Introduction: Solder Constructed Framed Pendant
In this "in the classroom" tutorial brought to you by Creating Linus Jewellery, learn how to solder construct a Sterling Silver Frame around a Roller Printed image. Tips and Techniques include: how to score and bend crisp 90 degree corners, File fit an insert, Bail making, how to make emery tools and tricks to help improve your soldering skills.
Materials used:
1. Roller printed or hammer textured "insert" piece
2. Framing material - I used flat rectangular sterling silver wire (2 mm x 6 mm)
3. Bail material - I used 2 mm round, sterling silver wire
Tools used:
1. Jewellers Handsaw
2. # 3/0 saw blades
3. hand File #2
4. Square Needle File #2
5. "C" Clamp
6. flexible shaft (rotary tool)
7. Emery paper (220, 400, 600, 1000, 1200 & 1500)
Step 1: The Insert
Start with your roller printed insert. Decide on what shape you would like. Square or Rectangle and roughly cut to size; make it a little bit larger than final size - 1 or 2 mm all around (image 1). Use a Jewellers handsaw to cut out the shape, not snips. Snips will curve and distort the metal; the insert needs to be very flat and the jewellers handsaw will not cause it to distort.
To learn more about:
- Roller Printing turn to page 50 in the July, 2012 issue of Creating Linus Jewellery.
- Hammer Textures turn to page 84 in the September, 2012 issue of Creating Linus Jewellery.
- Jewellers Handsaw turn to page 62 in the September, 2012 issue of Creating Linus Jewellery.
Creating Linus Jewellery is a free online magazine packed full of jewellery tutorials, interviews with jewellery artists and articles.
Step 2: A Little Refining of the Shape
File the edges even making sure the corners are 90 degrees; use a Square or a piece of paper to check the angle against (image 2)
Step 3: Cutting the Framing Material
The Length of the brackets will depend on the size of your insert. You will need 2 "L" shaped brackets. Each bracket will make up 2 sides of your frame. To begin with you will want the framing material to be a little long, as you will be butting up the edges of the brackets to solder them together (image 3).
Step 4: Ruff Out the Score
Using a separating disk, mounted on a screw mandrel, cut about half way through the metal. Make sure you are cutting a 90 degree angle across the long side of the metal (images 4 & 5).
When using rotary tools always tie back long hair and wear safety glasses. Be especially careful when using a separating disk as it is a cutting tool which can do you serious harm. Do not go too fast as it is easy to loose control of a separating disk, always pull the disk towards you and do not let it travel away from you. If a separating disk is allowed to travel in the direction in which it spins (away from you), towards an edge, it could grab the metal and run under the metal spinning out of control.
Step 5: Refine the Score
Using a "C" Clamp with a piece of leather against the metal (no scratches), secure it to the "V" Board (image 6). Finish the Score with a #2 Square File. Don't forget that the file is tapered and will give you an uneven score if you do not rotate sides while filing (images 7 & 8) You will need to file almost all the way through the metal - there should only be a paper width left (image 9). This will give you a crisp corner. If you do not go far enough through the bend will be rounded rather than square.
To learn more about Files and Filing turn to page 66 in the September, 2012 issue of Creating Linus Jewellery. Creating Linus Jewellery is a free online magazine packed full of jewellery tutorials, interviews with jewellery artists and articles.
Step 6: Bend the Score
Before bending anneal the metal. If you don't it will break. Carefully bend the score into the required angle. You will need to match the bend to the insert as it may not be a perfect 90 degree angle (image 10).
TIP----- If you find that it will not bend enough; the angle in the score may not be deep or wide enough. This can be fixed by annealing the metal again (or it will break) and slowly opening up the score in-order to continue filing. Then Repeat step 5 (yes you will need to anneal again before re-bending or it will break)
To Learn more about Annealing turn to page 46 in the July, 2012 issue of Creating Linus Jewellery.
Step 7: Soldering the Brackets
Solder the corners of the brackets with hard solder. This will secure the brackets so they are unable to move. They are very fragile and easy to break otherwise.
Flux the inside corner of each bracket. Position the first bracket so the inside is away from you and the corner is towards you. Heat the bracket evenly until the silver is a dull red colour then place a piece of Hard solder on top of the seam. Direct the torch on the lower outside of the corner until the solder flows through the seam (image 11).
