Introduction: Recliner-Bunk for Camper
My dream was to buy an old bus and make it into a home, but for various reasons that didn’t work out. Then I decided I would build a teardrop trailer, but I had to shelve that idea, too. I scaled back my ambitions, and decided to put a camper shell on my pickup instead. Even though I had to scale back my plans, I had a lot of ideas that I was able to incorporate into this project.
My main objective is comfort. I needed to have a comfortable place to sleep, but I also wanted a comfortable place where I could sit and read, or watch a DVD. I needed storage under the bunk and room for all my other gear, but I also needed the setup to be easy to store when not in use. I came up with a bunk that converts to a recliner. The basic concept seemed simple enough, but it took quite a bit of fiddling to get it to work. If I did this project again I would probably do some things differently, but the recliner-bunk provides the comfort I was looking for, and it changes from recliner to bunk with just a flip of two levers.
I made a few other furnishings to round out this project: an entertainment center, and side tables.
Tools:
Circular Saw
Jigsaw (Wood and Metal blades)
Belt Sander
Orbital Sander
Files (half-round, and full round, for fitting parts together
Power Drill and bits (including 1 1/2-inch hole saw)
Pocket Hole Jig. Router (optional for rounding edges).
Soldering Iron (optional for cutting Nylon webbing).
Materials:
One sheet of Baltic Birch plywood, 1/2-inch thick.
About a quarter of a sheet of 3/4-inch plywood.
Four, eight-foot long Douglas Fir one-by-fours
One eight-foot long Douglas Fir one-by-six
One eight-foot long Douglas Fir two-by-two
Several large and small size paint stirring sticks
Three sets of 2 1/2-inch hinges
Three sets of 1 1/2-inch hinges Four "hairpins" sized to replace the small hinge pins
Sand Paper Urethane sealer and brushes
200 Screws, Number 10, flat head, half-inch long (I used sheet metal screws because they have more threads)
180 Finishing Washers, Number 10
Pocket Hole Screws 1 1/4-inch (coarse thread for Douglas Fir, fine thread for the Baltic Birch, about 50 of each).
Nylon webbing, one-inch wide, about 17-feet, cut into 30 seven-inch long pieces (probably way more than needed).
Four 1/4-inch Lag Screws, 2 inches long, washers
Thick plastic pieces approximately 2 1/2- by 3 1/2-inches (to fold in half for rope guide)
About twenty feet of 1/4-inch rope
Zip Ties (200 pound capacity) about about 20
For the Entertainment Center:
1/4-inch Baltic Birch Plywood (about 32- by 24-inches)
Four lengths of aluminum tubing 3/4-inch diameter, 63-inches long (shorter would have been okay.)
One-by-four Douglas Fir trim (about two-feet)
One-by-two Douglas Fir trim (about 8-feet)
2 pieces 1/2- by 1 1/2-inch planed poplar trim molding.
Hidden cabinet hinges (Note: these are designed for 3/4-inch material. If you add the thickness of the plywood, you need to recess the hinges).
Multi-tool with thin wood cutting blade (for cutting out the door).
Step 1: Design
After a lot of head scratching, I came up with a bunk-board that is divided into three sections. Two pieces of half-inch plywood placed on edge support the bunk boards. The bunk support pieces are attached by hinges to a frame that lies flat on the bed of the pickup. A second set of "notched" supports is attached to the bunk support pieces, at right angles, so that when the bunk supports are folded down, the recliner supports swing into position. The notched support pieces allow the bunk board to form something resembling a reclining seat.
The basic concept seemed valid, but I wasn't sure if it would all fit together in the back of the pickup. I ended up making a model out of scraps of “foam-core” material to test various configurations. Scale models are a maker’s best friend because they let you to see exactly how moving parts work together. They are also a no-cost way to try different layouts to see what works.
