Introduction: Polyurethane Foam Soft Robot
Short Description
Learn how to build a soft, pillow-like robot using polyurethane RTV molding! [Difficulty: Easy to Medium]
Long Description
Soft robotics is an exciting new sub-field in the broader category of robotics. According to Wikipedia:
"Soft Robotics is the specific subfield of robotics dealing with constructing robots from highly compliantmaterials, similar to those found in living organisms."
Most soft robotics in research labs use molded silicone air-actuator systems. This Instructable will show you another method of soft robotics, where hard, traditional electric motors are covered with soft, molded polyurethane foam, negating the need for an air compressor and simplifying electronics to that of traditional hobby robotics. (Note that this Instructable is focused primarily on the tools, techniques and methodologies of using polyurethane foam as a construction material, and not the electronics and computer programming associated with building robots.)
Intro to Polyurethane Foam:
Polyurethane is a common and relatively low cost material used to make memory foam pillows, car seats, certain types of foam packaging and more. Typically, polyurethane is kept in a 2-part liquid state that when vigorously mixed, performs an exothermic chemical reaction that results in a solid shape in the shape of the mold it is poured into. Polyurethane comes in many different curing times and material properties, and can range from hard and soft plastics to rubbery to foamy.
Step 1: 3D Print Molds
The first step is to create a 3D-printed mold where the polyurethane can be poured into. Any standard 3D-printer material will work fine, such as PLA, ABS, Nylon and more. Sample molds for this project can be found in this Github link, courtesy of a creatively cool collaboration with Fine Arts Miracles.
Tips: Designing molds for polyurethane foam mold making may seem like a daunting process, but is actually rather simple if you keep these notes in mind:
- We recommend using a mold wall thickness of 3 to 4 millimeters. Additional thickness may make it harder to remove the mold.
- Separate the mold to multiple pieces. Really think about how the finished polyurethane foam cast will be removed once it is done curing inside the mold.
- Add a hole for pouring mixed polyurethane liquid into. This hole will be also used to vent out exhaust gases and liquids. A hole size of at least 10x10mm is recommended.
- Add as many curves and as little sharp corners as possible - this will make it easier to remove the polyurethane cast later on.
Step 2: Foam Making Materials
Once we have all the molds 3D-printed, we are going to need a few materials to begin polyurethane foam casting. To begin, we recommend these parts: (sample links provided for convenience:)
Materials
Equipment
Step 3: Setting Up for Polyurethane Casting
Setting up the work area:
One you have all the materials purchased and ready to go, go ahead and setup your work environment. Note that this project will get very messy! Wear gloves, goggles and the apron. Cover your work area with the garbage bag(s) or newspaper(s), which will protect your working area from slime and grime. Have the paper towels handy.
Preparing the 3D-printed molds:
Use the paint brush to apply generous amounts of mold release to all internal surfaces of all 3D-printed molds. Do this multiple times until every internal 3D-printed mold surface is glistening with mold release. Note that you should work fast, as the mold release has a tendency to dry up fast.
(Tip: Pour the mold release into a cup, dip the brush into a cup, and then apply the brush. Note that the cup and brush is not necessary if you have a sprayable mold release. Also note that not all mold releases are the same - contact your mold release manufacturer to see if it can cleanly release polyurethane foam.)
Step 4: Clamping 3D-printed Molds
Clamp the 3D-printed molds tightly so that the majority of viscous liquid cannot pass through in between the parts. Do not clamp the parts too tightly, or you may break the 3D-printed molds. Note that there is an opening for pouring 2-part mixed liquid polyurethane foam into. Do this for all of the molds you wish to cast polyurethane foam out of. (Note: This is easier with more clamps. If you run of clamps, you'll have to wait until the current foam piece is casted and cured, or buy more clamps.)
Step 5: Mixing Part a and Part B for Polyurethane
Once all the 3D-printed molds have generous amounts of mold release applied and are tightly clamped together with an opening to pour viscous liquids into, we can begin the polyurethane casting process. Use the mixing cups to measure and pour liquid Parts A and B into a cup at the manufacturer's recommended ratio. Vigorously mix both liquids until they are uniform (be sure to finish mixing before the manufacturer's listed Pot Life, otherwise the foam will began expanding in the cup and not the mold. Use a stopwatch to keep track of time).
