Introduction: Rocket From a Willow Branch
A diverse collection of wood gathered over the years can lead to some interesting projects. I finally got around to doing something I'd been thinking about for awhile—scratch building a rocket from a willow branch. Here's one way to do it...
Step 1: Tools
A range of power and hand tools and model building supplies were used in the construction of the rocket. They are listed below:
Power Tools
It is possible to substitute manual tools for some of these machines, but that would increase the difficulty of the project.
- lathe
- band saw
- scroll saw
- belt/disk sander
- vacuum system
- planer
- hand drill
Hand tools
A usual selection of hand tools is required, specifically:
- hand saw
- coping saw
Supplies
- sandpaper
- steel wool
- plastic wood or other wood dough
- wood glue
- wood stain
- polyurethane varnish
- spray adhesive
- silicone RTV
- 1/4-in wide by 10-in long elastic material
- card stock
Step 2: Materials
You'll need a willow branch. Any kind of wood could conceivably be used, but willow is good because it is not very dense, making for a lighter rocket, and it's easy to work.The willow available was well aged and collected off the ground from around a black willow tree (Salix nigra) approximately 10 years ago. It has been waiting for this ever since (Figure 1).
Select a piece that is about two inches in diameter and straight for at least a foot. Use a chisel or whatever works to strip the bark off of the branch section you wish to use (Figure 2).
Cut off a section of the debarked wood to use for the body and nose cone blank. This piece should not be too long; 6-9 inches is about right. The shorter the rocket body, the easier it will be to drill holes through it.
Step 3: Turn the Rocket Body/Nose Cone Blank
Since willow branches are not perfectly cylindrical, it is difficult to use a standard method of finding the center of each of the cut ends. Use your own judgement to mark the center of each end of the cut willow (Figure 3).
Caution: If you are not familiar with the set up and operation of a wood lathe, then do not proceed without the assistance of someone experienced in lathe operations.
Mount the willow piece between centers in a wood lathe and carefully turn it down to a diameter of about 1-1 1/2 inches in diameter. Rough form the general location of the nose cone on the tail stock end.
Use sand paper to smooth the finish. Keep working until the length of the piece is of uniform diameter (Figure 4).
Step 4: Shape the Nose Cone
Remove the body/nose cone blank from the lathe. Use a combination of belt sanding and hand sanding to finish the nose cone. You have some discretion as to the shape, but I prefer blunt ends for experimental rockets (Figure 5).
Step 5: Separate the Nose Cone From the Body Blank
While holding the body blank firmly (like in a vise with wooden jaws and some additional rubber padding to prevent surface marring), use a coping saw (or other fine toothed saw) to cut off the nose cone (Figure 6).
Step 6: Drill Out the Rocket Body
This is by far the most difficult phase of the construction. If one had a large enough engine lathe, it would be great to chuck up the body and drill or bore either end to the correct specifications. One end needs to have the correct inside diameter to hold an engine, and the other side needs to be large enough to allow for a recovery system.
Note: The following operations could be done in a large drill press. Otherwise, hold the work firmly but gently in padded vise jaws to perform the drilling.
Start by cutting off the unturned part of the end opposite the nose cone to bring the rocket body to its final length.
Then, re-mark the centers of the body ends. Since this piece should be uniformly cylindrical, a machinist's center finder should work, but I eyeballed the centers anyway.
Use a small center punch to carefully and accurately mark the spot to drill on the each end.
Use a small diameter drill (about 3/16-in) to drill a pilot hole 1/2-in deep in the center of both ends of the body blank.
The motor chosen for this rocket is an Estes B6-4, which had a diameter of about 0.688 inches (11/16-in) so I used the next size smaller drill I had, 21/32 (0.672-in). I figured an 11/16 drill would have some runout and make the hole too large for a good fit, so I opted to go undersize and hand work the final diameter (Figure 7).
Drill out the nose cone end of the body as well, but DO NOT ALLOW THE DRILL HOLES TO MEET IN THE ROCKET BODY.