Even with the model, I had to noodle on the layout for quite a while before I could decide on the final dimensions. One of the downsides of the “convertible” bunk is that to change the configuration you have to unload everything stored under the bunk. I wanted the space between the bed supports to be wide enough so I could use cheap plastic storage bins that I could slide out and shove under the pickup. I decided that I needed about a 16-inch wide space for these bins. Simple enough, but I also felt it was important for the vertical bunk supports to rest securely in the grooves of the pickup bed. Unfortunately, these two criteria left me with a bare 36-inches between the inside edge of the pickup bed and the outside edge of the left-most, bunk support. Since I'm using half-inch thick plywood for both the bunk and the vertical supports, this left a very thin edge for the bunk to rest on. I could have just made the bunk an inch wider, but I had already made the decision that I needed fifteen-inches between the edge of the bunk and the wheel well to fit an ice chest and cook box.
I solved this problem by attaching a two-by-two “rail” along the inside edge of the vertical bunk support. And I extend this two-by-two piece to meet the head frame so the bunk board wouldn't slip down into the gap when changing positions. .
The final design is pretty simple. There are three basic components to the recliner-bunk: the bunk board (in three sections), an undercarriage that consists of a flat frame with two sets of rotating supports attached to the frame with hinges; and a head frame that sits against the front of the pickup bed, and includes “stops” to set the back of the recliner in various positions. I am currently using an off-the-shelf foam pad that folds into three 24 by 36-inch sections. This works, but eventually I plan to make three separate cushions so that two can be used for the back and seat of the recliner. The handles at the end of the bunk supports will hold the three cushions in place in the bunk configuration. I’m including some bonus steps for other furnishings to make the camper more comfortable.
Step 2: Cutting Out the Parts:
My plan to use a single sheet of plywood for the main bunk components meant that I had to make some compromises. In addition to the bunk-boards, I needed two pieces of plywood 9 ½-inches wide for the bunk supports (the wheel wells are nine and a half-inches high), and these support pieces needed to be five feet long to provide enough support for the three-piece bunk. This meant that I couldn’t just cut the three-foot wide bunk by ripping a one-foot wide strip off my sheet of half-inch plywood. Instead, I cut a three-foot wide section from one end of the plywood, and used that piece to make the head and foot parts of the bunk. The two five-foot long by nine ½-inch wide bunk supports are cut out of the remaining five-foot long piece of plywood. But this left me with a piece for the back rest section of the recliner that was only 29 inches long (less saw kerfs), which was three inches shorter than I figured I needed. But it seemed like a reasonable compromise. This left me with a couple of scraps from my sheet of 1/2-inch plywood, and I used those scraps to make two arm rests and a couple of side tables (see steps X and Y).
Even with my best-use of the sheet of half-inch plywood, I still needed more plywood to make the notched supports for the recliner. I had a four-foot by 15-inch wide piece of ¾-inch plywood left over from another project, and I ripped this in half to make two pieces seven 3/8-inch tall for the notched-recliner support pieces. I used parts of these, and some other scraps, to make additional support pieces for the undercarriage.
In the bunk configuration, the bunk is moved over to the passenger side of the pickup bed, allowing room to store an ice chest, cook box and other gear beside the bunk. Because the bunk needs to slide back and forth to change configurations, I decided to attach ropes at the front corners of the bunk, and run ropes through pullies mounted on the outer edges of the head frame. The ropes make it easier to slide the bunk back and forth. when changing configurations, but I don't think they are really necessary.
I used a 1 ½-inch hole saw to make handles for moving the bunk around and for pulling up on the back support piece to change recliner positions. Several of the round cut-outs were saved for making "rollers" to assist with raising the bunk into the recliner position, and more were used to make pulleys to move the bunk back and forth.
Step 3: Making the Bunk
As discussed previously, the bunk is in three sections. I decided to use strips of one-inch wide Nylon webbing for the hinges joining the bunk parts together. Initially, I'd planned to use epoxy to attach the webbing strips to the bunk parts, but I wasn’t confident that I could get the measurements right the first time. Once again, my choice of plywood and my general stubbornness made it hard to find screws to attach the webbing strips to the half-inch plywood. I really wanted to use Number-10 screws and finishing washers (see photo for comparison of Number-8 and Number-10 screws), but I couldn’t find a hardware store that carried Number-10 screws, in the half-inch length. I ended up ordering the screws and finish washers on line. I was planning to use two screws for each end of the straps, but since I had to buy in quantities of 100, I decided to put three screws in each end. Both the number of screws and number of straps for the hinges is overkill, but as I was building the bunk I got to thinking it would probably be stout enough to drive on, in an emergency (say to get out of sand or mud), so I went ahead and used an excess of screws, just in case.
