Introduction: Quilter's Sewing Machine Table.
Here, inevitably, is a project made for my wife, Lizzyastrouk, as an accessory for her at the Manchester Maker Faire.
It provides the quilter with a larger level surface to arrange squares on, whilst sewing.
Thrown together in a morning, it uses 10mm thick acrylic for the top surface, into which I cut the outside profile of her favourite sewing machine.
Step 1: First Measure Your Machine.
I was fortunate that Lizzy has a sewing table with an insert cut to take her machine, so I just copied that.
You need to measure, reasonably accurately the profile of your machine at the level of the platen. I'd make a template to check the design fits !
My table size was limited by what I could fit into my laser cutter, but you don't have to use a laser, and you don't have to use acrylic, but it does look pretty.....
I also added a series of parallel engraved lines to the platen, 0n 12.7mm, 1/2" centres, as a sewing guide - so the long lines you see DON'T go through !
Step 2: Cutting.
Laser cutting is really simple, if you've got it, but otherwise standard wood techniques work just fine. I used a fine pitched circular saw to cut the profile to final size outside, to save over an hour on the laser.
If you use acrylic "by hand", you can scratch the guide lines in with a piece of hacksaw blade, sharpened into a very thin chisel.
Step 3: Edge Polishing.
Edge polishing can be done in two ways - the traditional file/ abrasive/abrasive/abrasive/abrasive/metal polish method.....or the fire method.
The fire method needs a small, very hot, blowtorch, speed, co-ordination and courage.....
1.) File the edges smooth to remove the saw marks.
2.) Use a Stanley knife (box cutter) blade as a scraper, and plane off the file marks.
3.) Take a hot torch - I'm using an oxy-propane torch, and FLASH it down the edge - it takes around 2 seconds to do one long 600mm (24") polish.
Here's an instructable on flame polishing
Here, I've used 6mm corner radiusing cutter in my router, and gone right round the frame. It helps let the fabric move freely. around the table.
Step 4: Stand.
The stand consists of 5 pieces of 10mm (3/8") ply, to form a platform exactly as high as the sewing machine platen - the thickness of the new plate.
Cut the strips on a table saw (with appropriate precautions) and then glue together - making sure the strips don't interfere with where the machine will sit !!!
Clearly there's actually scope to put some more bits and pieces storage in the underbox - if I revise the design, I'd probably open the front of the box up a bit.
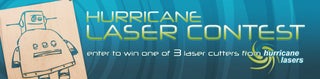
Participated in the
Hurricane Lasers Contest