Introduction: Reclaimed Bowling Alley Desk
I don't typically work with reclaimed materials, but recently a client asked if I could make a modern style desk out of a chunk of bowling alley flooring he purchased on Craigslist. Much to my surprise, the bowling alley floor was basically a butcher block nailed together. It was definitely wouldn't work as a desk top without some work; it was pretty floppy, uneven, and had large gaps between boards. In order to keep it rigid, someone had installed a piece of angle iron that was pretty rusted. It was too short and too deep to work for the desired top dimensions (30" deep x 60" wide), had missing pieces and a bunch of holes drilled in it. Basically, it was in tough shape.
So I decided to rework it into a proper butcher block top, glued together with tight glue joints, a smooth top, and rigid across the width. Also, for the base frame, the client wanted it to be modern -- so we went with black iron pipe. It's not too expensive if you cut your own threads, and it can be very rigid.
Step 1: Break Down the Bowling Alley
First off I wrote a number and letter on each board to signify it's starting location in the floor. I had initially hoped to put it back identically, which later proved to be unfeasible and still get my final dimensions. It was however, helpful for replacing the bowling "tick" marks in the correct locations.
Then, I removed the angle iron. Most of the screws came out fine, but the person who installed it was nice enough to twist off a bunch of the heads. So I got out my vise grip and got the rest of the screws out. It's really key to remove all the metal parts from these if you hope to use a planner in the latter steps.
Next, you'll want to pull apart the boards. You can see from the pictures, they're solid maple, about 3" thick, with a profile cut into them to help align the parts. They were attached to each other with some pretty vintage construction adhesive, which was quite brittle and came apart fine, and some 3" twist nails. You might think a 3" nail shouldn't be hard to pull out, but I've only done that in pine, which is as soft as butter compared to this hard maple. I was amazed what it took to get these nails all pulled. I started with the little tools before breaking out my 4' wrecking bar. It was definitely needed. Make sure you're prying from the bottom, many of the pieces took some battle damage during this step, but it was always on the bottom, so no one would ever see it. Also, a bunch of pieces split during this process, don't get too hung up, you can repair them later.
It probably took a good 3 hours, but I eventually got all the boards free and the nails pulled.
Step 2: Cleaning and Organizing the Boards
Now it's time clean up all the boards. Best case scenario you only have to contend with the residual glue, but most likely you'll have yourself a nice layer of bowler sweat mixed with dust. I'm not exactly sure what it was I was removing, I tried not to think of it and all the sweat covered bowling balls had been rolled down. Find you happy place and remove everything that isn't maple.
Next I organized all the boards, and cut them up as needed to splice together a 30" x 60" surface. Make sure you don't have too many short pieces near the edges, it'll be a real pain later during the glue ups. Also, make sure you don't have any immediately adjacent joints between the end of boards and rows -- it'll weaken the whole setup. The only thing I had to pay attention to was the placement of the bowling arrows, making sure they had the same spacing and were symmetrically spaced. I generally put everything back where the numbers had it originally in the field, but then moved pieces around so I could get the final dimensions and meet the above rules.
At this point I also clamped everything up just to get a feel for what the final width would be. I planned to do it in two glue ups, running each through the planer to smooth it before doing the final joining. With the thickness of my boards, I would do 12 and 13 boards for my two respective glue ups.
Also, I used some good old wood glue to fix up a few of the boards that had split when I was removing the nails.
Step 3: Epoxy Everything Like Crazy, Then Clean It Up
I like to use epoxy for these big glue ups, I get a much longer working time before the glue sets up and epoxy does a nice job of adding strength in gaps as well as filling them nicely. If this isn't your first rodeo, you know to do a dry run before you mix up 10 oz of epoxy. Set all the pieces out, get some clamps setup and do a dry run. This will help decrease the panic later.
Now you and I both know you ignored that solid advice about a dry run and are plowing along blindly hoping for the best. I hope your dreams don't wash up on the shores of reality.
I used a bunch of epoxy, probably around 10 oz per glue up, mix it up at once, use a big disposable cup and a acid brush to mix and apply. I didn't take a lot of pictures during the glue up (something about the panic). I like west Systems epoxy, it's locally available in bulk for me. Don't get to showboating and use the fast hardener, make sure you're using a slow hardener.
Clamp it down good. This is the best shot you have of getting nice tight joints. You'll want to use clamps on both the top and bottom so you don't get un-even pressure and make a taco shape out of it.
Wait 24 hours for a good cure on the epoxy, then un-clamp it clean up all the epoxy drips that solidified on the bottom. I used a couple planes to clean it up. It doesn't have to be perfect, but you don't want it to be too rough or it won't feed into the planer well. I generally just made sure there were no big high spots on it.
Repeat for the other half.
Now, go get yourself a 15" helical head planer. If you don't have one, it's really going to suck to smooth this all out with a hand plane - it's doable, but expect many hours and a full body workout. I've done it before, but the 3 hp planer does all the same work with better results in about 5 minutes of planing. It's amazing. Send it through, alternating sides until both are the same thickness and smooth.
I had initially been worried that the bowling arrow marks on the floor would cause problems at this stage -- with all the grime on it, I couldn't tell if it was end grain, and there was always the worry that they wouldn't be that deep and I would remove them entirely with my planer. I lucked out big time, they were face grain walnut plugs, and they were at least as deep as the material I removed!
