Introduction: Solution for Warping ABS 3D Prints
As many people who print with ABS know, 3D printing with ABS can be a really frustrating experience. I do a lot of printing with ABS and for months I could not find a good solution. However, after all my experimenting I think I came up with a viable solution that uses no acetone or expensive materials.
Note: PLA plastic will not adhere to the bed with this method.
Step 1: Why Printing in ABS Is So Hard
For those who might be new to 3D printing, this section will explain why ABS is hard to print without failure. You might be asking yourself why people want to print with ABS if it is so hard to print. ABS plastic has very desirable characteristics such as high toughness which allows it to withstand high stresses. However, ABS plastic can shrink between 7-10% when it cools. This becomes problematic because if the ABS doesn't adhere to the build plate, it will shrink and detach itself causing a failed print. You want the plastic to adhere to the build plate such that it does not peel off easily, but you also want to be able remove the piece when it is finished printing without damaging the piece or the printer.
Step 2: Acquiring Supplies
You will need two supplies: plastic packaging tape and a glue stick. Both can be acquired easily at an office supply store or on amazon.com. I am using the Elmers brand extreme glue stick. I have found that this glue stick works better than the smaller purple kind.
Step 3: Setting Up the Build Plate
Take the plastic packaging tape and cut it into long pieces. For this build plate, I am applying the tape horizontally across. Make sure the pieces are slightly longer than the length of the bed so you can fold the edges under to ensure the tape doesn't peel up.
When applying the tape, make sure the build plate is cool as air bubbles will form more easily if it is warm. If any air bubbles form when applying the tape, take a plastic card (credit card, license, etc.) and remove all air bubbles. It is very important that no air bubbles are trapped under the tape.
When the tape is completely applied, take the glue stick and apply a generous layer of glue. I usually apply the glue in horizontal strokes and then vertical stroke. Allow at least 15-20 minutes to allow the glue to dry before printing.
Step 4: Printing and Future Care
I have been printing ABS and PETG plastics with no warping issues at all. I plan to test some other filaments like HIPS in the near future.
To remove the print from the build plate, wait until the print cools and then peel it off. I have found that sometimes I need a thin piece of metal to pry the edge of the print off the build plate. However, I have never had any trouble getting the print off the plate.
After each print, the layer of glue that I applied to the build plate sticks to the bottom of the print. To print again, just apply another a layer of glue to the area that the print was removed from. To remove the glue layer on the bottom of the print, just rinse it off it warm water. The glue stick I have is water soluble.
I only replace the packaging tape every once in a while when the glue starts to build up unevenly. I can print about 10-15 times before replacing. To replace the tape, I heat up the build plate to about 60-70 degrees to weaken the adhesive and then I gently peel the tape off.
Thanks for reading! I hope this method helps with your 3D prints. If you have any questions, please feel free to comment.
Also, with such a divisive and frankly toxic election season, you might find it refreshing to vote for my tutorial :D
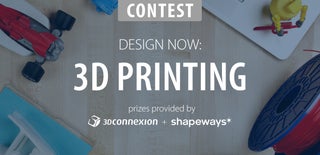
Participated in the
Design Now: 3D Design Contest 2016
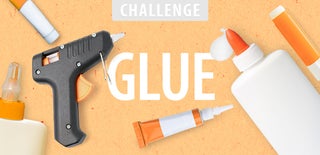
Participated in the
Glue Challenge 2016