Introduction: Realistic Sculptures From Foam With Glow-in-the-Dark Epoxy Base.
Hi everyone, thank you for checking out my instructables.
This is my instructables for the Faux-Real Contest. If its not too late...
As some of you know I love to make nautical things especially when it comes to anything nautical and fishing. I am a huge believer in conservation. I live by the code, "Once they're gone, they're gone". I believe in taking pictures of the trophies not mounting or eating them. Big one's make big baby's. Now, I do love eating fish, but I follow my state's guidelines when it comes to eating fish...But that is another story for another day. Anyway, to show my love for these awesome creatures by displaying a tail or a faux mount on the wall, it makes me happy that I didn't have to kill that line of fish and I didn't have to pay 100's of dollars to have a company duplicate it. I have made many projects just like this one, please check them out in the links below.
You know my obession, do you know yours?
Whatever it my be, I am sure you can make something to put on display in your home by using this process of foam, coating, detail, and paint.
Step 1: Materials and Tools
All materials, like almost all projects, could be substituted out for others. I will try to give you some alternatives materials that you can use and if I miss any or you know of one, please let me know in the comments below. I try to use what I have at the house before I go out of the way to get more items.
What I used for Core Material: Foam Insulation
In the past I have used craft foam and even spray foam. For this one I wanted to use foam insulation (green/blue sheets picked up from your local big box home improvement stores). I recently got a ton of small pieces of this stuff from my job (I am a teacher). My awesome drama teacher buys sheets of this stuff to paint and make into scenery for her plays. After repainting and re-purposing the sheets for multiple productions, she will break them up and put them in trash bags to be recycled later.
I grabbed two 55 gallon bags of these pieces and took them home. I cut off the rough pieces on the band saw and put them in the corner of my shop to be used for projects like this.
Alternative Core Materials: Craft foam, wire, crumpled paper, aluminum foil, oven-clay, EVA foam, even Packaging Styrofoam
Ooey-Gooey Stuff I used: Glue, Plaster of Paris, 2 Part All Purpose Putty, 2 Part Epoxy for Counter/table tops, Acrylic Paint, Window Cleaner with Ammonia, Clear Acrylic Spray, White Spray Paint, Pigment Powder
The Tools I used were: Silicon Basking Brush, Silicon Container, Razor blade/ knife, Foam Shaper Rasp, Sand Paper of variant grits, Belt Sander, Palm Sander, Rotary Hand Tool with flexible shaft, multiple carving bits, airbrush.
Step 2: Make the Initial Shape of the Piece
Gather Material and Glue:
I knew making the fish tails that the initial shape on the bottom is thicker, more cylinder shaped, but not as wide as the thin fin top. Knowing this, I stacked my pieces to narrow to wide. I glued them together using regular white glue. If you use this same glue (or even a wood glue will work) make sure you let the pieces dry, thoroughly. Use clamps and/or weights if you can. If you don't allow sufficient time to dry, the individual pieces will want to come apart when you start applying pressure from sanding and shaping. If they come apart, reapply some of the lost glue, reattach, and let dry.
Shaping:
When the pieces were dry, it was time to shape. The tools I used to cut the large portion of the unwanted foam from the piece was a combination of a band saw, razor knife, and foam hot wire. Pretty much if the piece didn't fit in my band saw, I used a razor knife or hot wire to cut the foam. If you don't have a band saw or hot wire, you can use a hand saw, rotary tool with cutting disc, grinder, or just use a razor knife the whole way through.
SAFETY: Wear a respirator or mask...Dust can get overwhelming
After getting the huge chunks off, it was time to work on some of the smaller shaping. I went for the combo of the foam shaper rasp, belt sander, and palm sander. With the foam rasp, I just scrapped the surface of my pieces till I got to my desired proportion. I then went to my belt sander and smoothed out as much as I couple possibly reach with that piece of machinery. Sanding drum on the drill or oscillating sander would probably be a better tool to use, but I don't have those in my shop, YET. After the belt sander, if I needed any more smoothing, I would use my palm sander. ***Be careful sanding this stuff; one thing, it sands very fast, second it creates a lot of dust, wear your safety equipment.
