Introduction: Steerable Continuous Track Concept
In this Instructable, we will go through my adventure of designing and modeling a steerable track/tread (as in tank track). I will try and cover as much of the modeling and simulation steps as possible, I will try to communicate all the important information in the text but there might be useful tips and information in the picture annotation. I hope you can learn something from me here and I can learn from you too! so please comment (especially how to do things more efficiently with motion simulator)
So a little background on this project. (no important instructions here)
I recently started my internship at a construction/agriculture vehicle company (Kubota) and after speaking to a few of the employees there and looking through the catalogs, I learned that tracks that can be retrofitted to tractors are in high demand. The problem is the good quality ones are too expensive and the affordable ones very unreliable. The usual approach is to have a set of tracks for the front wheels and another set for the back allowing it to steer as usual.
So i thought to myself, what if we could have a track system that will be able to span from the front to the back and still be steerable. after making a few quick sketches and quick googling, i proceeded to work on the CAD model in Solidworks
The two main inspirations
https://www.google.com.my/url?sa=t&rct=j&q=&esrc=s... (never seen this)
http://en.wikipedia.org/wiki/Hyanide (Seen this many years ago)
*Regarding similarity to airport baggage carousels
https://www.google.com.my/search?q=airport+baggage...
Honestly, I am not entirely certain how airport baggage carousels or conveyor belts work in detail. From my observations, the movement is usually restricted to rotate about 1 axis. Airport carousels and sushi shop belts are usually flat (or at a fixed angle) and would allow the vehicle to steer but it would not wrap around the wheels. I would appreciate it if someone with knowledge on this subject can provide some input.
Few thoughts about this project/system
- I undertook this project mainly to gain a better understanding and feel for how tracked vehicles work, as well as to sharpen my skills with Solidworks and its motion simulation package.
- It is a very crude model, ease of manufacturing and upkeep is only lightly considered.
- Halfway through this project I thought it could be a good method for steering a single tracked vehicle like the Hyanide, I feel that the Hyanide's design would have poor turning radius and this method could do better
Some additional design criteria
- I made it a point to design the tracks such that stiff material may be used (such as metal tracks used by construction vehicles and military vehicles ) It can still accommodate rubber cleats for traction but flexibility must be due to mechanical linkage.
- The tracks must still provide advantage of lower ground pressure and better traction. The track is also designed to minimize damage to the ground, but maneuverability is prioritized.
Potential application for this system
- Retrofit to tractors
- Tracked vehicles that want to minimize damage to the ground (construction and landscaping vehicles)
- Single tracked vehicle, like the Hyanide. Could be used in rough terrain, snow, or maybe even on the water
- Military vehicles to improve maneuverability
- Robots, hobby or otherwise
Ps* If I can get my hands on a 3D printer, I can print and test out my design for a cute little robot.
Step 1: Designing the Track/treads
*UPDATE*
Since many did not notice the section i wrote on preventing sideways drifting of the track/track slipping off. I would like to note its on step 5. I have also added renderings with idler wheels and "suspension" since I know its TLDR (too long din't read)
The main difference over traditional track systems is that we need to be able to rotate a section of the track in an additional dimension to allow it to turn. Each link should have 2 degrees of freedom in terms of rotation.
I started with a sketch on how i would want it to work. Each link will be made of 2 parts where at one end we allow rotation in one axis and at the other end rotation in a perpendicular axis.
I name the part that will contact the ground as "Main Plate" and the part that allows for the additional flexibility is named "Pivot Plate"
The main plate will need to be able to pivot around adjacent main plates while maximizing contact with the ground. To achieve this, a semicircle is used for the front. To ensure that the adjacent main plate pivots correctly, the pivot should be located at the center of the circle. At the back, I made a "chopped off" semi circle, chopping off the tail allows it to turn properly (refer to picture).
As for the pivot plate, since it is closer to the "wheels" than the main plate is, it is also the pivot plate's job to allow for some interface that allows power to be transmitted to the tracks. The pivot plate is also going to have some interfacing surface with the guide rollers that we will cover later. The pivot plate is basically has one end that allows a main plate to rotate about an axis and another end that allows the next main plate to rotate about a perpendicular axis. It also has a large protrusion that allows the drive cog to engage it and turn the track, much like rack and pinion gears.
