Introduction: Quick Clamp / Release Vice
I do quite a lot of work with circuit boards and small mechanical parts and was finding the 'helping hands' crocodile clip type tool too fiddly and a bench vice too big for my needs, so after a bit of thought I designed my own light duty 3D printed vice with a novel tension and release method.
This vice is ideal for holding small parts or circuit boards up to 70mm (2 3/4") while you adjust, solder or glue etc and has an advantage over a screw thread vice when working with delicate components in that you can better feel how much pressure is being applied.
To clamp, insert the workpiece into the jaws, pull the elastic cord through the slot to a suitable tension then pull the cord down to lock.
To release, simply pull the cord up. The tension on the elastic is eased and the workpiece freed.
After a bit of practice it's a matter of a couple of seconds to clamp a workpiece in place.
Step 1: 3D Printed Parts
The .STL files for the three parts are attached. If you do not have access to a 3D printer but want to build this project you could use one of the many printing companies who will print one-offs for a reasonable price. You can upload the STL files to them and receive a completed print back in a few days.
The obvious choice of material for the print (for me, anyway) is PLA, due to its rigidity, 'slippiness' and low shrinkage. Nylon would be stronger but as this is only intended for light use, PLA is adequate for the job.
I printed this onto glass with 3 shells and 30% infill. If your printer has trouble with bridging then support underneath the roof of the 34mm recesses in the base would be a good idea. Mine printed fine without.
My 'magic formula' for adhering the first layer of a print is a strong sugar solution. Smooth it onto the glass plate (heated to 50°C) with a finger and it stays tacky, providing good adhesion. I've just changed from clear to frosted glass and finding the same adhesion but a better finish on the contact layer, so I'm happy with that.
My first prototype of this was almost spot on and the only changes I made to the final version were to add a small round to spread the forces on the base vertical, a centre-post in the bottom recess to centre the washers and to narrow the cord gripping jaws slightly. I initially had a cut-out in the jaws to hold a PCB but found this was unnecessary once I added the neoprene.
Step 2: Additional Parts List
1) 3D printed base, slide and toggle as above.
2) 6 x 32mm (1 3/8") washers or similar to add weight to the base.
3) Small amount of 1mm (1/16") self adhesive neoprene sheet. Neoprene is a dense rubber and should last a while as long as it's not overheated (e.g. by soldering too close). 1.5mm or 2mm would do equally well.
4) 4 x self adhesive feet. Not vital, but gives more of a non-slip to the vice. Mine came from a small network switch box. Alternatively use a bit of the neoprene mentioned above.
5) A 200mm (8") length of elastic bungee cord, 3mm (1/8") diameter or so. 3mm is ideal but the gripping method will adapt for a bit thinner or thicker.
6) Adhesive : I used the foaming polyurethane Gorilla glue but cyanoacrylate (superglue) or epoxy could be used instead.
Most of the additional parts you will probably already have around the house / shed. If not, eBay or the local hardware shop will. The only thing I had to buy was the neoprene rubber sheet.
Step 3: Fettling the 3D Printed Parts
Once assembled the slide should move freely along the base of the vice; the exact dimensions give a 0.2mm clearance between the sliding parts. However, depending on how well your printer is set up you may well find that the slide . . . won't. Fear not, but do not force the parts otherwise they may jam immovably.
First of all, check the edges of the slide bottom layer. Depending on your first layer nozzle height, this may be squashed out slightly (to give adhesion to the print bed) and need a bit of sanding or trimming with a blade. Also check for over-extrusion at the edges. Once you can feel that things are beginning to fit, spray / rub some wax furniture polish onto a cloth and give the sliding parts a wipe. This will make all the difference. Now slowly and carefully work the slide backwards and forwards along the base and you will feel things beginning to ease. On the two I made the slide will move from end to end under gravity alone.
Step 4: Assembly
1) Cut a strip of neoprene rubber approx 12mm (1/2") wide. I found it's tidier to cut the split piece to size before attaching, rather than sticking it on then trying to cut out the middle section. Remove the backing and attach to the jaws of the vice.
2) Glue the washers into the recesses in the base of the vice to give it greater stability and a solid feel.
3) Pass the bungee cord through hole in the slide and knot it. A bit of glue will stop the knot from pulling out and keep it in the recess.
4) Pass the other end of the cord through the toggle and knot it so the unstretched length of the cord puts the slide around 3/4 of the way down the base. This will stop the slide from coming off the end when not in use. Trim off the excess length.
5) Attach the four feet, and you've finished. Go and make another one !
Step 5: Final Thoughts
Although the vice works perfectly well, it would be nice to not have the cord slot in the middle of the jaws. To that end I'm working on a redesign of the cord grip which will retain the simplicity and effectiveness of the vice but not have the split jaws.
First pass for this is to simply turn the slot through 90 degrees but I think this can be improved upon with a button-press locking mechanism. I will update the Instructable once this is working.
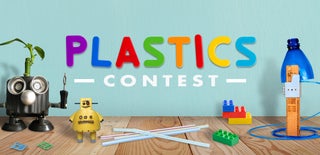
Runner Up in the
Plastics Contest