Introduction: Patterned Plywood Hatchet Restoration
Yes, this is a guide on how to restore a particular kind of hatchet, HOWEVER. It also contains information on how to create a patterned plywood design, how to repair a "perfect handle" style tool handle with a metal tang running down the middle, and other generally helpful ideas on tool restoration and woodworking.
Plus these hatchets aren't difficult to find or particularly expensive. So, you can easily replicate this finished product on your own!
---Please check out the video at the top of this guide to ensure a fuller understanding of the steps involved, and also because I took a long time making it and I think you'd like it.---
Thanks
- Keith Decent
Note: You will be handling a hatchet during the project, and hatchets CAN be sharp, in very deceptive ways. PLEASE take every precaution and be sure to wear any and all Personal Protective Equipment needed for each step of the build!
Supplies
In order to restore this hatchet, you'll need
Tools:
- Table Saw: or any saw capable of safely cutting a long strips of plywood and also cutting 45 degree angle down the long side of that strip.
- Chop Saw: Or any saw capable of safely cutting 1in slices off the end of your strips
- A good prybar: or anything that can help remove the handle from the hatchet. I chose a beefy, flat head screwdriver.
- Grinder: Or anything capable of cutting the pins of the hatchet handle. A hack saw or even a file can work for this.
- Clamps: You're going to need to be able to clamp a section of 10" x 5" plywood pieces together in a jig, as well as clamps that can tighten effectively on the handle of the hatchet. I recommend 12" quick-close clamps for each.
- Packing Tape: or any other tape that wood glue won't stick to
- Blue Tape: or any appropriate masking tape
- Wood Glue: epoxy could work too, but really, just use wood glue here
- Cleaning Tools: I used a wire wheel and a Dremel with some fine polishing bits, but you can use anything to clean the metal of the tool that you think will work. Rust dissolvers, wire brushes, polishing pads. Whatever it is you are comfortable working with safely and according to directions.
- Band Saw: or any saw capable of cutting out the curved shape of the handle safely. This could be a coping saw or a jigsaw as well.
- Sanders: I utilize an oscillating belt sander, a random orbit hand sander, and a power-feed drum sander. You can do all the same work with a belt/palm sander and some hand sanding, or even with rasps and sandpaper if you want to.
- Hand Saw: or any saw capable of safely cutting a small dowel into an even smaller dowel
- Drill/Drill Press: You'll need to make a few holes, If you're making a custom dowel, like I did, you'll need a hand drill. Have a bit the same diameter as the round holes in the steel handle.
- Pencil: For marking things
- Two Small Screws: Something that will securely hold your scale into the handle for the sanding portion of the project. Nothing too long, less than 1/2" long should do fine. Just make sure the heads are bigger than the holes so they don't pull through.
- Sandpaper: For the final sanding of the handle, you'll want to use grits from 80, 120, 220 and then to 400.
- Hammer/Mallet: You might need one for stubborn parts.
Materials:
-The Hatchet: This guide is for a 1940s-1960s model "Boy Scouts of America" or "BSA" Hatchet by The Bridgeport Hardware manufacturing Company. If you'd like to create your own version, you can search "Vintage Bridgeport BSA Hatchet" on E-bay and you should find multiple listings. Make sure the one you choose has the same style handle as the one in this guide.
- 3/4" Plywood: Use a HIGH QUALITY plywood with a VENEER CORE. I can't stress this enough. If you cheap out, you will end up with voids and LOTS of filling, and it will not look as good as the example. I used 3/4" Baltic Birch plywood. You don't need very much so finding smaller pieces in a scrap pile or specialty dealer is recommended. Rockler is a good place to start.
- 1/8" Wood: I used some leftover black walnut, but you can use any 1/8" wood, but hardwood is recommended. If you have the tools, you can create it yourself out of thicker material, or just buy it outright. Again, Rockler has this stuff.
- Hardwood Dowels: I don't know the exact size of the dowels required for this project, but I was able to make the correct size out of a 1/4" dowel I already had, using the techniques I will show you. You can also cut a 1/4" square strip of wood and use that.
- Finish: I used wipe-on poly for my handle finish. you can use whatever clear finish you are comfortable with or prefer. I also recommend picking up some wax (like butcher's wax) for rust prevention.
Step 1: Tear Down the Hatchet
- If, like mine, your hatchet still has the handle and pins attached, you'll need to remove these, along with any tape that is holding the thing together.
- Use your pry bar to remove and loose or broken handle pieces first
- Use your grinder/hacksaw to cut the metal pins holding the handle in place.