I also made a pin just to hold it together. But in hindsight, we can probably omit this pin to allow for faster computation in the motion analysis (will be covered later) since the mates defined will be sufficient
Step 2: Assembling the Track Optional: Solidworks Mate Reference Tips/simple Tutorial
If you are already proficient in assembling chains and tracks in solidworks, feel free to skip this step.
Initially I assembled one link (main plate+pivot plate+pin) and saved it as a separate file then I tried to assemble multiples of it together. The results were not satisfactory as I could assemble the track, but it could not rotate.
In order to assemble the track to the desired length quickly, I used mate references instead. Mate reference allows the parts to "snap together" when you hold them close together in assembly.
How to set up mate reference
- Open the first component/part file.
- Select "Mate reference", Found in Features>Reference Geometry>Mate Reference
- First name the Mate reference. *Important* make sure it is exactly the same as its counterpart in the next component.
- Next is to select the desired surface or edge or point and the desired mate type (default is ok, but not always the best) If you use surface or edge, you will usually need more than one mate reference, ensure the order of primary, secondary and tertiary mates are the same for its counterpart.
- Open the next component/part file.
- Repeat steps 2,3 and 4
- Repeat for as many components and mate reference you need.
Once you have your mate references set up, when you open the parts in an assembly file, they should snap together and automatically generate the desired mates when you bring them close together.
Step 3: Designing the Drive Cog/wheel
I am not sure what the correct term is, so forgive me please. Here its more of a story of failure, the few initial iterations did not work properly when tested with the motion analysis. So why would you bother to read about my failures? so you don't repeat them.
In the initial design, I positioned the tracks into a semi circle, drew a circle, drew lines from the center of the circle to the pivot plate protrusions and measured the angle of these lines. I then made the wheel and cut out narrow slits for the protrusions to interface with. The problem is that the spacing between the protrusions are very large unlike conventional tracked vehicles, this made it quite unreliable from the test i did.
Next I tried widening the slots and later i tried adding more slots but to no avail. Finally I took a different approach and instead of a solid block with slots, I made a Yo-Yo like wheel with plates.
To be honest, it works but its very poorly designed and I am not very satisfied with it. However it works well enough for a concept.
*The drive wheel could also use heavy trimming to reduce weight and material cost.
Step 4: Holding the Track in Shape
To ensure the track maintains its shape for operation, we need another wheel in front and a way to hold both of the wheels.
The design of the front wheel is pretty straightforward. The front wheel can be exactly the same as the drive wheel as some vehicle (some tractors) are 4WD. Here I used a YO-YO shaped wheel similar to the drive wheel but without the interfacing plates, this was done mainly to cut down on computational time.
The structure holding the wheels are a little more complicated. We will need to ensure that we are still able to steer the track since thats the whole point of this project. Also keep in mind, we will need some way to maintain tension on the track when the track is steered. Remember the hypotenuse of a triangle is always shorter than the sum of the other 2 sides.
There are many was to achieve this, here is what i did.
The rear bracket is "fixed" as in it will be attached to the vehicle chassis or will be the chassis and it is the reference point for all other parts. (The universe revolves around the rear bracket!!). The rear bracket simply holds the rear axle in place and provides pivot for the front bracket. The front bracket has a point that pivots about the rear bracket and a slot that holds the front axle. The front axle is held in a slot so we can place springs that act to maintain the track in tension.
In hindsight, for a design made to be retrofitted to 4WD vehicles, tension of the track should probably be maintained using a mechanism similar to a bicycle chain tensioner. If the front wheel is also a drive wheel for a non-single-track-vehicle, the vehicle's front axle should enter from the pivot and power the track's front axle through a gear system.