In the recliner position, The foot of the bed becomes the seat; the middle of the bunk becomes the back-rest; and the head-board hinges down to rest on one of the four cross members in the head frame. The seat-back drops down into one of two notches in the recliner-support boards. With four back-rest positions and two seat positions there are many options for achieving the desired level of comfort. For the back-rest to slide down into the locking notches, there needs to be slack in the straps forming the hinge between the back-rest and the seat. To make te necessary slack, I clamped scraps of 3/4-inch plywood between the bunk parts before screwing the straps in place. It took me a couple of tries to get the strap arrangement right, it's easy to get confused about which side of the bunk-boards to attach which end of the strap to. Look at the picture to see how the straps go from the top of one board to the bottom of the next board.
I didn't account for the thickness of the straps when I was measuring the bunk board. This made the bunk a little tight, but it does stay put.
Step 4: Making the Undercarriage
The key to the convertible recliner-bunk setup is the movable undercarriage. The undercarriage is basically a flat frame made of Douglas Fir one-by-fours with one-by six cross members. Two sets of support pieces are attached at right angles, and the paired supports are attached to the frame with three hinges per support pair. The first set of support pieces (bunk supports) are half-inch plywood rectangles that extend from the tailgate to within a foot or so of the front of the pickup bed. These vertical bunk supports are attached to the frame with hinges, and the second set of support pieces (made of 3/4-inch plywood) has notches cut at the appropriate reclining angles. I tacked the two pairs of support pieces together and used clamps to test out various positions. I had previously tried several positions by propping up pieces of plywood scrap and tracing the angles. I used these angles to check for comfort with the bunk boards. I simplified things by selecting just two angles for the recliner supports. The trick to making the recliner positions work is to make sure the front of the seat has enough support that it won't lever the back-rest out of its locking notches. I made the second seat position so that the front end of notch matches the angle for front point of the first seat position. The first seat notch only supports a few inches of the rear of the seat, but the in that position, the front edge of the seat rests on the end of the second notch. Refer to the pictures for a better understanding of the relationship.
After testing, I decided to angle the back part of the first notch so the recliner could be tilted back further. With the two main notches, and three back support positions, the recliner can be set at several different positions.
The two notched recliner supports are attached to the half-inch bunk supports with pocket screws. These make a strong joint, but there will be a lot of lateral pressure on this joint when changing positions. To add support, I cut a couple of quarter-round pieces of ¾-inch plywood to hold the pieces at right angles. For additional support, I used an old boat-builder's tip and made 'knees' by cutting plywood rectangles into boomerang shapes. This provides good support, but also allows storage bins to be slid under the bunk.
Step 5: Making the Head Frame
The head frame is built against the front of the pickup bed and supports both the head of the bunk, and the seat back recliner positions. This frame just fits behind the tie-downs at the front of the pickup bed. There are two main cross members, and additional "stops" made from plywood scrap are fitted between the head frame cross members. I added some one-by-six support blocks between the cross members, and the cross member at the bottom of the head frame is drilled to fit bolts at the ends of the base frame, so the two frames can be attached with wing nuts.
After the first test, I realized that the head section of the bunk needed to be lifted up during the switch, to allow the bunk to be placed in the recliner position. I had some long (14-inch) narrow scraps of 3/4-inch plywood and I attached "rollers" made from the hole cutouts to make these. The rollers are attached to the ends of these pieces with quarter-inch lag bolts and washers. The roller assembly is attached to the quarter-round support sections at the front of the undercarriage. I experimented a bit to find the best position for the roller assemblies. the rollers lift the head section of the bunk board, but this board needs to be held down at the front, to make the rollers lift the back-rest into position. To make better use of the bunk, I used the jigsaw to cut a section about an inch-and-a half wide out of the top board of the head frame. This narrow piece of scrap is attached to the head frame uprights to hold down on the head board from lifting, while the bunk board is being raised into the recliner position.