Step 4: Bring Em Together
Now, you've got two giant and heavy chucks of maple. In order to join them together, you need to get both sides of the joint exactly parallel and smooth. If you have a jointer, go for it, otherwise a #6/#7 plane will work great. I removed the raised portion on the edge in order to smooth it out. When I did the original glue up, the wood would flex enough to resolve some of these problems, but now that it's 14" wide, there's no flex, so you gotta get it perfect. I usually set them vertically to see how the glue joint looks, mark areas that need work, plane, and repeat.
Once you've got the glue joint tight, I added some dominos in order to get things aligned correctly. You could also use biscuits, but dominos are much more rigid and align in two dimensions instead of just vertical. The dominos really don't add much strength, it's going to be more than strong enough with all that glue surface.
Now glue it up, clamp away, but keep in mind nothing will be flexing, so you don't need quite as many clamps. I used epoxy again to help fill any gaps in the joint.
Step 5: Get the Edges Right
In order to give a nice smooth edge on the front and back of the slab, I didn't want to use any piece with a profile routed on it, so I got two new pieces of 5/4 maple, cut them to size and glued them on the slab. Here I just used yellow glue, and made sure they were just a little thicker than the overall slab (~2 7/8"). Once it dries trim it down to the right thickness for a nice smooth joint. I always start with a hand plane, then a card scraper, then 150 grit sandpaper.
Next, you'll need to true up the end grain on the slab. The boards will have slipped all over during glue up, so now's the time to fix it. I used a straight edge guide and a circular saw to cut as deep as I could, flipped it, lined it up again, lifted the saw to just barely cut through the remainder, and did the second cut. I got pretty close, < 1/16", but still it took some sanding to bring it true. I used 80 grit sandpaper on my oscillating sander to bring it down to smooth.
Then I added my usual finish, one coat General Finishes "Seal A Cell", and 4 General Finishes water based topcoat.
Step 6: Make the Pipe Base
In keeping with the modern look my client wanted, I decided to make a black iron pipe base. I decided to use 1 1/4" pipe, as a nice balance between rigidity and weight. I also decided to thread my own pipe so I could really fine tune the final height. You could however buy all precut/threaded pipes, keep in mind the cost will be much higher.
As far as the design, you could try to make this without any lower supports, but I hate desks and tables that wobble. The cross supports give it nice support to keep it from racking under load. Also I put the rear cross support at the level that the user can put their feet up while sitting. You could also certainly modify this into a standing desk (permanently) if you want with longer legs.
You'll need a couple of tools to make this base.
- Pipe threader ( I bought el cheapo from Northern tool that worked pretty decent for around $80, with six thread sizes)
- Pipe Cutter (you can get by with a angle grinder or chop saw if you love sparks)
- Thread cutting fluid
- Pipe vise (I tried to make due with a hole drilled through some wood and my wood vises, but this didn't have enough bite to keep it from spinning.
- Pipe Wrench (I tried to do without, but the final leveling would have been impossible without it).
You'll also need some pipe fittings
- 6 x T-fittings
- 4 x Floor flanges
- 4 x Pipe caps
- A bunch of pipe (I got it done with 2 x 10' lengths)
I started by cutting all my pipe to length, I wanted to make sure I had a 2" gap between the edge of the top and the edge of the floor flanges. So I set out all my floor flanges on the top in their desired positions, set the T-fittings on top, and measured the lengths of each pipe. Make sure to account for the amount of thread that will be left in the fittings. Take care to get the lengths equal for all the vertical pieces. I used a pipe cutter to cut them, since it was low noise/dust/spark and was pretty precise. Just get the tool set in the right place, tighten it down, and spin it around the pipe. Tighten it a quarter to a half turn each time you rotate it around the pipe. There's plenty of good youtube videos on this to help.
With the pipes cut, it's time to cut some threads. Doing this manually (no power threader) will take some time and some muscle. There's lots of good video's on how to cut threads as well, but my 3 tips would be, make sure you have a good way to clamp the pipe, use plenty of cutting fluid, and plan on it taking some time. At my best, I probably took about 5 minutes per thread if everything went well. I did buy two short lengths of pipe pre-threaded. They're the two 3" pieces of pipe to join the rear leg cross support T-fittings. It was short enough that I wasn't sure I would have enough room to clamp and thread well. Keep in mind, I paid about $5 each, and a whole 10' length is only $21. That's why I didn't do more of them.
Also, as I put things together, do it in such a way that you can use other pipes to tighten everything up as you go. One nice freebie is that you can adjust it a little bit at the end by really cranking down on some pipes to get everything to sit level.
Once I had all the pipes cut, threaded, and assembled, I put them on my assembly table and did a final leveling. Then I flipped over the top, marked the screw holes, pre-drilled, and assembled with #14 flat head screws.
I then sanded all the base down to get rid of any sharp metal from the pipe vise or pipe wrench. When I was happy with the entire base, I painted it all with flat black spray paint.
One final thing I noticed after the fact, by doing the legs the way I did, I could detach the top and rotate the outer legs in and make it a form of "flat pack" base. I usually don't ever make my furniture flat pack, because it almost always makes it weak and wobbly. This setup however kept it nice and rigid!
Thanks for looking.
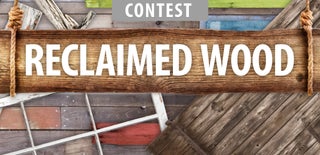
Second Prize in the
Reclaimed Wood Contest 2016