Introduction: Retractable Casters for a Scroll Saw.
This project involves making a DIY retractable caster system for this scroll saw stand. It is a flexible system that can be used on many other projects as well, you just have to adjust for size and weight.
Step 1: Introduction to the Project.
I have enjoyed reading the Instructables website for a few years now and I decided it was time to give something back, so here is my first instructable. I hope you find it useful.
I recently made a stand for my scroll saw out of mostly re-purposed lumber and scraps I had in the shop from a set of plans in Wood Magazine's 2002 publication of "101 Workshop Projects". The plans are found on page 84 and are titled the "super-sturdy scrollsaw stand" and they can also be purchased at this website if you are interested: http://www.woodcraft.com/Product/409617/Scrollsaw-...
Since these plans are someone else's intellectual property I am not going to be sharing how I built the stand. Instead this is an instructable about how I added a set of retractable casters to the stand. This allows me to easily move my saw around the shop with little effort. While I like my scroll saw, I do not use this machine very often and I was tired of tripping over it where it has been taking up valuable floor space when not in use. Getting it up on a stand that can quickly get it out when I need it and then easily get it out of the way when not in use means I will probably find more uses for the saw in the future.
Step 2: Getting Started.
The first step was to draw up a quick sketch of what I wanted to build. Unlike a lot of modern wood workers who like to build things in sketch up first, I prefer to think with a pencil in my hand. I think it probably goes back my high school days of drafting before auto cad became a thing when drawings were done by hand with a t-square, a scale ruler and a set of drafting triangles. Anymore I tend towards quickly drawn crude plans that gets my ideas on paper and then I refine them as I build. Often times when the plan meets the pavement it changes midway through. This happened on this project.
As you can see my crude plan calls for a wood box that will sit on the top edge of the feet and tightly between the two uprights of the stand. The original plan called for a piece of pipe or all thread attached to a board and through two sides of the box as a hinge point for the casters. At the other end of the board there is a handle attached to the lower cross beam to act as a lever to force the board down and lift the stand up onto the casters and while this would have worked I came up with a slightly different way to do the same task after the box itself was built.
Step 3: Cutting the Sides of the Box.
The next step is to make the frame that will house the floating caster board. I scrounged through my cut offs and found enough poplar to make the box. I started on my nine inch miter saw and cut two boards at sixteen inches and two more at sixteen and a quarter inches. Since the boards are five and a half inches wide my fixed nine inch miter saw cannot cut them in one pass so I setup the first cut, set my stop block, made the cut and then turned the board over and finished the cut. The stop block allows me to do that and easily match my cut.
After the four boards were cut to length, I ripped the boards to a width just a hair over four inches on my band saw. Just about a thirty second of an inch. The reason for cutting them just a little wide was so I could sand the edges on my disc sander and still come out at four inches rather than a little under my desired four inches.
Step 4: Assembling the Box.
The box was dry fitted with screws and no glue. Because it will be attached to the feet and the uprights of the stand it will be sturdy enough with just a couple of screws and a butt joint assembly. To avoid splitting when using screws or nails right at the end of a three quarter inch board I like to take the time to mark and drill pilot holes.
I took the two sixteen inch boards and used a quick square and a pencil to mark them at 3/8's of an inch from each end of the board and then drew a line at that point across the end of the board. I then repeated this for each end of the two boards. Still using the quick square I marked two points on each line both one inch in from the sides. Using a center punch and a hammer I lightly punched each mark to avoid having my small drill bit wander when drilling.
Moving to the drill press I drilled four holes in each board with a 1/8 inch drill bit. Then using a hand drill and a counter sink bit, I counter sunk all eight holes.
Using a set of corner blocks I lined up each corner so they were square and even and clamped them in place. Notice the paper shim I used because these corner blocks are salvaged from furniture shipping and are not quite flush though they are square. I need to take them to my disc sander and true them up but the shim worked fine for now. After they were lined up I used my drill and a 1/8 inch drill bit to drill pilot holes into the ends of the two sixteen and a quarter inch boards to avoid splitting. Then using my drill with a driver bit, I set two screws at each corner that were one and five eighths inches long. I took my time and made sure everything was square and level as I worked. After the last screw was in place I was able to test fit the box onto the stand. It was a nice tight fit that was just loose enough that I didn't have to force it into place but snug enough it was tight.
(I want to apologize for the fuzzy picture with the screws and the drill. I didn't check my pics as I went, I just took them and moved forward which turned out to be a mistake as it gave me a few fuzzy pictures I didn't know about until I moved them to my computer).
