Introduction: Scale House
This model was designed and built as a teaching aide for students undertaking a Cert 1 in General Construction. Cut outs have been included so that students can see all the components that go into the construction of a house. The techniques used are for modelling purposes and should not be used to construct a full size dwelling.
Step 1: Tools & Equipment
The majority of this build was completed using hand tools. When ever power tools were used the appropriate PPE (Personal Protective Equipment) was worn.
1. Tenon saw
2. Bench hook
3. Tin snips
4. Pencil
5. Ruler / Tape measure
6. Hand Drill
7. Drill Bits (1mm, 1.5mm, 2.5mm, 4mm)
8. Laser Cutter (optional) and software (AutoCAD / Illustrator / Coreldraw etc)
9. Table saw
10. Radial Arm Saw
11. Long Nose Pliers
12. Floor Plans
13. Spring Clamps
14. F-Clamps
14. Philips Head Screwdriver
15. Bench Vice
16. Roofers Square
17. Spirit Level
18. Sliding Bevel
19. Combination square
20. Center Punch
21. Masking Tape
22. Thickness-er
23. Safety glasses
24. Hearing Protection
25. Rags
26. String Line
Step 2: Materials
1. A sheet of 18mm MDF or Ply wood.
2. Hardwood
3. Dressed Pine 40 x 40
4. Miniorb
5. Sheet Metal 1mm thick
6. 12 sheets of interior grade ply 600mm x 400mm x 3mm
7. 8g 32mm Chipboard self tapping screws
8. Brads 20 x 1.25mm
9. Brads 15 x 1.00mm
10. PVA exterior grade glue
11. Weldbond
12. 2 sheets of ABS
Note: Balsa could be substituted for the hardwood for ease of construction. The sheet metal could also be substituted with cardboard if you are using a lighter framing material.
All measurements are provided in mm.
Step 3: Plans
You can use the provided floor plans or find an alternative on the internet. Choose ones based on their simplicity to start with for ease of construction. I have modified these plans to show the main components that go into constructing a house.
Convert all measurements to mm and scale down a 10th. e.g. 1ft = 0.3048m, when scaled by 1:10 1ft= 30mm
Alterations:
The breakfast nook has been removed along with the pantry, hallway and other internal walls. The roof has been changed from a Hip and Valley to a Gable.
Step 4: Foundations
The foundation is construction from a sheet of 18mm MDF (970mm x 1220mm). It was cut slightly larger than the house to be constructed; this allows for the overhang of the roof to be encompassed by the base board.
Using a pencil, tape measure and roofing square the center of each brick pier was marked on the base board.
Use a pencil, Ruler / Tape Measure and Roofers Square to the position of the external walls and all of the brick piers. Find the centers of the Brick Piers by drawing a line from each corner to its diagonally opposing corner. Use a 2mm drill bit to make a pilot hole all the way through the MDF.
Optional: Using a Cad package like AutoCAD, Illustrator, Corel Draw combined with a laser cutter you can add a visual texture to elements of your building. It is best to apply the texture before cutting the piers to the required length as it will speed up the process.
Draw the side of the material to be used for the Brick Pier to the correct dimension in AutoCAD. Apply a textured fill to this shape (rectangle). you may need to adjust the scale of the texture to obtain the desired results. Delete the rectangle and you should be left with the texture. This is a vector based image so you will need to adjust the power settings for your laser to ensure that it doesn't cut too deep. Print the textured design onto the first surface and the rotate your material and repeat for all sides.
The piers need to be cut at 240mm, this a standard height used in single story houses of this era. Mark the centers of the pilot holes in the same manner as above. The pilot hole is drilled with a 2mm drill bit 10mm deep. Place a dab of PVA glue on the marked postion on the MDF, align the pilot holes and affix the pier using an 8g 32mm chipboard screw, coming up from the base. The screw will clamp the 2 pieces of material together and allow you to keep on working.
Step 5: Ant-Caps
The Ant-caps are made by cutting 50mm squares of 1mm Aluminium Sheet with a pair of tin snips. Use a pencil and ruler to ensure that each Ant-cap To create the bent edges, place each piece in a bench vice and gently bend until it looks correct and repeat for each side. Punch the center of each cap with a Center Punch and hammer. This will ensure that the drill bit doesn't slide when making the pilot hole. Use a 1mm drill bit to create the pilot hole. Place a dab of Weldbond onto the underside of the cap and affix to the top of the Brick pier with a nail (Brad 20 x 1.25mm)
Step 6: Bearers
All framing material (hardwood) has been milled down to the required thickness and width based on the scale of 1:10; a thickness-er was used to do this safely.
Cut the Bearers so that they travel the entire length of the house. The position of the Bearers should be on the center of the Piers.
Bearers: 15mm x 12mm x 900mm
Use Weldbond (contact adhesive) and nails (Brads 30 x 1.60mm) to affix to the Ant-Caps. Ensure that you pre drill a pilot hole with a 1.5mm drill bit as the timber can split.
