Introduction: RMS - 3D Printing Clear RMS Brick With the Objet
This tutorial is for exploring and learning how to use the 3D Objet printer with the Vero Clear and Vero Black materials to embed a branded content into CAD model a modular form. This instructable is based on a prototype designed for the Resilient Modular Systems, PBC Modular Brick Unit.
Resilient Modular Systems is a Public Benefits Corp, and leader in innovative sustainable modular components for the building industry in emerging markets
More information - http://resilientmodularsystems.com
Facebook - https://www.facebook.com/ResilientModularSystems
Twitter - http://twitter.com/RModularSystems
Designed by -
Wendy W Fok | Founder
Resilient Modular Systems, PBC
Step 1: 3D CAD Model
Step A:
Hand-sketching is a large part of my design process.
Much of the process of making this CAD model was based on trying to find the best solution of constructing a casted version of a 3D model that would work with a either 2-Part or 3-Part mold, for the larger part of the RMS mission. Therefore, a lot of the exploration is to look into ways to best manipulate a form that could be easily formed into a simple injection mold system.
Step B:
One could first model the form of the modular in any 3D CAD software, where then the font (an extruded solid text geometry) can then imbedded within the modular formwork, and then prepared into a STL file.
This particular form is designed in McNeel's Rhinoceros 3D (this could also be easily designed in Autodesk Fusion - an open source and free program) and then exported into a STL file, to be imported into the Connex system that imports the STL File for printing into the Objet printer. The font that is used was our RMS logo text proprietary to Resilient Modular Systems.
Step 2: Importing STL File Into Connex for Objet Printer
Before making the print, it was made sure that the steps of the print was prepared properly, that there were no errors within the file system, and then the Objet machine that I was using was cleared, from the person who used it; otherwise, there could be a risk of a collision of the files, and/or the print-head are not cleaned and the print will not come out as well. Before printing, I also made sure to record all the support materials, and various other printing materials that are used for the project.
Step 3: Clearing Out the 3D Prints
This particular print took around 2 hours to print. Therefore, immediately after the print was ready, I made sure to go to the machine and take out the prints, so that the resin does not harden too much onto the print bed, and destroy the bed. Also, this would allow one to easily clean off the pieces, to ensure that the Vero Clear materials are accessible.
Step 4: Cleaning the Print-head and Machine
Shortly after taking out the 3D printed pieces, one is suggested to clean out the print heads, and also the bed, to ensure that the next person using the machine, or the next print, come out in good shape. It is suggested to use micro-fibers to clean the heads, and also a small amount of alcohol, to ensure that the resin does not stick to the machine parts.
Step 5: Cleaning Out the Parts
The layers of the prints for Vero Clear are usually coated with a heavy base of gelatin like material that surrounds the pieces. Therefore, to 'reveal' the pieces, one is usually required to use wax carving tools to take out all the resin based parts. However, before carving the pieces, I made sure to soak the pieces for around 5 to 10 minutes, since these pieces are simpler in geometry, I did not need to soak them too long. In the past, for larger pieces, I've soaked them overnight, in clean water. This would make removing the outer gelatin layers easier.
Step 6: Air-pressured Clean
After removing all the larger parts of the gelatin surrounding pieces off from Vero clear pieces, it would be suggested to use the air-pressured cleaning machine to give a final removal of the rest of the surrounding materials off the parts. If the parts are delicate, make sure that the pieces are contained; otherwise, the pieces may risk being throw everywhere and break.
Step 7: Final Pieces
After cleaning out the pieces, the final pieces could be dipped into resin to be kept a more sheen and glossy feel; however, as one could see, the interior "RMS" fonts are quite well revealed, once the cleaning process is finished, and looks pretty solid.
Then, you're good to go. Make a photoshoot within a well-lit room with a step-and-repeat (sunny/daylight is generally the best for the naturally lit photos).
Resilient Modular Systems is a Public Benefits Corp, and leader in innovative sustainable modular components for the building industry in emerging markets
More information - http://resilientmodularsystems.com
Facebook - https://www.facebook.com/ResilientModularSystems
Twitter - http://twitter.com/RModularSystems
Designed by -
Wendy W Fok | Founder
Resilient Modular Systems, PBC
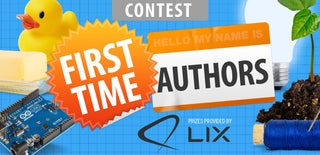
Participated in the
First Time Author Contest 2016
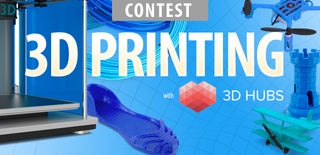
Participated in the
3D Printing Contest 2016