The rear bracket is very basic and can be modified. Some of the possible modifications:
- Made into just a frame that can be bolted onto a vehicles chassis for retrofit
- Made to hold additional idlers and suspension
- Made to hold flexible guides that can "shape" the way the track interfaces with the ground. (more on this later)
- Made into the chassis of a single track vehicle. (You can put your rider on top or even inside! but not under)
Step 5: Track Guides and Suspension System
The main purpose of the track guides are to ensure that the track will bend where you want it, how you want it. The design of the guides are very straightforward, it is basically something that holds a couple of rollers that restrict the tracks motion in certain directions (translational and/or rotational)
For the top guide, you mainly want the track to bend at the pivot, this is because it allows for the smallest footprint and would not allow the track to "cut into" the vehicle's body when steering, this also ensures that the tracks engage the wheels straight on and would be less likely to fall off. One of the simulations i performed without the guides actually saw the tracks fly off.
For the bottom guide, having the track bend at the pivot should allow for the best possible steering at the cost of some ground damage but I may be wrong as its a deduction based on intuition. You can and maybe should have multiple instances of the bottom guide modified to accommodate suspension springs and dampers. The bottom guide may also be used to "shape" the track into a smoother curve instead of an abrupt bend.
The rollers are basically donuts, its really just 2 concentric circles extruded.
Step 6: Mostly Done! Motion Analysis and Simulation in Solidworks
The track system is mostly done. Here I will share on my work trying to simulate the system steering while in motion. Here I wanted to see how it all works out and have a cool animation to show for my efforts, the values calculated and data acquired are disregarded as they mean nothing since I did not input any accurate data (like weight, density, forces, speeds) but its alright since its a proof of concept. To achieve all this, I used solidworks motion to run the analysis.
I will be very grateful if anyone is willing to share their experience on how to improve the computational efficiently. I basically learned all this as I went along.
You can also animate the assembly using the animation tool or basic motion tool, however I could not get it to work the way i want it to and solidworks motion was able to.
- You will need to enable solidworks motion by going to "triangle beside options">Add-Ins...>Solidworks Motion.
- Then at the bottom of your screen switch to the motion analysis tab.
- First we will define what parts are in contact and will not "phase/ghost/wallhack" through other parts. To improve computational efficiency, I used the group contact function. The whole track was placed in once group and the parts it comes into contact with (both wheels, guides+rollers) are placed in the second group.
- Another contact group was defined to contain the front bracket, front axle and front wheel. This is to prevent the whole thing from collapsing or the wheel from flying off into orbit.
- To simulate the spring holding the tracks in tension, I used 2 forces applied on the from axle relative to the front bracket. I used forces instead of actual springs because I am not sure how springs act in the simulation and experiments with it were not fruitful.
- Add a motor to the drive wheel to get it running and add a motor to the front bracket to see how it turns.I also added a large plate to act as the floor which makes it more realistic.
- Press calculate
- Do something else, its going to take awhile. After turning down the frame rates and accuracy it took me 7 hours to solve 3 seconds of motion.
Be warned, save as many videos of it as possible when you can. Solidworks crashed on me when i clicked "save" (happens everytime, hope its just me)
Extra Tip* It might be wise to turn the accuracy and frame rates down and test in successive complexities. What i mean by testing in successive complexities is that for the first time, just test a few links of the track with the drive wheel, then test the whole track with both wheels, next add in the tensioner force, then add in the steering motor next and lastly add in the floor.
Step 7: Thats It!
Here are some of the videos I could record before solidworks crashed on me. You can go to my youtube channel to look at a whole playlist of ill-sorted videos on this project
http://www.youtube.com/playlist?list=PLoUSuSQ_C_4V...
And a little extra rendered images
I hope you would have learned something from this adventure of mine. Please do leave a comment, especially if there is something you can teach me (and everyone who reads comments)
*Ps, vote for me! if I get a 3d printer, I will print this out (a more refined version) and test it!
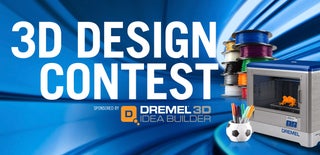
Runner Up in the
3D Design Contest
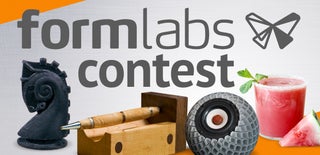
Participated in the
Formlabs Contest
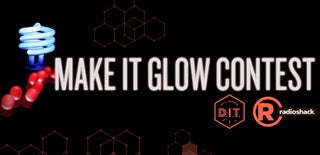
Participated in the
Make it Glow!