Introduction: Reclaimed Step Stools
These step stools I made awhile back out of a scrap pile I had left over from a shelving project. It was the same scrap pile that I made the End Grain Glasses Case out of and they feature the same shiplap boards in them.
This step stool isn't for everyone. They are heavy and heavy duty. They weigh approximately 36 lbs. Most people enjoy a light, easy to move step stool. I don't necessarily work out though, I feel like I'm active enough through my occupation. So just lifting this stool around is like a small workout every time you move it. All joking aside, I actually like how solid they are and how they don't move unless you move them. I use them for a lot of things in this respect. They can double as something to cut on, remove/drive nails on, portable mini workbench, etc. I've even screwed things, such as an air regulator, to them and trusted that they weren't going to tip over. I also made two so that two people can lift up/support longer items at the intervals and at the same height, respectively. I can even imagine securing a walkway (2x12) between them and using it as just that extra boost to paint something long/high or work on, etc.
I had no intentions of making an Instructable out of this project when I initially made them because I figured there were plenty of step stool projects already published and the world didn't need another design. After searching through many of the step stool projects on here though, I didn't see any that resembled what I made and so I decided to go ahead and publish it. I didn't take a whole lot of detailed, step by step pictures like I would normally if I thought the project would end up as an Instructable, but I think there are enough that most can follow along just fine.
Step 1: Cut the Frame
The frame is made up of short 2x6's and 2x4's. Collectively together, they would add up to be a sizable piece, but I had lots of short pieces to use up anyway so this worked out good. These pieces will determine the height of your stool and steps. I could see modifying this design to fit the need. I chose a final height of around 22" and a step height of 11". This was determined by measuring an existing stool I had (it was around 16" tall) and adding how much I wanted for that extra boost for high shelves.
Cut list for frame of my stool:
4-2x6@21"
2-2x6@10"
2-2x4@9.5"
2-2x4@14.25
Feel free to modify and remeasure your lumber to fit to your needs.
Once you have your pieces cut, you can lay them out like in the picture, pre-drill and screw the pieces together. I used 3" screws and about two per board in an alternating pattern to prevent splitting. Basically, I just aligned the 2x4 piece with the top edge of the side and the step at it's height; both pieces with the approximate distance away from the front and the back that was equal to the width of the board I was going to use to cover the whole thing (about 3/4"). One thing to note here is the picture is incorrect. In order to actually make a stool, you need to have the layout with the boards in a mirror image otherwise you're going to make two of the same side. Ask me how I know this.
Good news is, screws are easy to disassemble and reassemble.
Step 2: Cut the Steps
I had plenty of this 1X shiplap that was either, too short for my shelving project, or had big splits or broken edges. I figured out the width I wanted by placing my feet at a suitable sturdy stance that was reasonably step size and taking a measurement. My steps measure 18" wide.
After that, it was a matter of finding pieces of this shiplap that were long enough, ripping off the bad edge and then cross cutting to length. After I had a few of these pieces, I could figure out the best way to orientate the layout so that the width of the pieces filled the step areas and that I was taking advantage of the shiplap wherever possible. I usually had to custom rip a final piece for it to work out right.
So this project I made using mostly basic tools before I decided to invest in some better woodworking tools. I did all of the rip cuts with a circular saw. I may have crosscut the 2x6's and 2x4's on the miter saw because...why not? But I could see accomplishing the basic project with just a circular saw and a cordless drill.
When the steps were all cut, I just screwed them down with 1 5/8" screws in the end grain of the 2x6 sides, as well as the 2x4 supports. All of the screws used in this project were leftovers from another project.
Step 3: Fill in the Rest
This step probably wasn't necessary, but I thought it looked cool so I added a few strips to nail to vertically in between the 2x4 supports and filled in the front, back, and inner step area with more shiplap. You can see more of what I did to nail to in a later step on the bottom area when its upside down. I added another board in there to further tie the 2x6's together at the bottom. Between the top and step section though, I just ripped a 2x4 the right length in half and screwed it in vertically between the two 2x4 step supports as a nailer. Both of these solutions were way overkill but that's what I did.
These filler pieces end up being the same length (mine were approximately 14.5") so it is the same process as the steps. Rip off the bad edge if any, cross cut to length, and put into place utilizing the shiplap where ever possible. I picked up a cheap air nailer for the shelving project and I just put these pieces in using 1 1/4" 16 gauge brads. I questioned how good they were going to stay put seeing as this was to be moved around a lot but none of them have worked loose so far.
One thing to note, its helpful to install the inner step area before you enclose the front or back because otherwise it would be hard to get to with a cordless drill/air nailer. I think on the second stool, I did this before I even attached the top step.
Step 4: Make Two
Just like having two cordless drills, grinders, etc., its awesome when you have two stools that are exactly the same. You can have two in different areas, have two people elevated to the same height, etc. The possibilities are greatly expanded.
Repeat all the steps up until now to yield two step stools.
