so why not do it step by step so others can do it as well?
With this project I used:
Pallet wood
Chalkboard
Royal Palm Resin ( www.royalpalmresin.com )
Personal Protective Equipment: Safety glasses, earplugs, dust mask, gloves etc)
Table Saw
Dowel Jig (or a pocket hole jig)
Picture hangers
Cup/key hooks
Step 1: Finding the Wood
I decided to make this message board out of some old pallet wood I had around. You can make it out of almost anything, but the important part to remember is that you want to be sure the wood is thick enough to hold the chalkboard material.
In choosing pallet wood, I knew there were going to be nails and holes in the wood. I chose this wood intentionally because I wanted to fill the voids with resin to add a little something different to the message board.
Pull more boards off the pallet than you think you will use, this way if some break or they just don't look quite that right to you, you have more options to choose from.
Step 2: Strip Your Wood!
After I decided which boards I would use out of the pallet, it was time to clean it up. Make sure you pull all nails or staples out of the boards. Sticking yourself with one of those or running it through your saw blade will not be fun! I also cleaned out any knot holes or bug holes to later fill with resin.
Step 3: Layout Your Project
After I had cleaned out all of the nails and holes, I started laying out the project, looking to see which board I wanted where. I looked for the boards with the most character (i.e. the most holes haha). Once I finally decided on which section of the boards I had wanted it was time to go to the saw.
Also find yourself a board for the base of the message board. This can be used to hold the chalk and hooks for keys.
Step 4: Cut to Length
To decide what size you are cutting your pallet wood, you obviously need to know what size your chalkboard is going to be. I had some pieces of chalk board left over from previous projects so I just used one of those. You can either find a chalkboard from a hobby store or even use some of the chalkboard paint available from home improvement stores. If you decide to go that direction, make sure you follow the steps on the can and let the paint cure enough so you don't scratch it while handling it.
Seeing as how there is no set size to this project, you need to get the basis of your measurements for the pallet wood from your chalkboard material itself.
When cutting the boards, you want to take into account how you will be putting the chalkboard in it. I ran a groove along the sides of my boards to recess the chalkboard inside of it. Depending on your tool set ups, you can also just mount the chalkboard to the back of your pallet wood.
In either case, you want to be sure when you cut the pallet wood, you don't short yourself. You can always cut it again if its too long!
I decided to run 2 vertical boards, with my two horizontal boards in between. For the vertical boards, I found the measurement of the chalkboard and then added the width of both top and bottom horizontal boards.
For the horizontal boards I measured the top of my chalkboard.
I marked the distances out on my boards, deciding which piece I wanted there and then headed over to the saw.
Be sure to have proper PPE (personal protective equipment) when cutting on the saw such as safety glasses and ear plugs. If you are not comfortable or have not been properly trained on the saw, I suggest finding someone who is that is willing to help you.
Step 5: Size and Fit for the Chalkboard
Now that your boards are cut down and easier to handle, it is a lot easier to see the shape of your frame coming together.
If you put your piece of chalkboard on the frame, you will see that the frame is a bit too big for it. This is where I make my adjustments for how I will be holding the chalkboard.
Since I will be putting a groove in my boards, I will want to shrink them about 1/2" . This will allow me to put a 1/4" groove all the way around on the inside so I can recess the chalkboard into the pallet wood.
If you are just going to mount your chalkboard to the back of your frame, you may want to cut your boards a little smaller to give you more "meat" to secure your chalkboard to.
Step 6: Prepping and Cutting the Groove
If you have decided to cut the groove in your board, I find it helpful to mark the side that is to receive the groove.
Lay your frame out again and mark left, right, top and bottom. I also like to put an "x" on the board to be sure I am cutting the correct side.
Then it is time to set up the saw. For this I measured the thickness of my chalkboard and used a stacked dado blade set. I made the set up just a bit thicker than that of my chalkboard so I would not have a hard time getting the chalkboard in to the pallet wood frame. I also set the blade height at around 1/4" .
If you do not have a stacked dado blade set, you can use your single saw blade, just be sure you do not take out too much material. A little loose will be okay, but if the opening is too big the chalkboard may not be sturdy enough and rattle when writing on it.
I try to take a piece of the same wood (that isn't part of my project) to do my test cut on. This way I can test fit and location of the chalkboard without ruining a board I had intended to use for my project.
Step 7: Assemble the Frame
After I have cut all the grooves in the board, I dry fit all the pieces. If I am happy with how they fit, then I continue to assembly.
If you find there are gaps between the boards, you can make your groove deeper to help close them up.
Once you are happy with the fit, its time to attach all the pieces. There are a few ways you can do this. You can use a pocket hole jig or dowels. I chose to go with dowels for this one, for no other reason than I it had nearby!
I glued the dowels, slid my chalkboard inside and then attached the final piece. Make sure to clamp it to get a nice tight fit and let it sit for the glue to dry.
Step 8: Prepping for the Resin
After the glue dried (I waited 24 hrs), I removed the clamps and then taped the front of the chalkboard with blue painters masking tape to protect the surface from accidental spills when pouring the resin.
