Introduction: Paper Throwing Stars - Laminated Paper (Micarta)
What do you think of when you think of paper? Probably not throwing stars, but that is exactly what set out to attempt in our latest project. Now, while we must admit upfront that these particular throwing stars aren't functional; they certainly could be. For the sake of this project, however, we'll treat them as purely decorative and share our thoughts on how we could make them functional.
Here are the materials and tools that we used to create these paper throwing stars.
Materials:
- Construction Paper (20 sheets, two colors)
- Epoxy Resin (Famowood Glaze Coat) but any will work
- Latex Gloves
- Silicone Tray or Mat (waxed paper will work as well)
- Containers for mixing resin
- Spreader or Roller (for applying resin)
- Spray Adhesive
- Pattern (get it here)
- Spray Clear Coat
- Spray Paint (optional)
Tools:
- Drill Press or Drill with bit sized for holes on the pattern
- Band saw, scroll saw or coping saw for cutting straight edges
- Various Sanders (we used a belts sander, strip sander and hand sanded some)
Before you get into the directions, take a few minutes and watch the overview video of the entire project so you can get a better feel for the following steps.
Step 1: A Look at the Materials
The materials you'll need are pretty basic less the resin.
Latex gloves are a good idea since the resin is extremely messy and ridiculously sticky. Not to mention it stinks a bit. Not as bad as polyester resin, but still not amazingly pleasant.
Small paper cups work good for the mixing as do plastic cups. For some projects you may want cups with measuring lines, but that is not the case for this project. We just mixed up what we thought we would need.
A tongue depressor/popsicle stick works great for spreading the resin around. Peter Brown also had a great idea in his Micarta project where he utilized an HDPE roller. It appears to work well also.
The silicone tray (cake roll pan) isn't necessary, but it did help keep the resin in one location. Waxed paper or a silicone mat would work well also.
The resin we used is Famowood Glaze Coat. This is just personal preference and one that we are familiar with. Any epoxy or polyester resin would do.
Obviously we used some paper as well. We opted for construction paper. In hindsight, cardstock may have been a better choice, but we'll get to that later.
Step 2: Mixing the Resin
There are a lot of tutorials and Instructables about how to mix resins so we'll keep this short. Basically, this is a two-part epoxy resin. There is a part A and a part B. Both get mixed together in equal amounts. Mix them well and that's about it. We can't say how other resins are mixed because we primarily use two-part epoxy resins. Polyester resins are a whole different ball game and have a lot of varying mixing ratios.
For this project we just mixed it in halves to fill our cup. Really, we just eye-balled this one. No science or mathematics involved.
Step 3: Layers of Paper Into Micarta
This entire step is primarily just layering the sheets of construction paper or whatever paper you use. Each layer receives a healthy coating of resin that is spread out as evenly as possible. Construction paper is a thirsty beast and will drink ever drop of resin you give it.
It's important to note that we did press firmly on each layer and somewhat rub it into the layer beneath it.
We think this may have been a mistake on our part. Perhaps it was how much the paper soaked in the resin, but as you will see in later steps, there are some spots that decided they didn't want to adhere as well. Lesson learned. Again, we'll get to that.
After all of the sheets are laminated or layered together, we let it sit to cure for the recommended 12-24 hours. We did set a case of water on top of the layers with another silicone layer in between, but this was an after thought and we didn't capture image or footage of this.
Step 4: Checking the Sheet
We removed the laminated sheet from the silicone tray. It came out with ease. We checked it by bending it and looking for voids. At the time it looked great and there was absolutely no flex.
Step 5: Prepping With the Pattern
We placed the pattern on the smoothest side of the laminated sheet using a spray adhesive. Any type of adhesion for the pattern will do, including a glue stick. It could also be a good idea to add a layer of masking or painters tape first, though we didn't do this.
You can get the pattern on our website if you would like this exact same one.
Step 6: Cutting Out the Throwing Stars
To make things as easy as possible, we decided to use a forstner bit to remove all of the holes and rounded areas first. It is important that the sheet is flat on some sort of waste or spoil board. If not, the back end will likely tear out. Even with the a sacrificial piece we still had some tear out.
We used our band saw to cut all of the straight lines. We cut as close to the line of the pattern as possible. You could also use a scroll saw or coping saw. If all goes well, you should have what looks like a pretty cool throwing star shape.
Step 7: Sanding and Shaping
We used the belt sander to get both the faces as clean and flat as possible. This was a first attempt for us, so the first one or two we did weren't so pretty. This also helps remove the leftover pattern and residue from the spray adhesive.
The strip sander was used to add the faux sharpened edges. This worked well and allowed us more control than the belt sander would have.
Hand sanding with 240-grit sandpaper helped refine the edges a bit.
NOTE: this is one of the places where things started to go wrong. While sanding some of the edges started to peel away. The culprit is still unknown to us, but we think that it was either a lack of pressure during curing, the fact that the paper used soaked in the resin so well or the heat from sanding caused it to come undone.
Regardless, it can be repaired with a dab of super glue and some minimal hand clamping for a few seconds.
Step 8: Finishing
All of the throwing stars were sprayed with a generous coat of semi-gloss clear coat. This helps to brighten them up a bit and give them a little shine. Another added benefit we discovered was that it aided in keeping the paper that had come loose adhered to one another.
We left two unpainted and then painted one with a copper-metallic paint and another with a silver paint. All of them were still sprayed with clear coat.
Step 9: All Done!
For a first run we were pleasantly surprised with how they turned out. Again, they are purely for decoration or display, but the process was a great learning experience.
What We Learned
- Cardstock may have been a better choice since the resin would have laid between the layers instead of disproportionately seeping into each layer of construction paper.
- If there had been better adherence with the layers a decent point and edge could have been put on these.
- Resin and paper being sanded smells... odd.
- Clamping pressure may be something to look into, rather than weighted pressure
Hopefully, you had some fun seeing how these were made. Even more so, we hope it inspired you to make something. If you have any questions or would like to weigh in on what might have worked better, feel free to do so in the comments.
If you didn't get a chance, make sure you check out the video. We would greatly appreciate it. Also, check up in the corner and if you like this particular project, consider voting for it in one of the contests it has been entered in to.
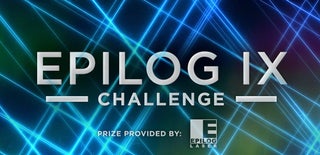
Participated in the
Epilog Challenge 9
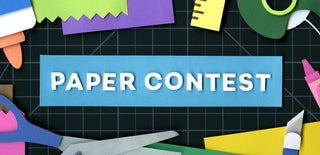
Participated in the
Paper Contest 2018