Introduction: Silk Screening Napkins and T-Shirts
I've always enjoyed taking a design or picture of mine and printing it on a shirt, but small-run custom designed shirts are costly, and the results are always hard to predict. This Instructable will walk you through how to take a custom design and silk screen it onto a shirt. The process is very enjoyable and the results are on par with what you would order online or even buy in a store (assuming the same method is used). This instructable encompasses two project done simultaneously using the same methods. The first project was a run of 25 monogrammed napkins and the second was a set of custom t-shirts.
Full Discloser: I made it at Techshop and I highly recommend anyone near one to check them out.
Materials List:
Silk Screening Ink: I used Jacquard Professional Screen Printing ink, which you can find here
~ 2 feet of vinyl suitable for a CNC vinyl cutter: I've always bought all my vinyl from a Techshop, and they typically have a lot (and colors are not important for this instructable since it will be disposable)
Material with with to silk screen: Shirts, napkins, burlap, anything that will be compatible with the ink and method used. Definitely bring some scrap material with you as well.
1 Silk Screen: I used the Techshop's silkscreen, but it was very similar to this one.
1 Silk Screen squeegee: The Techshop typically has some around, but this is what they look like.
1 Hot air gun: To help dry the ink post-screening
1 Iron: To set the ink into the material
Vector Editing Software: I interchange between Adobe Illustrator and Corel Draw regularly, but the files I used here are in Illustrator
Techshop Classes Needed:
CNC102: CNC Vinyl Cutter SBU
ART103: Silkscreen Printing SBU
Step 1: Design and Print on Vinyl Cutter
- Work out design in Illustrator or Corel Draw
- Import design into FlexStarter (the program the CNC vinyl cutter uses)
- Align design with the lower left corner of the canvas
- Take a scrap piece of vinyl and set it up in the vinyl cutter
- Setup your print settings (this will at least involve mirroring your piece)
- Cut your design out on the vinyl cutter
- Hit "Reset" on the Vinyl Cutter (the one at the SF Techshop required this step, which is why I include it here)
- Adjust pressure and speed settings and test print again to get desired cutting depth and speed
- Cut final piece
- Remember that you want the cutting needle to cut through the first layer (the vinyl), but not the second layer (the backing)
- The vinyl piece will need to be mirrored in order to come out right on the fabric
- For one color designs, black is where ink will be coming through. Keep this in mind as you design
Attachments
Step 2: Weeding - a Test of Patience
- The first picture shown is what your vinyl looks like when it's fresh off the vinyl cutter. Now you must separate all the portions you would like ink to pass through.
- Vinyl is prone to stretching, and when that happens you're in trouble. Stretching is most likely to occur when you're making progress on weeding, but the sticky part of the removed vinyl makes contact with the sheet. Trying to unstick the two pieces typically stretched both. This must be avoided.
- I to the use my hand as much as possible to stick separated vinyl. If that gets too unwieldy, then I grab some scissors and just cut it off.
- Depending on the complexity of the design, I've had weeding sessions take anywhere from 30 seconds to 45 minutes. I've attached a few more pictures to show just how complex you can go with vinyl designs, and how that can really prolong the weeding process.
Step 3: Transfer to Silk Screen
- Lay out your vinyl in front of the roll of transfer paper
- Pull out a sheet that encompasses vinyl on all sides
- Slowly and carefully use a squeegee to flatten out the transfer paper onto the vinyl
- Using either the blade of scissors or a knife, cut the vinyl free from the the table. I always cut the transfer paper only, keeping about 0.5" margin of extra transfer paper on all sides.
- STEP NOT SHOWN: Remove the white backing material from the vinyl. This should be done VERY carefully. Keep a dental pick handy in case any vinyl pieces start to lift up from the transfer paper
- Place vinyl sheet onto silk screen. You only get one shot at this, so get it right.
- Remove transfer paper from vinyl. This step is a bit trickier than when the vinyl backing had to be removed since it's stickier. I use a squeegee to help keep the vinyl down as I remove the paper (picture shown).
- Fill in any exposed silkscreen with scraps of vinyl. Any exposed section run the risk of allowing ink to pass through. Use whatever you have around to cover it (scraps of vinyl are typically available and work well for this purpose).
Step 4: Lay the Ink!
- Clamp your silkscreen into the silkscreening jig. I preferred the simply ones the SF Techshop provides.
- If doing more than one piece in your run, mark out with tape or pencil where it should be placed to minimize setup time
- Place your test piece under the screen
- Using a squeegee, prop out your screen so it's not resting on the fabric
- Lay out your ink above the design
- Do your flood coat: this is using a squeegee to fill the silkscreen with the ink and get it primed for transfer to the fabric. It should only be done once*
- Remove the squeegee that was propping up the screen and place it on the fabric
- Do your fill coat: this should be with firm pressure and done once**
- Lift the silkscreen carefully and let the fabric fall away on its own
- Carefully remove the test piece and examine for quality
- Repeat with final piece if everything turned out well***
- When you are either done or the ink begins to dry, remove the silkscreen and rinse it out with warm water. CAUTION: This can irreparably damage the stickiness of your vinyl and it may begin to feel off. If that happens, well, try to see if you can repair it, but otherwise you'll have to print out another one.
- If totally finished, air dry your silk screen post thorough rinsing.
* Use a squeegee that covers the entire width of your design. If you don't see ink flood the entirety of your design, that's probably alright so you should continue with the fill coat. Doing more than one will cause bleeding of the ink onto your fabric and it will likely look bad.
**Same deal as the flood coat. You've really only got one shot at this. Doing more than one can cause bleeding of ink.
***It typically takes one or two test pieces to get into the groove with laying ink. You can press too light or too firm, so you're going to have to find what works for you and your fabric.
Step 5: Set the Ink
- If available, checkout a heat gun to hasten the ink drying process (otherwise it can take 1+ hours to dry)
- Use an iron to set the ink. Iron setting will depend on the type of fabric you're using. This smoothes out the final texture. My understanding is that the ink texture is roughly because of the makeup of the silk mesh the ink has to pass through. Ironing helps even out all the peaks and valleys of the ink.
- Use starch after if necessary. It made our napkins turn out excellent!
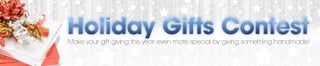
Participated in the
Holiday Gifts Contest