I then taped the backside of the frame to try and close up the holes that went all the way through so I did not have any resin come out the backside when pouring.
**Spoiler alert- whatever I did, didn't work! The resin just kept pouring out! More on that later!
Step 9: Mixing the Resin
With this project I knew I wanted to use resin to fill the voids in the wood. I have used resin in the past, but mostly for making blanks with pens that I make. That resin needs pressure to cure to avoid bubbles and I knew that my boards would not fit so I looked for another option.
I'm typically try to avoid resin from hobby stores as I do not know how long they have been sitting on the shelf and I didn't want to ruin my project with a bad product.
That's when I had found Royal Palm Resin. (available at www.royalpalmresin.com ).This is a 2 part epoxy resin which comes in 2 variations. The original and the thin. What drew me to this brand is that the thin version can be used without a pressure vessel to have it cure bubble free. There are also different sizes of each kind, so if you only have a small project you don't need to be stuck buying a gallon if you don't want it (though after using Royal Palm Resin I am going to start finding reasons to use it more). I had contacted the owner of the company on his facebook page and he was super quick and helpful with answering any questions I had (that's also a bonus to me - I usually have lots of questions and what better way to get the answers than from the person most directly associated with the product!)
Another bonus of this resin is that there is virtually NO odor at all. You could mix and pour this in your kitchen if you needed to ( I don't suggest this as it can be a bit messy but you get the point!)
When I got my resin it included detailed instructions on how to mix and use it properly which was great.
I followed them easy enough and got to mixing (make sure to wear some disposable gloves!)
I made way more than I had needed but I would rather have that had happen than to not have enough. Luckily I anticipated this and had one of my pen blank molds ready to use in case!
Make sure to properly mix the resin, getting rid of the "streaks" that you can see when they first get poured. When the streaks are gone, and looks perfectly clear, it is properly mixed.
For my project I wanted the resin to have a color, so I used a bit of a copper mica powder. These are available at craft stores or other online suppliers.
Once that was mixed in, I used to heat gun as suggested to warm the resin (making it more fluid and easier to pour, along with aiding in getting rid of some bubbles)
Once the proper consistency was reached it was time to pour!
Step 10: Pouring the Resin
Start filling your voids with the resin.
As you can see I'm not exactly the neatest which is why i put the painters tape down!
This is also when I had my major fail moment. The tape I had used on the backside of the frame failed miserably and I had resin seeping out the back.
If you end up using resin to fill the voids I suggest looking on other instructables here or videos on how to properly prep your surface to avoid this!
Well, slightly discouraged from this, I had set my frame aside to cure and to figure out what my next option could be. Coincidentally, the owner of Royal Palm Resin had contacted me to see how I was doing with my project! Talk about customer service! After some discussion with me, he said that there would be no problems adding another pour of his resin on top of what I had already done, it just needed to be clean of any debris or dirt.
Renewed in the ability of being able to fix the mess I had created, I went back to my project after 48 hours (allowing for a proper cure). I looked at the backside of the frame and saw that most of my holes had been covered with the cured resin. I took a hot glue gun and filled a few of the pinholes that were left and then made another batch of resin.
This time was a success! Now it was time to let it cure another 24-48 hours before I moved on to sanding.
Step 11: Sand, Sand and Sand Some More
After the resin had properly cured, It was time to sand the frame.
First before sanding, I brought the assembled frame back to the table saw to square up all the edges so they were uniform.
After that, I began sanding. I started at 80 grit with my belt sander, then progressed all the way up to 400 grit. Occasionally I would wipe the surface down with denatured alcohol to help remove excess dust from sanding.
For the base of the message board, I wanted to keep the rustic look going, so i just used my belt sander to wear down a groove on the board for a piece of chalk. You could also use a router to do the same thing, but I like the look of the sander technique myself.
Step 12: Putting a Finish On
After the message board is sanded and free of dust, its time to finish.
I put a thin coat of boiled linseed oil on first then I put on a few coats of lacquer to help protect the wood and give it a little shine.
This is an optional step if you don't want to do it, but I like the shine it gives the wood and the the resin also
Step 13: Attaching the Base and Hooks
Once the lacquer has dried, screw the base to the frame. I used some clamps to help pull the wood tight to the base, then just used a few wood screws to hold it.
You can use almost any kind of hanging hook you would like, but I went with D Ring hangers that were rated for a little more weight. Depending on the wood you chose, the weight of that combined with the keys hanging off the hooks can add up quick!
I then measured the front of the base and marked out for the key hooks, evenly spaced apart.
Step 14: Done!
Now that the message board is done, its time to find the right place to hang it!
I hope this was helpful to some people. I enjoy making these for housewarming gifts for people and in my own house as well.
Thanks for reading!
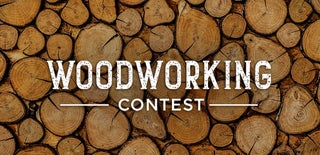
Participated in the
Woodworking Contest