Introduction: Recreating the Westar-35 Blaster
In this instructable, I will share the process I used to design and fabricate my own Westatar-35 blaster.
First, allow me to geek out a bit:
The Westar-35 blaster was a commonly used blaster by the Mandalorian group, "Deathwatch". It was also the weapon of choice for Sabine Wren and makes brief appearances in Disney's "Mandalorian" series. I like the simple, functional design of the blaster (typical of the Mandalorian clan) and took inspiration from the many iterations shown in Star Wars media to create my own take on the weapon.
Hope you enjoy!
**NOTE FOR 3D PRINTERS**
While this was conceived as a CNC milling project, I did include .stl files created from the 3D CAD files I created for this design. You can go to the last step to download them.
Supplies
Tools:
2.5D CNC Milling Capability
Sandpaper
Clamps
Painting supplies
Materials:
Plywood (0.5" thickness)
MDF (0.25" thickness)
Dowel pins (.25" diameter - 1.5" long)
Dowel pins (.375" diameter 1.5" long)
Bic pen (2)
Glue
Painting supplies
Step 1: Let's Discuss the Design
The angular look of the Westar-35, lends itself well to a multi-layered assembly where each individual layer is machined using predominantly 2D machine paths. This also lends itself to a simple design and assembly.
The general process is to use 1/4" mdf to create the outer two layers on both sides of the blaster assembly and 1/2" plywood to form the core (backbone) of the blaster assembly. The rigidity of the plywood becomes necessary as the core piece will need to include a large cut-out section to make room for the trigger assembly. This means that some sections of the core will have rather thin wall thicknesses and it's desirable to avoid having them blow through during cutting or assembly/use.
The outer MDF pieces are glued on to the plywood core and all of the pieces being sandwiched together are located relative to each other by dowel pins that pass through each of the pieces.
I got the overall shape of the blaster by looking up images of the westar-35 online and sketching the general shape. I then recreated those sketches in 3D models using Fusion 360. I added a few oy my own features, including a saw-tooth aesthetic on the back end of the blaster and I chose to lean into the blockier front end as opposed to other versions that usually rounded off the "muzzle" of the blaster. When I had a design I liked, I was ready to move on to creating tool paths.
Step 2: Let's Talk About Machining
As mentioned in the previous step, the core piece has a very large section cut out of it to make room for the trigger assembly. We'll discuss the trigger assembly more later on in this instructable, but I wanted to make sure that the trigger could actuate (slide back and forth). This meant I had to give special consideration to creating an internal, spring-loaded, mechanism to actuate the trigger. That was probably the one part of the design that required the most iteration but I eventually figured it out.
Anyway, as you can see from the screenshots I've included here, the actual machining paths are pretty simple. The core plywood piece and triggers require only a few contouring cuts and the outer mdf "scale" pieces are only a little more detailed with the inclusion of small pockets and grooves. The one thing that I want to specifically mention (because it tripped me up a bit) is that the left and right sides of the blaster are mirror images of each other. This means that you can't just create a tool path for one side of the blaster and then cut it out twice. While you'd end up with the correct number of pieces to assemble, half of them would be inverted.
Like I said, I learned that one from experience. haha.
Anyway, thanks to using Fusion 360, the transition from 3d model to machine path, to g code was pretty painless. I've included the g-code files for the left, middle, and right sections of the blaster for those looking to make their own! (As a note on these files.... I wrote each to have the reference origin in the lower left-hand corner of each of the workpieces)
Anyway, now let's get to the assembly:
Step 3: Assembly -- Outer Scale
The first step is to take one of the outer MDF scales and insert a 3/8" dowel pin near the front of the piece and a 1/4" dowel in the hole near the rear. This dowel pin should be pressed in place, but not glued for now. After painting, the dowels will be re-inserted and secured with crazy glue.
This outer scale will now become the bottom of the "stack" as we proceed on with the assembly.
Step 4: Assembly -- the MDF Blaster Body and Handle Insert
The next piece of the assembly is the first piece that actually defines the full shape of the blaster body (along with a small insert that gets glued into the recessed area in the blaster handle). The "blaster body" MDF piece has grooves cut into it that align with the dowels previously placed in the outer scale. The blaster body piece is slipped onto these pins and positioned so the pins are all the way forward in their respective grooves.
Now, these grooves: they could very easily be simple holes, but I found that the grooves allowed me the ability to move the "scales" relative to each other a bit easier. This made glue-up a bit simpler -- but that was a personal choice and you could opt to make the grooves holes instead.
Now, normally I'd say to just go ahead and glue these pieces together but if you haven't painted anything yet then it's not actually the right time for that. When I built this, I did a full dry-fit of the assembly (which is where most of these pics come from). After that, I painted everything as needed and then, once everything was painted I re-assembled and glued everything up.
