Introduction: Rave Crystals
I call 'em my rave crystals just because that's the first thing that came to mind when I was making them, but while they certainly do make excellent party lights, they can just as easily become theatrical props, pretty mood lighting for your den, or a magical-looking nightlight for children. Plus being battery-powered means they're portable and can be plonked down just about anywhere.
Time: About twelve repeats of the Pacific Rim soundtrack (i.e. twelve hours). Less or more depending on overall size and number of crystals and LEDs.
Skill: Moderate. Requires minor clay-sculpting and the ability to wire up and solder simple LED circuits.
Caution: Don't be stupid with soldering irons or knives or ovens.
Step 1: Get the Party Started (AKA: Tools & Materials)
Required
- Aluminum foil
- Clay. Preferably polymer (Fimo, Cernit, Sculpey) because they provide a longer time to work them, and a shorter time waiting for them to harden.
- Quartz points, or other clear or highly translucent crystal. Even glass shards or bits of Plexiglas if you're desperate. I got my crystals at a local gem and mineral shop.
- RGB LEDs, the kind that change colour automatically. Can of course use solid-colour LEDs too, but it all looks so much cooler if the colours morph.
- Electrical wire
- Resistors
- On/Off switch
- Power source, e.g. 9V battery like I used here.
- Battery connector
- Soldering iron
- Electrical solder
- Heat-shrink tubing
- Drill bit the same diameter as the LEDs
- Pin vise (or a power drill if overkill is how you roll)
- Craft knife, e.g. X-Acto knife
- Felt-tip pens or markers
- Craft foam in roughly 2mm and 6mm thicknesses.
- Pale-coloured felt-tip or gel pen if your foam is a dark colour.
- Regular ol' dark-coloured felt-tip pen if your foam is a pale colour.
- Epoxy or other kind of durable adhesive that can glue craft foam together.
- Black and white paint for natural rock hues. Or go completely psychedelic; I won't judge.
- Old, beat-up paintbrushes that don't matter if they get trashed
- Matte varnish
Recommended
- Plastic sheet or mat to cover your workspace while you do the clay thing.
- Safety glasses
- Small heat gun or lighter
- Respirator and/or fume extractor and/or someone waving a big piece of cardboard toward an open window during soldering.
- Why am I even mentioning safety gear? It should be second nature for this kind of work. (Ask me how many times I've walked out of the workshop still wearing my safety glasses because I'm so used to them I forgot they were on my face.)
Optional
- Apoxie Sculpt or other air-dry clay-type stuff
- Rolling pin for use on clay (i.e., don't use the one in your kitchen).
- Old, already-dried clay scraps
- Slip-joint pliers or vise-grips or any other large chompy pliers
- Superglue
- Coarse files
- Clear plastic wrap
- Large pin or sewing needle
Step 2: All About That Base
Crumple bits of aluminum foil into something vaguely rock-shaped. Be messy about it. Size-wise, it needs to be large enough that a battery (9v here; size it to fit your power source) and a bunch of wire and LEDs could fit comfortably inside it were the foil ball hollow. Once the size and shape is to your liking, wrap one final smooth layer of foil around the whole thing. This is so it can be more easily removed later. Rave Crystals MKI was rough as all get out, and I had a time of it picking all the foil out of the clay later on.
Step 3: Layer Up
Grab your clay, soften it up and slap it over the top and sides of the foil "rock". The layer should be roughly as thick as your LEDs are tall. Mine here is about 4mm. I used a roller to flatten the clay out to a uniform thickness and a big enough sheet to cover the foil in one go, but mashing it flat by use of hands is just as acceptable, although it probably won't come out as even.
Once all that is done and the whole foil ball (except the underside, obviously) is completely covered, let the clay harden according to the manufacturer’s directions (bake it if it’s polymer clay, let it sit for however long if it’s air-dry clay, etc.).
I used white Fimo because I had a lot of it. Next time I may use something more rock-like in colour so I don’t have to paint it later on.
Step 4: Build Me Up, Buttercup
Time for more clay! Yes, more. This layer needs to be nice and thick, at least around 1cm, because it will hold the crystals. Unlike how I did it, throw neatness out the window. Mash irregular bits of clay all over it. Let it be messy and irregular and uneven, like a real rock.
Step 5: Crystal Clear
Time to get your rocks on.
Decide whereabouts you want the quartz points set up, and start pressing them into place. Depending on the shapes of the points and the thickness of the layer of clay that was added in the previous step, some more clay might need to be built up around the bases of the crystals to secure them in place. I removed and repositioned things several times before getting an arrangement that I liked.
Now is also the time to begin adding a bit of proper texturing to it to make the base look more rock-like. Poke and prod and generally scuff up the surface of the clay to give it a rocky texture. I had some big lumps of old air-dry clay that dried out before I used all of it that I crushed into smaller chunks with a set of slip-joint pliers. I then embedded the resulting slivers and chunks into the fresh clay to get some neat texture.
Remember that the on/off switch needs to go somewhere too, so leave a small space clear for that. A flatter area around the back side where it will not be as visible is best.
Once that is done, it is time to harden this second layer. The larger crystal points can be left in place during baking, but for any smaller, thinner ones it is a good idea to remove them -- carefully so their sockets in the clay are not deformed -- because wiggling them out of the clay after it has cured is inviting breakage (ask me how I know! :B). Certain types of rocks don't handle heat as well as others, so if you're using something other than quartz, maybe do a bit of research on how they cope with it before shoving them into an oven. And if you're using plastic, definitely remove all of it before baking.