Note: Use a piece of tape on the body drill to mark the depth of the required engine hole and to prevent the nose cone hole from going to far.
Strive to get the nose-cone body hole as deep as while still leaving about 1/4-in between its bottom and the bottom of the engine mount hole. Doing it this way allows for a built-in depth stop on the engine mount side, which simplifies construction.
Step 7: Fit the Rocket Motor
Using rolled up and small strips of sandpaper, work on the engine mount hole to adjust the inside diameter and depth so that the motor slides in with out too much resistance (Figure 8). You might choose to use some kind of power tool to adjust the diameter and depth of the engine mount hole. Keep working until the engine goes in all the way and stops when it reaches the full depth of the hole (Figure 9).
Note: You may have to go back with the body drill to properly set the engine mount depth. If the hole gets too deep, remove material from the engine end of the body to shorten it.
Step 8: Fit the Nose Cone
Fashion a short plug to attach to the nose cone from willow wood, a dowel, or anything else of your choosing. It should be a bit smaller in diameter than the diameter of the hole in the nose cone end of the body tube, and about half an inch long.
Wrap teflon tape around the plug until it fits the nose cone hole easily.
There are a number of ways to install the plug on the nose cone, but to get the best alignment possible, I placed the plug in the hole (Figure 10), covered the plug with red paint, and placed the nose come on the plug and body to make sure it was was centered. The paint marked the best location of the plug on the nose cone (Figure 11).
Glue the plug onto the the nose cone flat (Figure 12).
Step 9: Drill the Through-Hole in the Body
It is now time to connect the engine compartment with the recovery compartment so that the engine can blow out the recovery system at the end of the burn.
Note: This is why you do not want to make the body too long. You need to be able to get a drill all the way through the center of the tube. A jobber's drill as shown in Figure 13 will allow for a much longer body tube.
Use a drill slightly smaller than the one used to start the engine mount and nose cone holes in the body, and drill the rest of the way through the engine hole into the nose cone hole. This provides a gas path between the compartments.
Use sandpaper to smooth any rough surface remaining inside the body tube.
Step 10: Make a Willow Board
To keep the rocket as willowy as possible, flat thin willow wood is needed to make the fins. You'll have to make a small willow wood board.
Begin by cutting the center section out of a fairly wide piece of willow branch (Figure 14). The piece you end up with should be about 1/4-1/2-in thick. Try to get the sides of your cut as parallel as possible (Figure 15).
Then run the board through a planer and take it down to 1/16 of an inch thickness, which may be as low as your planer will go (Figure 16).
Note: Although it would be harder, it is possible to make a board such as this by substituting a belt sander for the planer.
Step 11: Fabricate the Fins
Make a paper template for whatever fin shape you desire. I stuck with a basic triangular-rectangular combination. Use the template to layout the fins (3 or 4, maybe an extra) on the willow board (Figure 17). Cut out the fins, preferably with a scroll saw, band saw, or perhaps a coping saw.
Step 12: Install the Fins
Once your fins are sufficiently sanded and shaped, it is time to glue them on the body.
Set up some sort of support system to hold the rocket off the work surface far enough to clear the fins (I used 2x4's and paper towels). Use wood glue to attach the first fin on the engine mount side of the body. Set the fin as accurately as possible in terms of its alignment and position on the cylindrical body. Let dry (Figure 18).
Note: You may choose to layout and mark the locations of the fins, and this should be done if using a 3-fin configuration. However, for the 4-fin configuration, I just eyeballed them.
Install the next fin in the location opposite the first fin (assuming you are using a 4-fin configuration). Let it dry. Continue adding the fins, allowing at least half an hour glue drying time between fins (Figure 19).
Step 13: Reinforce the Fins
To provide additional strength to the fin mounts, dissolve a bit of wood dough (Plastic Wood or other) in acetone to create a thick but flowable slurry (Figure 20).
Note: Use a high density polyethylene, metal, or other acetone-safe container to mix wood filler.
Use a small brush to apply this material to the joints where the fins meet the rocket body (Figure 21).
