Introduction: Retrofit an Antique Scroll Saw to Use Modern Blades
I picked up a really cool old scroll saw from an estate sale recently. It is a Sears Model 103.23440, and even though it was built in 1948 it still purrs like a kitten. The only problem is that old scroll saws like this one were designed to accept 6 inch blades, which you can't really get anymore, whereas modern scroll saw blades are all 5 inches long. Because I wanted to use my favorite 5 inch scrollsaw blades in my antique 6 inch scrollsaw, I decided to make a simple adapter so it could accept 5 inch blades.
I'm not sure how relevant this instructable will be to someone who doesn't own this exact model of scrollsaw. Still, I figure it will help at least one person with this machine who has the same problem I did. Or, maybe it will inspire others to hack their own antique woodworking equipment to make it usable again.
Step 1: Overview
To get a standard 5 inch blade to fit on a scrollsaw designed to hold outdated 6-inch blades, we need to add an extra inch to the assembly that holds the blades. Here you can see photos of before and after the mod. Read on to see how I made the custom bolt that fits between the scrollsaw's armature and the blade holding assembly, extending it by a little more than 1 inch.
Step 2: Supplies
To perform this conversion, you will need:
7/16"-24 Banjo Bolt from http://www.ebay.com/itm/130972167072
JB Weld
7/16"-24 Plug Tap
7/16"-24 Bottoming Hand Tap
1/4-1/2 Tap Wrench
A 10mm drill Bit
A small washer
(The reason you need the special taps is that the threads that this machine's blade-holder screws onto are non-standard.)
Step 3: Remove Wiring and Potting From Banjo Bolt
The banjo bolt I got on ebay had a wiring harness attached to it. After cutting off the wiring with pliers, I drilled out the remaining plastic with a 7/16" drill bit, leaving a hollow cavity inside the bolt. After drilling, I had to use a screwdriver to pry out some stubborn plastic.
Step 4: Fill the Cavity With JB Kwik and Re-Drill
The hole I drilled was slightly too large to thread it with my taps, so I had to first fill it in with JB Kwik, wait a few hours, then re-drill a 10mm hole. It seemed a little silly to fill a hole in just so I could drill it again, but it got the job done.
**A cool trick to get a perfectly centered hole on a round part like this is to do it backwards -- put the part in the chuck of the drill-press, then clamp the drill bit to your vice underneath it.**
UPDATE: The JB-Weld gave out after a few weeks of use, so I took the bolt to my local welding shop, who filled it with slag for free. I then re-drilled the hole and it now works great after more than a year.
Step 5: Tap the 10mm Hole
Using A 7/16-24 plug tap and a little oil, tap the threads into the hole you just drilled.
Step 6:
Being careful not to get any JB Kwik on the walls, I glued a #8 steel washer flat at the base of the hole. This washer will be important when tightening the bolt onto the scoll-saw later.
Step 7: Add Bolt to Blade Holder
Using a wrench, I unscrewed the blade holder from the scrollsaw. It took a little elbow grease and some actual grease, but it wasn't so hard to remove.
Next, I screwed my custom bolt onto the scrollsaw until it bottomed out against the washer, then gave it a little extra tightening to lock it in place. (I was a little nervous I was going to strip the bolt's threads, since they are just made of JB Weld, but they have held up to a lot of use so far without so much as getting loose.)
Lastly, I reattached the blade holder, this time onto the custom bolt. The blade holder now sits about an inch lower than it was originally designed to, and can reach down plenty far enough to grab 5 inch scroll saw blades. Success!
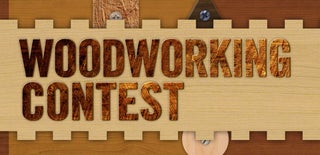
Participated in the
Woodworking Contest