Step 5: Cut the "feet"
This is when I learned that most floor surfaces, however flat they appear, are all different and uneven. That being learned, the stools with the flat bottoms were a bit "rocky". I didn't feel like they were going to tip over or anything but it was just slightly unnerving so I decided to cut the middle section out leaving a smaller foot section that would contact the floor at more of a point and this helped greatly with the rocking problem.
For this, I employed a reciprocating saw because my jigsaw blade just wasn't going to make it through all of the thickness I ended up with. I marked the height and centering marks on the side and drew the radius using a section of an old unloading auger tube from a combine. After that was done on all four sides I just cut them out following the lines.
Step 6: Band the Crotch
I began calling this the crotch section because it was situated between two feet. Makes sense right?
The reason I used the unloading auger tube as the radius for the cut out is because I had planned on doing this step and rather than bending straight sheet metal in a radius, I thought it'd be easier to just cut them out.
To cut the bands, I just measured the width I need and marked them out on the tube. To get the length, I believe I just set it up there and marked it. Then I just used a cut off wheel on an angle grinder to get the rough pieces cut. I set them and place and trimmed here and there to get the corners and edges fitting good. Then I drilled way too many holes and countersunk them. I then transferred the holes onto the stool. Once those were marked I cleaned the bands up with a flapper wheel and painted them a red oxide primer. While the paint was drying I pre-drilled the holes for the screws and then once it was dry, I screwed them in using 1 1/4" screws.
I thought that this would be a detail that made it more early 1900's ish/heavy duty looking being that they crossed the line into way overkill anyway. Plus, the cuts didn't come out very straight or smooth using the reciprocating saw and I wanted this area to be smooth and splinter free. This was a good solution because it became a good spot to grab these things to move them. The bands actually do tie the pieces in together tightly but I doubt on whether or not they are even necessary.
Step 7: Add Handles/make a Jig First
After using these stools for a number of projects since their creation, I got tired of having to bend all the way down to the floor to grab the cut out area to move them around. A stool this heavy needs handles. I decided the best way to do this repeatedly was to make a jig. I anticipated using this jig for other projects in the future so it was really a no-brainer to spend the extra time to make a jig.
I based the size of the handle holes off of an existing stool. Those handles were too small for my liking because, sometimes I wear gloves and its difficult to get your hand out without the glove getting pulled off. So I made a drawing of the existing hole and then added the amount I wanted to enlarge it in either dimension. Once I had that figure, I could add in the amount needed for the size of collar I planned to use. For my handles, it went something like this:
I wanted the total height of the handle to be 1.5" and the total width to be 4.5"
I wanted to use a 1/2" collar on my router with a 1/4" straight bit
The jig therefore needed to be 1.75" in height and 4.75" for the outside of the bit to cut a 1.5" X 4.5" hole with the right radius on either end.
I had a fairy thin board from some other project so I made a pass over the jointer on one face and one edge. Then took it to the table saw and squared up the rest of the board. Once squared up, I could layout the hole. I used an 1.75" forstener bit to drill holes on either end with the drill press to form the radii. Then I used my router with a 1/4" straight bit to connect the holes. This was done freehand. I suppose you could use a jig saw, but I can run a straighter line with a router. After I had the hole, I used a file and some sandpaper to clean up any imperfections.
Step 8: Use the Jig and Make Some Handles
Once the jig is made, the process is fairly simple. Line up the jig where you want the handle to be, square it up, secure it, and run around the edge against the collar in increasingly deeper increments. I used tape to secure it. If I was thinking more, I would've chosen a longer piece for the jig so that I could clamp it away from the routing area but, such is life. The tape method worked well but I made sure I made light passes and didn't have to push hard on it.
Reaching the maximum depth setting on my router, I then used the same bit to run a couple passes across the middle section. This allowed me to remove the jig and chisel out the waste to that level with a chisel and a hammer. I moved on to a drill with a 1.5" forstener bit installed in a hand drill. This was perfect because the hole I had opened up was exactly 1.5" so the bit had a guide to start. Having two holes clean through the 2x6s, I used a hand saw cutting between the holes, much like making the template.
It may be important to mention that there are many ways to make handle holes and I don't think any which one is better or best. I chose to go about this process this way because it was easily repeatable, especially on uneven surfaces like I had, because the template provides a flat surface to ride on. Lining up the template is a breeze because of all its square edges. Then once the hole is routed and chiseled out, lining up the drill bit for two holes per handle is a breeze because the radius is already started, all you have to do is follow it through. After the holes are drilled, you can remove the rest with a saw using the edges as a guide, leaving only a bit of material left to clean up. Its kind of one of those a lot of easy work versus a few hard work situations.
The other reason I went about making the handles this way was because I only have a fairly short 1/4" straight bit and there was no way it was making it through the approximate 1.75" of the 2X6.
