Introduction: Wooden Ratchet and Clank Explosive Crate
This box was a solution to both my need for a large storage box, and a bedside table, and was the perfect excuse to replicate one of the most memorable static props from a video game! Given the success of this project, I'm considering making additional themed boxes to accompany it.
The tool list for this build was relatively short, although a circular saw with adjustable cutting angle was a necessity due to the need for the vertical panels to meet at a 45° angle. A drill, impact driver and jigsaw were pretty much the only other things I needed during the assembly process. As for consumables: Wood glue, 20-30mm screws, sandpaper and filler were just about all I needed to get it ready for painting, for which I used a durable oil based paint and spray on lacquer.
Step 1: References
These are some of the in-game screen captures I used to determine the best way of making the crate.
The explosive crate differs from the regular crates in the fact that the vertical faces are recessed slightly deeper, and part of the explosion emblems are actual 3D protrusions rather than just bitmaps. In the interests of retaining more of the box's internal space and avoiding the need for more types of wood, my take on the box has shallower recesses that are achieved solely by adding borders to the edges.
I did make some small alterations when designing the box, such as recessing the top and bottom faces in a similar fashion to the sides, making the entire logo 3D, and not correcting the screw placement on the vertical supports after securing the side panels to them.
Step 2: Parts List
The cube measures 45cm in height, width and depth, and is constructed from 26 separate pieces of wood.
12mm plywood was used for the 4 side panels, and thicker 15mm ply for the top, base, vertical corner strips and border strips. Depending on the precision of the cuts, there was some fine tuning required to allow the whole assembly to fit together correctly, most notably when aligning the 4 vertical panels with the vertical corner strips
2* Top / Base: 420mm x 420mm (Corners truncated at a 45° angle to produce a new side 70mm in length)
4* Vertical strips: 420mm x 70mm
4* Side panels: 390mm x 345mm (Vertical cuts at a 45° angle, 345mm is the width of the larger side)
8* Side panel border strips: 35mm x 345mm (Cut at a 45° angle toward the ends, 345mm for the larger side)
8* Top / Base border strips: 50mm x 410mm (Trimmed to size after positioning)
Step 3: The Initial Frame
The first step was to mount the 4 vertical corner pieces to the base plate. The 70mm diameter of the vertical "pillars" should correspond perfectly with the truncated corners. While it would be possible to secure them with a screw at the bottom of the pillars, I used 90° angle brackets to give more stability to the initial frame, until the side panels were in place. Contrary to the photos, the pillars sit outside the base, not on top of it. This is so that the 390mm high side panels combined with the 15mm of the top and base plate match the 420mm of the pillars.
Step 4: Side Panels + Borders
While I don't have any images of the box immediately after installing the side panels, it was a simple process of fitting them "inside" the 4 pillars from the previous step. The 45° cut should overlap the pillars on their interior face by a small amount, so wood glue will greatly add to the box's strength at this stage, although several pilot holes with 30mm screws won't hurt either. The side panels will sit flush with the bottom plate.
The lid was the key part of the build to align correctly: With the sides secured in place, the top lid had to go on and sit perfectly flush with the 4 corners. Some sanding was necessary to correct the minor differences. Next, the 4 horizontal strips that attach to the top of the size panels had to be adjusted to also sit flush with the top of the lid. Finally the 4 strips for the top panel had to be aligned with the outward facing sides of the last strips added to give the impression of being a single piece. Each strip had to have two 45° angles cut from each end (One to allow the other strips to meet up with it, the other to continue the vertical corner piece upwards as a single plane).
This last step involved the most trial and error, so it was inevitable some of the joins ended up marginally misaligned, although the filler fixed all the minor gaps.
Step 5: Side Emblems
To replicate these emblems, I scaled the image of the side of the box from the screen capture so that it was a 1:1 representation of the size of the box I had made (Roughly 33cm). I traced the whole logo onto paper from the screen, then cut them out to use as templates, however, the three "arc" shaped parts of the emblem should form a circle when their ends are matched to each other, so I placed them together, measured the internal and external radii and drew the circle and explosion symbol onto 3mm ply.
After cutting out 4 copies of each using the jigsaw, re-separating the circle into thirds and sanding down all the edges, I gave them all a coat of pale yellow acrylic paint before briefly test fitting them on the unpainted box.
Step 6: Painting
A very limited palette of just 4 colours was all that was required to paint the cube, and the use of separate pieces for the yellow emblems reduced the need for any masking tape.
After sanding down any rough edges and filling in any gaps that had not been properly aligned during assembly, the interior and exterior of the box both received 2-3 coats of a pure red oil based paint. The next stage was to create an upscaled version of the explosion emblem that was cropped to fit within the borders of the box, and apply a much lighter shade of red (I used a red / white acrylic mix). The acrylic was a little reluctant to dry without beading up on the oil based paint, as expected, so using a dry sponge to dab it on while applying gentle heat with an air gun was the most effective solution.
Step 7: Weathering
In order to accentuate the 3D features of the box, such as the emblem and borders, I airbrushed a dark brown across most of the box. This could theoretically be done with dry brushing, but an air brush will always produce much more evenly diffused patterns. The diluted paint would almost instantly bead up on the red paint, so even with multiple light coats, a heat gun was vital during this stage.
In the image you can see the difference between the non-weathered and the weathered side.
Step 8: Finished Product
Even after fully drying, some of the acrylic paints were slightly susceptible to smudging, although this was solved by applying a couple of coats of generic clear coat lacquer to the whole box.
This box now serves as a storage box and the perfect height bedside table to leave my phone on overnight!
Step 9: Bonus Step: ½ Scale Crate
I made a second box several months after the original and documented the earlier steps slightly better. Here is a compilation of photos and condensed instructions for the second crate!
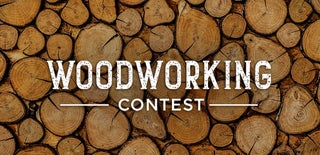
Participated in the
Woodworking Contest