But before you take them all out, get good, crisp reference photos of the placement, from multiple angles, especially if there are lots of smaller crystals that look kind of similar to each other. It will make putting everything back later much less aggravating.
Step 6: Light Up
While the base is baking/drying, it's time to wire up the LEDs. I'm not going to get into the intricacies of circuits and resistor calculations and all that jazz here, because that is a complete Instructable all to itself, and other people have already covered it far better than I ever could. This one is a good place for LED newbies to start. I've included the diagram of the six-LED circuit inside the Rave Crystals MKI prototype. The MKII shown in this Instructable has eighteen LEDs wired up in two parallel blocks of nine LEDs, which are in turn wired together, also in parallel.
The power switch does not need to be soldered on yet, and some of the future steps will be easier if it is not.
Guess who totally soldered the switch on already.
Step 7: Empty Spaces
Clay all properly set? Good. Remove the crystals if you did not do this already, and dig out the foil. Now we have a hollow clay dome that hopefully looks at least a bit like a rock on the outside.
Step 8: Hole in Your Soul
Or in a clay rock, anyway.
If you haven't removed all of the quartz points yet, do so now. Wiggling them gently but firmly will usually be enough to get them loose.
Get a drill bit the same diameter as the LEDs you used, and drill a hole at the bottom of each crystal socket. My LEDs are 3mm, so my drill bit is too, though I drilled some pilot holes with a 1.5mm bit first to reduce the chance of chipping during final drilling, then enlarged them to the final size. In this case the LEDs fit so well that they can simply be pressed in place and don’t require any gluing to stay put.
Step 9: Rock It
If the base is still not adequately rock-like for your... liking, now is the time to scuff it up some more. Coarse files can be used to chew up the surface, and crumbs of dry clay can be glued to the smooth spots to add more roughness. Watch out that nothing gets stuck in the socket holes, and remember to leave a clear area big enough for the power switch, which will be dealt with in the next step.
Step 10: On/Off
Time to cut out a hole for the switch. Hope you left some space for it! Also make sure it is not set too close to the edge; you want to be leaving at least 10-15mm (½") clearance for the base cover (getting to it in Steps 14 & 15), and also just for general structural stability.
Polymer clays like Fimo and Cernit can be carefully cut with a sharp craft knife, but something tougher, like Apoxie Sculpt, or less flexible and more brittle might need to be sawed through or drilled out and then filed/sanded to final size. Rotary tools like a Dremel will be useful for such a job.
Step 11: Paint It Black
If you used clay that was already a rock-like colour, this step might be unnecessary. If your base is a very not-rock colour, it is now time to slap some paint on that sucker. Black makes a good basecoat, but of course if you want to use white or brown or day-glow fuchsia, that's cool too.
Step 12: Turn to Stone
Basecoat done? Good. Now we're going to really make it look like a rock.
Step 13: And the Light
Once the base is painted and varnished and dry, it's time to place the LEDs. If you goofed like I did and made the base just barely big enough to hold everything, solder the switch to the wires before placing the LEDs into their respective holes so there is less risk of melting any of the plastic coating on the wires. If there is lots of space, then it might be possible to solder the switch after final placement of the LEDs, which allows for precise sizing of the wire lengths needed to go to and from the switch.
Step 14: Come Cover Me (Method 1)
Time to make the bottom plug/cover to hold all the electronic bits inside. The craft foam used in this step should be at least 5mm thick, but probably does not need to be more than 10mm unless your base is super huge.
This is one method of making the base cover. If you have an especially small, sturdy one, like my Rave Crystals MKI, sometimes it's enough to press it into the foam directly without the foil in the way, and simply cut around the imprint it leaves behind (trace it with a pen before starting to cut, as the foam will eventually pop back up and "erase" the lines, so if it takes a while to cut it out, the lines might vanish on you).
This step could also be done after final baking/curing/hardening (and reinforcing, if necessary or desired) of the base, back in Step 7. It'll fit in anywhere between Steps 7 and 13, really.
Step 15: Come Cover Me (Method 2)
And this is another way of doing it. I prefer the previous method because it's faster, but had to do it this way for the MKII version because I inadvertently messed up the base with the sloping bits. They made my outlines all mushy and difficult to follow, and I went through three attempts before giving up and modifying my approach to what you see here. This one may be a better option for especially large and/or oddly shaped bases, but can be a bit challenging to do without an extra set of hands to help you out.
Step 16: Stick Like Glue
Requires adhesive that can bond foam/plastic. I used Loctite's 5-minute power epoxy because I'm impatient about glue drying.
This to That is a good site for figuring out how best to glue a thing to another thing.
Step 17: Rockaria
At last it is time to put all the crystal points back in their sockets. Glue shouldn't be needed if everything was well built-up at the start (all of mine are simply friction-fit, and I can shake it upside down without anything falling out), but if yours turned out a bit too loose and/or you want to make everything doubly secure, put a tiny bit of clear glue or epoxy on the crystals before pressing them into place. Again: make sure it is glue that is, or will dry to be, clear.
Step 18: Let It Glow
Connect the battery, close it up, flip the switch and bask in the multicoloured glow.
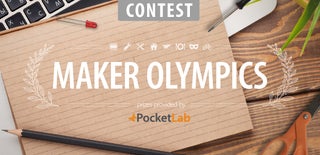
Participated in the
Maker Olympics Contest 2016
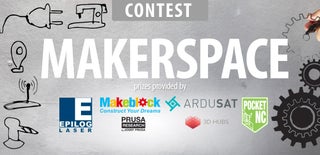
Participated in the
Makerspace Contest