Next is Coating
Step 3: Coating & Sanding
The first coat I put on my tails is a mixture. And there is no wrong way of mixing it. A good rule of thumb is you want the mixture to be of the thickness of pancake batter. The base of MY mixture is Plaster of Paris (PoP) and water. You can stop there, and start coating your piece, but I understand that plain PoP will most likely crack when dried. To prevent this, I like to add white, or white paste to the mix. This substance does not crack and will give a hard, but forgiving/flexible coat. I also initial thought I would put some acrylic paint in the mixture to help with the base painting (that's why its more tan color than a grayish white).
Let the coat dry.
After dried, sand the the coat smooth. If you end up sanding into the foam core, it will be okay. We are going to end up putting another coat on. I actually put on 3-4 coats; one of PoP and the rest 2 part all purpose putty.
Step 4: 2 Part All Purpose Putty
There are multiple brands to choose from. I first used the Bondo brand (gray color) then into the Gator Brand (pink color). This stuff is amazing. You have the putty resin and then a small hardener cream. I mixed according to my directions. Wear gloves with this stuff, because once it cures, its done. For me, curing time was anywhere from 15-25 minutes depending on temperature. Once cured, you can start sanding. When sanding, do it in a well ventilated area, with a respirator, and full wrapped goggles. The putty produces A LOT of dust when sanded and carved, but it's worth it, because it works ( in my opinion) so much better than PoP. My problem when working with this stuff was I had no goggles, just safety glasses so I was covered. But nothing but a compressor and blower can't clean up.
****A bonus for starting with the tan color PoP, is that if you did go to low when sanding and carving, you will when to stop when you see that next layer before getting to the foam core.
Step 5: Carving
When I layed out my details on my tails like the scales or actual bones in the fin, I used a pencil and a permanent marker.
I cut my own stencils using clear plastic from grocery store deli container. The stencils are of individual scales to make it more manageable to transfer them to fish.
To carve the details into the tail, I used rotary tool with a flexible shaft attachment. I used a combination of different bits to carve and smooth out my pieces. I used a ball tip bit to carve the deeper grooves in to my tail for the scales. I also used rotary sanding discs and drums for the rotary tool to get to those weird angles that my palm sander and belt sander couldn't reach.
Make sure you double check your details before you start carving. It could save you time in the long run...
***Note: scales in these photos were put on backwards...
Step 6: Man, I Messed Up... Thank Goodness for My Momma!
So I pretty much did this project twice, but I took it as more of a positive than a negative. After I painted the tails, I sent some pictures to my mother. She said they are incredible, but there is something wrong with them. And then she helped me figure it out...
I CARVED THE SCALES IN THE WRONG DIRECTION!
Nice thing about this material is; if you mess up, you can go back and fix it at any time. So I sanded the paint and the clear coat off the tails, put a thin layer of putty on again. Marked my scales and other details. And carved them out again. I even cut the 2 bigger redfish tails to a smaller length that gave an appearance of a tailing fish.
In the end, I maybe could of gotten away with them in the wrong direction, but it would of ate me alive. So it took me an extra day, but the scales came out better than before.
***Mov. Files are quick videos of the first time I painted them, but the scales were in the wrong direction.
Step 7: Painting and Clear Coating
Handling
To make my tails easier to handle and touch/smudge proof. I hot glue the base to a square piece of cardboard. This made it easy to paint, because I would just grip and rotated the cardboard to paint my pieces.
Base Coat
I started the painting process by spray painting the tails in a flat white as a base coat.
Hand Painting
I thought I could paint these by hand...I was wrong...I am a horrible at hand painting with a brush. I might as well just finger painted them. If you are a better hand painter then go for it. I sanded down my speckled sea trout tail and repainted it using an airbrush.
Airbrush
What I did before I had an airbrushing...I can't remember and don't want to. I use a cheapo airbrush from Harbor Freight. I use regular acrylic paint, some are metallic, some are color changing. Pick the colors that you would like for your pieces. To prepare and thin the paints, I use blue glass cleaner with ammonia. I take a paper disposal cup, add my colors, mix with a wood tongue depressor. Once I have the color I want, I spray the glass cleaner into the cup and mix till I get a "milk" consistency. Start with your dark colors and work to your lighter ones. Practice makes perfect.