Step 7: Joists
Joists are laid across the Bears at 45mm center spacing.
Joists: 10mm x 12mm x 780mm
Mark the centers for the Joists on the Bears. Clamp the Joists in place and pre-drill your pilot holes using 1mm drill bit. Place a dab of PVA glue on to the Bearers at the required marks and nail the Joist down with 20 x 1.25mm Brads. The Joists at the front and back of the building will need to be doubled up as external walls will be affixed to them.
Step 8: External Walls
The Internal and External walls are made from the same material as the Joist. I wouldn't recommend going any smaller with hardwoods as you increase the risk of splitting.
Walls are made up of a number of components:
- Top Plates - Top section of the wall
- Bottom Plates- Bottom Section of the wall
- Studs - Vertical components of the wall.
- Supporting Stud- Supports the Lintel
- Nogging - Bracing components of the wall that go between the Studs.
- Jack Studs - Smaller Studs that go below windows
- Lintel Jack Studs - Small Studs that go above the Lintel or Door Header
- Lintels - Bracing that goes above windows
- Door Header - Bracing above doors
- Ribbon Plates - Lengths of timber that tie multiple walls together
- Sills - The bottom section of a Widow.
The lengths for the walls are obtained from the floor plans. You will need to take note of the door and window openings. Cut the Top and Bottom Plates first on the radial arm saw. If you don't have a radial arm saw then you could also use a tenon saw. I have attached the AutoCAD and and PDF version of the wall framing layout. Studs are generally layout with 45mm center spacing. Using a scrape piece cut at 35mm provides an excellent spacer. The placement of each Stud is marked with a cross on the Top and Bottom Plates (as seen in the attached files). Drill pilot holes with a 1mm drill bit. Glue and nail (Brad 20 x 1.25mm) the studs into place ensuring that they are aligned with their appropriate mark. Some of the studs have been doubled up where there are windows, doors or join with another wall.
Cut Noggings to fit in between the studs. Noggings are general placed in the center of the wall Note placement in the photo. they are glued into place with PVA glue.
Doors are constructed with Supporting Stud and Stud being glued together and then affixed to the bottom plate. The Lintel is glued and nailed on to the Supporting Stud and then Lintel Jack Studs are affixed at the appropriate dimension. Doorways are constructed 93mm wide internal dimensions.
Windows are constructed in the same manner as the doors the Sill being installed at the appropriate height (Check the plans for details). Jack studs are affixed below the Sill using PVA glue.
Step 9: Bracing Walls
The walls should be erected plumb and square. If they are out then you will find it difficult to align your roof trusses. use a small spirit level to ensure that the frames are plumb.
In order to keep them square we will apply some bracing. This can either by a piece of 1mm Ply or a strip 1mm thick x 10mm wide aluminium. The aluminium strip is apply as close to 45 degrees as possible. Both the Ply and the aluminium are glued and nailed (Brads 20 x 1.15mm) into place. Use Weldbond for the Aluminium and PVA for the ply.
Once erected the walls are nailed into place with Brads (20 x 1.25). Make sure to drill pilot holes.
Step 10: Floor
The floor is constructed from 3mm interior ply. A layer was put down to help stiffen the structure. Each of the floor boards was then cut on the Laser cutter (10mm width) and double nailed (Brads 20 x 1.25mm). Due to the risk of splitting, pilot holes were used to reduce this risk. To save your fingers from injury it is recommended to use a pair of finger nose pliers to hold the brads while hammering. Depending on the lengths of your floorboards you will need to custom fit them.
Step 11: Internal Walls
The internal walls are constructed in the same manner as the external walls, with the studs being slightly shorter to accommodate the thickness of the floor. No bracing is used for the internal walls, this is normally provided by the plasterboard etc. They are nailed into place, and a ribbon plate is attached to strengthen the structure.
Step 12: Veranda / Porch
The Veranda is constructed in the same way as the main section of the house.
- Mark the position of the Brick Piers.
- Glue and fasten the Piers and Ant-Caps into place. The front two piers are cut to the full height of the external walls. A Rock texture can be added to them using the laser.
- Cut and fasten the Bears and joists into place. The bears should be positioned from right to left, this will ensure that the floor boards are going across the front of the building (See Picture)
- Floor boards are cut and nailed into place the same way as the internal floor.
- Support beams are then installed in preparation of the trusses.
- Finishing touches to the veranda (single story)
Step 13: Stairs
The Stairs are made from some 3mm ply for the Stringers (sides) and hardwood for the Steps. an AutoCAD file has been included that shows the dimensions. For the Stringers an outer and inner piece were cut for side; these were then glued together. Once dry the steps were then glued (PVA) and nailed (Brads 25 x 1.25mm). The completed stairs are then glued into place with PVA glue. You may find that they need to be nailed as well, or else they could come off the model.
Step 14: Roof Truss
Before the trusses can be assembled a ribbon plate needs to be attached to the Top Plates. This adds rigidity to the structure and ensures that the walls don't go out of plumb or square.