Allow the Silver to cool till it is no longer glowing and carefully place in pickle.
Repeat steps with second bracket.
To learn more about soldering, flux and the different types of Solder (Hard, Medium, Easy and Extra Easy), read my tutorial "sterling silver band ring" on page 48 of the September, 2012 issue of Creating Linus Jewellery.
Step 8: Forming the Frame
Each bracket will require a "Just right" end and a "Long" end. Mark the length of the "just right" end of the brackets and file or saw to the correct length (photo 12). Then saw or file it to size (image 13). You must get a good joint. This is tricky. Using a #2 Hand File, file the "just right" ends until they but up with no gaps against the "long" end of the opposite bracket (image 14)
A word of encouragement
It is likely that you will end up shortening the length of the brackets while trying to fit the seam - this is ok - keep in mind that the Insert is a bit larger than what the final size will be. It is easier to file the insert to match the Frame once the frame is soldered together.
Go slow and check the fit often. This is a difficult seam to match - look at it from many angles. if you get frustrated it is a good time to stop and have a nice cup of tea. Fresh and calm always beats irritated and tired.
Step 9: Setting Up the Frame
Make sure when you set up the Brackets to form the Frame that you get the size correct by sliding the Brackets to the right Position. Remember to make the interior Frame a bit smaller that the Insert as you can always file the Insert smaller to fit the Frame (image 15).
Solder the brackets together using hard solder. This step is very similar to step 7. This time since there is more than one joint, Flux both joints - solder the first joint then rotate the firebrick so that the second joint is in position and solder it (image 16).
Tip:
Yellow ochre can be painted on to the original two solder joints to discourage the solder from flowing. Yellow ochre is a natural paint pigment; it is sometimes referred to as ani-flux as it does the opposite of Flux. Flux keeps the surface clean where Yellow ochre dirties the surface - Solder does not like to go where it is dirty and dirtying up the surface of the solder will often (though not always) prevent it from flowing.
Yellow ochre all of the original joints. You will have to use discretion here - you can not allow the Yellow Ochre and Flux to mingle. Remember the joints that you want to solder must stay clean. So, only put Yellow Ochre where you can, without risking contamination of the flux.
Step 10: Emery the Inside Frame
Once the insert is soldered into place it will be very hard to file or evenly emery the inside frame - so file and emery before soldering. Start with a good # 2 square needle file in the corners. It is important to get a crisp corner - it will help with the fitting of the Insert. Go slow and check often, be careful of thinning out the edges or creating ruts with the file. There might be extra solder in the joints causing them to be rounded rather than nice and 90 degrees - file away the extra solder. Once the corners are completed emery the inside frame with 220 Grit and work through 400, 600, 1000 and 1500. Don't do any Polishing. It will be very difficult to get into the inside corners with a polishing tool. I prefer to leave the finish at a nice even 1500 emery than have an uneven polish. (image 17)
Tip ---- Clean as you go? When working on a complex solder constructed piece with many joints it is hard to know when to clean (emery) solder joints. My rule of thumb is to ask myself this question: Can I get to it once the next joint is soldered in place? If the answer is no - then clean it now. Leaving extra solder in a joint until all of the soldering is completed is a "trick" that can save you a lot of problems later. Every time you solder one joint you risk opening up all of your previous ones. By leaving the extra solder, there is a good chance that the solder will not flow out completely should the joint open up. if you clean all of the extra solder away leaving only the solder in the joint and it opens up there is nothing there to flow in behind it.
Step 11: Tip: Emery Tools
Polishing tools can not get into every spot but the right emery tool can. I love Emery tools (just ask my students how much and listen to them moan!). It is well worth the effort to make emery tools - they will save you time and give you precision.
Using 1/8 MDF board cut strips - For this project I made mine 6 inches long and the same width as my double sided tape. I prefer MDF board as it is very flat (giving you good contact to the metal) yet flexible. Simply adhere the emery paper with the double sided tape. This is an example of a basic emerying tool. I have many specific and more complex emerying tools in my kit that I make as I need them.
How much emerying is needed? Well the harder the spot to get into the more emerying I do. My minimum is 220 and 400 grit (from here I can get a good finish with polishing tools). But with hard to reach spots I will go all the way down to 1500 grit - I find that I do not need to polish the silver at this point, saving me from trying to find a polishing tool that will fit. I always prefer an even fine emery to an uneven polish.