Step 5: Adding Cleats.
It was at this point that my plan changed. After testing the fit of the box and doing some measuring I realized that I would be better off with a lever that was in the middle instead of at one side of the frame. This would give me more room for the lever to move rather than being restricted by the uprights. The best laid plans of mice and men . . . .
At this point I decided the floating board would really float inside the box and hinge in the middle rather than be attached and hinged at one end. By pressing down in the middle of the floating board the ends could push up against a set of cleats attached to the box frame. This would raise the stand up and set the weight of the saw and the stand on its new wheels. With this new plan in my head but not drawn up I got to work.
First I found a length of two by four that had been trimmed down to a little under three inches wide and decided that would be my cleats. I took my marking gauge and set it to one inch. I decided upon that measurement based upon the height of the casters I had purchased which are two and a half inches high, the height of the stand's feet which is one and a half inches, the thickness of the floating board which would be three quarter inches and the height I wanted to lift the stand up which was also three quarter inches. By setting the bottom edge of the cleats one inch up from the bottom of the box that would set them at two and a half inches off the floor. Since the floating board will be three quarters of an inch, the thickness of the board will give me my three quarter inches of lift when the ends press up against the cleats.
I used my marking gauge to mark a line on both the inside and the outside of the box. I cut the cleats to 16 inches long on my miter saw (I don't have pictures of this). I then used my tape measure to mark three points on each side of the outside of the box. One in the middle and two a couple of inches in from the outside of the box and one and three quarter inches up from the bottom. I took one of the two cleats and carefully lined the bottom of it up with the one inch line I had marked in the inside of the box and held it in place with two clamps.
Using my drill and a 1/8 inch drill bit I drilled pilot holes, then counter sunk them and drove in three two inch screws with my drill and a driver bit.
I repeated these steps on the other side of the box and finished attaching both cleats.
Step 6: Cutting Out the Floating Board.
I had a salvaged piece of three quarter inch plywood that had been sitting around for about 12 years that someone had glued a bunch of fake grass to with hot glue as a start at a model railroad and never went any further. I used my quick square and checked to make sure the edge was square. I measured over sixteen and one eighth inches and made a mark. I used my quick square to make a line and then used a yard stick to extend that line across the board. I then cut that piece of board off with my small skill saw making sure to cut to the outside of the line. I then turned the cut off 90 degrees and measured out fourteen and a quarter inches and made a new line and cut the waste off with my skill saw while making sure to once again cut to the outside of the line. After checking to make sure the board was square, I set the fence of my band saw at eight inches and cut the board in half. This left me with two boards that were eight inches wide and fourteen and a quarter inches long.
Step 7: Adding Hinges and the Casters.
At this point I unbolted the saw from the stand because I wanted to work with it off the floor and didn't want the saw in place for that.
I had a couple of door hinges laying around that never got used on a different project so I decided to use them for this instead. After laying out the hinges, I used my drill and a driver bit to secure the hinges in place with the screws that came with them. I then set a caster on the board and eyeballed it to make sure it was in a position where it could swivel without hitting the sides of the box but as close to the corners as I could get them. That turned out to be about one inch from the edges of the board. Using one inch screws and my drill I screwed down the casters at all four corners. At this point I oiled the hinges with a light machine oil since they were a little stiff and worked them to loosen them up. All the screws I used for this were too long and had extended clear through the board but I test fit it anyway. I found I had made it a little too long so that when I pressed down on it to lift up the stand, it lifted the stand but got wedged in the up position and wouldn't release to lower the stand. After pulling the box and the floating board out by sliding them both sideways until they were off the stand, I then took the floating board to my belt sander and ground the protruding screws down flush with the board so I could use it on my band saw without scratching the table. I decided that three quarters of an inch should be about right to trim down the board so I used my band saw to trim both sides down by 3/8's of an inch on either side. I apologize for the bad picture of this step.
Step 8: Test Fitting.
I laid the stand down on it's side and set the floating board inside the box. After setting the stand back on it's feet I tried pushing down on the hinged board to see how easy it lifted the stand without the saw. The hand you see in the one picture is my son's hand trying it out. It worked fairly well going up but because I left the cleats square it would lock in position and not easily drop the stand back down.
Step 9: Rounding the Cleats.
I decided that I needed to round the bottom edge of the cleats to make the stand easier to not only go up but return back to it's feet.