I drilled 1 1/2-inch holes in the sides of the head frame, just above the bunk support cross member. Blocks are attached above these holes, on the outside of the head frame, and pulleys are attached to the bottoms of these blocks. A "shroud" formed from scraps of plastic keeps the ropes from falling off the pulleys.
Step 6: Arm Rests (Optional)
One of the pieces of scrap from my piece of half-inch plywood was four-inches wide and three-feet long. I cut that in half and drew an arm-rest shape, making the cut-away piece the same width as the back of the arm rest. The narrow cutoff piece was long enough (eight-inches) to use for the front arm rest support piece. This support piece is attached (unattractively) to the arm rest with a hinge on the underside. I knocked the pins out of two more hinges and found “hairpins” at the hardware store to substitute for the hinge pins. This makes it so the arm rests can be removed for folding, or if they turn out not to be comfortable
I cut out the pieces to make the arm rests, but they seemed like they would just get in the way, and I didn't really like the idea of having more pinchy places on the bunk than I have already. I may make some foam arm rests when I make the cushions that I'm planning for the couch and mattress.
Step 7: Entertainment Center
[It took me a while, but I realized that I'd be better off just mounting the DVD player on an arm that attaches to the side rail of the camper. It's less trouble and works better. I took out all that overhead sliding shelf thing and now have more space.]
It's nice to relax around a camp fire, but sometimes I'd rather just lean back in a recliner and watch a movie. I bought a relatively inexpensive portable DVD player, but I needed a shelf to put it on. Things are pretty cramped in the camper, so I wanted to attach the DVD shelf to the ceiling. The camper came with two rows of hooks in the ceiling, but I was worried that if I attached the shelf to the hooks at the back, it would be in the way when I was getting in and out of the camper. But the shelf needs to be near the back of the camper to watch a movie while sitting in the recliner. The solution was to mount a double-set of rails along the side of each row of hooks; and have the shelf slide forward and backward on the lower set of rails.
I found these inexpensive ($4 each) 3/4-inch diameter aluminum tubes at an industrial supply store, and used zip-ties to attach one set of these "rails" to the outside edge of each row of hooks. A second set of rails is attached to the first set, with blocks that have holes drilled through them. The wooden blocks keep the rails at the right spacing, and allow the DVD shelf to slide forward and back on loosely mounted zip-ties. Because the rails are only attached at the ends, the shelf can slide nearly the full length of the camper shell.
The shelf is made from 1/4-inch Baltic Birch plywood, and reinforced with pieces of one-by-two trim. I left about an inch of plywood extending beyond the frame at the front and back edges to provide a place to clamp things (lights, fans, etc). I cut a rectangular "door" in this shelf, sized to fit the DVD player, and the player is attached to this door, so that when the door is opened downward, the DVD player (with the screen flipped around) faces toward the front of the pickup.
The drop-down door, and the edges of the opening are framed with one-by-two trim, which provide good mounting points for the hidden hinges. A piece of one-by-four trim is attached to the back side to make it easier to mount the hinges.
I've used these hinges before, but I had forgotten that they only work for 3/4-inch trim. Because I used quarter-inch plywood, in addition to the 3/4-inch trim, the hinges didn't fit right. If I had it to do over again, I would have chiseled out places for the hinges, but instead I just sanded part of the plywood piece to make room for the door to open to 90-degrees. The hidden hinges won't hold the door closed by themselves, at least not on bouncy roads, so I added a simple bolt that just slides through a hole in the frame, and into another hole in the DVD door. This is kept in place with a springy piece of old rake tine. I don't care much for this arrangement, and I intend to find something that looks better, but it works for now. I may put some padding under the DVD player in the future, but it seems to work okay.