Later in this project a more complex emerying tool will be needed. I made this one with 1/8 MDF board (cut to the same width as double sided tape and 3/4 inch long). Using fast setting glue (krazy glue) attach a handle made out of doweling.
Step 12: Fitting the Insert
File the Insert with a #2 Hand file to fit snugly into the Frame - no Gaps - it should require a little force to fit but not so much that it bends or bows. Go slow and check often. It is helpful to use registration marks to ensure you are always checking in the same position (image 18).
Step 13: Positioning the Insert
I like to use coins to set the depth of the insert - metal will expand and contract when heated, which can cause a tight fitting insert to slip. By using Coins or scrap bits of metal, during soldering, underneath you can prevent the insert from moving. Just be sure if using Coins that they are made of material that can withstand high temperatures - some of the newer coins are made with low melting alloys - I learnt this the hard way! (image 19)
Step 14: Setting Up for Soldering
Place solder on the backside of the insert (that way if there is any solder mess it will not flow onto your image). Flux along the edges of the contact points - both front and back. Yellow Ochre as much of the original solder seams (the brackets), as possible with out contaminating the flux (use your discretion). Place the piece front side down on the Fire Brick. Using wire Silver Solder, Lay in "strips" of Medium Solder (Flux the Solder strips) against the inside frame wall (image 20). Do not use too much solder, which could flood the piece.
TIP:
Yellow ochre can be painted onto the Roller Printed side to act as a barrier against solder spillage (image 21). Just be sure not to allow the Yellow ochre to mix into the flux; if it does wash with soap and water, and reapply.
Step 15: Soldering the Insert Into the Frame
Heat the piece evenly using a medium sized flame until the metal turns a dull red. If the Flux boils causing the Solder to move - move it back - the Solder must be touching both the insert and the frame wall.
Once the Metal turns a dull read move the flame so it is pointing low on one of the outside frame walls and draw the solder towards the wall - once this happens on one side - keep moving the torch until the solder on all four sides has pulled through the seams. (image 22)
Allow the Silver to cool till it is no longer glowing and carefully place in pickle.
Step 16: Making the Bail
In-keeping with my Leaf motif I wanted the Bail to resemble a stem. To do so I started with a 6 Inch piece of 2 mm round wire. Using a Cross Pen Hammer against a steel block forge out the Stem with graduated blows, leaving the end of the wire wider. Use files and emeries to smooth out the hammer marks. (images 23, 24 & 25)
Lets Talk Design:
When Designing Jewellery there are some practicalities you should not ignore. Pendants Hang. So The Design should take this into consideration. I do not like to just "stick" a Bail onto my Pendants. Every part of the Design should be considered and incorporated. Using a theme or Motif can help. Not only did I use a Stem as my Bail inspiration, I also cut a "tare" into the upper left hand corner of my roller print insert- reflecting yet again a natural Leaf.
You might have chosen a different image or even a texture for your Insert. What ever your Insert might be, take some time to consider the design of your Bail - it is an opportunity to add further interest to your piece.
The other thing to consider about a Bail is that it is a "ware" point. The chain will rub up against the Bail, causing it to thin. Starting with an already thin Bail will result in breakage. The Bail on a Pendant is usually the first thing that needs repair.
Step 17: Fitting the Bail
Where ever possible I like to avoid a "butt" Joint. By slotting or pegging a joint you make it stronger and more incorporated into the design. In the case of my Bail I am able to make the Joint Slotted by Filing a slot onto the back of the frame, using a square needle file (image 26). Go slow and check the fit often - NO GAPS - I filed the slot about half the thickness of the Bail (image 27).
Before Soldering the Bail to the Frame emery the Back edge of the Frame flush and smooth, starting with 220 emery through 400, 600, 100, 1200, 1500 grits. It is much easier to get at the back edge of the Frame before the Bail is soldered on (image 28). I like to use a steel block with self adhering emery papers but a bit of spray glue works nice, just be sure the steel block is very smooth; the block can be sanded smooth with a palm sander starting with course emeries and working down to smooth, 220 grit is smooth enough.