First I removed the three screws holding one of the cleats in place. I set the table on my band saw to a 45 degree angle and set my fence on the other side of the blade. This allowed me to trim off the inside corner on the bottom side of the cleat. I took the cleat to my belt grinder and finished rounding off the cleat with an 80 grit belt. I reinstalled the cleat with the three screws and did the same thing to the second cleat. I then put the box back in place on the stand and placed the floating board inside it. The stand now went up and down so easily that I had to cut a 3 inch long block of wood to keep the casters in the down position while I worked on it.
Step 10: Attaching the Box.
I used screws to dry fit the box to the stand. Each upright got two screws through it into the box after I drilled pilot holes and counter sunk them. The bottom screw is a three inch screw that is long enough to go through the upright, the box and into the cleat. The upper screw is only long enough to go through the upright and into the box. Both screws are one inch apart.
I turned the stand on it's side and drilled two pilot holes through the bottom of each foot and into the middle of the edge of the box at each corner. I counter sunk the pilot holes and then drove the screws in with my drill and a driver bit. This firmly attached the box to the stand and then I set the saw back on the stand to test and make sure everything was sturdy and worked with the extra weight. Everything seemed solid and I was happy with how it performed.
Step 11: Making a Lever Handle
After using my ruler to make a four inch wide rectangle on a piece of poster board, I marked the middle line and then free handed a shape onto it. I measured up from the bottom of the handle to the center point of the lower upright on which is four and three eighths inches and marked that point on the paper pattern. Since I wanted the curved face to come in contact with the floating board sooner I offset the mark by a half inch and used that for my rotation point. I cut the pattern out with scissors punched a hole through the rotation point with a sharpened awl and lightly screwed the paper pattern in place on the lower upright of the stand and checked to make sure it made contact where I wanted it to. I ended up trimming the pattern a little to fit and when I was happy with the design I traced my new pattern onto a three quarter piece of scrap pine I had laying around.
After rechecking to make sure my band saw table was once again square to the blade I cut the handle out on the band saw. Since the current blade on my band saw leaves a slightly rough cut I took the time to sand the edges on my disc sander and the inside curves on my oscillating sander. Then I drilled a one eighth inch pilot hole at the rotation point on my drill press.
Step 12: Testing the Lifting Handle.
For testing purposed I temporarily mounted the handle to the lower upright with a screw. As you can see I set the rotational point on the upright a half inch off center to the right. by offsetting both the rotation point on the handle and the upright I was able to mostly center the flat bottom end of the handle over the hinge point on the floating caster board.
First I tested to make sure the stand would go up and down without any extra weight on it and then I set the scrollsaw on top of the stand without bolting it down since the stand is still sitting on a piece of plywood laid flat on my saw horses as a work surface and I don't want to lift them down as one unit. I then tested to make sure the handle would indeed both raise and lower the stand. With the weight of the scrollsaw on the stand it takes a little more force to lever the stand up onto the casters than without it but not so much so that it makes it hard to operate. I decided to call this test a success and took the scrollsaw back off the stand.
Step 13: Final Handle Attachment.
I drilled the center upright and the handle out so I could fit a bolt through them. I then took a three inch long 3/8" bolt along with three matching fender washers and a nylon lock nut and bolted the handle to the frame. I sandwiched the handle between two of the washers and used the third under the lock nut and tightened them down until snug but loose enough so the handle can easily rotate.
Step 14: Finished.
At this point you could take some time to paint, stain and/or varnish your piece if you want to. Since I live in a pretty dry climate I do not have a lot of problems with wood swelling or warping so I am going to leave the piece as bare wood for now and will probably take some tung oil finish to it at a later date. Since it is a shop project I am not really worried about pretty at this point and since I want to get all of my fixed power tools up on retractable casters I will save the finish work for another day so I can move forward to getting a more flexible shop instead. With that in mind I set the scroll saw back on the stand and bolted it in place. I am calling this project finished for now.
I hope this gives you some ideas for getting your own tools up on a set of retractable castors. This type of system can be built inside a cabinet as well and you can attach a foot lever arm to one of the hinged boards that extends through a slot in the side of the cabinet to be able to raise and lower the cabinet. If you affix a spring loaded hook to the end of the foot lever that will act as a catch you can then lock it in place in the upright position and then easily return it back down to the floor. If you build it in a cabinet you will still need the rounded cleats to raise and lower the cabinet but those can be as simple as some large dowel rods screwed in place.
Please remember to use appropriate safety gear at all times such as hearing and eye protection when working with tools.
Thanks for reading.
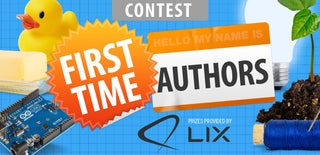
Participated in the
First Time Author Contest 2016