I added a small boxed-in area at the front edge of the shelf (about six-inches wide). This extra shelf space provides a place for a Bluetooth speaker, DVDs, and other odds and ends. I store a number of devices and things that need power on this shelf, so I picked up a 12-Volt extension cord and an outlet multiplier that I mounted on the shelf. In addition to playing DVDs, this particular DVD player will, supposedly, pick up local broadcast TV stations. I’m optimistic, but not expecting much at the $79 price for this unit.
[Note: After living with this for a while, I wonder why I never thought of just buying a monitor arm and mounting it to the side rail of the camper. This was inexpensive, but it takes up so much space for what it does. I may pull that nonsense out of there and install a new mount.]
Step 8: Side Tables
I had a couple of pieces of half-inch material left over from the bunk, and I used these to make a couple of side tables that “lock” into the tracks that run along the inside edge of the pickup bed. I made a mock-up of the anchoring assembly using a scrap piece of 1/2-inch plywood and a paint stirring stick. I used a utility knife to cut a quarter-inch wide strip off of one side of the paint stirring stick and glued this to the upper edge of the table. I rounded the bottom edge of the plywood below the quarter-inch strip of paint stirring stick, so the edge of the table can rotate into the track. The remaining piece of paint stirring stick is glued to the underside of the table edge, about a half-inch in from the edge. A little bit of sanding was necessary, particularly to paint stirring stick on the underside, to get the test piece to rotate into position and lock in place.
When I was satisfied with the test piece, I scaled it up for a small (eight-inch wide) table/shelf, and even though the table was fairly secure, it still needed a leg to support the front edge. For the leg, I used another paint stirring stick to make a “cleat” near the outside edge of the table, and cut a third paint stirring stick to jam between this cleat and the top of the wheel well. The leg is secured to the underside of the table with hook-and-loop material. I did the same thing with a larger, 14-inch wide table, and used the larger size of paint stick for the cleat and leg. It took a bit of sanding to get the fit right, but the tables can be set up at various positions along the track. The larger table has a second leg for mounting to the pickup bed, instead of the wheel well. When not being used as a table, the larger table also serves as a drawing board for future projects.
Step 9: Updates
Mattress cushions
A good mattress was a priority, so I bought a twin-size, high-density foam mattress, four inches thick, and topped that with a two-inch layer of latex foam rubber. I cut the foam pieces to make three cushions, 23 1/2-inches by 31-inches, and glued the latex pieces to the foam pieces with aerosol adhesive. I found some pretty inexpensive upholstery material at a fabric store, and bought bulk zippers on line that were cut to fit. The cushion covers are just simple box construction, with a zipper along the long seam.
Curtain Loops/magnets
I cut slits in the interior carpeting at the upper and lower corners of the camper and epoxied loops of rope behind the carpet to attach para-cord strings for curtains to slide on.
Update: These just kept pulling loose. I finally bought bolts and drilled through the camper shell to anchor the curtain loops to the inside corners. Since I am going to have bolts sticking through the camper shell, I decided to go a step further, and bought eye-bolts to an anchor the curtain loops. Now I have places to hook shade tarps on the sides of the camper.
Blackout curtains
I bought this blackout fabric on line and sewed curtains for the camper. This fabric is too thick to just sew a sleeve to string the para-cord through, so I sewed button holes (top and bottom) every few inches. The rear curtain doesn’t have button holes along the bottom, it just hangs. I found that I kept sitting on these rear curtains, so I strung them on an elastic cord to prevent damage. On bright moon-lit nights, or when I have to park near street lights, it sure is nice to have the ability to make it dark inside.
Ceiling Tracks
Installing these likely voids the camper warranty, but I felt that I needed them. I just took the screws out of the luggage rack tracks, and bought longer screws to have sufficient length to attach the tracks. Only one of the pre-drilled holes lined up, so I had to drill mostly new holes in the tracks.
Grab Bars
I found some fire-sprinkler pipe hangers that I used to mount 1 1/4-inch diameter, stainless steel closet rails to the tracks. I feel like the grab bars are pretty sturdy, but I try not to put my full weight on the bars when I grab them.
