Introduction: Rainbow Glow in the Dark Longboard Made With Wood and Epoxy
I've been doing carpentry in school and teaching younger children carpentry basics for a long time. Most of my work involved only wood, and I've always wanted to experiment more with mixed media. I started coming across beautiful videos of people designing and building "River Tables" on YouTube a few years ago. These tables were made out of two slabs of wood separated in the center by a channel of solid transparent epoxy coursing its way from one end of the table to the other. Sometimes the epoxy was even mixed with pigments to make the table more colorful.
I've had some unopened epoxy pigments lying around and gathering dust for quite some time and when I saw the 'Rainbow Contest' on the Instructables page, I thought it would be a great opportunity to finally use them and fulfill my desire of working with wood and epoxy!
I've also always wanted to make myself a Longboard. This was the opportunity to use epoxy with pigments and build a longboard -- a cross between something to have fun with and something beautiful to enjoy.
I go out many times in the evening to cycle or roller-blade, and I thought it would be nice to make the deck glow-in-the-dark as well. The phenomenon know as 'Phosphorescence' is the property of a material/element to absorb radiation from a source (in our case mainly the sun) and slowly, over a long period of time, emit all the absorbed radiation in the form of light. If you're interested in the physics behind this, check out this site.
The difference between a Skateboard and a Longboard?
- Longboards are meant more for smoothly cruising at higher speeds for longer distances whereas skateboards are meant more for quick acceleration and performing stunts.
- Kicktails are bends at the extremities of skateboard decks, allowing the rider to perform such stunts and tricks. Most longboards on the other hand have simple flat decks.
This 44 inch longboard deck is made out of two long pieces of wood and epoxy. The epoxy pigments were used to color it the way I did. The coloring can be done in any way, even in your favorite color if you want so feel free to play around with the pigments. Making the deck glow in the dark is again up to you.
It was my first time working with this quantity of epoxy, and I was worried initially whether a combination of wood and epoxy would be enough to support a human weight. With trust in expert opinion, the end the results turned out to be great and the longboard has been carrying both me and my brother without any problem for the past 2 weeks. The epoxy even gives the deck the perfect amount of flex!
In this Instructable I hope to give you an idea of how to use epoxy and wood to make a sturdy colorful longboard that is both something visually distinctive and usable. If you don't think you'll ever go longboarding, you can use this concept and shape it instead into a counter-top, serving tray or anything you want or think you'll use! It turned out so well that I hope to make a few table coasters with this method soon!
This longboard turned out to be quite inexpensive as well. A regular commercial longboard could cost you anything from 100$ upwards. I ended up spending about 55$ for the entire project!
I suggest you watch the video above while going through the isntructable to give you a better visual understanding.
Please don't forget to drop a vote in the 'Rainbow Contest' if you liked this project. Feel free to leave any questions in the comment section below. Happy making! :)
Supplies
Materials to build a 44" long 8.5" wide longboard:
- Two strong pieces of wood around 44" long and 6/8" thick (preferably straight from a sawmill so that they have natural curves). The width of the wood can be flexible but it should be at least 2.5" wide.
- About 4.4 liters of epoxy
- Violet, Indigo, Blue, Green, Yellow, Orange, Red epoxy pigments. Buy colors according to your preference. I used all of them to make a Rainbow Longboard
- Epoxy glow in the dark pigments
- Longboard trucks and wheels
- Mold release wax or spray
- Caulk sealant for the mold
- A few long scraps of wood and plywood to make the mold
- A few disposable cups to mix the epoxy in
- A pair of gloves
- Finish: Natural oils or wax.
Some tools that might be useful (optional):
- Photoshop
- A jigsaw
- A drill
- An orbital sander
- A heat gun
- A buffing wheel/pad
And you're ready to go!
Step 1: Choosing and Printing Your Longboard Template
There are many many great longboard templates out on the internet. I chose to go with a 'pintail design' by Gorden & Smith from the Fiberflex series.
