Introduction: Simple Leather Card Caddy
Sometimes, you don't need a wallet. You just need something to hold all of your gift cards, points cards, membership cards, discount cards, etc.
This is a perfect solution to throw in a purse or coat pocket. Very minimal and simple to make. Just to make things interesting, I'm going to intentionally do some things wrong and show you how to fix it.
This is a relatively simple leatherwork project. Don't be turned off by the amount of steps, I just like to type a lot. The design and construction requires very basic skills. However, this is a great project to practice your skills while making something useful. Let's begin!
Step 1: Materials
Tools:
- razor knife
- rotary cutter (optional)
- ruler/straightedge
- harness needles
- awl
- marking wheel
- tooling stamps and hammer (optional)
Materials:
- 3 - 4 oz. leather (outer layer)
- 1 - 2 oz. leather
- waxed thread
- leather glue
- leather finish
- leather dye
In brief, we need lining leather (1-2 oz.), slightly thicker leather (3-4 oz.), a way to measure and cut it, and a way to sew it up.
Step 2: Draw Up the Pattern
I like to draw up everything in a vector-based drawing program, like Inkscape, even if the design is simple. This gives me the ability to quickly and easily adjust dimensions. It also makes it easy to save a copy of everything I design for future reference.
We're going to have three staggered pockets on each side, plus one centre pocket. We'll make the outermost layer on each side out of thicker leather, just for added stiffness and so that we can tool a design on it.
The pockets need to have approximately 1/8 inch seam allowance on each side. If our stitching line is too close to the edge of the leather, there's a possibility it will tear when we punch holes with the awl.
I've included the Inkscape file and a JPeg of the pattern. You can also just draw your own. While you can measure and draw the pieces right on the leather, I always print and cut out paper templates first. They make it easier to figure out where to cut to get the most out of a section of leather. It also let's you test out how your pieces will fit together before you make any expensive cuts.
Attachments
Step 3: Cut Your Leather
Place your leather flesh (rough) side up on a smooth surface. A sturdy table or even a hard floor works. Place the paper templates on your leather. Arrange them to make the best use of the shape that you have, minimizing waste. Remember that you're making the two smallest pieces out of your thicker leather.
Mark the corners of your templates onto the leather with a pencil or marker, then use a straightedge to draw lines connecting the corners. If something doesn't look quite right, refer to your templates. It's very easy to fix any mistakes at this stage, so double-check before moving on.
Once you're satisfied, cut out your pieces using a razor knife or roller cutter. I recommend using a metal straightedge as a guide. The key here is to cut carefully but firmly, in one steady motion. A sharp blade is essential here. If you can't make a nice smooth cut, try sharpening your blade or changing it out.
*Safety Note: Whenever you are cutting leather, remember that tools designed to cut leather will easily cut through the thin layer of leather that is your skin. Be careful!
Step 4: Tool Your Design
At this stage, you can decorate your outer pieces if you wish.
To start, use a sponge to dampen your leather thoroughly and evenly. Let it sit for a few minutes until the surface begins to return to its original colour.
There are entire books dedicated to describing tooling techniques. For this project, I decided to just use some stamps with complete designs on them rather than make something from scratch. If you don't have any stamping or tooling supplies, you can make decorative cuts with a swivel knife, or even draw on your leather by pressing hard with a stylus.
I don't have any in-progress shots of this step, but I wanted to show off the hammer I made. One face has a few layers of leather over it to minimize wear on my stamps.
Set this aside to dry completely before continuing.
Step 5: Assemble and Sew
Line up all your pieces, tallest in the center, shortest on the ends, like so.
If everything looks good, stick the bottom 1/4" of each piece to the next one in the stack. Take care to make sure that they stay aligned.
Contact cement is tricky stuff. It seems to have a working time of about half of a second. At the same time, it can be picky about what it will stick to. Sometimes the grain (smooth) side of leather will have a finish that doesn't play nicely with the cement. If this is happening, I find it helpful to rough up the area to be cemented with sandpaper. A thin layer of cement and a few seconds of pressure should give you a secure bond.