- use the hammer to knock the pins through the frame if they are stuck
Step 2: Clean the Hatchet
- Starting with a rough wire wheel (I have mine chucked into a hand drill and clamped to my bench, with a clamp on the trigger, BE CAREFUL if attempting this and only do so if you are comfortable taking full responsibility for your actions), clean the rust and dirt off of the hatchet frame.
- You can use whatever cleaning tools you have to do this but the idea is to use the rough wire wheel or brush, then a finer wire wheel or brush, then a scotchbrite type of plastic wool, then some plastic or rubber polishing tools. I used Dremel bits I already had, but you can use whatever you have available.
- I wasn't going for a high polish and brand-new look, as it would ruin the beauty of the wear already on this piece. Feel free to get yours to whatever stage you prefer.
Step 3: Create the Plywood Strips
- The goal of this step is to have a long strip of plywood, where the flat ends look like a right triangle with one of the 45 degree corners cut flat as shown in the picture (sorry its a bit blurry)
- Set your saw to cut a 45 degree angle in the long edge of your plywood.
- Carefully cut the piece all the way down the length, at the very edge so you don't waste any wood.
- Set your saw to cut a perfect 90 degree angle.
- Adjust your fence/saw so that you're cutting 1/8" behind where you would cut to make a perfectly triangular strip. Basically look where you'd have to cut to make a perfect triangle in the end, then adjust so you'll be cutting about 1/8" further into the board.
- Cut down the plywood and detach your strip.
- Repeat all of the previous steps to make at least 4 strips. You'll want probably over 200 combined inches of strip by length.
Step 4: Create the "V"
- If your strips are very long and unwieldy, you can cut them in half, I used about 36" long sections for mine.
- Spread glue on the 45 degree angled side of two of your strips
- press the glued sides together and secure with tape or rubber bands. take extra care to make sure that the edges all line up perfectly and to wrap the tape or bands VERY tightly. Clean up any "squeeze out."
- You should be left with what looks like the block letter "V," but extruded.
Step 5: The Jig
- While waiting for your strips to dry, you can create this jig. Using leftover plywood, make a rectangle about 12" x 6"
- Glue and or nail two flat strips (12" x1" and 5" x 1")to the top and side edge of the rectangle.
- Cover the surfaces of these in packing tape, making sure to not leave any wrinkles.
- Take a 12" x 1" strip and cover it in packing tape, and do the same for a 5" x 1" strip
- You should have something that looks like the above image. If not, take a minute, think about what went wrong, and try again. Note my bottom strip of plywood is smaller than 5", and I'll explain this later.
Step 6: Building the Pattern
- Once the "V" strips are dry, unwrap and discard any tape or rubber bands.
- Mark and measure on your chop saw or equivalent so that you are prepared to create 1" slices of your strips.
- Carefully cut one inch chunks until you are no longer safely able to do so. Repeat until you have about 80 chunks/slices.
- sand any chips or rough edges on your chunks, making sure that the small "v" shaped valley and peak at the top and bottom are clear of glue/debris. Taking the time now to get it right will ensure a clean and beautiful fit later.
- arrange your chunks in the jig in the pattern shown, spreading glue on the surfaces where it will touch another piece. Mine needed to be 4 pieces wide, more or less, so I'd suggest starting there. (in the video and pictures I have 3 wide and had to add a few in later)
- Check the handle of your hatchet against the pattern before clamping to ensure you have enough space.
- Clamp the long sides of the jig together with the pieces in between, being careful that the pressure does not cause the pattern piece to buckle or bend, and that all of the pieces are tightly fit together.
- Mark the short strip you cut to the inside width of the jig, and then cut it to that length, and then clamp together the short sides, as shown. Again, be careful not to let it buckle.
- Note, you will be doing this twice, because there are two handle scales.
Step 7: Prepping Your Pattern Piece
- Take the patterned piece out of the clamps.
- Sand the piece flat and fill any gaps with wood glue and sawdust
- Once dry, trace the shape of your hatchet handle onto the patterned piece.
Step 8: Cutting the Handle Parts
- Take your masking tape, and use it to make a template of the inside of the hatchet handle, in between the "walls" of the handle cavity.
- Transfer that template to your 1/8" material and carefully cut out along the outside using your bandsaw or equivalent tool. use a sander to fix any parts that are too wide, checking it against the hatchet handle. Remove the tape template (or recreate it if necessary) and repeat this step once it fits.
- Carefully cut out the handle shape from your patterned pieces. NOTE that you need to cut to the OUTSIDE of the shape. It must be larger on all sides than your hatchet's handle.
Step 9: Gluing Up the Handle
PLEASE NOTE: in these steps, you are making handle scales for BOTH sides of the hatchet, so you are making two sets in the OPPOSITE shapes of each other. Don't make the handle for the same side twice!