This step shows you how to make an outline of your template on Photoshop, to resize it and print it out.
If you like the template I used:
You can skip this step. I've attached the Photoshop file of the template below. Go ahead and print it in full size and keep it aside for later. If you like the template but want a different length or width, feel free to adjust the "image size" (refer to the next section on how to do this) in Photoshop of the attached file.
If you want to use a different template:
There are quite a few lovely longboard designs available online. I found mine by by simply searching for "Longboard templates" on google. Keep scrolling until you find something you like. Remember you need a picture of the longboard design from a top view. (Follow the following steps and refer to the pictures above)
- Import the image into Photoshop
- Use the "Quick Selection Tool" in the left panel to select the outline of your template. Do this by clicking all around the template, as close to the border as possible.
- Create a new layer
- Select the background layer and erase the image of your template using the "Eraser Tool" leaving only the selected outline.
- Go to Select > Modify > Border, and set the border to about 4 pixels. You can now press 'Ctrl + D' to deselect, and you should see a line around the border of your template.
- Next, go to Image > Image Size, and set the size to what you want. I set it to 43" long and 8.5" wide. If you don't know what size to set it to, here's a great size guide to help you out.
- Go ahead and print the template outline in full size.
Attachments
Step 2: Choosing and Sanding Your Wood
Choosing good, strong wood will determine the outcome of your project. Remember you'll be standing on your pieces! Some strong woods you could use are: Maple, oak, cherry, ebony etc.
I found a beautiful thick slab at a local sawmill. The sawmill owner had no idea what wood it was and I just couldn't identify it. I used a saw to cut a different slab of the same wood and it was incredibly hard. The slab I purchased was thick enough for me to cut in half, leaving me with two 6/8" thick slabs.
The wood you choose needs to be about the length of your longboard template and about 6/8" thick leaving you enough space to sand the pieces. There aren't any restrictions for the width of the piece because it depends on how much epoxy you're willing to pour in the center, but they should be at least about 2.5" wide.
Now you're going to need to sand your pieces. It would be useful to have a sanding machine, but if you don't have one, a lot of sandpapering would do the job. 120 grit followed by 220 grit on my Random Orbital sander worked perfectly. Make sure you do this until the wood is smooth, without any rough marks.
Step 3: Deciding the Placement of the Wood
Now that you have your template printed out, and your wood smoothly sanded, lay it out, and place your pieces of wood on it. I fiddled around with the positions until I liked the way it looked. How you place the wood is completely up to you, although there are some key factors you might want to keep in mind:
- Most of the wood should be placed inside the template so that when you cut out your shape, your final deck has as much wood as possible and is as strong and sturdy.
- At this stage, remember to remove any bark on the slabs of wood. Bark does not stick very well onto wood and this could leave you with weak areas that might break.
- Try and place the wood so that it fills both extremities of the longboard template. This is usually where the trucks and wheels are attached and it would be slightly stronger if they are placed close to the wood. But if your wood does not allow this, it's okay your longboard should still be strong enough.
- Since both of my slabs were initially from one piece, I inverted them so that the straight side was facing outwards. This was just because I felt it looked more aesthetically pleasing this way. But this depends on the shape of wood you have. Keep moving the wood around until you like the way it looks.
Keep the wood in this position and move on to the next step.
Step 4: Building a Mold
You now have to make a mold to cast the epoxy in between and onto the wood. For this, you need a rectangular sheet of plywood about 6" wider and 6" longer than the longboard template, as the base of the mold. (6" longer than the maximum length and 6" wider than the maximum width of the longboard). In my case, the dimensions of the plywood were about 48" x 14"
Once you have the ply wood sheet cut, use some mold release wax to cover the surface. This has to be done in order for the epoxy not to stick to the plywood base. Make sure you spread a generous wax coating about 5-6 times over.