Clear Coating
Using an airbrush, lets the acrylic paint dry super fast. So by the time you clean up; you put away your paints and equipment, your piece will have more than enough time to dry. I used spray clear gloss acrylic spray. I followed the manufacturer's directions for applying multiple coats. I did 2 coats on each tail.
"All about that Base"
When the clear coat dried, I pulled the tails from their cardboard base and peeled away any hot glue residue. I then hand painted all the bases black, applied my custom rod building logo to the bottom with the date and my initials. After putting my mark on it, I then coated the bottom with one layer of the same acrylic spray from before.
From there you can be done. You put them on display, but I took it one step further. I wanted to make it faux water to go along with my tails.
Step 8: Drip, Drip, Drip...Faux Water From 2 Part Epoxy
Material:
I used plain-jane countertop/table top epoxy from my local big box home improvement store. In the past, I have used this stuff and for the most part its pretty clear with tiny little bit of yellowing, when casting with it. Yellowing for this didn't bother me, because I knew I was going to be using some blue and teal pigment dyes to color the epoxy to look more like water. I also added blue glow-in-the-dark pigment powder for an awesome effect.
Set Up:
For 2 of my fish I used a container the was some what flat/ thin that had a lid. I cut the edge of the lid off so that the top would fit inside the bottom of the container. I then cut the lid so that the tail would be coming up through the lid. To make the water ripple effect in the epoxy, I took my hot glue gun and ran lines on the bottom of the lid.
For the other 2 fish, Small redfish and speckled sea trout, I had to come up with a different, more radical display of the water, because of how I set them up. I was thinking of a splash effect. So I used a cup for the sea trout and a plastic bowls for the small redfish. The idea is that I could take hot glue and replicate the splash. Pour the epoxy in to the mold, where it would fill up around the hot glue.
Caution***: Test your hypothesis before flat out trying it on your pieces. Also COVER EVERYTHING THAT YOU DON'T WANT TO HAVE THE WATER (EPOXY) ON WITH SOME TYPE OF DEMOLDER. I used a combination of petroleum jelly and actually demolding spray to coat my pieces. Combination... Basically any flat surface like the bottom of the base of the container I would use the petroleum jelly. For all the nooks and crevices, like from the hot glue, I would spray with the demolding spray.
Get your pieces ready, mix your epoxy to what is recommended by the manufacturer, add your dye, and pour. I used old cardboard and pieces of old office chair mat to pour on to. So If it dripped or spilled, it would go on that before my carpet or rug.
Allow time for curing...
Step 9: Cleaning Up/Closure
After your piece has cured its time to release it from its mold. If you coated the right things with your demolder everything should come out easy. I like to take a razor blade and cut down the sharp edges of the epoxy. I will also take my rotary tool with a diamond cutting disc and cut any unwanted epoxy that hinder the look of water.
Lastly,
I made four fishtails. Can you make what you love with this technique, absolutely!
What ever you choose to make; make sure it's what you love...and you have the proper safety equipment
With mine, I will be keeping one and giving the other three away. This project was fun, but messy and so if you are okay with that than this technique is for you. I think I would of finished this project in a weekend if I only worked on one and if I had no set backs. But all in all I had fun.
I love the way they turned out. These are definitely not my last fish tails I will be doing. I am sure I will be doing more in the not-so-distant future.
Mov. File: Short video of the two bigger redfish tails.
Vote:
I worked very hard on these. Please do my a favor, if you like this, please vote for it in the faux-real contest.
Questions/Comments:
If you have any questions or comments about my process or my illiterate ways, please feel free to post. I will always get back to you.
Thank you!
Step 10: LET'S PLAY a GAME...
These are two collaboration of pictures of real and painted redfish and sea trout. Can you find the foam ones from this instructables?
Hint*** I used the same pictures from previous steps.
Thank you Again!
Please Vote!
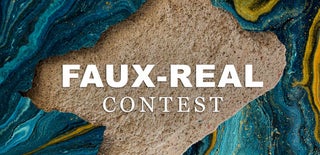
Participated in the
Faux-Real Contest