I had modified a set of steps that I originally built for my dog to climb up onto the tailgate. I re-cut these steps so they would slide in under the bunk. After falling off the stairs one night, I got rid of them and am happy to have the extra storage. Now I get into the camper by sitting on the tailgate and using the rear grab bar with my feet on the tailgate to pull myself inside.
Square lumber bars
Once the grab bars were in place, I had a convenient place to attach more cross members that I attached other things (fans, lights, bookshelf) to. I found three-quarter-inch square trim pieces four feet long, and attached them to the grab bars with zip-ties. Since the grab bars are pretty slick, I put a wrap of gorilla tape around the ends to give the zip-ties something to grab onto.
Fans
I have a number of USB powered fans in the camper. One is a seven-inch, square box fan that fits fairly neatly in the pass-through window. I have in set up to work like a whole house fan, pulling air in through the back and blowing it out through the cab. Other fans clamp to the cross members or are just hand-held to cool my head.
Book shelf
I made this so I could have a place to put some reference books and maps, but it’s become a catch-all for everything I can’t find a place to set down. I tacked a length of round pipe wrap insulation to the back of the shelf so it wouldn’t bang on the window. I bought a bunch of cheap little steel hangers and used a torch to heat them up so I could flatten one end of the hanger and put a twist in it so the shelf could be hung from it’s center of gravity. I have a few extra of these over-the-door hooks that I use here and there to attach what-not pouches to the cross bars.
Mosquito net
Here’s where some of the magnets I glued in with the curtain anchor loops come in. The mosquito net attaches to the rear hatch with a loop around each of the door handles. The loops of elastic cord are threaded through a sleeve that runs along the middle section of the top of the mosquito net. From there, the mosquito net has little magnets sewn in to match up with the magnets glued to the inside of the camper. I added some interior magnets near the corners of the upper door hinge, so the mosquito net can be mounted to cover the entire gap in the door. The net is divided in the middle for access, and I added some weighted string that I got at the fabric store to the bottom of the mosquito net to make it hang better.
Quick Changing Room
The doors on this pickup open in opposite directions, blocking the view from front and rear, and this setup only needs something to cover the space between the doors (and perhaps shades on the windows) to have a fairly private place to change clothes. I sewed little pockets to hold strong magnets at two corners of an oversized beach throw. This throw doesn't take up much room, and it can be attached to the two doors with the magnets in seconds. The magnets I bought have a hole in the bottom for attaching to things, and I attached some wooden knobs to a couple of these magnets to anchor the lower part of the throw to the door, in case the wind is blowing.
Gate Pull-straps
Once you’re inside the camper, it’s kind of difficult to reach the hatch and tailgate to close them. I attached a stirp of nylon webbing between two of the screws at the edge of the tailgate to make a handle. I have another length of the nylon webbing that has loops for carabiners that attach to this handle, so I can pull the tailgate closed. I even added a spring-clip, attached to another strap to release the tailgate latch. This needed something to make the strap pull outward on the handle, so I just taped a round plastic container to the pull strap, to give it a way to pull the latch outward.
For the upper hatch, I made a long strap to fit between the latches (on the inside) and attached it by putting grommets in the strap and bought some steel carabiners to mount the strap behind the door latches. This big loop makes a convenient handle, and I have another strap, with carabiners, that attaches to this big loop. While I was making straps, I decided that I didn’t like the way the door clanged open, so I made up a set of short straps that limit how wide the door can open. I have grommets in a couple of positions on this strap, so I can have a couple of open positions. When pushing the hatch open, you can use your foot on the strap to make the hatch open more slowly.
Pocket table
I had made this little side table, but it wasn’t very useful; so, I cut out the center of the table and stapled a canvas pouch to the underside of the table. I already had a big lap board made from quarter-inch thick plywood, so I’m using this lap-board as a cover. This pouch makes a good place for all the little things I like to have handy, and it still works as a side table. I also revised the legs, making an “H” arrangement with paint stirring sticks. The legs sit far enough back that they don’t interfere with sliding things in along side.