The roof trusses are constructed out of the same material as the walls. To ensure that all the trusses are the same I would recommend making up a template. You could use a laser or cut one out by hand (AutoCAD Files and PDF are attached). You will need to construct 11 Main Trusses + 4 extra Top Cords for the main section of the house and the Veranda needs 4 Trusses + 2 extra Top Cords. It is recommended to cut all your pieces slightly larger than required so that they can be custom fit for any irregularities in the timber.
Step 15: Roof Bracing
Roof bracing is made up of 2 components:
- Diagonal Speed Bracing
- Roofing Battens
The Diagonal Speed bracing is made from 10mm strips of 1mm thick aluminium sheeting . These are laid diagonally across the roof, they are glued and nailed into place with Weld bond and Brads 15mm x 1.20.
For the Roofing Battens you can use 1mm Ply cut into 10mm strips on a Laser Cutter. They will need to be cut to length so that any joins, sit half on the truss. Each batten is glued with PVA and nailed with Brads (15mm x 1.20). The battens are placed 90mm apart.
Step 16: Roofing
The roof is constructed from Mini-orb. If your roof is square then this should be a relatively straight forward job; but if your roof isn't square like mine then you will have a slightly harder task ahead of you.
Carefully mark out the length and width of the Mini-Orb; make sure to pay particular attention to the lower section of the roof as this will be visible. Once you have cut out the section of material, the position of the battons need to be marked on both edges of the Mini-Orb. 4G 13mm pan head screws are used to to affix the material in place. To ensure that the finished products looks neat, each whole is marked and pre-drilled. The holes are placed on ever 4th ridge. When connecting 2 pieces of material it is best to overlap them by 6 - 8 ridges. This will ensure that both pieces are secured.
Step 17: Roof Capping
The Capping will give the roof a finished look. Remove any screws that are at the top of the roof; the capping piece will be placed here. To make the capping piece, you will need to cut strip of 3mm sheet aluminium to a width of 40mm. Mark the center and the bend to an angle of 45 - 50 degrees. Ensure that it fits and then drill a hole through the capping piece and the mini-orb. Fasten with the same screws that you took out.
Step 18: Acrylic Roof
The Acrylic Roof was added to provide strength to the cut out.\
Lay the a sheet of Acrylic over the are that it is to cover. Trace the shape using a marker and then cut it out using a scroll saw. Cut it slightly larger then you will need, this allows for any alterations to be made. The final fit should be snug. All of the edges need to be polished to a high finish. Use a ruler to scrape along the edges of the acrylic. This will remove any variances in the acrylic from the cutting process. Wet and Dry sandpaper (400, 600, 800 and 1000 grit) is used to remove any white lines. After the sanding has been completed using a small amount of Brasso on a rag to polish to a high shine.
Step 19: Gables
Gables are a decorative feature the keeps the weather out of of the roof cavity. The components were cut using the laser and then adjusted to fit on the disc sander. Each piece was glued and clamped to secure it in place.
Step 20: External Cladding
The External Cladding is made from a sheet of 3mm door-skin ply, ripped down to 20mm strips.You could do this on a table saw or a laser as I did. See the attached file if you are using a Laser.
Each piece of cladding is nailed in place so as to overlap the lower member. This ensures that the top board holds the lower board in place. See illustration for more information.
Step 21: AutoCAD to CorelDraw
Many of the files that I have included were drawn up in AutoCAD. I have included the DXF files where possible; however you may wish to alter them for your own model. The files can printed from either AutoCAD or Corel Draw. Lasers generally work better with Corel Draw as AutoCAD tends to flip the images during printing.
To convert your AutoCAD files to CorelDraw you will need to complete the following sequence:
AutoCAD
- File
- Save As
- Change the file type to DXF
- Ok
Corel Draw
- Open
- New
- Set the bed size of the Laser that you are useing
- Ok
- File
- Import
- Scale 1:1
- Ok
- Place cursor in the top left hand corner and click
For the Epilogue laser the line thickness must be hairline to cut. If you want to raster then you will need a line thickness of 0.25mm or higher.
Attachments
Step 22: Barge Board
The barge board is made from 3mm Plywood. This was glued and nailed into place with brads.
Step 23: Flashing
Flashing was added to areas where the roof touched external walls. In a real world situation this would prevent water from getting into the building. On the model the flashing helps to orientate the roof when it is removed. The flashing was constructed from 1mm aluminium sheet and bent on a magna-bend. A similar result could be achieved by carefully hammering the metal into a right angle along its length.
Step 24: Soffit
The Soffit is the external section under your trusses. There was a gap where the Soffit was to be installed; spacers needed to be cut to bridge this.By doing this it ensured that the soffit would not flex when nailed and glued into place. This was the last component for the construction of the house. Labels where added to the building for teaching purposes.
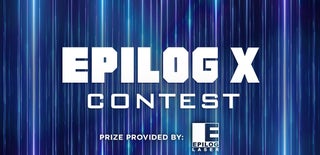
Participated in the
Epilog X Contest