- Test fit your 1/8" hardwood handle piece in your hatchet's handle area. Be sure it sits flat and just a little bit higher than the surrounding walls. If it doesn't, then use sandpaper or files to adjust it until it does.
- spread glue on one side of your 1/8" hardwood handle piece.
- Drop your glued piece into the handle area, glue side UP
- Place your corresponding patterned piece on top, lining it up so it overhangs the sides and bottom of the steel hatchet handle
- Clamp them in place
- Repeat for the opposite side
Step 10: Shaping the Handle
- Do the following steps for each handle scale, ONE at a time
- Place the handle piece into the handle cavity on the hatchet.
- Drill two very shallow holes into the back of your handle scale through the axe handle in order to mark the positions
- Screw the handle piece to the hatchet using your short screws. Make sure they fit into the handle holes in the hatchet and have heads larger than the holes, so they don't slip through
- Use your belt sander or equivalent to sand the edges flush with the steel part of the hatchet handle.
- Use your belt sander or equivalent to roughly sand in the curves and angles for a comfortable grip. Use any remaining old handle parts or pictures for reference. You'll be removing a LOT of material here, so be patient and check your work often.
- Sand the rest of the shape with your 80 grit paper on your palm sander or equivalent and then work your way through the grits from 80 to 120 to 220 to 400, to smooth out the piece.
- Fit your scale into the hatchet handle. If there is a gap between where the plywood part should sit flush against the steel (because your hardwood flat part is too thick) then use a sander to thin the hardwood part, carefully, until it all sits nice and flush. You may need to slightly round or chamfer the top, long edges of the hardwood piece to ensure a tight fit.
Step 11: Creating the Dowels
- If your dowel isn't the exact right size for the handle holes or you are making one from a square 1/4" x 1/4" strip, sharpen the top with a knife or pencil sharpener or with a sander, then chuck the flat end into a drill
- Run the dowel or strip through the steel handle hole with the drill on a high speed setting, applying light pressure until it starts to break through. It will shave itself down to the same size as the hole. Be careful, as the metal WILL get HOT when you do this.
- Remove the sharpened end of the dowel and mark up 1/2" from there
- Cut the dowel into 2 1/2" lengths using your hand saw or equivalent. I do NOT recommend power tools for this step as it is very dangerous to use them for small parts.
Step 12: Drill Your Pin Holes Into Your Scales
- Using a drill press or equivalent and a drill bit the exact size of the steel handle holes in the hatchet (or at least a TEEEEENY bit smaller but not too much) drill 1/4" into the scales where you previously drove the screws, being careful not to over-drill and break through any thin parts of your handles.
- Be sure to keep the holes as straight and perpendicular as you can to the flat bottom of the scale.
Step 13: Handle Assembly
- Without using glue, insert the dowels into the holes of one scale
- Insert the scale with the dowels into the hatchet handle with the dowels going through the corresponding holes.
- Align the other scale with its holes over the dowels and press them together.
- Take note of any gaps or mistakes and fix them. You can further trim the dowels if the handle doesn't close all the way, for example. Do not move on to the next step until they are fixed to your satisfaction.
- Disassemble the handle and add glue to the all of the holes in both of the scales
- Repeat the first 3 parts of this step, and clean up any "squeeze out" or glue drips.
- Add clamps and let sit until cured.
Step 14: Finishing the Hatchet
- Using wipe-on Polyurethane or your chosen clear finish, coat the handle and let dry. I did 4 coats of poly, but you probably need more or less based on your choice. Make sure to remember the top and bottom edges.
- Using Butchers Wax (or your chosen axe wax), coat and then buff the entire hatchet, handle and all. This will ensure rust prevention.
Step 15: Final Sharpening
- There are many MANY tutorials on how to sharpen a hatchet out there. I personally just hold the blade at it's bevel angle against a wet stone and then move it around. You can watch the embedded video for my method. You may have your own, or you may find one you like better. Either way, it's important to not do this step until you've finished the piece, as the small bits of swarth and scum could get embedded in your nice handle.
- It's also worth noting that sharpening last will help prevent nasty cuts while you're working on the project itself.
Step 16: Enjoy!
There you go! You have a beautiful piece that is also a useful tool, and I imagine you've learned a couple of useful techniques along the way! have fun and be safe!
If there's any mistakes in this guide, or if you found it useful, let me know in the comments or by message.
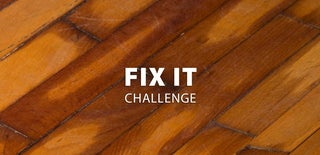
First Prize in the
Fix It Challenge