Sun Shade
There is nothing particularly original about hanging a tarp from the back end of the vehicle. I did make up a set of one-piece poles made from half-inch diameter fiberglass rods that came four to a pack. Two of these poles are fitted with epoxied-on copper end caps. The caps are drilled and have quarter-inch bolts sticking out for tarp-grommets to slip over. The other two poles (they came in a set of four) were shortened an inch or so, and have copper ferrules with holes in the ends (designed for battery terminals) epoxied on each end. These poles can either be slid in behind the mounts for the luggage rack (either to the rear or to the side) so a tarp can be stretched out and mounted on the other poles. The end holes are about six feet apart, so a six-foot wide tarp can be hung from the pole ends with carabiners.
In a pinch, the two poles with the battery terminals can be mounted to the sides of the luggage rack and hooked together, A-Frame style, to hang a porta-shower. All four of these six-foot poles slide in under the right-hand side of the bunk, but it takes a bit of wiggling to get them all the way in so the tailgate will close.
Wiring
This camper came with a bank of three, 12-volt outlets, that are wired directly to the car battery. I bought a variety of 12-volt USB charge converters, and a ten-foot long USB extension cord. This extension cord happened to fit inside the aluminum tubing that I used for rails that run along the ceiling of the camper. I used some pieces of plastic tubing, heated to expand one end a bit, and slid them in the ends of the aluminum tube I ran the wire through, so the wire wouldn’t chafe. At the other end of the extension cord I mounted a USB outlet multiplier to the overhead with Velcro. I have a number of lights and fans that plug into these USB outlets.
Recently I added an antenna and digital-to-analog signal converter, both of which use USB power, so I have a virtual rat-nest of wires velcro-ed to the ceiling, but I can pick up local news and weather on my DVD player when I'm traveling, so it's totally worth all the extra clutter. I found a USB power hub that has individually switched ports, so I can leave the antenna booster and signal converter off, if I just want to watch a DVD.
Locking bars
It always bothered me that somebody could open the camper while I was sleeping inside. The latches that hold the camper hatch closed are essentially “T” handles that extend through the door with an “L” piece on the inside that rotates to engage the door frame. I cut some pieces of aluminum flat bar (eighth inch thick, by an inch wide) about six inches long. These little bars sit on top of the “T” handle shaft, behind the little “L” pieces, and extend across to the door frame. With one of these little bars sitting on each locking mechanism. There is no way anyone outside can open the door, even if they turn the handles. I drilled holes in these little locking bars and attached them together with a piece of elastic so I can pull them out easily if I’m in a hurry to get outside.
Pass-through window seal
The little windows that open between the cab and the camper allow dust to blow into the camper when driving on dirt roads. I put a seal around the tailgate, but the gaps between the camper and the pickup is wide along the sides and the top, but narrow at the bottom. This makes it difficult to seal the gaps evenly. I made a little square frame out of copper tubing (just pushed together), and wrapped pieces of rubber pipe wrap around the tubes. this still left some gaps, so I used some more of the rubber pipe insulation (larger size) to fill in the gaps on the sides and the bottom. Rubber insulation is softer and doesn't "squeak" like the polyethelyene foam pipe wrap insulation does.
Sliding Window Locks
I cut two lengths of fiberglass rod, that sit in the window tracks and jam up against the end of the window frame to keep the window ajar, but do not allow the window to be openned further. To keep these from rattling out of place and getting lost, I put little tape "tabs" at the end of the fiberglass rods to keep them more or less in the tracks. A small piece of Gorilla Tape attaches the end of each bar to the window frame to keep them in position. To open the window all the way, you just lift the rod out of the track and let the end rest on the inside edge of the camper shell.
[More photos to follow.]
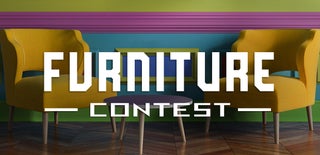
Participated in the
Furniture Contest 2018