You're also going to need 4 straight slabs of wood that will sit on the plywood, making a closed border around it. 2 of them should be the same length as the sheet of plywood, and the other 2 have to fit tightly in between the longer pieces. The height of the 4 slabs has to be at least 1/5" more than the height of the wood you're going to cast epoxy onto. Wax the 4 slabs just like you did for the plywood base.
First nail the 2 longer slabs of wood firmly parallel to the border of the plywood, and then fit the other 2 smaller slabs tightly in between the longer ones. Make sure that before you do this you've marked exactly where you the slabs have to be nailed and that they are at exact right angles with each other.
Once you've nailed them into place, use calk or any other sealant and spread it in between all the gaps that the straight slabs of wood make with the ply wood. I used an 'M-seal' sealant to do this, and then I went over it with a sealing putty. Caulk works in the same way. Don't forget to cover gaps on the top and areas where the nails create small holes with sealant. Let the sealant set and harden for some time, and then put one final layer of wax all around your mold.
Now, keeping the wood an your template beside the mold, carefully place the wood into the mold taking care not to disturb the positioning of the wood you decided in the previous step. Make sure you place the wood right in the center of the mold so that it isn't too close to any of the borders.
Place the mold with the wood inside on a stable table, and use a spirit level to correct any slants. Now fasten 4 clamps at each extremity of the wood in the mold to hold it down. I made a mistake of not doing this until I had poured a layer of epoxy, and the wood started to float upwards.
There are other ways to build a mold. I just chose this method because all the materials were close to home. Check out how this person builds molds. This is an alternative and more common method to build a mold for epoxy.
Leave the whole setup the way it is, and continue to the next step!
Step 5: Playing With Colors (optional)
It was my first time working with epoxy pigments, and I didn't feel very confident using the pigments directly on the piece on my first go. If you are confident with pigments and you know how you want the colors, go ahead to the next step. But if it's your first time and you're not very sure, I recommend that you do a small scale trial.
What you'll need:
- A small plastic box
- A pair of gloves
- Epoxy pigments
- Epoxy resin
- A few disposable cups
- A few sticks to mix the epoxy
- A heat gun/hairdryer
NOTE: I used a different type of epoxy just for this experiment because the main focus was on the way I wanted the pigments. You'll notice the epoxy is opaque and viscous. The epoxy used for the main piece is clear and more fluid.
Thoroughly mix a small quantity of the resin and the hardener in a disposable cup. Make sure you check the mixing ratios, they vary depending on your type of epoxy. Pour the epoxy into the small plastic box. Mix a pigment of your choice in a very small quantity of epoxy and pour it onto the epoxy in the box and mix it slowly. Keep playing around with the pigments until you're satisfied with the design! Lastly, use a heat gun or a hairdryer to remove bubbles that appear on the surface.
If you liked the way this turned out, you're ready to take on the real piece!
Step 6: Pouring the First Layer of Epoxy and Adding Pigments
My plan was to pour totally 3 layers of epoxy. The first one being a thin plain layer without any colors. The second layer of epoxy including all the pigments, and finally a third layer of clear epoxy to fill up the empty space on top and give the colors inside some depth.
Take out a few disposable cups and keep them aside for later. I ran out of disposable cups, so I simply cut a few plastic bottles on each side and used them as cups.
Get your epoxy out, and prepare a 1.5 liter batch (for the longboard size I made). Don't mix any pigments yet. Slowly pour the epoxy into the mold around the wood only. The first layer should be only one third of the height of the wood. As you can see in the picture, I forgot to clamp the wood down. Make sure your clamps are securely fastened to prevent your wood from floating up.
Next, mix a half liter epoxy batch. Divide the epoxy into as many parts as you have pigments. In my case, I divided the epoxy into 6 cups. Take out your pigments, and mix each one into a separate cup. NOTE: If you are using powder pigment, make sure the powder doesn't settle at the bottom. At this stage add glow in the dark pigment to any of the cups which have a matching daylight color (optional). For example, I mixed the blue glow powder with the normal blue pigment etc.