Step 5: Let's Talk About Painting
I pulled my inspiration for color scheme largely from the design of Sabine Wren's orange blaster. Personally I like orange and thought it really popped against the black and grey. You can, of course, go with your own color scheme.
To simplify painting, I used spray paint for the majority of the job. There is only one piece, however, that is a single, solid color (the trigger). That meant I had to tape-off regions on each piece where I'd eventually need to add a secondary color. As you can see in the picture, I was able to do this with some blue painter's tape.
To achieve more of a "battle-worn" look to the blaster, I used textured metal spay paints for the black and grey (see image of the Rust-oleum spray cans)
The primary color I used for the outer scales, handle inserts, and the trigger was grey. The other pieces were painted black. After all the pieces were painted and allowed to dry, I removed the painter's tape and painted in the secondary colors with a brush (orange or black highlights).
Step 6: Let's Talk About the Trigger
Ok so the next piece in the assembly is going to be the plywood core, which means it's as good a time as any to discuss the trigger mechanism.
Like I said earlier, I wanted to have a trigger that could actually move -- so I needed to develop a simple spring-loaded design. I reflected on that for a little while and I was actually sketching out some ideas when I realized that I was holding the solution in my hand: a pen!
All Bics have a very simple spring system used for extending and retracting the ball-point tip. So I decided to simply leverage that and remove the cartridge and spring from 2 pens. I then found a drill bit that matched the diameter of the ink cartridges (a tight fit so that you have to press them into the hole made by the drill bit). I then drilled holes into the back of the handle in the plywood, though the wall and into the cavity where the trigger sits. I then used those same holes as drill guides to drill matching holes into the edge of the trigger. The holes don't need to be perfect, they just need to align between the trigger and the blaster body.
After drilling the holes, I inserted the ink cartridges in the handle until they protruded far enough into the cavity for the trigger and then I trimmed the cartridges flush with the back side of the blaster handle. This takes a little tinkering to get just right, so I would move the trigger back and forth until I was sure I had the range of motion and feel that I wanted before trimming the cartridges to flush.
Now this goes without saying, but each cartridge is filled with ink. So, when you trim them, that ink wants to spill out and it can get a bit out of hand and messy. I handled this by using crazy glue to secure the cartridges in place in the handle and, at the same time, placed a few beads of glue to seal up the back end of the (now open) cartridges.
Step 7: Back to the Assembly
Last we left off we had the outer scale (with dowel pins), the mdf blaster body with grooves slid onto the pins, and the core and trigger assembly all put in place.
Now the next step in the process is to repeat what we've done on the other side of the blaster (but in reverse order) by placing the MDF blaster body (with handle insert) and finally the outer scale onto the dowel pins. The pins should now sit flush on both faces of the blaster's outer scales.
Step 8: Quick Reference Final Assembly and Glue-up Guide--
OK so I wanted to have a reference where all the steps for assembly and glue-up can be found together in one place:
I'm assuming that, at this point, the pieces have all been painted and no dry-fit test assembly is needed.
1) Using crazy glue, attach the dowel pins into the outer scale on one side of the blaster
2) Slide the MDF blaster body piece onto the pins. Apply glue to the outer scale piece and press the two pieces together -- being sure to slide the scale/pins all the way forward in the grooves on the MDF blaster body piece
3) apply glue to the plywood core piece and place it on the stack, using the pins to correctly locate the piece. Be sure to slide the pins all the way forward in the plywood core's grooves.
4) place the trigger assembly into the cavity in the plywood core piece. Ensure the springs and pen cartridges are in place and secured.
5) glue the opposing MDF blaster body piece in place (as was done in step 2). At this point, it is very important that you ensure no glue gets onto the spring mechanism or trigger. I suggest handling this by using a gel adhesive with a very fast dry time (like crazy glue) and being very careful with how much is used.
6) slide the outer mdf scale into place on the pins -- being sure to place a few dabs of glue in the pin holes on the outer scale to secure the pins.
7) using a paint brush, go around and apply touch-up paint as necessary -- including painting the ends of the dowel pins (orange in case)
Step 9: Finish It!
I applied several coats of polyurethane; sprayed on all the surfaces of the blaster. I used a semi-gloss sheen because I didn't want it looking TOO shiny (looking for the battle-worn look after all)
Once it was all done, I had to put it in its rightful place on my workshop wall!
This is the way.
Step 10: A Present for Our 3D-printing Friends:
A request was made to create .stl files for the different components of the Westar-35 design shown here. I figured, it wasn't any real problem to do and hey, all us CNC operators gotta stick together right?
So for those of you interested in this design, but only in possession of a printer, I've included .stl files that I created from my 3D Cad models.
May The Force Be With You.
Attachments
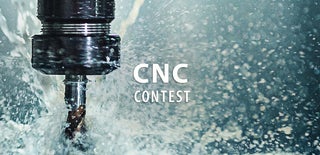
Runner Up in the
CNC Contest