Note: Most polyurethane foams come in a liquid 2-part mix, Part A and Part B. Before using them, read the manufacturer's instructions very carefully, as not all polyurethane foam mixes are the same. In particular, look at the Pot Life, the Mix Ratio, the Cure Time, and the Expansion Rate. Here is a quick description of each:
- Pot Life is the time you have to mix the two liquid parts together before the chemical reaction starts.
- Mix Ratio is the ratio in which you should use the two liquid polyurethane parts.
- Cure Time is the time it takes for the foam to finish forming after being poured into the mold.
- Expansion Rate is the rate at which the volume expands from the liquid state to the solid state.
Also note: It is possible to add various colorants and other additives to the mix to alter the cured foam's properties such as colors, UV tolerance, density, squishiness, hardness, cure time and more.
Step 6: Pouring the Mix Into the Mold
Once you have vigorously mixed the Polyurethane Parts A and B in a mixing cup, pour the mix into the clamped 3D-printed mold. Cover the top with your remaining mold pieces if necessary, though we recommend leaving a small hole open somewhere on the clamped mold for exhaust gases and liquids to escape. The foam, if mixing correctly, should uniformly begin to expand and change from a liquid state to a foamy gooey solid state. Use the stopwatch to wait the manufacturer's recommended cure time. Once the manufacturer's recommended cure time has passed, the foam should be done expanding and will be no longer be gooey, but rather soft, pillow-like and foamy like a sponge.
(Note that this is an exothermic reaction and the foam is expected to be somewhat warm. It is not hot enough to melt the plastic however.)
Step 7: Removing the Polyurethane Foam
Once the manufacturer's recommended cure time has passed, you can now remove the cured polyurethane foam from the mold. Note that even with generous amounts of mold release, the resulting polyurethane cast can be quite difficult to remove, due to friction and the initial complexity of the mold design. Be careful not to rip the polyurethane foam when attempting to remove it! We recommend using tools like paint spatulas to help you remove the casted polyurethane part. (Removing the foam will be easier with softer, more flexible foams and simpler mold designs.)
Step 8: Common Errors for Troubleshooting
If this is your first time making polyurethane foam, your first shot is likely not going to look very pretty. Common defects in the first mold are inconsistent hardness, splotches, incorrect volume, remaining gooeyness, and near impossibility to remove the casted foam. This can be caused by a variety of newbie mistakes:
- Inconsistent hardness and splotches are usually caused by not vigorously mixing the liquid polyurethane enough.
- Remaining gooeyness is usually caused by not using the correct mix ratios for Parts A and B, or by not vigorously mixing the liquid polyurethane enough.
- Incorrect volume is usually caused by not pouring the right amount of expanding polyurethane liquid foam into the mold, or by not vigorously mixing the liquid polyurethane enough.
- Near impossibility to remove the casted foam is usually caused by poor 3D-printed mold design (with a lot of sharp corners or hard to get to areas) or by not having added enough mold release at the beginning.
Step 9: Finishing Your Polyurethane Foam Robot
To finish the rest of the polyurethane foam robot, repeat steps 3 to 7 for the remaining 3D-printed mold pieces. To adhere different pieces together, we recommend using a foam-safe glue or using additional polyurethane foam as the bonding agent (polyurethane has a neat property of adhering to polyurethane and other surfaces very, very well).
This Instructable was written with the purpose of hopefully enlightening 3D-printer enthusiasts how to create their on expanding polyurethane foam parts using RTV molding. If you are a 3D-printer enthusiast, we hope this Instructable was useful to you, so that you may begin your very own polyurethane foam molding adventures ;)
Cheers - John Choi
(P.S. Special thanks to Fine Arts Miracles for collaborating on this project and the Frank Ratchye STUDIO for Creative Inquiry for their advice and support during this learning process.)
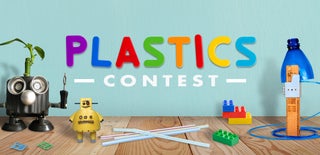
Participated in the
Plastics Contest