When this material has dried, use fine sandpaper to smooth the entire rocket body, fins, fin joints and nose cone.
Step 14: Install Recovery Elastic
This rocket could possibly be launched and recovered without a recovery system, because of its small size and light weight. Initially a parachute system was installed, but even after modifying the chute to be smaller than stock size, there was still not enough room for it in the body tube. So, an alternative streamer system was eventually used.
Use a piece of standard elastic (like would be used in sewing and clothes making) about 6-8 inches long.
Fold one end of the elastic into a piece of thin card stock (like from an index card) and glue it together with wood glue (Figure 22). This forms the mounting pad that will be glued several inches deep in the nose-cone hole.
Attach the other end of the elastic to the nose cone. Do this by carefully drilling and countersinking a pilot hole in the end of the nose cone plug and fastening the elastic to the plug with a small countersunk wood screw (Figure 23). Cover the exposed screw head with a small amount of silicone RTV.
Glue the other end of the elastic (now officially a shock cord) about 2-inches deep in the nose cone hole. Use some kind of tool (like a long nail or a pencil) to push the shock cord mount pad tightly and as flatly as possible against the inner body wall.
Step 15: Install a Streamer on the Shock Cord
There was a piece of plastic left over from the previously mentioned parachute modification attempt, which turned out to be perfect for a model rocket streamer. Any kind of colorful plastic (like low density polyethylene) to make a streamer about 6-8 inches long and 2-3 inches wide should be fine.
Set the rocket on top of a newspaper and layout your streamer underneath and in the middle of the exposed shock cord (Figure 24).
Carefully coat the inner surface of the streamer with spray adhesive (3M Super 77). Then quickly fold the streamer over and onto itself binding it tightly to the shock cord. Trim the streamer to its final size and shape.
Treat the streamer with a light dusting of baby powder to deactivate any glue remaining on exposed surfaces. Any residual stickiness will interfere with deployment of the streamer during flight. Figure 25 shows the completed recovery system.
Step 16: Install Launch Lug
We would be using a standard 1/8-in launch rod with this model so a stock commercial lug was installed.
To locate the lug the longitudinal balance point of the body was found by balancing it on a finger. The lug was attached with wood glue and the joint was sealed with acetone diluted plastic wood (Figure 26). Plastic wood was painted onto the lug itself to improve its stainability.
Step 17: Final Finish
Ultimately, the rocket should be painted to better protect the surface, but for a prototype willow rocket, I thought it appropriate that the natural wood finish should be on display.
The rocket was sanded once again with fine grit sandpaper and the model was stained with a cherry red stain. After drying, the surface of the rocket was buffed with very fine steel wool and a finish coat of gloss polyurethane was applied (Figure 27). Time to fly.
Step 18: Test Flight
As shown in the embedded video, the rocket was launched on Wednesday, June 25, 2014.
Step 19: Lessons Learned and Willow II
It was disappointing to fail to recover the rocket. After searching for half an hour, no trace of it was found. Even a fragment would have yielded valuable information, but it was not to be.
Looking back on the project, here are some thoughts.
- At the very end of the close-up video of the launch you can hear the recovery charge ignite indicating all went well with the engine sequence.
- From that point, either the rocket disintegrated or the recovery system was not deployed. There was no sign of the orange and white streamer at the end of the flight.
- Use a retaining clip on the engine so it cannot blow out the back when the recovery charge fires.
- I was surprised at how high the rocket flew. A less powerful engine would have been better for first flight.
- It is possible that the willow wood was not strong enough to withstand the thrust of launch and/or the internal pressure generated by the recovery charge. Reinforcing the body or making the body tube walls thicker might be a good idea.
Willow II, fare thee better. Speaking of which, a video of Willow II test flight is embedded above. Although it was not a stellar flight (the fins need to be improved, among other things) it was recovered.
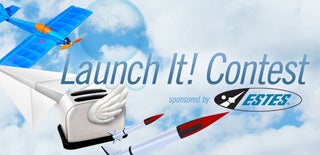
First Prize in the
Launch It! Contest