Introduction: Socket Trays
I have long desired a better way to organize my sockets in my Husky toolbox. After searching for and not finding quite what I wanted, I found that I just needed to design my own.
So, here are my Socket Organizers.
Step 1: Requirements
As with any design project, I first set out to determine what I wanted.
- Socket end up - I want to be able to see what I am grabbing; 6-point, 12-point, size. I find that when I am looking for a tool, I look for the size visually as opposed to reading the size.
- Easy to grab - I am a large person with big hands. I don't want to have to pinch my fingers down to fit them in to grab a socket.
- Low profile - This is really the biggest issue that I had with the trays available on the market, they don't tell you how high the sockets sit off the drawer. I want my Deep sockets to fit in my shallow drawer, which means that they need to sit only about 2 mm from the drawer.
- Grouping - I want to try to group the sockets by the most commonly used. Even if you disagree with what I think are the most common, it still puts the sockets in groupings that will be memorable.
- For SAE: 3/8", 7/16", 1/2", 9/16"
- For Metric: 10, 11, 12, 13mm
COMMENT: Someone mentioned that there is a lot of wasted space in my design. This was intentional because these trays were designed to fit in my drawer, front to back, with about 1/2" space overall. This space allows me to easily grab a tray and take it to my work area. This is also the reason that I did not make these interlocked with each other. Thank you for the comments, I appreciate them.
Step 2: Design
For the design of my trays, I used TinkerCAD.
Following are the steps that I took during design:
- Determine what socket sizes should be included for each ratchet size. (My socket set is a Craftsman Mechanic's set but does not include all of the socket sizes that larger sets have.) To determine what could be included in a socket set, I went to the Craftsman website and searched for individual sockets. Another good site for determining this would have been McMaster-Carr.
- Layout the sockets in patterns that allow for grouping by common use and give easy visual identification. Basically, I am trying to create patterns that would allow me to put my hand on the socket that I want without really looking at the tray.
- After layout, it was found that I had areas of empty space on my tray. This quickly became recessed to allow for temporary storage of nuts and bolts.
- After achieving tray arrangements, I then added some indents to the sides to assist with grabbing the trays. It is not my intent to remove the trays from my drawer, but if I did, I figured a little lip for the fingers to grab would help.
- Design requirements for 3D Printing:
- Base model - This model was the initial design with recessed letters. This was intended for easy painting of the letters. This design would also allow for strategic filament changes on a single extruder printer if I chose to printer the letters in a different color. (see Single Extruder section.)
- Dual Extruder Model - This design fills the letters of the base model for a 2nd color for use with a Dual Extruder printer. This design also includes alignment lines that are there only for the purpose of aligning the text to the base when printing.
- Red will be used for SAE sockets. Blue for Metric.
NOTE: I did not have all of the sockets for measuring. I estimated the size for those that are not in my tool box.
Step 3: Technique #1: Painting
Printing:
Since these trays will be in my toolbox in my un-insulated garage, I chose PETG and ABS as my preferred filaments for this project. PLA is the easiest to print but may distort in the heat. I printed with 15% infill, 3 walls, 3 bottom layers and 6 top layers.
Painting:
I used Testers Model paint. For applying the paint, I tried a bent paper clip, a broken plastic paintbrush handle, and toothpicks. Of those, I feel the filed down toothpick worked the best. It was still difficult to keep the paint from getting on all the surfaces. I also tried a Sharpie red pen to paint over the areas to give crisp lines. But, the Sharpie smeared when sealing, so may want to re-think this method.
Sealing:
I used 2 coats of XTC-3D for sealing these trays.
Painting Conclusion:
I am a terrible painter.
Step 4: Technique #2: Single Extruder - Filament Change
Printing:
I have not used this method, yet, for this project. But, I will be using this method for printing the 1/2" socket trays as those trays are too large for my dual extruder printer.
The procedure for this would be:
- Place a pause in the printer's GCode at layers located 3 layers lower than the surface of text that I want to be displayed. (So, 3 layers below the bottom of the recessed letters.) At this pause, I will change the filament to a different color. (white)
- Place a pause in the GCode at the layer just above the surface of the recessed letter. At this pause, I will change the filament back to the base color (Red/Blue)
I have created an Alarm box for this purpose to alert me when it is time to change the color. For more information on the Alarm Box, please see my write-up at: Color Change Alert Box for 3D Printer
For another example of how I changed colors on my single-extruder printer, please see my write-up at: Robot Lightswitch Plate
Print Settings:
Since these trays will be in my toolbox in my un-insulated garage, I chose PETG and ABS as my preferred filaments for this project. PLA is the easiest to print but may distort in the heat. I printed with 15% infill, 3 walls, 3 bottom layers and 6 top layers.
Step 5: Technique #3: Dual Extruder - Multi-color
Printing:
For Dual-Extruder printing, I use a FlashForge Creator Pro.
Creation of printer code involves selecting one extruder for the base (Red or Blue) and one extruder for the text (White). I have to then center the files over the top of each other. To assist with this, I have added lines that line up with the outside edge of the socket.
Print Settings:
Since these trays will be in my toolbox in my un-insulated garage, I chose PETG and ABS as my preferred filaments for this project. PLA is the easiest to print but may distort in the heat. I printed with 15% infill, 3 walls, 3 bottom layers and 6 top layers.
Step 6: STL Files
For Technique #1 or #2, you will only need to download the Base files. For Technique #3 (Dual), you will need both the Base file and the Text file.
Please Note: I have not printed from these exact files, so please let me know if you have issues with printing these. Also, I have not printed the 1/2" trays, yet, as my large printer is currently down for maintenance.
Attachments
SAE 3-8 Shallow Text.stl
SAE 3-8 Shallow Base.stl
SAE 3-8 Deep Text.stl
SAE 3-8 Deep Base.stl
SAE 1-4 Shallow Text.stl
SAE 1-4 Shallow Base.stl
SAE 1-4 Deep Text.stl
SAE 1-4 Deep Base.stl
Metric 3-8 Shallow Text.stl
Metric 3-8 Shallow Base.stl
SAE 1-2 Shallow Text.stl
SAE 1-2 Shallow Base.stl
Metric 3-8 Deep Text.stl
Metric 3-8 Deep Base.stl
Metric 1-4 Shallow Text.stl
Metric 1-4 Shallow Base.stl
Metric 1-4 Deep Text.stl
Metric 1-4 Deep Base.stl
Metric 1-2 Shallow Text.stl
Metric 1-2 Shallow Base.stl
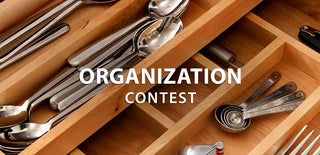
Runner Up in the
Organization Contest