Step 9: Flush Cut and Round Over
I got as far as the last step and pondered for a while on how I was to clean the rest of the handle out nice and smooth. I didn't own any longer router bits or there wasn't enough travel in my plunge base to clean the rest of the rough out of there so, rather than use a file or drum sander, I did what any self respecting person would do. I splurged and bought another bit that was going to work perfect for this problem. It happens to be a 3/4" diameter flush cut bit that is 1 3/4" long with a top guide bearing. The top bearing is what makes this bit interesting because when I first used the template & collar method, effectively the template was transferred to the stool at the right size about 1/2" deep. Now all that needed to happen was for the rest of the rough to be taken out of there and that 1/2" deep template outline was going to be the perfect guide for the bearing. It was as simple as installing the bit, setting the depth so that the bearing was riding on that 1/2" section and run each handle hole.
After that process was done, I could now use a 1/4" round over bit to ease the sharp edges around the handles. This is of course for comfort. This was another case of installing the bit and running the handles. Those guide bearings are pretty cool.
One challenge I came across was that one of the stools had about a 1/8" difference in the thickness of the 2X6's I used for the construction of the sides. This made it difficult for the router to do it's job with either the flush cut bit or the round over bit. Both of these work better with flat level surfaces. So I took a straight bit and carved a section in the thicker board so that it was now at the same level as the other board. I then placed and taped down some 1/8" spacers to the thinner of the two boards to create a level surface for the base of the router to ride. This made the round over all at the same level.
Step 10: Handle Borders
I decided to roll with the sheet metal theme and cut out some pieces that would border the handles to give some accent and reinforcement.
Starting with more combine sheet metal, I was able to get one handle border out of each piece. This process included the layout of one piece carefully. I could then use that piece as a template for the remaining three.
The initial layout was based off of that section I cleared out to make the even round over on the one stool side. I figured out that I could aim for about a 3/4" larger piece all around the border of the handle hole and it would look pretty cool.
So to lay this out was a bit tricky but I may be able to save you some time if you ever attempt something like this. Start with good center lines and work from those. Once you have good center lines, you can trace the inner hole by making two straight lines parallel to each other at the desired distance apart. That desired distance can be used to figure out the radius at the ends. Just divide by 2. So for instance, my inner hole I made at 2 1/4" wide to give a good clearance to my round over edge for transition. The radius for these ends is therefore set at 1 1/8". This measurement is also important to note because this will also help locate the center point for these said radii on either end. If you know your desired total length (in my case 5 1/4") then you can divide it by 2 as well and take that quotient (2 5/8") and subtract your radius (1 1/8") to get the amount needed to measure from absolute center to find each end radius center point(in my case 1 1/2"). This is where it helps to have a divider or compass. You can set the radius on either tool and just trace the radius off of the center point on each end. But you could also find something round with the right 2 1/4" diameter (holesaw, etc) and center that to draw around. I didn't have a 2 1/4" object so I used the divider.
Moving on to the outer ring, just measure from the straight lines of the inner hole outward the desired thickness of the band on either side and make two more parallel lines. Basically, now you can repeat the same process. In my case the outer ring was 3 3/4" wide and therefore my radius increased by 3/4". So in my case I set the divider at 1 7/8", drew the radii off of the same end center points. If any of this is super confusing, refer to picture 3 in this step and it should make more sense. I screwed up the first layout and ruined a piece because I didn't notice the mistake until I cut it out. Then I came up with this layout method which worked way better.
After everything is laid out, then its basically a matter of going after it with whatever cutting tools are available. I used a cut off wheel on an angle grinder, a smaller air powered cut off wheel, a small 1/4" die grinder, a bench grinder and a 60 grit flap wheel to get to the final picture in this step.
Step 11: Mark, Drill, and Countersink
Once you have an adequately cut and smooth piece that looks like its going to work, its time to make some holes to attach it.
I initially planned for 4, but then decided it looked better with 6. The process is all the same though. The layout is one I just picked out that looked good and was on an even measurement to make it easy. I've been into red sharpies lately.
I had a step bit installed in my drill press already and so I decided to use it. All holes were drilled to fit my screws. In my case that was 3/16" and then they all got countersunk with a countersink bit.
Now that I had a good template I could just repeat the entire process 3 more times.
Step 12: Paint and Install
I painted all the handle borders with a red oxide primer, just like the crotch bands. After they were dry I could line them up on the stool and mark all the holes. Then its just a matter of pre-drilling for the screws and screwing the pieces down.
Step 13: Final Product
Here is a couple pictures of the final stools. I think they have a certain character about them. I definitely enjoy the extra height boost they provide on a consistently needed basis in the shop with high shelves. This ended up being a good beginner wood work project for me and later on an excuse to use my router and buy more cool bits.
All in all, they work well for me and what I use them for and I'm pretty happy with the way they turned out and the materials used to make them.
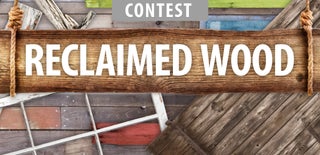
Participated in the
Reclaimed Wood Contest 2016