Step 18: Soldering the Bail
Yellow Ocher all of the Solder Seams. Flux the seam to be Soldered and the connecting point on the Bail. Lay the Frame Image side down. Use a Third Arm or Coins or Scrap bits of Metal to prop up the Bail in place. Heat the Frame section first - this is your Heat Sink. Once the flux has gone clear place a ball of Medium Silver Solder on one side of the Slot and direct you heat to the opposite side pulling the Solder through the frame.
TIP Heat Sinks:
When Soldering two pieces together where one is significantly larger than the other; the two pieces will heat up at different rates. Part of the reason is that they are of different masses, but also the larger mass will "suck" heat away from the Smaller. Always keep in mind that Solder is attracted to the hottest point. By heating the larger mass first allowing the heat to move from it to the smaller mass you are controlling the flow of heat. Paste Flux is a good indicator of heat temperatures; once enough heat has moved from the larger mass to cause the flux to go clear on the joint the metal is hot enough to place the solder. Give the larger mass just a bit more heat (until it turns dull red - not bright red) - then go in for the "kill". Direct your heat on the opposite side of the Solder - to "draw it through the Joint towards the flame.
Step 19: Finishing
Now that all of the Soldering is done it is time to do the Finishing. First Trim off the Frame overhang using a saw (image 29). File and emery the frame sides smooth (220, 400, 600, 1000, 1200 and 1500 emery). Polish to a bright finish.
Emerying the back and front of the Insert will be more tricky - here is where emery tools come in. For the front of the Insert the finish will depend on what your image or texture is; because of the imprint I could not do to much emerying or risk losing the image - I decided on a light emery only 1500 grit using my emery tool.
For the back of the Insert I gave it a good emery - 220, 400, 600, 1000, 1200 and 1500 emery - no polishing, since I could not get into the corners evenly with a polishing tool (image 30). While the Bail is a straight piece; emery and polish. Carefully curl the Bail using fingers or Pliers.
To learn more about polishing turn to page 76 in the September, 2012 issue of Creating Linus Jewellery.
Lets talk about the Finish.
The finish is the part I like the least! I am all about the action: soldering, hammering, fitting things together - the fun bits. But the finish - well - is probably the most important part. No mater how well you do the action bit - carefully fitting that perfect joint - getting a beautiful clean solder joint - a poor finish makes it all look bad.
Heating sterling silver has one particular side affect: firescale. Heres the science: firescale is a red or grayish purple stain that appears on mixtures of silver and copper, such as sterling silver. At high temperatures, oxygen mixes with the copper to form cuprous oxide and then cupric oxide.
Once you are done all of your soldering firescale is not "noticeable" because it is covering the entire surface of the piece. Emerying or filing will start to remove the firescale making it noticeable because now there is a contrast of where it is and where it is not. You will never get a nice bright even finish without removing all of the firescale. Attempts to "cover" firescale with a texture will only result with a texture overtop of the firescale - since you can not hide a colour by putting a texture overtop of it!
What ever finish I choose to end my piece with I always bring it first to a high polish by emerying all of the firescale away and polishing. I might not leave it at a high polish but I always start there - a high polish will always make a texture look better.
When you can and when you can't remove firescale.
It is not always possible to emery away firescale. If a texture or imprint must be done before soldering it into place (as in the case of my roller printed Insert), emerying the firescale away after all of the soldering is completed, will result in the loss of my image. Instead I "live with it". One trick that can be used in this case is "raising the fine silver" or "depletion gilding". By heating and pickling the sterling silver several times (until you achieve a uniform white colour), you are creating a thin layer of pure silver at the surface - sterling silver is made of pure silver and copper. Once this pure silver surface is achieved a tumbler or brass brush can be used to polish it. Do not use emeries or polishing techniques that removes metal - as this will remove the very thin layer of pure silver. I only do this in areas that are recessed or textured; if used on outer surfaces repeated rubbing will remove the pure silver - the piece will look fabulous when you sell it, but will not take long before the firescale is noticeable - this is a dirty trick! Always remove firescale where you can.
Some artists choose to leave the firescale on a piece because they like the look of it - this is an honest design choice. In the end what is important is that you - the Artist - is happy with the work. It is important to make conscious design decisions - mush like good abstract art - your finish should be a result of choice not a lack of knowledge, skill or craftsmanship.
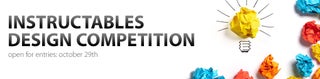
Participated in the
Instructables Design Competition