Now your leather pieces should be starting to look like something that can hold cards. If you sewed up the sides right now, it would look really slick, but I can guarantee you you'd never manage to force a card in between those layers of leather!
To keep our card caddy from becoming a solid stack of leather, take some old plastic cards (gift cards work well) and place them between each layer, as if they were sitting in the finished pocket. Pay attention to the heights of each card.
Now when we sew this up, the leather will stretch and the pockets won't be impossibly tight. Forming the pockets this way also means we don't have to worry about sewing or gluing a bottom to each pocket.
Use the marking wheel to mark stitching lines up both sides, 1/8" from the edge. If you don't have a marking wheel, you can use a ruler, a sharp eye, and a steady hand.
With the holes marked, punch them with your awl. Be mindful of where your cards are. When you're going through eight layers, it's easy to punch right through a card, as well!
With your holes punched, thread your needles and start sewing up one side. The cards will have a tendency to be squeezed away, so make sure that as you sew up the one side, the cards are staying in place, leaving a 1/8" margin on the opposite side. Continue along the bottom. To make it easier on yourself, leave a 1/4" seam allowance. You can always trim it shorter if need be.
Sew up the other side.You may find that the cards are getting in your way and you're struggling to keep your stitches away from the edge. What ever you do, don't take out the cards! If they don't fit while you're sewing, they definitely won't fit after!
You may have noticed that the stitching goes "under" the rose design on one side. All I did was simply bring the thread through every layer but the last one for a couple of stitches. It was a little tricky to do in such a tight space, but makes for a unique look.
Step 6: Square Up the Edges
Uh-oh, take a look at the first picture. When I cut out my pieces, I somehow wound up with them a little less than perfectly square. I went ahead and sewed them together, anyway. Fortunately, because I used the cards as a guide while sewing, all I have to do is trim the edges parallel to the stitching. Cutting through all the layers at once can be challenging. I used a new (sharp) razor blade and carefully shaved down the edge.
Now your card caddy is virtually done! Try removing the cards and see how they fit. They'll probably be in there pretty tight. Work them in and out a few times to loosen them up a bit. You don't want the cards to be too loose, so it's better to start off with tight-fitting pockets and let them stretch.
Step 7: Finishing
It's good practice to always burnish your leather edges. There's a lot that's been written on burnishing. Essentially, we're going to rub the edges so that the fibers compress and get all tangled in each other.
Start by moistening the bottom edge with a damp sponge. Place the edge perpendicular to a flat surface. Using a scrap cloth, quickly rub back and forth along the edge, at the same time pressing down on the up-facing side. If you simply held the item in your hand and rubbed the edge without applying pressure to the sides, the edge would start to flare outward. Continue this process until the edge becomes shiny, then repeat for each side.
Uh-oh, looks like I shouldn't have used a black scrap of material for this. The edge has bits of black all over it! Simple solution is to dye the edges solid black, which looks nice, anyway. I used a simple water-based leather dye and painted the edges.
After taking care of the edges, give the whole item a coat of leather finish. I used a water-based finish with "satin" shene, meaning it's flat and not glossy. You can apply it with a wool dauber, or just a paper towel.
That's it! We've skipped some details that will probably have some pros pulling their hair out and cursing at their screens, but you can always add new techniques as you learn them. There are far more technically superior ways to set up your stitches and burnish edges, for example. Bear in mind that a simple technique, well executed, produces better results than following complicated instructions without real understanding.
Hope you enjoyed this Instructable! Please ask me any questions or provide feedback. Also, please consider voting for me!
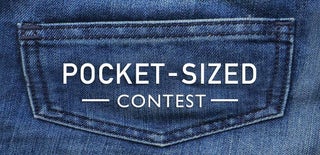
Participated in the
Pocket Sized Contest