Take the pigment(s) and pour it slowly onto the first layer of epoxy. You can use any stick to mix it in gently. Be careful not to drop any pigment(s) on top of the wood!
TIP: There might be small leaks in the mold. So make sure you keep an eye on the project for a while. Simply seal off any holes if you see epoxy dripping out.
After you've added all your pigments, use a heat gun or a hairdryer to remove bubbles from the surface. You may have to do this multiple times for the first hour. Now take a break for 24 hours to let the epoxy set!
Step 7: Pouring the Last Layer of Epoxy
Once the epoxy has set, remove the clamps holding the wood down, and prepare a batch of epoxy (2.4 liters for my longboard's size). There should be enough epoxy to cover the wood by about 3 mm. Don't pour too much epoxy or it might flow over the the mold borders!
Again use the heat gun/hair dryer to remove bubbles from the surface.
Take one last 24 hour break, and let the last layer of epoxy cure.
Step 8: Removing the Mold and Cutting It Into Shape
Once your epoxy has cured well, get a screwdriver (or anything that can be used to pry open) and a mallet out. Push the screwdriver under the sides of the mold and slowly pry it apart slightly. Do this all around the mold until it's sufficiently lose. Be VERY careful at this stage. One extra push could crack your piece. Slowly and gently pry the whole mold apart.
Now find the template that you printed in Step 1, and place it on the board and stick it on either end with tape. Trace the outline of the template with a marker and take the template off.
Use a jigsaw or any cutting tool to cut along the line. I then used a grinding machine to smoothen off any jagged edges made by the jigsaw.
Step 9: Sanding and Finishing the Piece
For this step you're going to need a sander. If there's no way you can get your hands on one, you'll need a LOT of sandpaper.
I started off by using 80 grit paper to completely level the surface. Then moved on to 120, 180 and finally 300. This gave it a perfect smooth finish. Remember not to press too hard, or the surface might get scratched. After that I attached a buffing pad to my drill and buffed the entire piece thoroughly.
To finish the piece I used about 2 cups of Borma Wachs Terrace Oil (a mix of natural oils) mixed with half a cup of turpentine. I poured a little of the solution onto a piece of cloth and went over the surface multiple times until it had a glassy clear effect. You could use wax as an alternative as well.
At this point it looked so beautiful that everyone at home wanted it to be hung on the wall!
Step 10: Attaching the Trucks
No longboard is ever complete without trucks! Trucks are what hold the wheels to the deck and allow you to turn. The trucks I used were about 9.5" in length. You could use the link provided in the 'Supplies' section to purchase your trucks or follow this guide to choose the trucks that suit your preferences.
The distance between the trucks is called the 'wheelbase'. The larger the wheelbase, the longboard will have more stability, but less maneuverability, and vice versa. Here's a guide to help you decide your wheelbase according to your preferences. My wheelbase was about 32".
Once you've decided your wheelbase, mark a point at both the very top and very bottom of the deck and draw a light line demarcating the middle. Place the center of the truck along that line, stick a pen or pencil through the holes and mark where holes have to be drilled. Make sure that the base plate of the truck is at exact right angles to the line you drew. If the trucks are not aligned accurately, your longboard won't go in a straight line.
Step 11: Final Results
For my first project with epoxy and pigments, I'm delighted with the outcome. I've been riding the longboard for about two weeks now, and noticed that the epoxy gives the deck great flex as well. It's especially beautiful at night when all the colors light up.
I didn't want to put grip tape on top of the colors, and found that it wasn't necessary as the finish was smooth but not slippery.
I hope this will be the beginning of many more epoxy projects to come! If you liked this instructable and found it helpful, please drop a vote below in the "Rainbow Contest". Thank you! :)
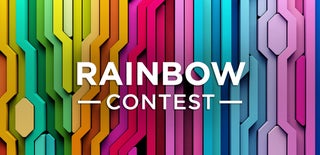
Grand Prize in the
Colors of the Rainbow Contest